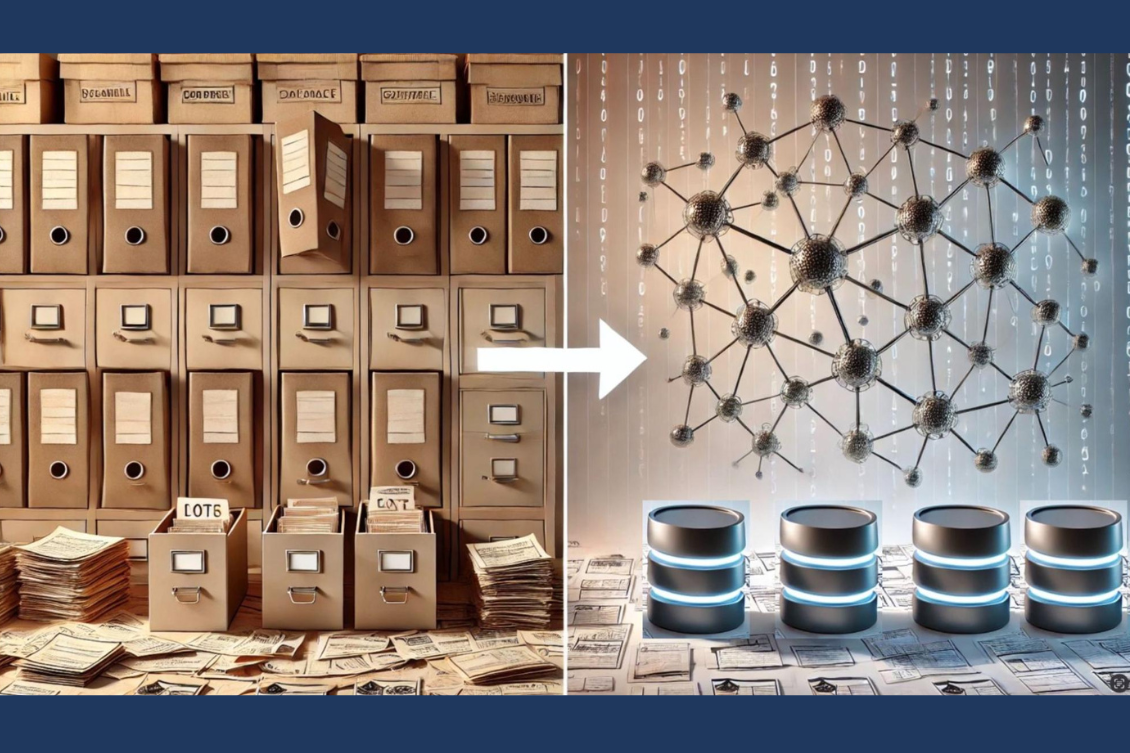
Data management in today’s digital age is absolutely important to help your business to thrive and not die. The “garbage in, garbage out” rule remains timeless: if you don’t manage your data properly, you’ll inevitably face delays, mistakes, and additional costs.
Ignoring data management in the 2020s is a bit like trying to run a library in the 1800s without a catalog: “Imagine a 19th-century librarian piling up books in random order, convinced sheer memory will suffice. Fast forward to today, and not organizing data is like having every book in the world scattered on the library floor—try finding ‘War and Peace’ when you need it!”
Things can indeed get chaotic without a structured approach to data management. In the past, libraries evolved with card catalogs and classification systems. Today’s data-driven world demands even more robust systems, capable of keeping up with fast-evolving digital information.
But despite all these obvious things, the status of engineering and manufacturing businesses remains very addicted to ignoring many best practices and data management systems. To their defense, many PDM/PLM systems were designed to very large enterprises and too complex and too costly to be used by small and medium manufacturers and also by small and agile engineering teams in large enterprises. So, they are using various DIY tools, shared drives, Excel sheets and other forms of unorganized data.
I just came from Germany where I met friends and colleagues working with industrial companies of different sizes. The following remark stuck in my head – every company does some data management and product planning using spreadsheets (or Excel).
Let’s talk about it and what best practices can help you to improve data management.
Why is Data Management Adoption Still Challenging?
While everyone agrees on the importance of data management, putting it into practice often lags far behind. Why? Years of experience have shown me that human nature is a significant factor. People aren’t naturally inclined toward systematic decision-making, often favoring immediate needs over long-term organization. This can leave successors dealing with an unsorted mess—data that lacks any logical structure or proper identifiers. These challenges add to the cost when companies try to transition to a more structured way of managing information
When it comes to engineers, the situation is tough. I admire engineers for the brilliance of the solutions and technologies they developed. At the same time, I’m amazed every day again, when engineers work hard to organize their product information using Excel. I can tell you – it can work for a single person. It can even work for a small group of people for some time, but you will start seeing cracks in these spreadsheets-based methods.
