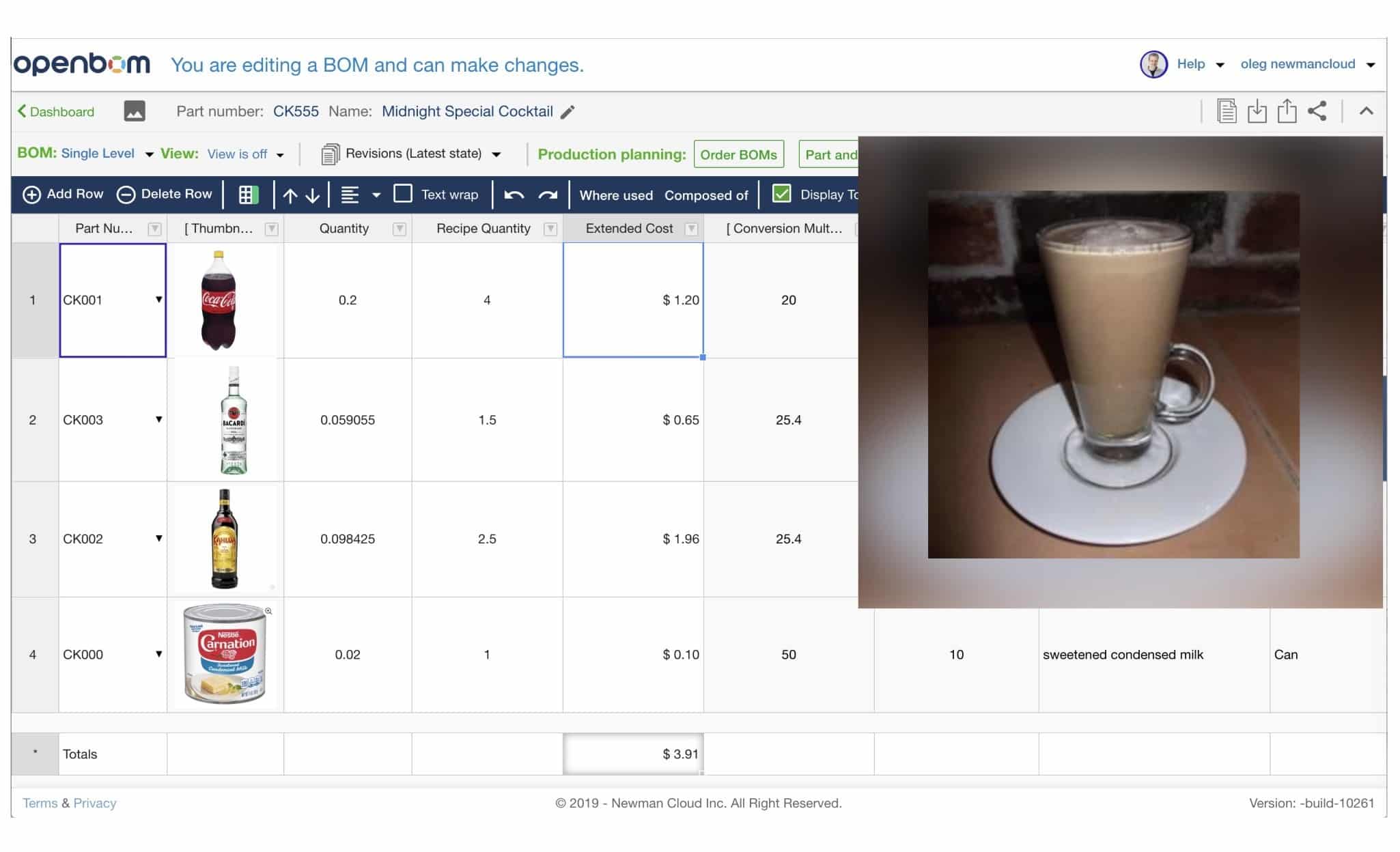
Food is one of the best examples to illustrate the Bill of Materials Management and manufacturing. If you think about it more, any restaurant is practically a manufacturing shop floor. You have products (dishes) that must be manufactured (cooked). To make them, you need to buy standard parts and outsource work (food ingredients and other instruments). Many questions in restaurant planning such as pre-cooked components, timing of orders, demand and supply, scrap, etc. can be modeled in the same way as you do in the manufacturing business.
Earlier today, I’ve got a question via OpenBOM website chat asking about how to create a bill of materials for a cocktail, manage ingredients orders and capacity. The question was too important to miss. Since my first blog about Thanksgiving Turkey BOM, I was looking at how to create a more mature example of a Bill of Materials for food. So, a cocktail is a great example and opportunity.
