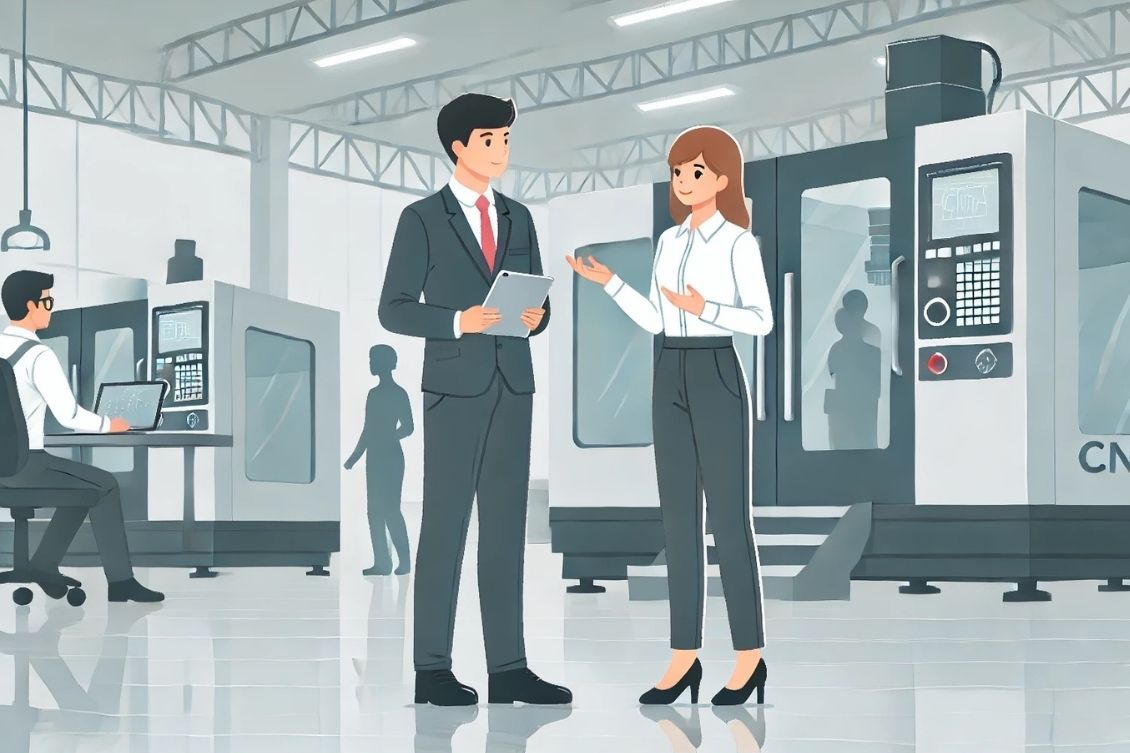
Sharing product data with your contract manufacturer (CM) is a critical step in turning your design into a physical product. However, sending over a detailed Bill of Materials (BOM), CAD files, or assembly instructions without proper preparation can lead to miscommunication, costly mistakes, and even production delays.
Think about it, if your CM doesn’t understand your specifications or makes assumptions about materials, you might end up with the wrong parts or a product that doesn’t meet your standards. Avoiding these pitfalls starts with asking the right questions upfront.
In this blog, we’ll explore four essential questions to ask your contract manufacturer before sharing your product data. These questions will help you clarify expectations, protect your intellectual property, and set the stage for a successful partnership.
Question 1: What Data Formats Do You Require?
Sharing product data is more than just sending files, it’s about ensuring your CM can easily interpret and use the information you provide. Different manufacturers work with various tools and systems, so understanding their preferred data formats is essential.
For example, some CMs might require CAD files in STEP or IGES formats for compatibility with their software, while others might need 2D drawings or structured BOMs in specific templates. If your data isn’t in the right format, you risk delays, misinterpretation, or additional costs for reformatting.
While Excel spreadsheets are commonly used to share BOMs and product data, relying solely on this format can lead to version control issues and human errors. Additionally, while Google Drive or Google Spreadsheets might seem like a convenient option for sharing and collaborating, keep in mind that Google services are blocked in countries like China. If your CM operates in China or other regions with restricted access, sharing via Google Drive could result in significant communication delays or data access issues.
Here is how you can approach this:
- Ask directly: Confirm the exact formats your CM needs for CAD files, BOMs, and other documents.
- Provide alternatives: If your CM is in a region where Google services are blocked, consider using neutral formats like Excel or sharing data through a secure, cloud-based platform like OpenBOM.
- Ensure accessibility: Make sure the chosen data-sharing method aligns with your CM’s location and technical capabilities.
