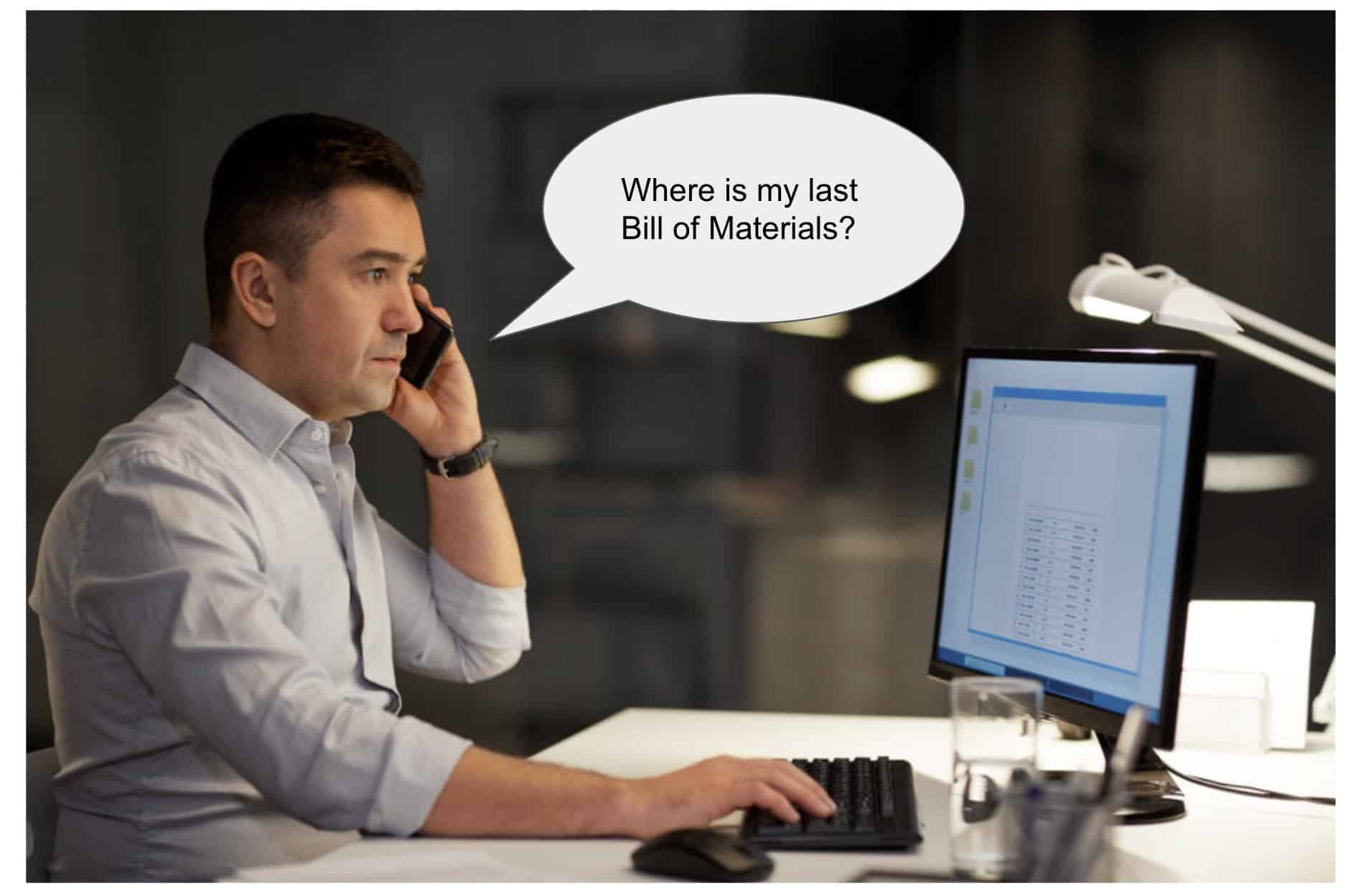
As a manufacturer, you’re constantly looking for ways to streamline your processes and improve your bottom line. Let’s put it in simple words, most of the manufacturing companies and engineering teams we are working with are looking at how to get advantages in time and money. It is very simple to say, but it is very hard to achieve. The reason for that is that product development and manufacturing activity is complex and requires good synchronization of multiple people, teams, and process. Think about a good restaurant as a comparison. Just by a willingness to make a good meal, you won’t make it a success. You need to have multiple people and activities, you need to bring great recipes, organize the kitchen, bring supplies, plan the delivery, organize the food cooking process and get it on time, so your customers will be able to come and enjoy the meal. One of the elements of this chain fails and the entire process won’t deliver the results. Product development and manufacturing are exactly the same.
