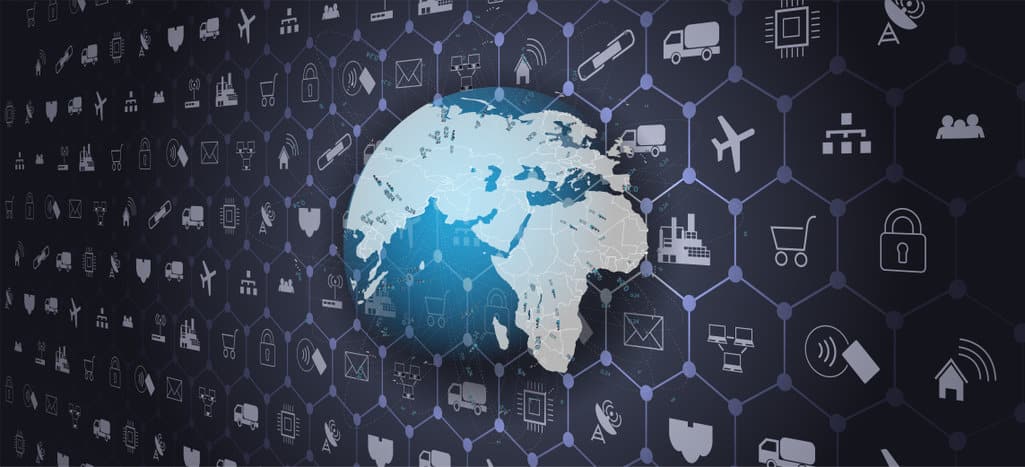
From the start of the pandemic, supply chains have been thrown into disarray. Since we have had a couple of years to adjust ourselves, it’s clear some of these trends are temporary while others are here to stay.
The short-term obstacles are more related to the production, pricing, and lead time of the product. While the long-term trends are more strategy-based, such as diversifying your supply chain and investing in software.
Here are 5 trends that are impacting the global supply chain.
Material inflation
Unless you have been living under a rock for the past year, you have noticed that the prices of goods have increased quite drastically. Brookings has stated that “the annual rate of inflation from October 2020 to October 2021 was 6.2 percent.”
Now, do not expect this to come down any time soon. One of the main reasons for this is because the costs of raw materials have been increasing. No matter the materials you are using during production, chances are that the price of the raw materials is considerably higher than what it was a year ago. Prices for silicone, plastics, metals, paper, wood, electronic components, and more have all seen a sharp increase in prices. As these products hit the shelves in a few months, you will be expected to pay more for these goods or go without them.
Those who have received quotes from their suppliers months ago should be aware. Those prices might no longer be valid as the cost of raw materials has increased. You should sort this out earlier rather than later. If you try to get around it and just place a PO, it will be rejected then time will be needed to re-quote the product.
Chip Shortage
The global chip shortage was one of the bigger trends that negatively affected manufacturing companies in 2021. Due to simple economics, the price of components increased because of supply and demand. Nothing happened to the demand, people still needed their parts but the supply wasn’t there to absorb the demand.
And if you think that 2022 will be better then you are in for a rude surprise. Supply Chain Dive claims that seven out of ten electronic manufacturers expect prices to increase between 7% – 8% in 2022.
To get around this, we will need to be clever and find alternative solutions. Elon Musk said that Tesla was “able to substitute alternative chips, and then write the firmware in a matter of weeks.”
If finding alternative components is not a solution then you will need to plan for the future, tie up cash flow in inventory, and hope that your sales forecasts are correct.
Shipping Costs
If you are a manufacturing company, you have noticed the increased costs incurred in shipping your product or materials from China to your localized warehouse or assembly facility.
Freightos has provided data that a 40-foot shipping container from China to the US now costs more than $20,000. However, recently, I have heard of costs going up to $30,000, I guess it depends on how desperate you are for last-minute containers. In July of 2021, you could have purchased that same container to ship the same route for just $11,000. And pre-pandemic, it was considerably less.
This is not just for the US, but shipping prices from China to Europe have also increased. Currently, a 40-foot container costs nearly $15,000.
Shipping Delays
The increased shipping fees are not the only logistical nightmare that is affecting manufacturing companies. If you are outsourcing production, you have noticed that the time it takes your product or part to leave the factory and arrive at your local warehouse is increasing.
According to World Economic Forum, ocean freight from China to the US was about 40 days a couple of years ago and now it’s up to 70 days. There are a number of reasons for this but the main takeaway is to not expect these numbers to go down. They will most likely stay around 70 days for the foreseeable future.
Shipping disruptions also create a domino effect across your entire business. It’s common to see your inventory depleting, get desperate, and air freight your product. Once your products arrive at the warehouse then it’s common for you to have a build of inventory that was not originally planned.
