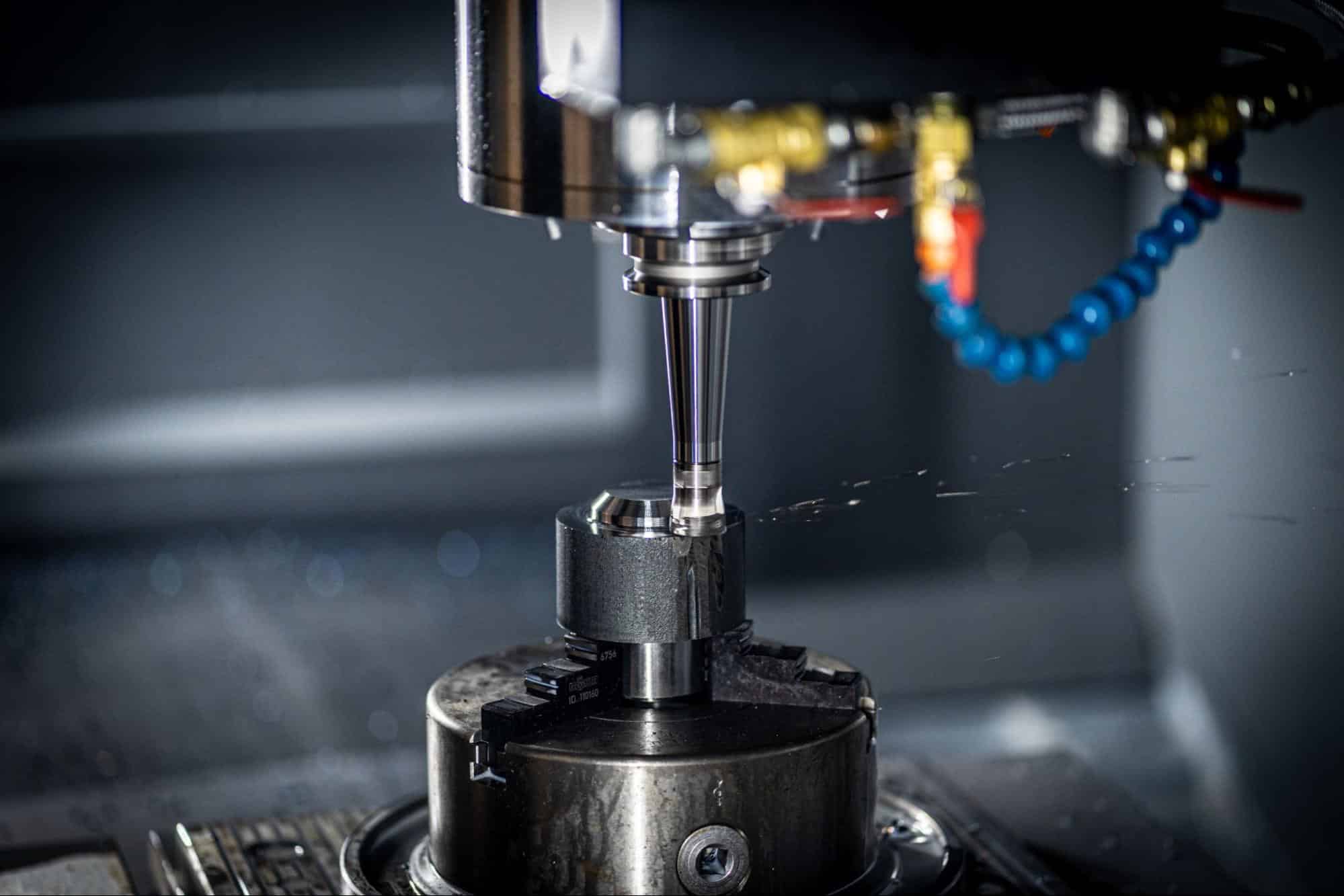
Working with a Contract Manufacturer can make your business thrive or can give your product a death sentence. With every company in the manufacturing business, you want to choose the right CM to work with. Leo Tolstoy famously said that all happy families are alike, but every unhappy family is unhappy in its own way. It is different in manufacturing. I found a few important traits or trends that are off-putting. Perhaps you did not go through the proper selection process or you have inherited a contract manufacturer with some bad trends. In this blog, I’d like to outline 4 bad trends of any company, that will be the signs for the larger concerns.
SOPs/WIs are not visible
This is probably the most fundamental but most often overlooked problem. Standard Operating Procedures (SOPs) or Work Instructions (WIs) provide a step-by-step guide of how to assemble or fabricate the part. Without these instructions, how do you know if you are assembling it correctly?
The general response from the general manager is that the workers know what they are doing and they don’t need it. But is that really true? Operators and line operators tend to have a high turnover rate. How can you guarantee with this turnover that the workers know exactly how to fabricate this part or to assemble it.
Contract Manufacturers, tier 2 and tier 3 suppliers without the correct SOPs and WIs tend to be a red flag.
Production Department Trumps the Quality Department
The production and quality departments usually get into heated arguments about the quality of a product. This is acceptable and is perfectly fine. Production wants to meet their daily shipping quota while quality has no problem delaying to ensure quality is acceptable. Both are good and both are doing their jobs.
However, I have seen a good amount of factories when the quality department is placed in the production department… This means that the quality supervisor’s manager will be the production manager. During these arguments, who do you think will win 100% of the time?
The quality department should be separated from the production department. They can report to the same manager or the GM but having the quality department under the production department will give the upper hand to the production department every day.
Dirty Floors and Offices
I had a client that would walk into every single bathroom when we visited suppliers together. He felt that if the workers did not have a decent place to use the restroom that the management team did not care about them. If the management team does not care about them then how do they retain good workers?
While I felt this was a unique way of looking at things, I also thought he was spot on. For a supplier to keep a clean and tidy work area and office is not expensive, nor is it hard work. It shows that you have respect for yourself, your workers, and your clients. More often than not, a supplier with a clean and tidy work environment will be a higher valued supplier.
Communication
The biggest complaint I hear about contract manufacturers and suppliers is their lack of communication. This is true and has always been a hurdle. However, a contract manufacturer that lacks adequate communication skills will usually leave answers pending much longer than they should be, don’t provide detailed answers, and leave emails or messages unanswered for days.
In any business, communication is very important. When you are on the other side of the world, it becomes even more important. If your supplier lacks communication then you can also assume there will be gaps with the quality standard, work instructions, design, overall planning, and more.
What is OpenBOM?
OpenBOM believes engineering, supply chain, and manufacturing teams should be able to seamlessly manage their parts, vendors, bill of materials, purchase orders, and change orders. All BOM, engineering, and manufacturing information are stored in the cloud which you can share with your team, contractors, suppliers, or anyone else that has access to your account. OpenBOM keeps everyone on the same BOM while providing you with the tools to streamline your development to production & scale up operations.
Register for FREE to create your OpenBOM account and reach out to us via support @ openbom dot com if you have any questions.
Best,
Jared Haw
Join our newsletter to receive a weekly portion of news, articles, and tips about OpenBOM and our community.