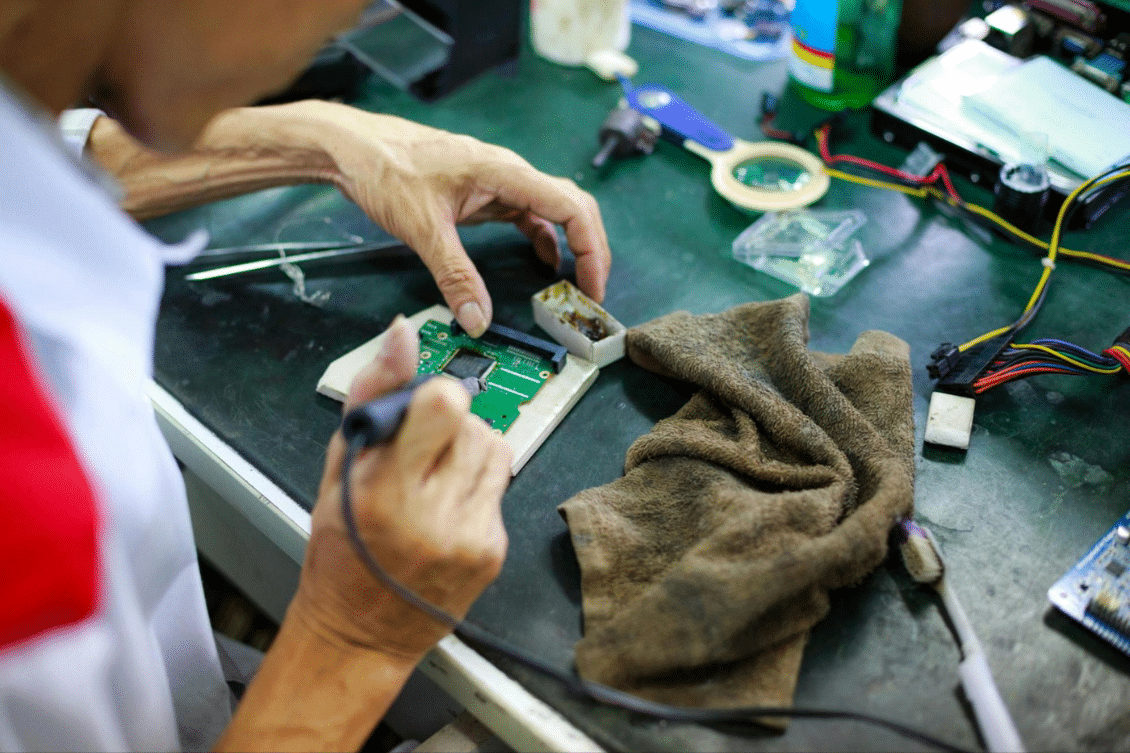
Preparing for mass production is stressful. There are usually years of hard work that went into development, creation of prototypes, marketing, and fundraising, and it all is for this one moment, your production launch. As you migrate from prototypes to production, many things will happen, there will be last-minute changes and it’s important to capture all of these changes and ensure that everyone is working on the same data 100% of the time.
Working on the wrong file, changing the wrong part, or not sending the correct revision to your supplier for fabrication will result in a loss of time and money. Both of these reasons are killers during production launch.
The Bill of Materials (BOM) serves as the backbone of any manufacturing operation. It details every component, part, and material required to bring a product to life. From the smallest screw to the most complex circuit board, the BOM captures your product structure, guiding manufacturers through the production journey.
With the BOM being the backbone and holding the manufacturing knowledge of your product, companies risk making errors and procuring wrong parts by using Excel. On the other hand, legacy Product Lifecycle Management (PLM) systems are costly and takes one employee to know how to run and operate this system.
In this blog, we dive into the pivotal role of BOM software and explore five compelling reasons why its adoption is paramount before embarking on the journey of production. From streamlined collaboration to enhanced efficiency, these reasons underscore the indispensability of BOM software in driving successful production launches and ensuring sustained excellence in manufacturing endeavors.
Reason 1: Streamlined Collaboration
In manufacturing, collaboration is second to none as it brings together the efforts of team members, suppliers, and stakeholders to bring a product from conception to reality. BOM software serves as the driver for this collaboration and creates a single source of truth.
Team members can effortlessly access, review, and modify BOM data, and store CAD files, facilitating agile decision-making and ensuring everyone remains on the same page throughout the production process.
In contrast, legacy PLM systems often present barriers to collaboration, burdening users with complex interfaces and rigid workflows. These systems require specialized training and expertise. Additionally, legacy PLM systems may lack the agility to adapt to the dynamic nature of modern manufacturing, further impeding collaboration and innovation.