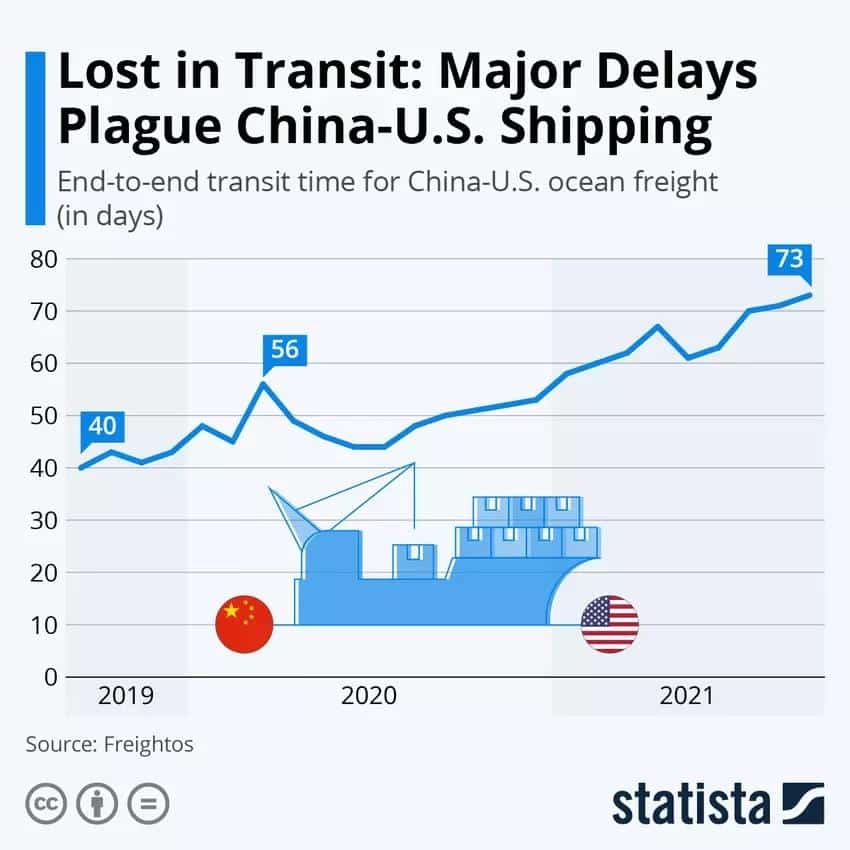
How Modern SaaS PLM Software Can Help?
Before, if you wanted a PLM or an ERP system, you might be paying hundreds of thousands of dollars. Unfortunately, the majority of small and medium-size manufacturing companies can not afford old legacy PLM systems because of their price tag to purchase them along with the infrastructure needed to sustain their use, implementations, and services. What would you rather do, invest every last dime into a software company or invest into your development and marketing teams to sell and scale production?
Another trend that’s pushing towards the adoption of affordable software is remote-style working. And why, not? Why hire someone based on location when you can hire someone based on capabilities?
With employees working in different cities and even different countries the way you manage your product becomes important. What this means is to bring all of your employees into a centralized location which is now offered on the cloud.
How to Diversify Your Supply Chain
If there is one thing that the pandemic has taught us is not to rely on just one supplier in one location. As we are coming out of the pandemic, we know the importance of how supply chain teams must identify alternative production partners. One contract manufacturer with one location will most likely be old news.
In order to reduce risk and to remain in control of the fabrication of your product, manufacturing companies will need to restructure their focus on manufacturing. The most basic talking points are:
- Re-shoring – bringing production back to your home country/region.
- Nearshoring – regionalizing production. Such as an American company moving production out of China to Mexico.
- Multiple assembly facilities based on customer proximity. Meaning, bring production closer to the core group of clients so you can assemble it quickly and deal with quality problems on-site.
- Have multiple suppliers for one component or one part. For example, if you use one contract manufacturer then your success is heavily dependent on this CM and also all of their sub-suppliers. If they go down, then you go down. So, have a few CM’s that can all scale up production if one does fail.
How OpenBOM can help?
OpenBOM is a cloud-based platform that manages all of your manufacturing and engineering data. Companies from startups all the way up to fortune 500’s use OpenBOM to replace excels, create a centralized database to bring in, store and share their manufacturing data, and streamline their purchasing & change management processes.
OpenBOM keeps everyone OEMs, contractors, suppliers connected “on the same BOM” while providing you with the tools to streamline your development to production & scale up operations.
REGISTER FOR FREE to check how it can help you.
Regards,
Jared Haw
Join our newsletter to receive a weekly portion of news, articles, and tips about OpenBOM and our community.