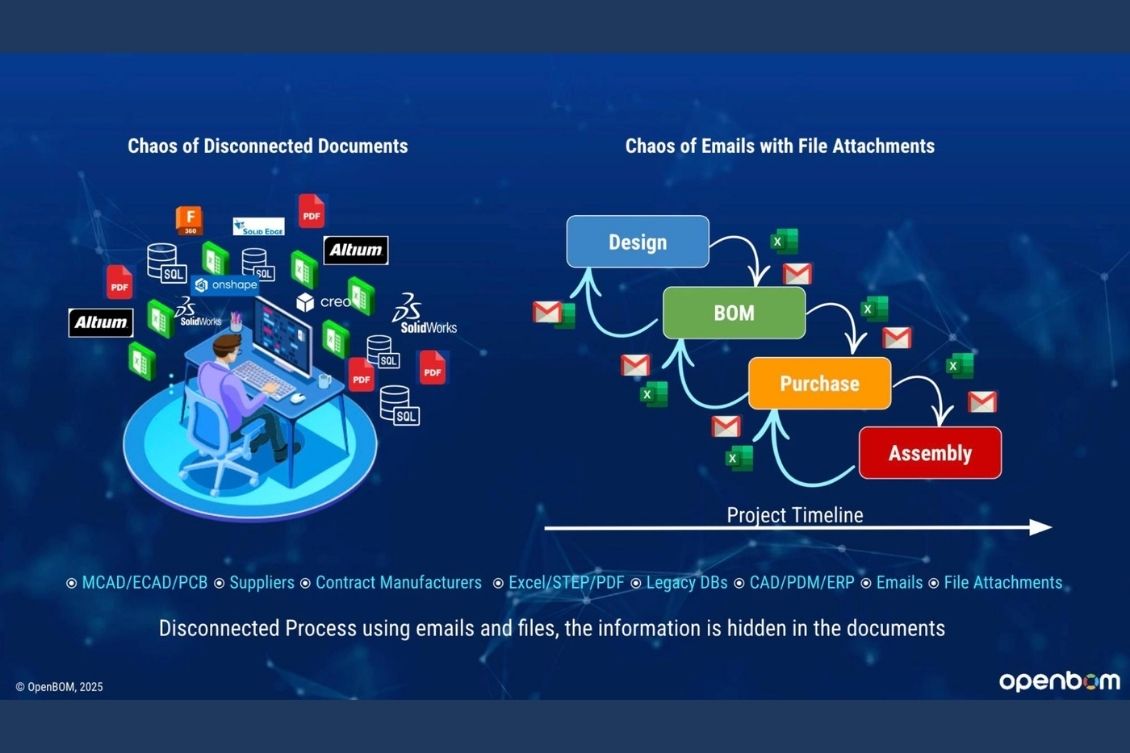
Product data is the backbone of modern manufacturing and product development. It drives every process, from design and engineering to procurement and production. But when product data is inefficient—scattered, outdated, or disconnected—it creates major bottlenecks that slow everything down.
In a previous article, I discussed three key challenges in product data efficiency – check them out (siloed data, lack of CAD integrations, inflexible and outdated data modeling) .
Today, I want to take a more detailed look at specific processes in your organization where product data inefficiencies are quietly damaging your productivity, increasing costs, and causing delays you might not even realize.
5 Critical Processes Where Poor Product Data Management Creates Bottlenecks
Product data inefficiencies don’t just cause frustration—they create tangible business risks. Here are five processes where poor product data management leads to unnecessary delays, mistakes, and hidden costs.
1. BOM Creation from CAD Data
Every product starts as a design, but the process of converting that design into a Bill of Materials (BOM) is often messy. Many companies still rely on manual data entry, Excel spreadsheets, and disconnected file storage to manage PDFs, STEP files, and part numbers.
What happens when product data is inefficient in this process?
- Engineers waste time manually extracting and organizing BOM data.
- Errors creep in—incorrect part numbers, missing revisions, or outdated specs.
- Manufacturing and procurement teams end up working with incomplete or inaccurate BOMs.
- Competitors who streamline this process move faster, with fewer mistakes.
2. Optimizing Product Structure & Controlling Changes
Modern products combine mechanical, electronic, and software components, and managing this complexity requires a well-structured product data model. However, many companies lack a unified approach, and engineers work independently, making it difficult to track and control changes.
What happens when product data is inefficient in this process?
- Different teams operate in silos, leading to misalignment between mechanical, electrical, and software components.
- No clear visibility into how design changes impact the entire product.
- Version control issues cause confusion about which design is the latest.
- Last-minute fixes and costly delays emerge due to overlooked dependencies.
3. Disconnect Between Engineering & Procurement
Engineering and procurement must work together, but product data must be synchronized for this collaboration to work. When these teams rely on separate systems or outdated spreadsheets, procurement decisions are based on incomplete or incorrect engineering data.
What happens when product data is inefficient in this process?
- Procurement orders the wrong parts or purchases incorrect quantities.
- Delays occur as procurement scrambles to adjust to unexpected changes.
- Unplanned costs arise due to expedited shipping, rework, or last-minute supplier changes.
- Excess inventory builds up while critical components are missing.
4. Inaccurate ERP Data Entry
ERP systems rely on accurate product data to manage production, inventory, and costs. However, many companies still manually enter product data into ERP from disconnected spreadsheets, emails, or outdated PDM/PLM systems.
What happens when product data is inefficient in this process?
- Incorrect data in ERP leads to manufacturing errors and supply chain disruptions.
- Inventory levels are inaccurate, leading to overstocking or shortages.
- Teams waste time fixing errors, causing delays in production and shipping.
- The entire organization spends more time firefighting problems instead of focusing on growth.
5. Inefficient Data Exchange with Suppliers & Contractors
No company operates in isolation—suppliers, contractors, and partners all depend on accurate product data. When data exchange is handled through email, spreadsheets, and manual file transfers, mistakes are bound to happen.
What happens when product data is inefficient in this process?
- Suppliers receive outdated drawings or incorrect specifications.
- Contractors waste time fixing errors instead of focusing on execution.
- Rework and last-minute changes drive up costs and slow down projects.
- The lack of clear, up-to-date product data erodes trust between business partners.
The Common Thread: Product Data Inefficiencies Are Costing You
Across all five processes, the root cause of these bottlenecks is product data inefficiency. When product data is scattered, outdated, or manually handled, it slows decision-making, creates unnecessary costs, and reduces business agility.
Your competitors who have streamlined their product data management move faster, reduce errors, and operate more efficiently. Meanwhile, companies struggling with product data bottlenecks are constantly fighting fires, fixing mistakes, and dealing with costly delays.
Conclusion
Business efficiency isn’t just about improving individual processes—it’s about ensuring that product data flows seamlessly across all departments. The companies that recognize and fix these product data inefficiencies will gain a competitive edge—not just by working faster, but by eliminating costly errors, improving collaboration, and making smarter business decisions.
If your product data is inefficient, your entire company is running slower than it should be. The longer these bottlenecks persist, the bigger the gap between you and your competition.
If you’re experiencing one of these problems, please contact us -we would be happy to share our experience of fighting with these problems.
Best,
Oleg
Join our newsletter to receive a weekly portion of news, articles, and tips about OpenBOM and our community.