Here is what I did. I grabbed a cocktail recipe online for “Midnight Cocktail”.
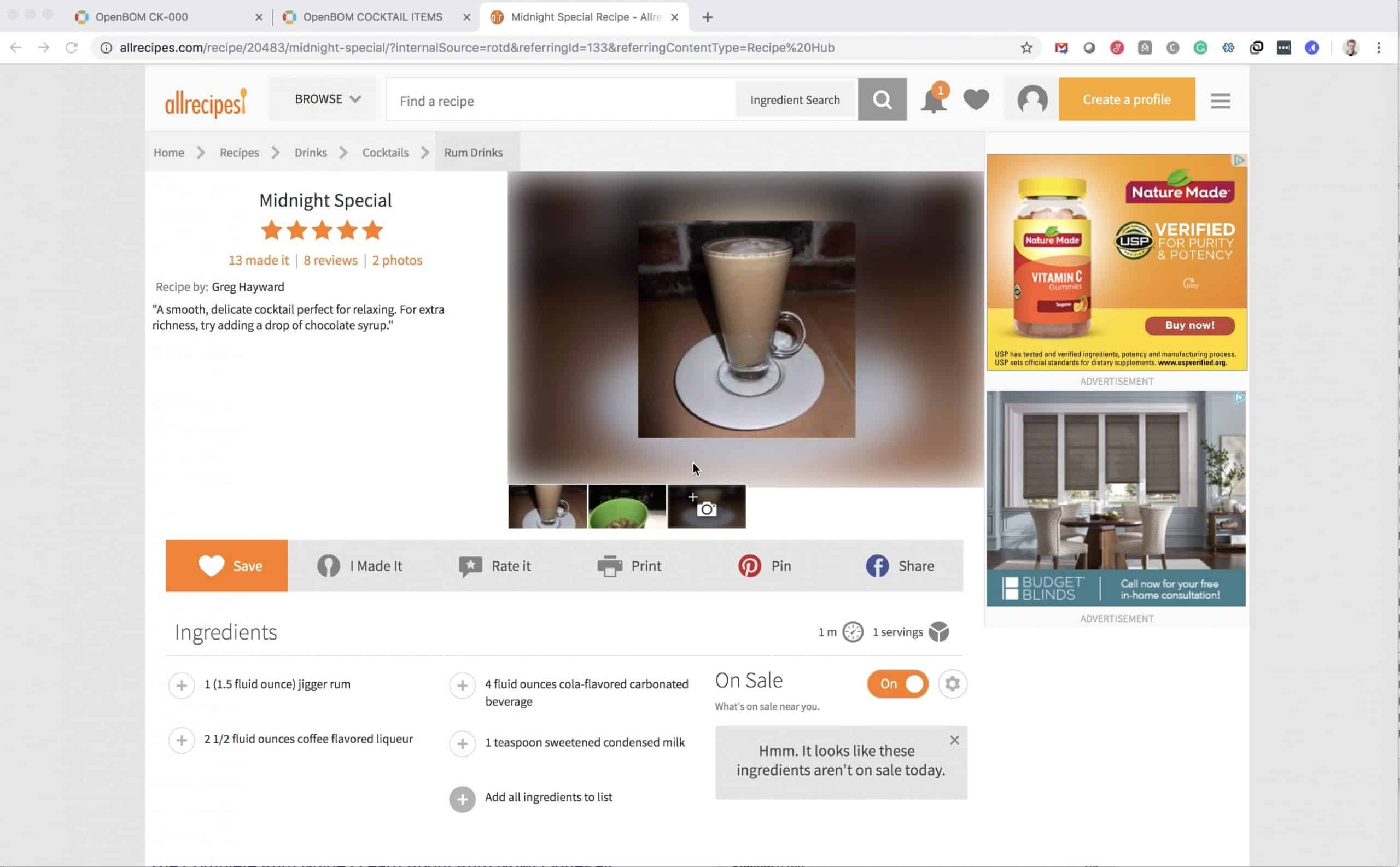
As a next step, I created a catalog of ingredients that will be included in my bar inventory. The catalog includes information about each item – Part Number, Image, Description, Cost, Link to suppliers. Etc.
