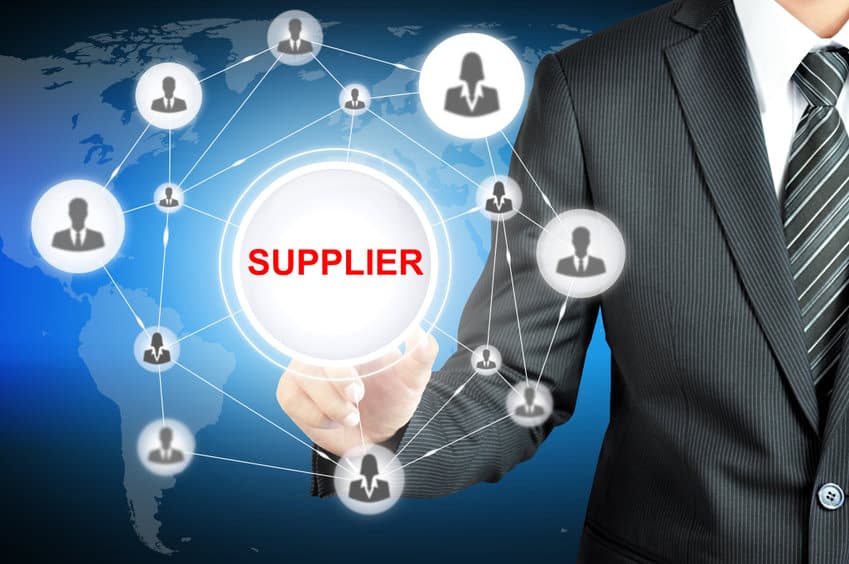
When manufacturers are looking to scale up production, one of the key considerations is working with the right supplier. One goal of developing a product is to distribute it to the masses. It’s the goal of all product-based companies to sell to as many people within their market segment as possible.
The most obvious thing you need to do to sell more products is to make those products. You will need to scale up production.
It’s quite common to see a product for the first time and think that the product came out of nowhere. While this sounds nice, it’s never the case. Scaling up production does not happen overnight. It takes a proper strategy that is paired with execution.
Here are four steps I have seen consistently that lead to a successful production scale-up.
1- Get your Quality Under Control
Any quality problems during prototyping and low volume production must be straightened out. You simply can not scale a product with quality issues.
One of the goals of design for manufacturing (DFM) is to improve the quality of the product. Having a product with multiple different parts that are dependent on each other increases the risk of a potential quality defect. During DFM, you identify the potential risk and eliminate it.
The risks of trying to scale a product with quality problems are the following:
- High reject rate
- Added costs of re-work
- Extended lead time & delayed shipments
- Shipping products with defects
Also, remember that quality problems will come up. However, there are certain quality steps you and your supplier can take to eliminate these problems from occurring again and again.
2- Understand your Costs to Scale Up Production
You need cash to scale up production. One benefit of scaling up production is reaching economies of scale. However, you still need enough money to place the order. And depending on the relationship you have with the supplier, they may not provide very favorable payment terms if there is no history of credit.
Depending on how you launched production, you might have used low-grade material for tooling to save on initial costs. You could have also used different fabrication methods to lower tooling costs. Think of 3D printing instead of injection molding or CNC’ing parts instead of die-cast.
While these low-volume methods of fabricating parts worked, they won’t work for scaling up production. The reason for this is that the supplier won’t have the capacity and because of the higher cost. Thus, the introduction of tooling.
Here are some costs associated with scaling up production:
- COGS. While this number does go down per unit, the total value increases. Make sure you analyze your cash flow here.
- Mass Production Tooling
- Assembly Fixtures/jigs
- Training of workers and operators
In the next part, we will look at automation, which is also a type of investment. However, due to the importance of introducing automation, it makes sense to have it as its own topic.
3- Introduce Automation
The purpose of automation is to increase the output of a consistent product at a lower price. When most of us think automation, we think of industrial robots. However, most automation is there to support the human touch. Such as automating specific sub-assembly steps.
When introducing automation, you want to locate areas of the production and assembly process that are a bottleneck. Some of these bottlenecks can be eliminated by breaking up the processes, changing the workflow, adding people, or automating the process.
4- Purchase Reliable Parts
In manufacturing, quick fixes are not reliable, nor are they sustainable. While looking for alternative components to save costs seems like a good idea, there are risks associated with it. Cutting corners to procure a cheaper part can potentially damage your brand and create a product no one wants.
Also, there are some brand components you must use. For example, if you are manufacturing a bike, you will most likely use Shimano because of brand recognition. While other alternatives will be cheaper, there are too many risks associated with using an alternative. Those come from both the customers themselves and the overall quality.
Again, finding alternatives is a great idea but they must be tested and approved before moving into production and threatening your scale-up plan.
What Can You Do Today?
Before you scale up production, it is a must to have your processes in order. During development, there will be multiple changes, prototypes, vendors, and more that you need to manage. Using excels creates a case where everyone is working on different data. That is where mistakes happen.
A centralized platform that connects your team, contractors, and suppliers is your solution. This creates a single source of truth and eliminates mistakes.
OpenBOM is a cloud-native data management and collaboration platform to manage your engineering and manufacturing data. Companies from startups to Fortune 500’s use OpenBOM to create a centralized database to bring in, store and manage their manufacturing data. With this infrastructure, users also use OpenBOM to streamline both their change management and PO processes.
If you need to improve the way you manage your data and processes, contact us today for a free consultation.
Regards,
Jared Haw
Join our newsletter to receive a weekly portion of news, articles, and tips about OpenBOM and our community.