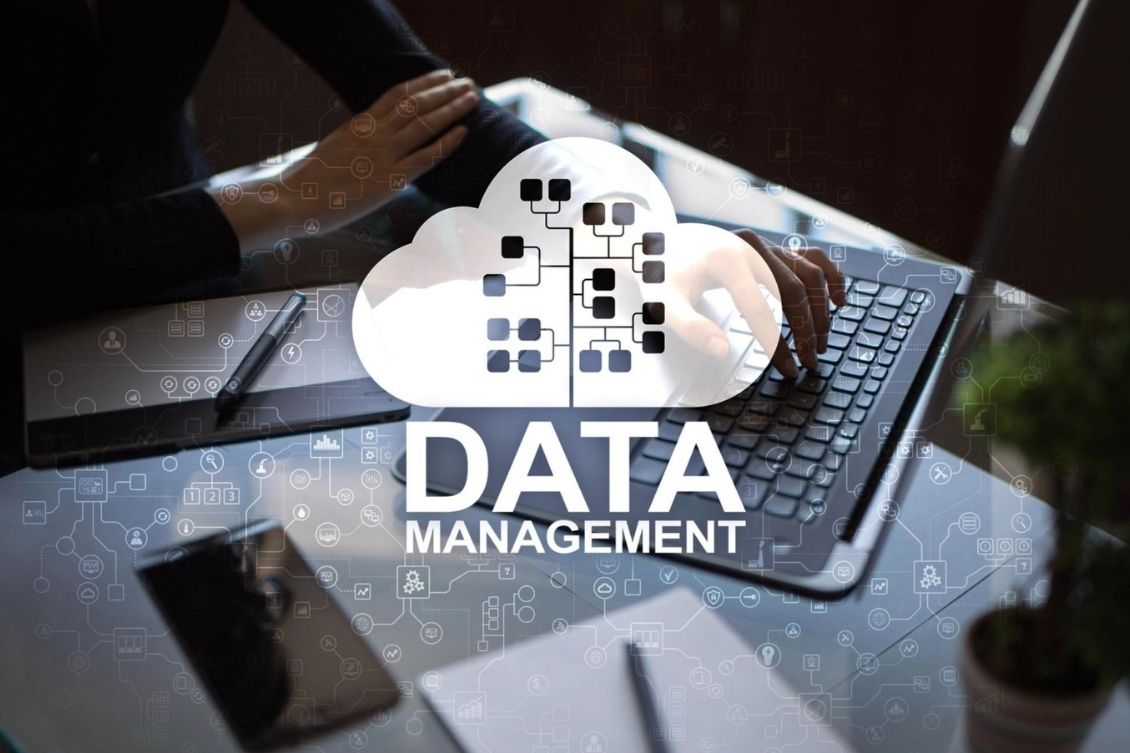
Modern engineering and manufacturing demand speed, agility, and real-time decision-making. Yet, one of the biggest roadblocks to product efficiency and decision-making in product development and manufacturing is the challenge of managing and sharing product data effectively.
Here are some interesting numbers – 68% of CEOs of the largest industrial companies are increasing investments in digital technologies. Only 25% of manufacturers have confidence in how data is organized, traceable, and reliable. And, the last one – only 17% of companies cannot live without their PLM software [Sources: Manufacturing 2030 NAM report, An EY research about trends in discrete manufacturing, CIMdata 2023 market research ].
Engineering teams struggle to communicate critical data with business functions like procurement, manufacturing, and service. This results in inefficiencies, errors, delays, and increased costs.
After 20+ years of PDM and PLM development, these numbers shockingly indicate that something is fundamentally wrong with the industry’s focus on PDM and PLM development, or something is happening with engineering teams and manufacturing companies that drive them into such a problem.
In my article today, I want to help you explore the three biggest problems with product data efficiency and why solving them is crucial for modern manufacturers.
Siloed Product Data Across Teams and Systems
One day, everything was simple—engineers were making drawings and sending them to production planners and manufacturing shops. Those days are over, but what replaced them are siloed engineering systems (aka CAD) that manage design and all related product and engineering data. Life was good with MCAD (mechanical CAD only), and the rest of the systems were somehow less important and less involved. As I heard 25 years ago when visiting one of the leading manufacturers of mobile phones, the right software “somehow magically comes to the right hardware.”
