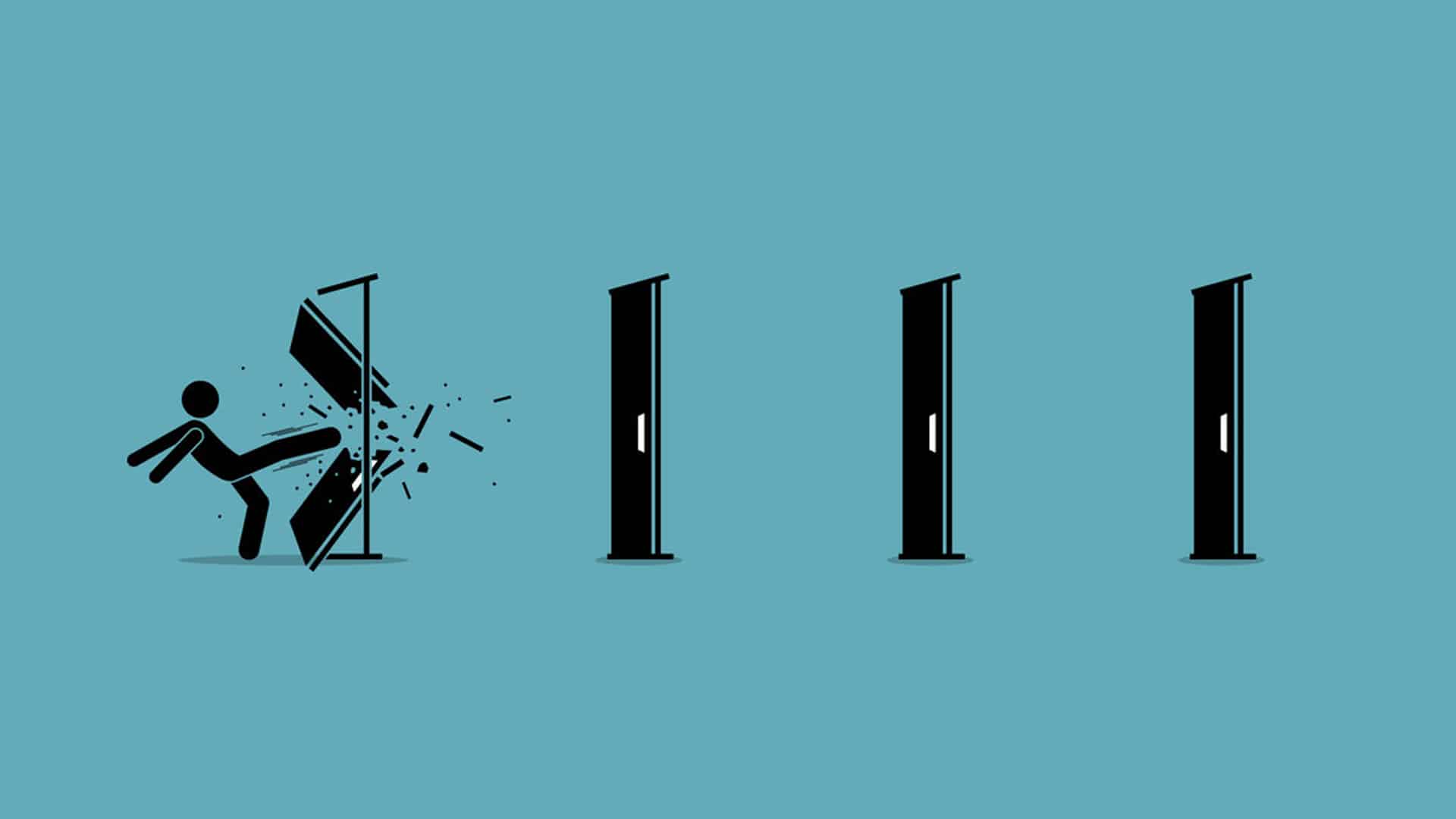
A New Product Introduction (NPI) includes all the activities within an industrial company to define, develop and launch a new or improved product. The steps taken to take those ideas from the idea stage to market is known as the New Product Introduction (NPI) process.