Modern product development with complex products including mechanical, electrical, software, and other systems is not a good fit for a spreadsheet you export from your CAD systems and file stored in the disc. Even if Excel helps you to make some smart calculations (which is btw very important to do). Working closely with many manufacturing companies, I’ve observed recurring patterns of mistakes and pitfalls (often unintentional).
In this article, I want to outline five best practices that any company, large or small, can adopt to leave behind the “spreadsheet planning chaos” and embrace a more organized approach to data management.
Five Key Practices of Data Management
Identification and Part Numbers
Assigning unique part numbers to everything you manage is an essential first step: items, documents, change orders, RFQs, POs—the list goes on. This isn’t a debate about “smart” vs. “dumb” part numbers; the critical factor here is creating a systematic approach to identifying all your key components and records. Proper identification and categorization of these parts is a foundational step to managing and accessing data consistently.
Imagine having a specific identifier for every item, so when you need to retrieve information on a component or document, there’s no ambiguity. By establishing a clear numbering system early on, you’re setting your organization up to save time, reduce errors, and simplify the process of accessing and analyzing data.
Data Storage
Centralized data storage doesn’t mean cramming everything into a single database, system, or folder. Rather, it’s about having a coordinated strategy where data and files are easily identifiable and managed under a unified framework, regardless of where they reside. A centralized approach allows you to get a complete picture of your product data, avoiding fragmented silos of information.
For instance, a multi-disciplinary Bill of Materials (BOM) can pull together every critical element of your product—mechanical, electronics, and software components—in one view. Instead of struggling with multiple exported Excel sheets from MCAD, ECAD, and ALM tools, you have a single source of truth. This “big picture” approach enables you to make more informed decisions and enhances collaboration across teams.
Cross-Department and Cross-Company Collaboration
Product data is most valuable when it’s accessible across the entire organization. It should be readily available to any department or even to partners outside the company without requiring tedious copying or exporting. Effective collaboration means that data can flow seamlessly across functions and locations, allowing engineers, designers, procurement, and manufacturing teams to work from the same set of information.
Think of it as a digital ecosystem where everyone accesses the data they need without creating duplicates or struggling with version control issues. This practice saves time, reduces errors, and helps align everyone toward the same goals, making it a critical piece of efficient data management.
Data Integrity and Version Control
Data integrity and version control are non-negotiable in any modern data management strategy. Without a clear history of changes, traceability becomes nearly impossible. You need to know exactly which component was included in a product you delivered to a customer two years ago or which supplier provided parts for a specific batch. Version control practices help maintain an accurate history of product changes, ensuring that you can trace every decision and every update.
A strong version control system allows you to answer questions about product history instantly, which is critical for compliance, quality assurance, and customer support. Maintaining this integrity across your data sets is what sets apart a reliable data management strategy from one that could leave you in the dark when an issue arises.
Flexible Data Modeling
Nothing stays the same forever. As your business grows and evolves, so will your data management needs. A flexible data model is essential to accommodate changes, whether they involve adding new attributes, introducing new data objects, or expanding business processes. Even if an out-of-the-box system suits your needs today, you’ll need one that can evolve over time to adapt to future requirements.
A robust, adaptable data model will support your company’s growth by allowing new dimensions of data to be captured without needing a complete overhaul. By planning for flexibility now, you’re building a foundation that will serve your organization as it adapts to future business and market demands.
Conclusion and Next Steps
Don’t let data manage you. Instead, you need to figure out how to manage your company data before it turns into a chaotic disaster.
Data management has come a long way since the days of paper engineering drawings piled in back offices. Back then, companies still had organizational methods—folders, filing cabinets, and librarians—to ensure information was properly classified. But today, as data volumes explode, not managing data properly could lead to severe operational and financial consequences.
It might seem convenient to let engineers handle data informally with spreadsheets, hoping to locate the correct Excel file with the right part or supplier information when needed. But hope is not a strategy. As your competitors adopt intelligent, automated data management practices, the cost of relying on outdated methods only increases.
Modern data management empowers you to access, update, and share the latest information instantly, eliminating “version roulette” and the risk of costly mistakes. With tools like OpenBOM, you can harness best practices for today’s data-driven world.
REGISTER FOR FREE and explore how OpenBOM can help your organization move from reactive to proactive data management.
Best, Oleg
Join our newsletter to receive a weekly portion of news, articles, and tips about OpenBOM and our community.