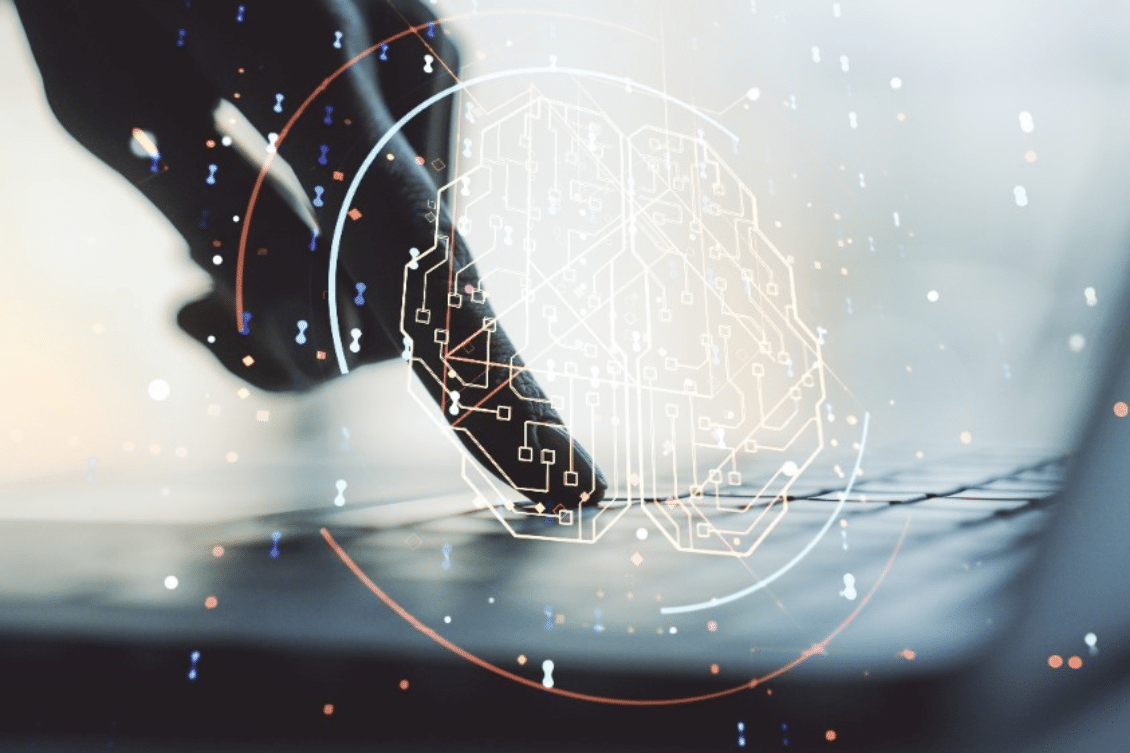
No one can say they weren’t warned about possible global disruption such as a war or pandemic. We had a pandemic in 2020 and, with a short break, got the war in Ukraine in 2022. In light of the news about China reaffirming their government commitment to take control of Taiwan, we should think about what will come next. Those events are rare and highly improbable. However, there are many other events. Think about supplier company failure, cybersecurity breaches, harsh winter, or tropical weather. These events are highly probable and have a high impact. Those events are not a question of “if”, but they are a question of “when”. The question is how to get prepared and predict these events.
The manufacturing industry is facing an unprecedented challenge like never before. The increase in the cost of raw materials and transportation, volatile currencies, and pandemic-related disruptions have all taken a toll on overall efficiency and profitability. To support seamless operations and ensure business continuity, manufacturers need to explore innovative ways to address these issues – one of them is to have a product information and lifecycle management strategy that can prepare a manufacturing company for a seamless operation and intelligent decision-making process. In this article, I will speak about 3 elements of your data management and information strategy that can better prepare your company for the future disruption and possible events I mentioned at the beginning.
Focus on Product Information
Data is the foundation of everything. It is very hard to think about anything intelligent when you don’t have the data about the product, how it is designed, and built, who are the suppliers and what is the cost of the elements included in your product. While the data is located in legacy databases, Excel spreadsheets, and multiple applications, it is very hard to impossible to get the right information at the right time.
Manufacturing companies are running multiple applications to support their operation and the data is widely distributed between these tools. Some of these tools are limited to departments and some of them are global. The common problem in every manufacturing company is to get a holistic view of all the information. It includes but is not limited to:
- CAD design and its derivating data
- Item catalogs with all connected pieces of information
- Product structure and bill of materials
- Orders, project specifications, orders, etc.
- Customer problem reports
- Many other pieces of interconnected information
The goal of every manufacturing company is to collect all the information and provide a single shared access to the data, up-to-date revisions, files, and pieces of data such as suppliers, specifications, drawings, etc. Only by organizing the entire set of product information, a manufacturer can de-risk its operation, because no matter what, all the information will be available and can be used to derisk the operation.
Knowledge Graph
Having all information about the product, files and BOM is not enough. Although it provides a great foundation for future decision-making, what is really needed is to build a network of dependencies and semantic connections between elements of the data. Think about the connection between components and their suppliers, relationships between product configurations, and countries to which these products are sold.
Knowledge graphs are a powerful information tool that allows getting all information organized and connected semantically. Building a knowledge graph out of a particular product, interlinked descriptions, design files, business needs, and events, combined with relationships with customers, suppliers, other businesses, and service providers creates a knowledge graph everyone is looking for.
Impact Analysis
Once you collected all the information and build relationships and dependencies, it is now the time to put them to use. The tool that is capable to get interlinked information in the context of product development, supply chain, or engineering decisions can make the entire manufacturing business much smarter, and provide some handy tools helping to discover information, validate impact, and build for the future.
OpenBOM Intelligent Services
At OpenBOM, we are planning to provide intelligent services using a robust and powerful OpenBOM platform. The core multi-tenant data management foundation with a flexible data model ensures OpenBOM will have all pieces of information lined up and ready for discovery. OpenBOM intelligent services will be combined with tools and methods to make data analysis and discover connections between data elements. In the first step, we’re expecting BOM comparison, change impact analysis, cost services, and several others.
Conclusion:
By focusing on holistic data management, tools to collect and check the data, and by building robust and scalable online services, OpenBOM plans to provide an intelligent tool to all manufacturing allowing them to swim better in the ocean of product information. Combined with navigation, calculation and analytical capabilities, OpenBOM product intelligent services will provide an access to all the information about your product, intertwined with cost, supply, production, procurement, compliance, and many other aspects of manufacturing design and operations to be able to use it by the time the crisis will come.
At OpenBOM, we are looking for enterprise companies interested in exploring future OpenBOM capabilities. Please contact us to discuss more.
Best, Oleg
Join our newsletter to receive a weekly portion of news, articles, and tips about OpenBOM and our community.