As companies seek to stay competitive, they listen and react to feedback from their clients. This usually entails developing new products. During the early brainstorming process, your company will compile a list of potential products that they can sell to their existing market.
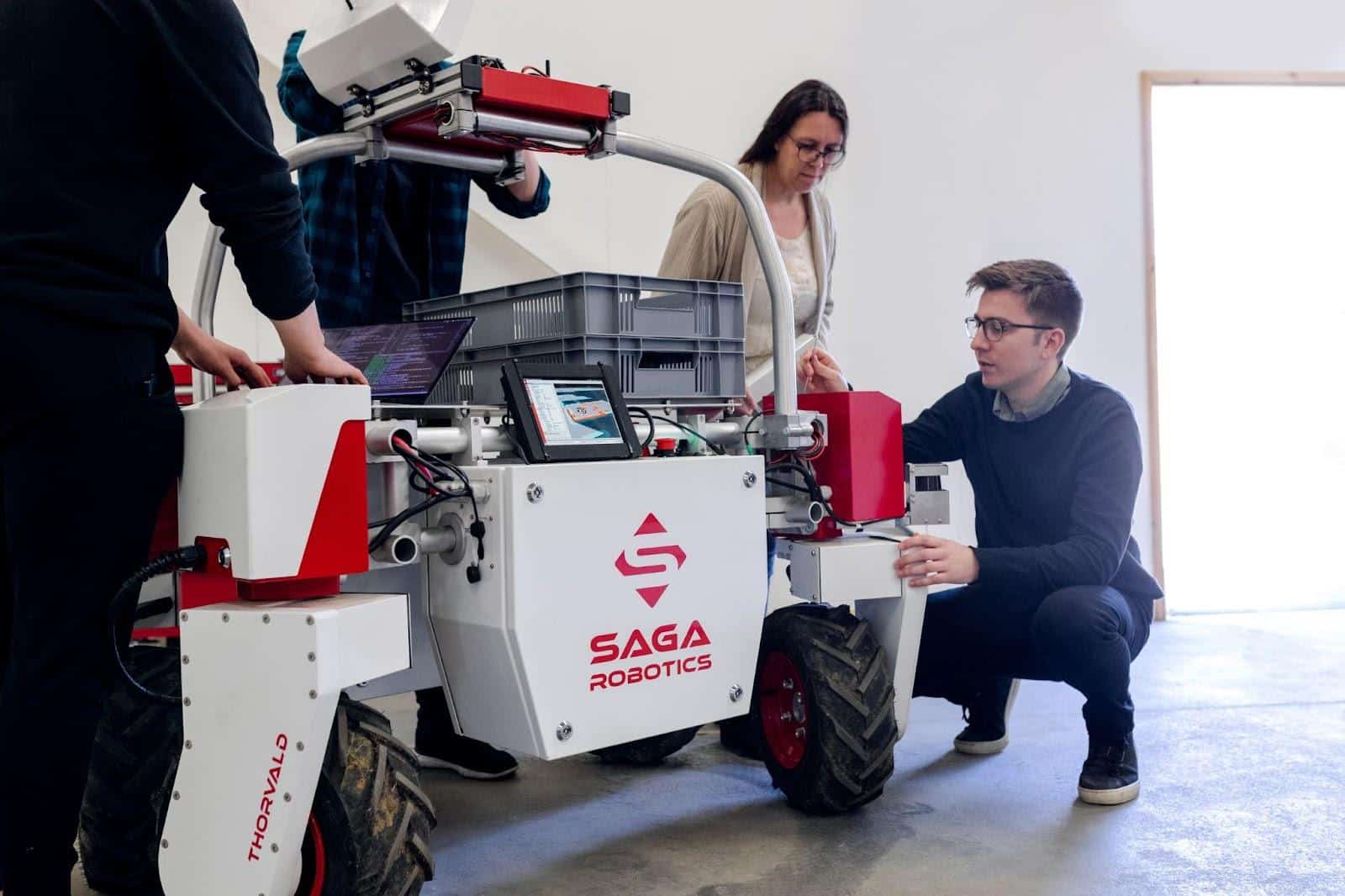
With the introduction of crowdfunding campaigns, entrepreneurs now have a platform to introduce their products to the market during the product development phase. Sometimes they just don’t work out, like the Coolest Cooler. They shut down and left 20,000 backers without their product. A huge failure.
