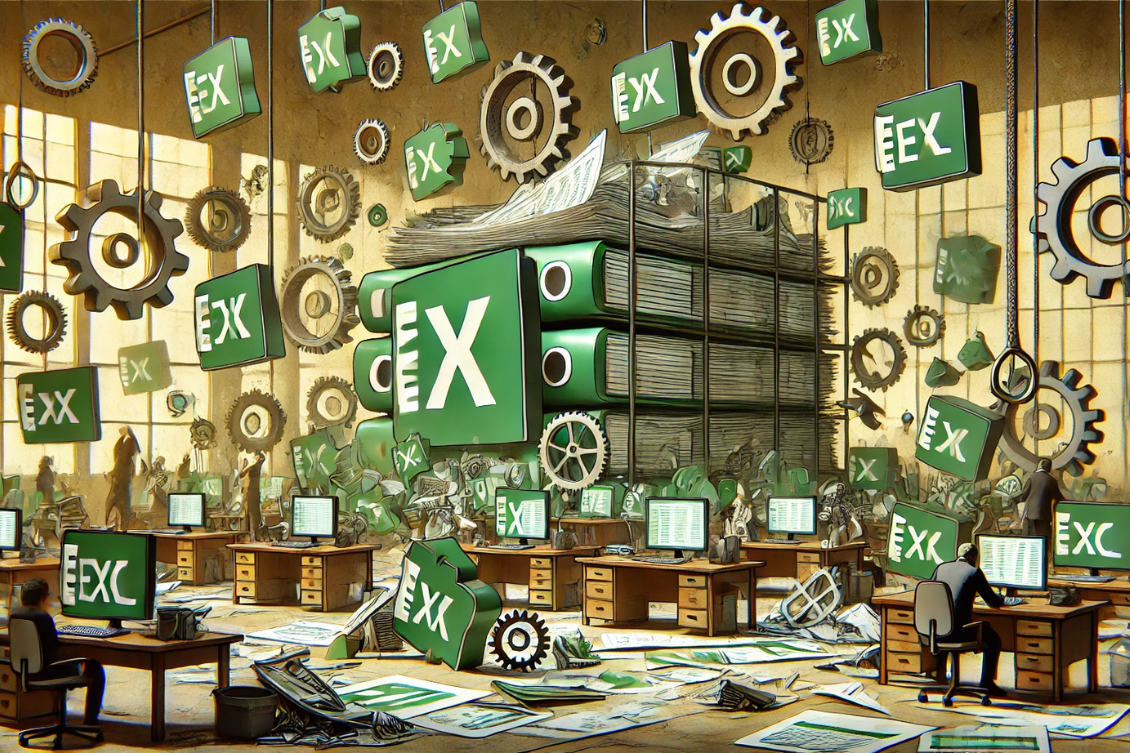
These days, ‘digital transformation’ has become a buzzword for consulting projects focused on digital strategy and implementations. But to truly succeed, it’s essential to strike the right balance between technology and strategy—leveraging initial wins while continuing to refine the overall strategic direction. The right approach ensures that technology supports long-term business objectives, rather than becoming a short-lived solution.
In yesterday’s article Digital Transformation in Manufacturing: How to Accelerate CAD to Quote Process, I shared ideas and strategies on how to bring technology to help manufacturing businesses accelerate their operation and build a new digital value. According to EY research, 68% of CEOs are increasing their investment in digital technologies. But the real question is, what to do with these projects? In the fast-paced world of manufacturing, having a digital transformation strategy is essential, but knowing how to implement it is equally important.
Yesterday, I shared my three-point strategy for digital transformation in discrete manufacturing: (1) digital BOM; (2) seamless design integrations; and (3) connected RFQ and supply chain processes. Like any strategy, there are two key dimensions to consider—technology and business leadership. As with tango, success comes only when both partners are in sync.
Now that you have your strategy, the next question is: How do you execute it? What does adopting digital technology really mean, and how do you avoid the pitfalls that many companies encounter during the transition?
Why Do Companies Fail at Digital Adoption?
Jos Voskuil recently touched on a critical point in his article “Technology is Here, Business Needs to Lead.” His premise is simple but profound: while the technology is ready, many businesses are held back because their leaders aren’t stepping up to guide the transformation. This idea resonates with Peter Drucker’s timeless insight, “Culture eats strategy for breakfast.”