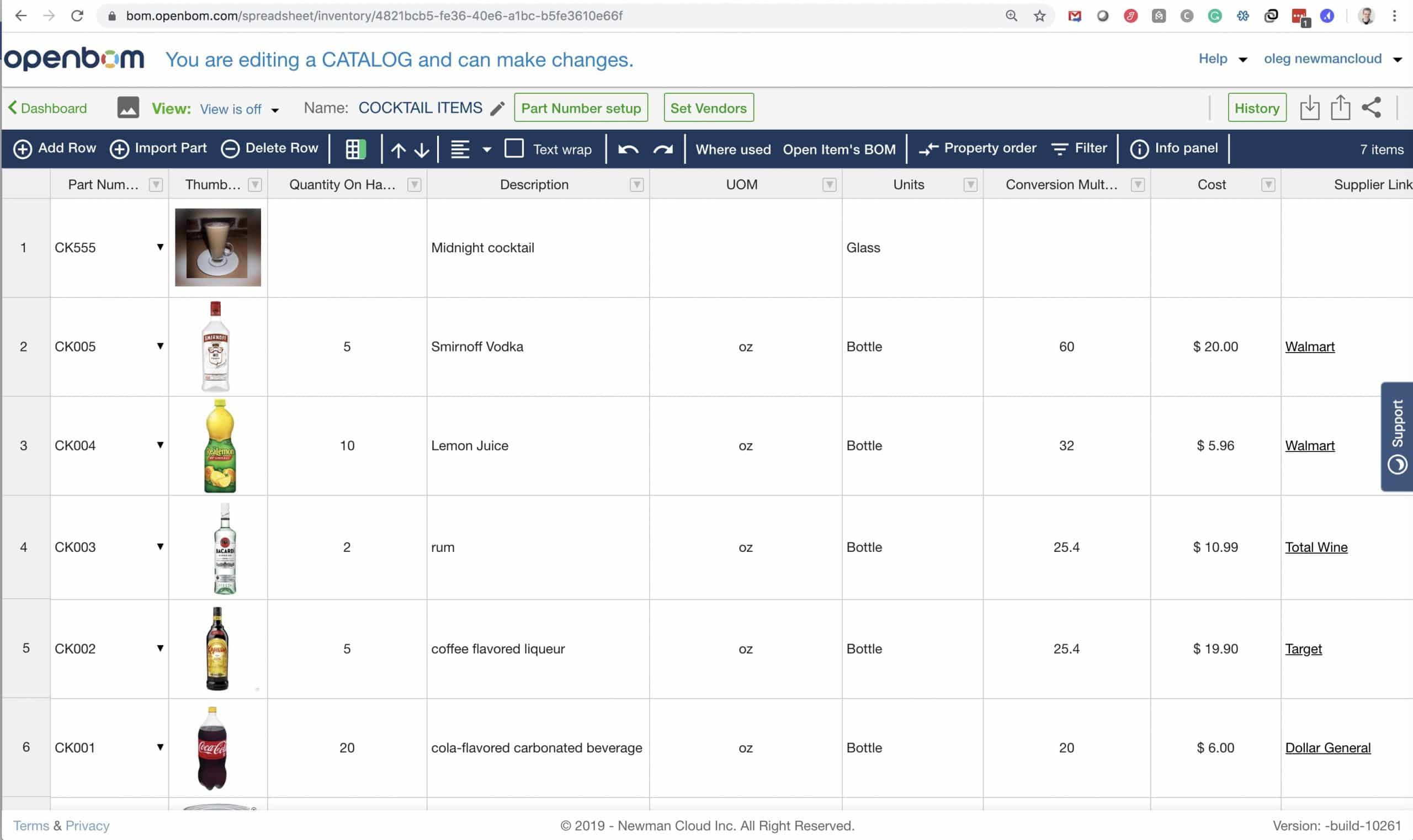
An important element of the catalog is the Unit of Measure and conversion multiplier to convert from units of measures of stock item to the unit of measure for part usage (recipe).
After that, I create a BOM for a single cocktail – Midnight Special. Here is a snapshot.