Reason 2: Data Accuracy and Integrity
In the realm of manufacturing, precision and reliability are paramount. Any discrepancy or error within the BOM can have ripple effects throughout the entire production process, leading to delays, defects, and ultimately, dissatisfied customers. This is often the result of working with an Excel BOM.
BOM software emerges as the defender of data accuracy and integrity, wielding a suite of powerful features to safeguard against errors and ensure the seamless flow of information throughout the product lifecycle.
While a lot of manufacturers use Excel, it falls short in its ability to uphold data accuracy and integrity within the BOM. Excel may offer rudimentary features, but it lacks the sophistication and granularity of dedicated BOM software. Human errors, formula mistakes, and accidental deletions are all too common in Excel spreadsheets, posing a significant risk to the integrity of the BOM data. Without robust version control mechanisms, Excel leaves the BOM vulnerable to version conflicts and data inconsistencies, jeopardizing the reliability of the entire production process.
Reason 3: Efficient Change Management
Change is inevitable in manufacturing where market demands, technological advancements, and regulatory requirements are in a constant state of flux. Effective change management is essential to navigate these shifts seamlessly and ensure that the BOM remains accurate and up-to-date throughout the product lifecycle. BOM software emerges as the anchor of efficient change management, empowering teams to track, implement, and document revisions with precision and agility.
BOM software streamlines change management processes by providing a centralized platform for teams to collaborate on modifications to the BOM. Automated change notifications keep stakeholders informed of any updates, ensuring that everyone is aware of the changes and their impact on the production process. Approval workflows enable systematic review and approval of proposed revisions, preventing unauthorized changes and maintaining data integrity.
One of the key features of BOM software is its comprehensive revision history, which documents every change made to the BOM over time. This audit trail provides invaluable insight into the evolution of the product, enabling stakeholders to trace the lineage of each component and understand the rationale behind specific revisions. This transparency fosters accountability and trust among team members, facilitating effective decision-making and collaboration.
In contrast, manual change management methods are cumbersome and prone to errors, often relying on spreadsheets, emails, and paper-based processes to track revisions. This fragmented approach increases the risk of miscommunication, version conflicts, and data discrepancies, leading to delays and inefficiencies in the production process. Excel, while commonly used for basic data management tasks, lacks the robust change management features necessary to handle the complexities of modern manufacturing.
Reason 4: Enhanced Productivity and Efficiency
In manufacturing, every second counts. Time wasted on manual data entry, repetitive tasks, and inefficient workflows can translate into significant delays and missed opportunities. BOM software emerges as a catalyst for productivity and efficiency, empowering teams to streamline processes, automate tedious tasks, and maximize throughput throughout the production lifecycle.
BOM software revolutionizes productivity by automating repetitive tasks that would otherwise consume valuable time and resources. Tasks such as data entry, component updates, and BOM generation can be automated, freeing up team members to focus on more strategic initiatives. This automation not only accelerates the pace of production but also minimizes the risk of errors and inconsistencies inherent in manual processes.
Furthermore, BOM software offers an abundance of time-saving features designed to streamline workflows and optimize efficiency. Integration with other tools such as CAD software, ERP systems, and supply chain management platforms enhances collaboration and data exchange, eliminating silos and fostering seamless communication across departments.
Reason 5: Scalability
As manufacturing landscapes evolve and production demands fluctuate, scalability and adaptability become essential attributes for success. BOM software emerges as a beacon of scalability, offering a flexible platform to accommodate growing production needs and evolving industry standards.
BOM software is designed with scalability in mind, capable of scaling seamlessly to meet the demands of both small-scale operations and large-scale enterprises. Whether it’s adding new product lines or ramping up production, BOM software provides the infrastructure to support growth without sacrificing performance or efficiency.
One of the key advantages of BOM software is its flexibility, particularly in the realm of cloud-based solutions. Cloud-based BOM software offers unparalleled flexibility, enabling users to access and manage BOM data from anywhere in the world, at any time. This flexibility fosters collaboration, empowers remote work, and ensures continuity of operations, even in the face of unexpected disruptions or challenges.
Conclusion
In the dynamic and competitive landscape of manufacturing, success hinges on precision, efficiency, and collaboration. As we’ve explored in this blog, BOM software emerges as an indispensable tool for navigating the complexities of production and ensuring success before launching new products.
From streamlined collaboration to enhanced productivity, BOM software offers a myriad of benefits that empower teams to thrive in today’s fast-paced market. By providing a centralized platform for collaboration, ensuring data accuracy and integrity, streamlining change management processes, enhancing productivity and efficiency, and offering scalability, BOM software equips businesses with the tools they need to excel in manufacturing.
Are you looking for a BOM software solution?
Register to OpenBOM today to start your digital transformation journey.
By: Jared Haw
Join our newsletter to receive a weekly portion of news, articles, and tips about OpenBOM and our community.