By understanding your CM’s format preferences and regional limitations, you can avoid unnecessary hurdles, ensure data accessibility, and create a smoother path for collaboration.
Question 2: What Level of Detail Do You Need in the BOM?
A well-structured BOM is the foundation of a successful collaboration with your CM. However, not all manufacturers require the same level of detail, and providing too much or too little information can create confusion, errors, or delays.
For example, some CMs may need only high-level details like part numbers, quantities, and material types. Others might require a granular breakdown, including sourcing information, manufacturing tolerances, and assembly instructions. The key is to strike the right balance, providing enough detail for clarity without overwhelming your CM with unnecessary information.
Here is how you can approach this:
- Ask for a checklist: Request a detailed list of what your CM expects in the BOM. This might include part descriptions, material specifications, lead times, or even alternative components.
- Tailor your BOM: Customize the level of detail to meet your CM’s needs while keeping it clear and organized. Tools like OpenBOM can help streamline this process and ensure no critical details are overlooked.
- Verify completeness: Before sending your BOM, confirm it includes essential elements like unit measurements, revision numbers, and any critical notes for production.
A clear and concise BOM ensures that your CM has everything they need to proceed confidently with production, reducing the risk of miscommunication and costly mistakes. It also sets the stage for a more productive partnership.
Question 3: How Do You Handle Changes to Product Data?
In manufacturing, changes to product data are almost inevitable, whether it’s a last-minute design tweak, a material substitution, or a revision to assembly instructions. How these changes are communicated and managed can make or break the production process. Mismanaged updates can lead to outdated files, incorrect parts, or wasted resources, all of which can be costly and time-consuming to fix.
CMs often rely on the most recent data to guide production. If they don’t have a clear process for handling revisions, your changes might not be implemented in time, causing production delays or errors.
Here is how you can approach this:
- Ask about version control: Does your CM have a system in place to track and implement data changes? This could include document control software or cloud-based collaboration tools.
- Clarify the process: Find out how your CM prefers to receive updates—whether through updated CAD files, a new BOM revision, or a formal engineering change order (ECO).
- Set expectations: Agree on a protocol for notifying and confirming changes. For instance, using a platform like OpenBOM allows you to update product data in real-time, ensuring your CM always has access to the latest version.
- Pro Tip: Make sure any changes are documented clearly, with revision numbers, effective dates, and notes explaining the update. This reduces confusion and keeps everyone aligned.
By understanding your CM’s approach to handling changes, you can establish a smooth and reliable workflow, ensuring that updates are implemented seamlessly and production stays on track.
Question 4: How Do You Ensure Data Security and Confidentiality?
When sharing your product data with a CM you’re entrusting them with your intellectual property (IP), one of your business’s most valuable assets. Ensuring that this information is protected from unauthorized access or leaks is critical to safeguarding your competitive edge and maintaining customer trust.
Without proper security measures, sensitive data like CAD files, BOMs, or proprietary processes could be exposed, leading to risks such as counterfeiting, unauthorized distribution, or loss of competitive advantage.
Here is how you can approach this:
- Ask about their data protection policies: Confirm if they follow industry-standard security protocols, such as encryption, access control, and secure file transfer methods.
- Inquire about NDAs: Ensure your CM is willing to sign a Non-Disclosure Agreement (NDA) that explicitly outlines how your data will be used and protected.
- Understand their storage practices: Where and how will your data be stored? For example, is it on secure servers with limited access, or in a cloud environment with stringent cybersecurity measures?
- Evaluate compliance certifications: Check if the CM complies with international standards like ISO 27001 for information security or ITAR regulations if applicable.
- Pro Tip: Use tools like OpenBOM, which offer secure, cloud-based collaboration and version control, reducing the risks associated with traditional file-sharing methods like email or USB drives.
Establishing clear expectations around data security and confidentiality not only protects your IP but also builds trust with your CM. It ensures that your collaboration is not only productive but also secure from start to finish.
Conclusion
Working with a CM can be a game-changer for scaling your production, but the success of your partnership hinges on clear communication and thorough preparation. Asking the right questions before sharing your product data ensures that both you and your CM are aligned on expectations, processes, and priorities.
By addressing topics like data formats, BOM details, change management, production workflows, and data security, you can minimize misunderstandings and set the stage for a seamless collaboration. Remember, the effort you invest in these discussions upfront can save you time, money, and headaches down the line.
Ultimately, a proactive approach fosters trust and builds a foundation for a strong and productive relationship with your CM, helping you bring your products to market with confidence.
By: Jared Haw
Join our newsletter to receive a weekly portion of news, articles, and tips about OpenBOM and our community.