Product lifecycle management is often considered a complex discipline, which includes many elements – strategy, data management, process orchestration, business optimizations, and many others. It is usually presented as a solution for large enterprises. Here is the thing. After working more than two decades with thousands of manufacturing companies of all sizes I can see the same problems are happening with the companies of all sizes. The difference between them is the solution – one size doesn’t fit all. Before speaking about the solution, let’s talk about problems first.
Five Signs You Have A Product Lifecycle Problem
Any manufacturing company that builds something has a product lifecycle process. It can be organized differently, but it does exist. Look around and you will see it – you can manage data using files and folders, you can have spreadsheets with a list of parts and you can have word documents to sign change orders. If you do so, you still have your product lifecycle process. I’m sorry to say, it might be ugly, but it is there.
In some cases, managing a part list using Excel can be a good solution. Exporting a list of part and send them to a printer using Excel can work. But when you consider Excel as a data management platform, things will start look ugly very soon.
I suggest you check the following five signs that will give you an indication that you have a problem and you need to seek a better solution than creating a giant Excel spreadsheet with all product information, revisions, suppliers, cost, purchases, and schedules.
Here are these five indicators. Take a look and make an assessment if you can associate your business problems with these indicators.
- You’re struggling to keep track of all the different parts and components used in your products
- You can’t easily track changes or revisions to your products or parts.
- It’s difficult or impossible to get accurate cost estimates for products or parts.
- Purchasing processes are taking too long, resulting in missed opportunities and increased costs
- There’s a lot of waste due to inconsistencies between design and manufacturing
OpenBOM Painkillers To Problems
The problems I described above are real. Talking to many manufacturing organizations, I can see how they struggle to bring a better data management solution to solve their problems. But, unfortunately, there is a good reason why Excel is the second-best software solution for everything. Everyone wants to leave Excels behind, but without good solutions, it is not a realistic task. For many years, the alternatives to manage BOMs and product lifecycle was to deploy a multi-million dollar project with IT, installation, configuration and implementation, service contracts, and big budgets.
It was true for many years. But these days everything is changing and the manufacturing industry is experiencing one of the biggest shifts in decades moving from old fashion spreadsheets and legacy databases to modern online applications. OpenBOM is leading the way and helping thousands of engineering professionals and manufacturing companies to jump from Excels into the future.
Here are five OpenBOM Painkillers to the problems I described above:
- Online SaaS, no installation required
- Flexible Data Management as simple as Excel and spreadsheets
- Out of the box integrations with Excels, Google Spreadsheets, CAD systems to import data
- Specialize to manage items, bills of materials, documents, formulas, rollups, and more
- Provides an integrated solution to manage inventory, orders, and purchasing
Conclusion
OpenBOM simplifies the way you can leave your Excel spreadsheets behind by providing an online (SaaS) platform to manage product data, organize Bill of Materials, revisions, manage files, changes and perform production planning and purchasing. For small and medium-size companies and divisions of large enterprises (especially for NPD process), OpenBOM provides a solution that is easy, flexible, and robust to replace messy Excel spreadsheets. Check OpenBOM customer stories online – each story will show you how companies left excel behind and organized their work and data. It is priceless and it will help resolve problems I’ve been talking about at the beginning of this article.
Check out what OpenBOM can do for you – REGISTER FOR FREE and start your free 14-day trial to explore all of OpenBOM’s features and functions.
Best, Oleg
Join our newsletter to receive a weekly portion of news, articles, and tips about OpenBOM and our community.