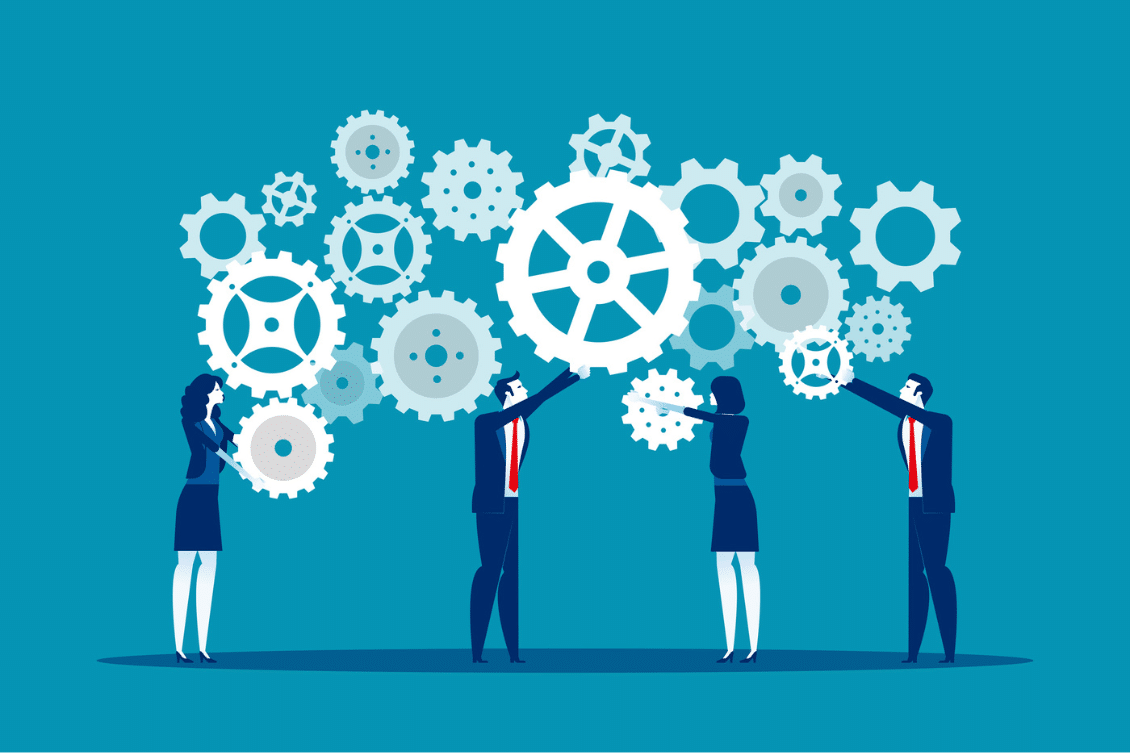
In my previous blog posts, I emphasized the importance of organizing digital information and developing integrated processes using OpenBOM. In the following article, you can check how OpenBOM is organizing a connected new product development process for engineering teams and manufacturing businesses.
OpenBOM New Product Development, and Connected Processes
The main outcome of this transformation is OpenBOM’s Agile New Product development approach, As you can see in the picture below, it allows you to switch from outdated paper (or document) driven process to a connected environment with information seamlessly flowing between team members and applications:
Today, I’d like to share the guidance for the process every company can transition from old-fashioned document-based workflows to integrated process development. To make this transition smoother, it’s essential to break it down into three manageable stages.
Stage 1: Define Data Models for Process
The first step in the journey towards integrated end-to-end process development is defining data models for your processes. This stage involves identifying the key data points and structures that your organization relies on to operate efficiently. These data models act as the foundation upon which your integrated processes will be built. Essentially, you’re creating a blueprint that outlines how information flows within your organization.
Here are typical building blocks you need to focus on.
- Design data, CAD files, requirements, specifications
- Engineering Bill of Materials (BOMs)
- Supply Chain and Sourcing information
- Production planning (work orders and POs)
- Sales information and maintenance data
The data can be prepared in any format, but it is important to be precise and outline all information that is needed in your team or company to do the work.
Stage 2: Organize Automatic Data Capturing Process
Once you have your data models in place, it’s time to focus on automating the data-capturing process. This stage is all about streamlining data entry and retrieval to reduce manual effort and minimize errors. By implementing automation tools and technologies, you can ensure that data is collected accurately and consistently across your organization. This not only saves time but also enhances data quality and accessibility.
The main goal of this process is to optimize time and eliminate mistakes. Although exporting data to Excel can sound like not a big deal, doing it all the time and making mistakes can make a difference. Here is an example of how OpenBOM saves 2 hours of engineering time every day.
There are three main ways to capture data automatically:
- Use OpenBOM integrations (with CAD and other systems)
- Use out-of-the-box imports from spreadsheets
- Use REST API to import data
Stage 3: Define Triggers and Integration Points
The final stage in the journey towards integrated process development is defining triggers and integration points. Here, you identify the specific events or conditions that will initiate actions within your processes. Triggers can be things like receiving an order, reaching a production milestone, or detecting a change in inventory levels. Integration points, on the other hand, are the junctures where different systems or tools come together to facilitate a seamless flow of information. By mapping out these triggers and integration points, you ensure that your processes work cohesively and efficiently.
There is no predefined recipe on how to make it work and the details are dependent on the systems. However, the following main principles are important:
- Identify multiple systems and keys and interfaces to communicate. The main goal here is to define how data can be identified and how data can be passed between multiple systems and teams.
- Identify source of change for each data element – a system where the data can be changed. By doing so, you define a single source of change (a place where each piece of information can be changed, or in other words, the master
- Identify “triggers” or events that will lead to data movements or updates. That will make an entire system operate independently.
Conclusion
Digital transformation is instrumental in improving process efficiency and enhancing decision-making effectiveness. The cornerstone of digital transformation is integrated end-to-end process development. OpenBOM provides a platform that supports integrated process development and offers collaborative tools for New Product Development (NPD) processes, catering to both small and large companies.
By breaking down the journey into these three stages, you can make the transition to integrated process development more manageable and less overwhelming. Remember, you can’t boil the ocean – taking it one step at a time is the key to success in this transformative journey. So, if you’re looking to accelerate your business in 2024, consider embracing integrated end-to-end process development with OpenBOM. Register to learn more and start your journey towards a more efficient and effective future.
REGISTER FOR FREE and start checking OpenBOM for 14 days of free trial. Contact our sales and support to learn more.
Best regards,
Oleg
Join our newsletter to receive a weekly portion of news, articles, and tips about OpenBOM and our community.