Unfortunately, most new product launches fail. According to Sofeast, “around 90% of new products manufactured in China fail on at least one objective (timing, quality, cost).” The manufacturing feasibility of a product is defined during the NPI process.

Source: Kickstarter
To maximize your efficiency during the NPI process, you will be leveraging the knowledge of other organizations throughout the process. Along with your internal team, you will be working with external suppliers, contract manufacturers, and others to leverage their knowledge and to bring your product to life as efficiently as possible. Failing to work with the correct team and choosing the wrong partners will hinder your overall success.
Roadblocks to a Successful NPI
There are several roadblocks we have seen that hinder you from a successful product launch.
Quality Issues
Let’s be honest, there will be quality problems. However, having the correct processes in place and having a team that can identify a problem and finds the corrective action is key to your success. Doing the due diligence to create objective quality standards is something else that is forgotten about during the NPI process.
Increased Cost
A common trend we see is that everyone wants to use the highest quality parts, but they are not willing to pay for the costs associated with those. Not having a team that understands the production processes and materials used in mass production will end in increased costs. Design for manufacturing and Assembly (DFMA) is an important part of optimizing each part to be fabricated and assembled during production. Skipping these steps will lead to increased costs amongst other problems.
Prototype to Scale Up
Creating a prototype to show investors, executives, key accounts, or to create a crowdfunding campaign can be done. It’s usually high touch and a lot of time is spent on making this one prototype perfect. But how do you transition a high-touch prototype into something that can be scaled and made repeatedly at high volumes on a production line?
Managing your Data
One part that slows down the NPI process is managing or updating all of your engineering and manufacturing data and files. This includes your contract manufacturer (CM) requesting a change to a part to optimize it for tooling and to have the part be changed on the bill of materials (BOM), drawings (2D and 3D), and all of the other specification changes that come with it. And then how do you distribute this to others? Mistakes happen manually.
Breaking down the roadblocks for a successful NPI
To streamline your workflows from idea to shipment, you will need to follow some processes and adapt the way you work. Here is what you can do to break down the roadblocks for a successful NPI.
Choose your Partners Wisely
Work with companies that have an advantage in something that you do not have. In other words, who can you leverage to ensure a successful product launch?
Change & Approval Process
Manually sending files to all of the stakeholders is tedious. Managing this is not any easier especially with a high BOM count. Using software to automate your change and approval process will reduce the number of man-hours spent on non-value-added activities.
Create your Production & Quality Documents
Make sure all of the documents, from the assembly guidelines through to the final functional tests, are objective. For example, calling a plastic part blue is not objective. Define a Pantone. This is the same for the quality specifications for each item and final assembly.
Work on a Centralized Database in Real-Time
Excels and spreadsheets have served a purpose but it creates documents that are not linked together, nor can they be linked to other files you are working with. Working on a centralized system will bring you closer to all of your team members, and contractors saving hours on manual tasks.
How OpenBOM Can Help?
OpenBOM believes engineering, supply chain, and manufacturing teams should be able to seamlessly manage their parts, vendors, bill of materials, purchase orders, and change orders. All BOM, engineering, and manufacturing information are stored in the cloud which you can share with your team, contractors, suppliers, or anyone else that has access to your account. OpenBOM keeps everyone on the same BOM while providing you with the tools to streamline your development to production & scale up operations.
Register for FREE to create your OpenBOM account and reach out to us via support @ openbom dot com if you have any questions.
Best,
Jared Haw
Join our newsletter to receive a weekly portion of news, articles, and tips about OpenBOM and our community.