Those days are over. Products are complex and include mechanical, electronic, and software components combined based on rules controlling revisions and changes. One of the most persistent challenges in product development is that engineering data often remains locked in disconnected systems.
Traditional PDM and PLM solutions, while essential for managing CAD files and product structures, typically operate in isolated environments (PDM for MCAD, PDM for ECAD, ALM for software), making it difficult for other teams—such as procurement, manufacturing, and supply chain—to access the latest, most accurate information.
Siloed data creates significant challenges across engineering, procurement, and manufacturing, leading to inefficiencies and costly errors. When engineering releases a design, procurement teams often struggle to access up-to-date BOMs, vendor lists, or part specifications, causing sourcing delays and incorrect orders. Manufacturing teams may work with outdated design revisions, leading to rework, scrap, and production delays. Additionally, the lack of real-time supply chain visibility results in last-minute disruptions, extended lead times, and poor supplier coordination, ultimately increasing costs and reducing operational efficiency.
Lack of Seamless CAD and PLM Integration with Business Systems
CAD and PLM tools play a critical role in product design, but they often fail to integrate smoothly with downstream business applications like ERP, procurement, or inventory management. Historically, PLM companies acquired several PDM/PLM vendors and technically “killed” the PDM business by making every CAD system affiliated with a specific vendor (e.g., SolidWorks PDM, Autodesk Vault, etc.). Furthermore, new “cloud-based” products are also designed so that their data management is forever connected to CAD functions (e.g., PTC Onshape, Dassault 3DEXPERIENCE, Autodesk Fusion, etc.). Each of these siloed systems, lacking integration, forces many manufacturers to rely on manual exports, spreadsheets, or disconnected databases to transfer engineering data into business systems—leading to inefficiencies and errors.
Poor integration leads to slow, error-prone data handoffs, making manual transfers susceptible to inconsistencies, version control issues, and costly mistakes. Without a flexible data model, managing BOM variants, alternate parts, and complex multi-level structures becomes a challenge, slowing down processes and increasing the risk of errors. As a result, engineers spend excessive time reformatting data and troubleshooting integration issues instead of focusing on design and innovation, ultimately reducing efficiency and stifling productivity.
Inflexible and Outdated Product Data Models
Traditional PDM/PLM systems rely on decades-old data models (ORM layers on top of SQL databases). Most of these models were built 25-30 years ago. While these models are robust and scalable, they lack the flexibility and capabilities needed to manage modern product data complexity, which arises from the integration of mechanical, electronic, and software components with increasingly complex product lifecycles—requirements, engineering, manufacturing, supply chain, sales, and maintenance. An additional level of complexity comes from changes in companies’ business strategies—shifting from product manufacturing to service providers, forming joint ventures, or adopting new manufacturing business models.
Today’s manufacturers require multiple BOM types, easy product lifecycle change tracking, and real-time collaboration, allowing engineers in multiple time zones, organizations, and countries to work seamlessly and share data instantly without needing to “synchronize it every 24 hours.” Many existing PDM/PLM systems were designed decades ago and lack the flexibility to support these needs.
Inflexible data models hinder adaptability, making it difficult for companies to introduce new product configurations, customizations, or process improvements due to software limitations. Rigid structures complicate the management of product changes and revisions, leading to challenges in tracking updates and maintaining accurate historical records. Additionally, traditional systems fail to support a connected data ecosystem, preventing the seamless flow of information needed to establish a continuous digital thread from design to manufacturing and service, ultimately limiting innovation and operational efficiency.
Conclusion: The Need for a Modern, Connected Data Platform
To stay competitive, manufacturers must eliminate data silos, improve integration between engineering and business systems, and adopt flexible, adaptable data models. There is a need to provide a scalable and robust data platform that connects multiple disciplines (mechanical, electronic, software), organizes data, and streamlines processes across multiple product lifecycle stages (requirements, engineering, manufacturing, maintenance, and sales). Additionally, companies must connect multiple stakeholders (OEMs, Tier 1-n suppliers, contract manufacturers, and contractors) through a “workspace” that links all of them and brings engineering data into business processes.
Are you experiencing the problems I described in this article? Does it resonate with your day-to-day experience? Please contact us and let us know. We want to discuss and learn more.
Best,
Oleg
Join our newsletter to receive a weekly portion of news, articles, and tips about OpenBOM and our community.