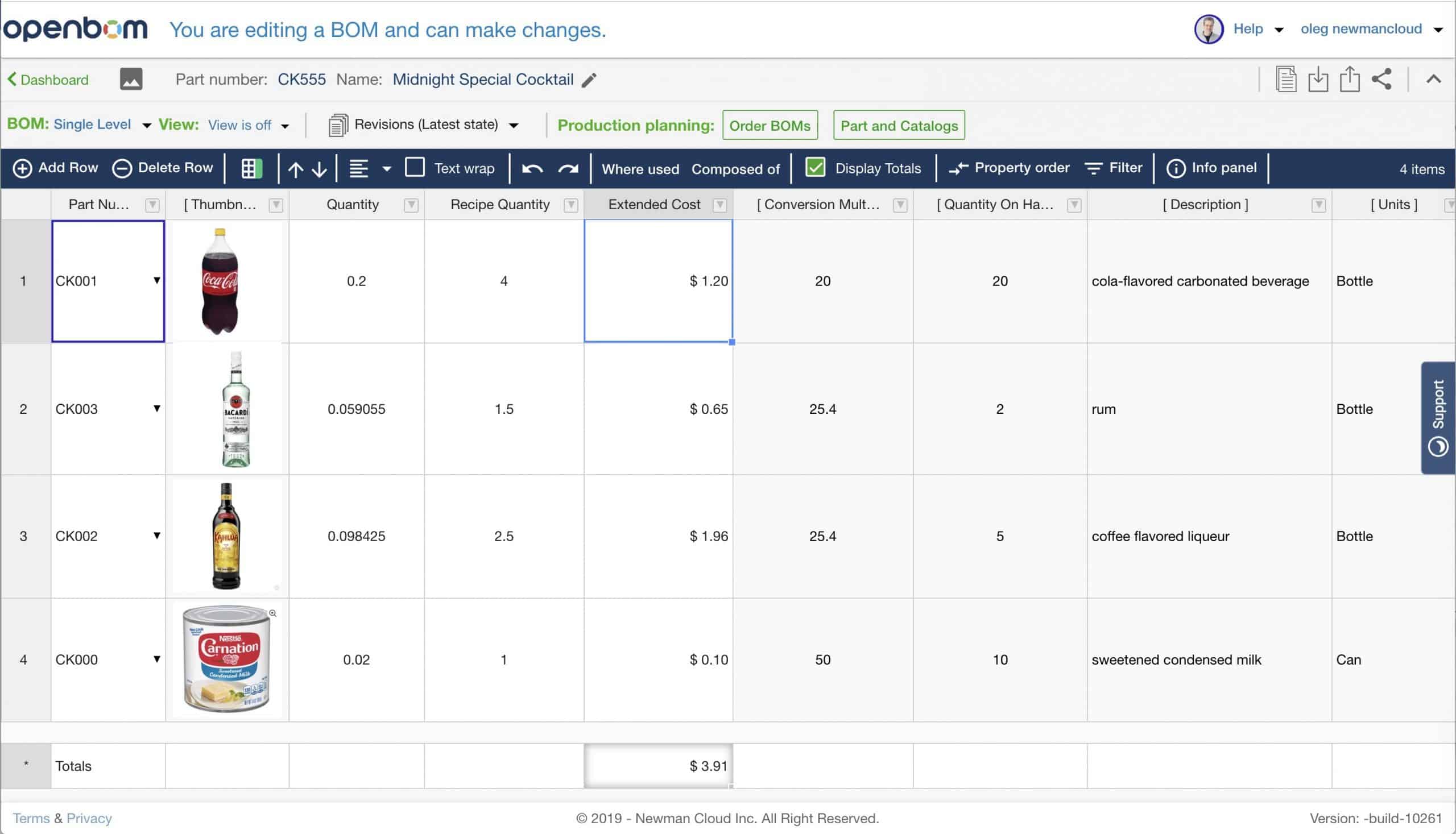
I created a few formulas. The first formula for Quantity- to calculate Quantity in a unit of measure we plan to buy ingredients. The second formula is to calculate Extended Cost (Quantity x Cost), including total calculation. So, now I know what is the cost of a single cocktail.
And I used this BOM to simulate “Order BOM” for two batches of cocktail parties – for 30 cocktails and for 50 cocktails. And I learned that I have enough materials (ingredients) for 30 cocktails, but I will be running out of rum if I will attempt to make 50 cocktails party.
The video below shows you the story.
Conclusion
OpenBOM has a simple and powerful mechanism to manage parts (Items) and usage of these parts in the Bill of Materials. We call it the instance reference model at OpenBOM. The model is extremely robust and allows us to manage a variety of information (even a cocktail BOM :)). Cost calucation including rollups can be easily done. Catalog and order BOM planning mechanism allows you to plan purchases and estimation if you have enough parts in stock.
I hope you loved the example. You can project how this use case can be applied to your company or team to produce catalog and bill of materials.
If you have questions or ideas for future videos, please reach out to me.
Best, Oleg @ openbom dot com.
Let’s get to know each other better. If you live in the Greater Boston area, I invite you for a coffee together (coffee is on me). If not nearby, let’s have a virtual coffee session — I will figure out how to send you a real coffee.
Want to learn more about PLM? Check out my Beyond PLM blog and PLM Book website
Join our newsletter to receive a weekly portion of news, articles, and tips about OpenBOM and our community.