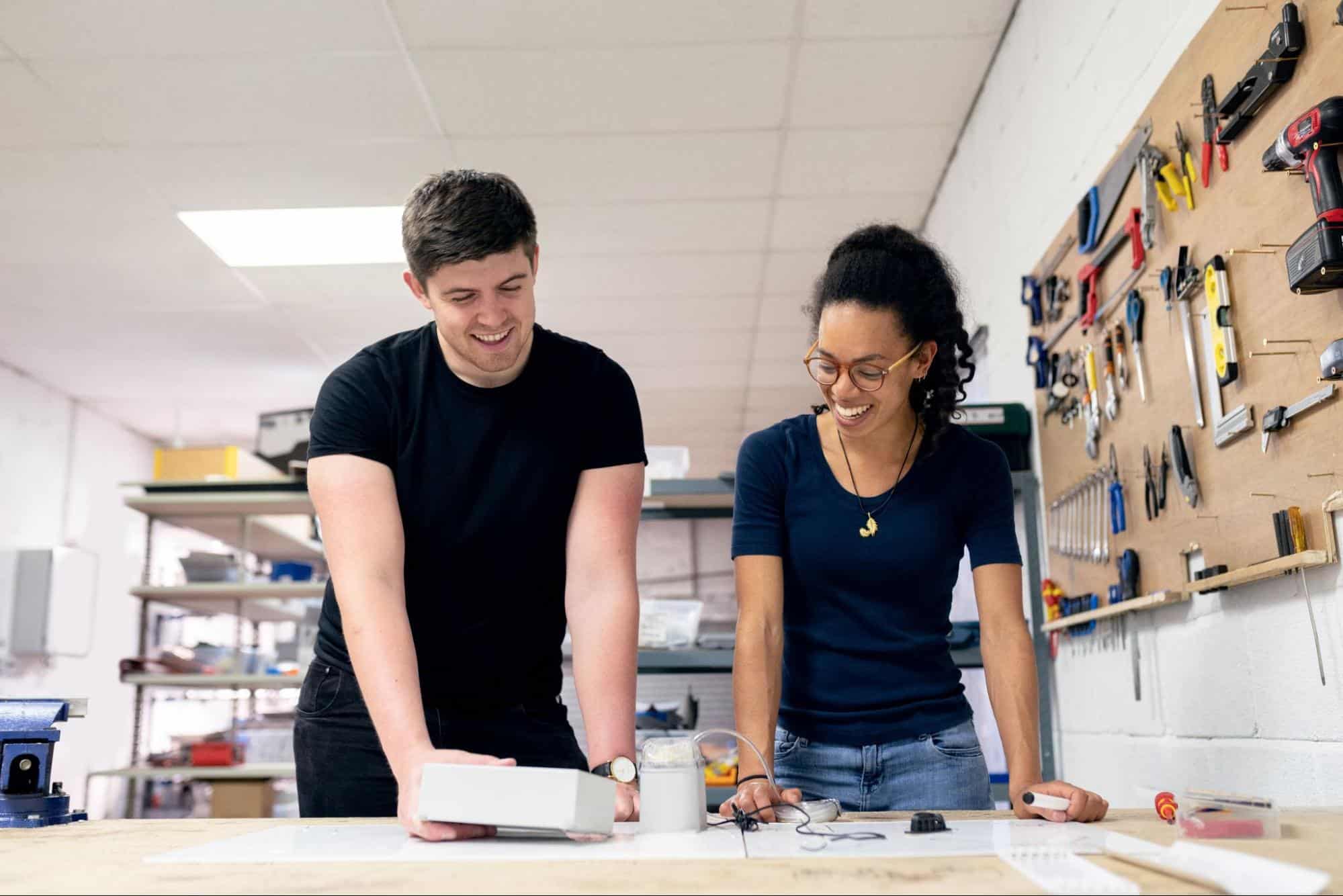
There is no such thing as an overnight success. At OpenBOM we speak with engineering teams, manufacturing companies, and entrepreneurs about manufacturing, hardware developers and discuss how to get from the idea to prototype and then to scaling their production. For the last decade, the industry has achieved tremendous success in democratizing manufacturing. Still, the seemingly overnight success means the dedication and execution of the proper new product introduction (NPI) steps.