This means that no matter how advanced the technology, if a company’s culture and leadership don’t support it, the transformation will likely fail. If your culture is Excel-ware, don’t expect this culture to disappear just because you bring a new shiny technology. You can’t simply impose new tools without aligning them with the organizational culture and fostering leadership that drives adoption.
Let’s explore the reasons behind this failure and how to avoid it by looking at three distinct approaches to digital technology adoption.
1. Simulate the Analog Process: Speeding Up, But Not Transforming
The first way companies often adopt digital technology is by replicating existing analog processes in a digital format. This might sound practical—it’s quick and doesn’t disrupt the workflow too much. For example, when transitioning from CAD to RFQ, you might digitize your bill of materials (BOM), enabling you to create better reports and share them more quickly via traditional methods like email or file sharing.
While this approach can deliver immediate efficiency gains, it misses the core value of digital transformation. Essentially, you’re using technology to perform the same tasks you did before, just faster. This method doesn’t truly improve your processes or leverage the full potential of the technology—it’s merely digitizing the status quo.
The problem with this approach is that it’s a short-term fix. You may gain speed, but you haven’t fundamentally changed how your organization works, nor have you unlocked new opportunities for innovation. In essence, you’re treating technology as a band-aid rather than as a platform for growth.
2. Forcing the Transformation Without Considering Culture
A common trap that businesses fall into is forcing a digital transformation without considering the readiness of the people who will be using the technology. Imagine a company that implements a new digital BOM system and expects every team—from engineering to procurement—to adopt it immediately without proper training or transition.
This heavy-handed approach can lead to chaos. People resist change, especially when they don’t fully understand how the new system benefits them or when they’re asked to abandon old habits without adequate support. What happens next? Adoption slows down, people revert to their old ways, and eventually, the transformation fails.
True digital transformation is a learning process. It’s not just about the technology itself but how people interact with it. Employees need time to learn and integrate new tools into their daily routines. The key is to implement changes gradually, allowing employees to replace inefficient methods in a step-by-step manner, rather than forcing them to dive into unfamiliar territory all at once. A poorly managed rollout can alienate your team, making the technology feel like a burden rather than a benefit.
3. Building New Digital Value with a Phased Adoption
The most effective way to adopt digital technology is to focus on building new digital business value and doing so in stages. The goal isn’t simply to replace old processes with digital ones but to create a digital assets that serves as a foundation for continuous improvement and future growth.
Take the example of implementing a Digital BOM. Instead of using it just to make paper-based processes faster, imagine how you can leverage the BOM as a living digital asset—one that connects data across engineering, procurement, and supply chain teams. This digital BOM could be the core of a fully integrated, collaborative environment where real-time updates flow seamlessly between departments, offering new insights and driving better decision-making. It can provide you a foundation for some data analysis and in the future will become a digital asset that can be used for processes you never thought about before such as spare parts ordering, costing, risk mitigation, and others.
Phased adoption helps with this. It allows you to introduce digital tools incrementally, giving employees time to adapt at each stage. Each phase builds on the success of the previous one, progressively transforming your operations and helping your team see the tangible benefits of the new system. This approach fosters a culture of innovation, where people are not just users of the system but active participants in its evolution.
By adopting this mindset, digital transformation becomes more than just a tech upgrade—it becomes a catalyst for reshaping the way your company operates, setting you up for long-term success.
Conclusion: Focus on Vision, Value, and Leadership
Digital transformation is not about jumping on the latest technology trend or replicating outdated processes with new tools. It requires a strategic vision, thoughtful leadership, and a clear focus on value creation. Companies that rush into digital adoption without considering culture or planning for phased implementation risk alienating their employees and missing out on the full benefits of digital innovation.
Successful digital adoption requires a combination of leadership that understands the importance of gradual transformation and a culture that supports learning and change. Ultimately, it’s about creating new value, not just faster results. The right approach will help your organization unlock the full potential of digital technologies, creating a foundation for future success in a fast-evolving industry.
Are you looking for a strategy to start your digital transformation project and use OpenBOM? Follow these simple steps – REGISTER FOR FREE and contact OpenBOM for onboarding service, which includes digital transformation guidance.
Best, Oleg
Join our newsletter to receive a weekly portion of news, articles, and tips about OpenBOM and our community.