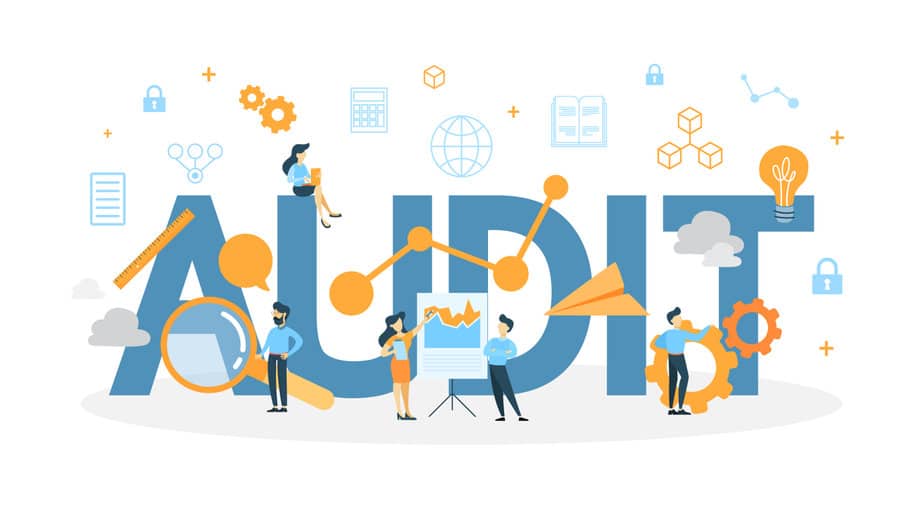
Do you feel safe placing orders to a vendor you have never met or audited? I guess it depends on the type of vendor. If you are procuring parts from a well-known vendor then not visiting and auditing their facility is ok. However, if you are searching for a contract manufacturer (CM) or another key supplier then auditing their facilities is important. Especially if there is no strong referral.
When you are evaluating a new vendor, one of the final steps is to audit them. Lately, companies have been blaming COVID for not being able to audit suppliers. However, you can hire a 3rd party vendor to audit your CM on your behalf. ChinaImportal.com provides a list of those companies.
Here are four reasons why you do not want to miss out on auditing your supplier.
1. Seeing is Believing
Sometimes what a CM shows on their website or provides in their marketing material is not always what you get. Auditing them will show you exactly what they have. Here are some points you will need to look out for.
- Do they have adequate machines and assembly lines for your product?
- Are the work areas clean?
- Do the machines have work instructions up?
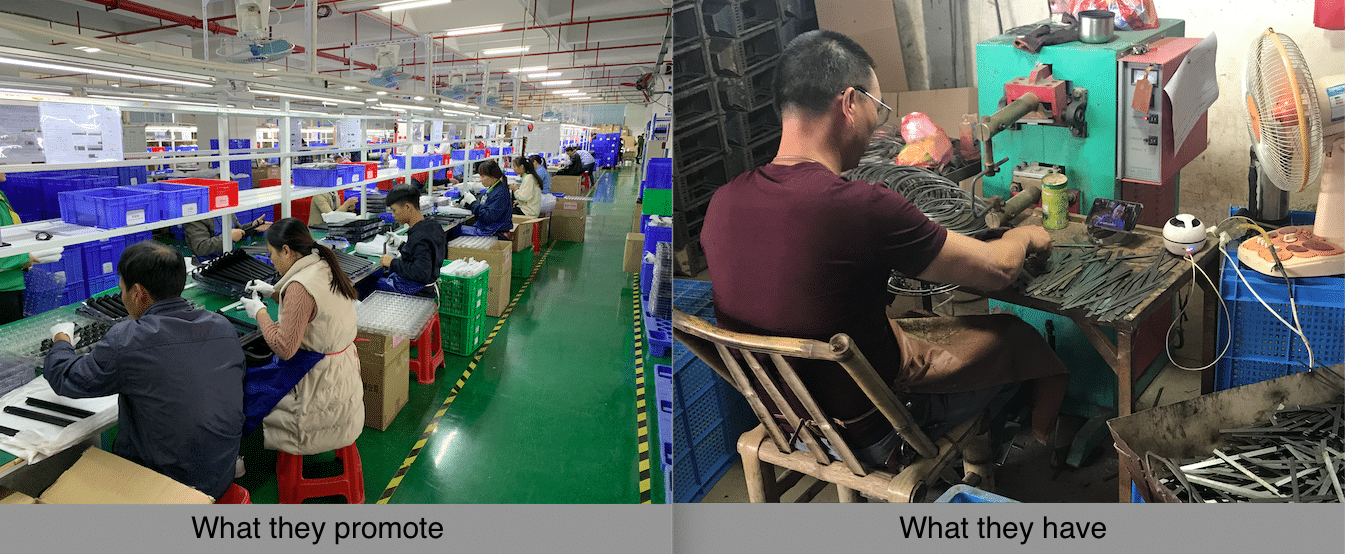
2. Identify Areas of Risk
Auditing your CM will help you to identify areas of risk in their production, engineering, quality, supply chain, and overall processes. Identify these areas of risk and evaluate their significance to you.
Some questions or places to look to identify areas of risk are the following:
- Do they have work instructions up in each assembly/fabrication area?
- Can they provide quality reports for any product?
- Are the non-conforming parts areas clearly identified?
- How do they deal with engineering change orders?
3. Get to know the Team
Since the pandemic, we have had to make do with web calls. However, nothing can replace meeting someone face to face.
When you meet the team in person, you can quickly bond with them and start to build a relationship with them.
When you meet the team you can get a better understanding of their engineering & technical team, their production confidence, their attitude to your product, and more. You will also understand better how willing they are to take on your project.
If you hire a 3rd party to audit your CM, they will report back to you about their experience of dealing with them. With their experience, they will also advise whether or not the CM has the correct mindset to build your product.
4. Understand their Processes
There are multiple parts of the manufacturing process, it’s not just about production. Before you work with a CM or a supplier, you need to understand more about the following:
- Can they support you with design for manufacturing (DFM)?
- What is their typical request for quotation (RFQ) process?
- How can they support you with the new product introduction (NPI) process?
- How do they have a corrective action plan for all parts with quality defects?
- What certificates do they have and do they follow the guidelines?
You can gather most of this information on a call or through multiple calls, there is still nothing that replaces visiting your supplier. While certain countries are still closed due to the pandemic, there are also multiple 3rd party companies that have the capabilities to audit a supplier on your behalf.
What Can You Do Today?
Regardless of who you are working with and the maturity of your product, you will need to manage our product information. You will also need to make this data readily available to your team at all times.
A centralized platform that connects your team, contractors, and suppliers is your solution. This creates a single source of truth and eliminates mistakes.
OpenBOM is a cloud-based platform to manage your engineering and manufacturing data. Companies from startups to Fortune 500’s use OpenBOM to create a centralized database to bring in, store and manage their manufacturing data. With this infrastructure, users also use OpenBOM to streamline both their change management and PO processes.
If you need to improve the way you manage your data and processes, contact us today for a free consultation.
Regards,
Jared Haw
Join our newsletter to receive a weekly portion of news, articles, and tips about OpenBOM and our community.