The Problem
Those who want to skip some steps and go straight for the gold will come across multiple problems. These problems consist of:
- Failing to work within your budget
- Developing a product that can not be made in production… Need to redesign
- Quality fails because you did not do any quality analysis
- Product inconsistency because you did not objectively quantify the quality requirements.
There are 6 steps you should follow to ensure your product is developed and launched successfully. The steps you must take in order to go from idea to shipping are the following:
- Define
- Feasibility Check
- Development
- Validation
- Implementation
- Evaluation and Improvements
Step 1: Define
During the define phase, the feedback received by existing customers will be linked with the product requirements. For example, if you have a current brand and your clients would like a similar product with different features then you define the features based on the feedback from current clients.
During the define phase, you create a business case for the product while also identifying the functional requirements.
Step 2: Feasibility Check
The feasibility phase looks at whether or not the product has the potential to succeed in the market. During this phase, the business case and the product specifications are defined. On the product side you should have the following:
- High-Level Bill of Materials (BOM): Not every detail needs to be defined but you should have an idea of what your BOM looks like
- Material Testing: In your BOM, you will have materials defined, tentatively. You can test the use of alternative material here.
- Design for Manufacturing & Assembly (DFMA) Plan – What will be the cost and lead time to transition you from development to production.
Step 3: Development
If you move to the previous phase, the management team see’s the potential in the product and would like to see more. The development phase looks at advancing the product development steps. Other steps within the operations and supply chain side might be brought in as well to start with vendor selection, DFMA, material forecasting, and more.
During the design phase, you should receive the following:
- Defined BOM
- 3D Design
- Start DFMA
- Develop functional requirements
- Prepare for audits
- Create prototypes
- Receive your cost of goods sold (COGS) from your supplier(s)
This is the stage when you can leverage the expertise of your supply chain or contract manufacturing partner. If you do not have these partners then you should take the proper steps to choose your suppliers.
Step 4: Validation
During the validation phase, product testing and final analysis will be performed. Upon completion of the tests, re-designs might be necessary, as well. The majority of the knowledge for the product is transferred over from you to your supplier(s).
During this step, you will ask yourself how did the product work and where can we improve. You will be looking at the following:
- Prototype analysis
- Confirm your COGS
- Start making tools
- Create drawings for production
Step 5: Implementation
During the implementation stage, you are looking at your first production run while also looking at ways to prepare for production scale-up. Your manufacturing processes and quality requirements are defined and it’s time to launch production.
During this stage you are looking at the following:
- Developing and defining your work instruction (WIs) and standard operating procedures (SOPs)
- Start with the pilot build
- Ensuring all the tools, jigs, and fixtures have been made correctly
- Start your first production run.
Step 6: Evaluation and Improvements Steps
Your evaluation steps will look at how successful your launch was. It also looks at how you can improve the next orders and also how you can improve yourself going forward with future development projects.
HowOpenBOM Can Help?
At OpenBOM we believe engineering, supply chain, and manufacturing teams should be able to seamlessly manage their parts, vendors, bill of materials, purchase orders, and change orders. All BOM, engineering, and manufacturing information are stored in the cloud which you can share with your team, contractors, suppliers, or anyone else that has access to your account. OpenBOM keeps everyone on the same BOM while providing you with the tools to streamline your development to production & scale up operations.
Register for FREE to create your OpenBOM account and reach out to us via support @ openbom dot com if you have any questions.
Best,
Jared Haw
Join our newsletter to receive a weekly portion of news, articles, and tips about OpenBOM and our community.