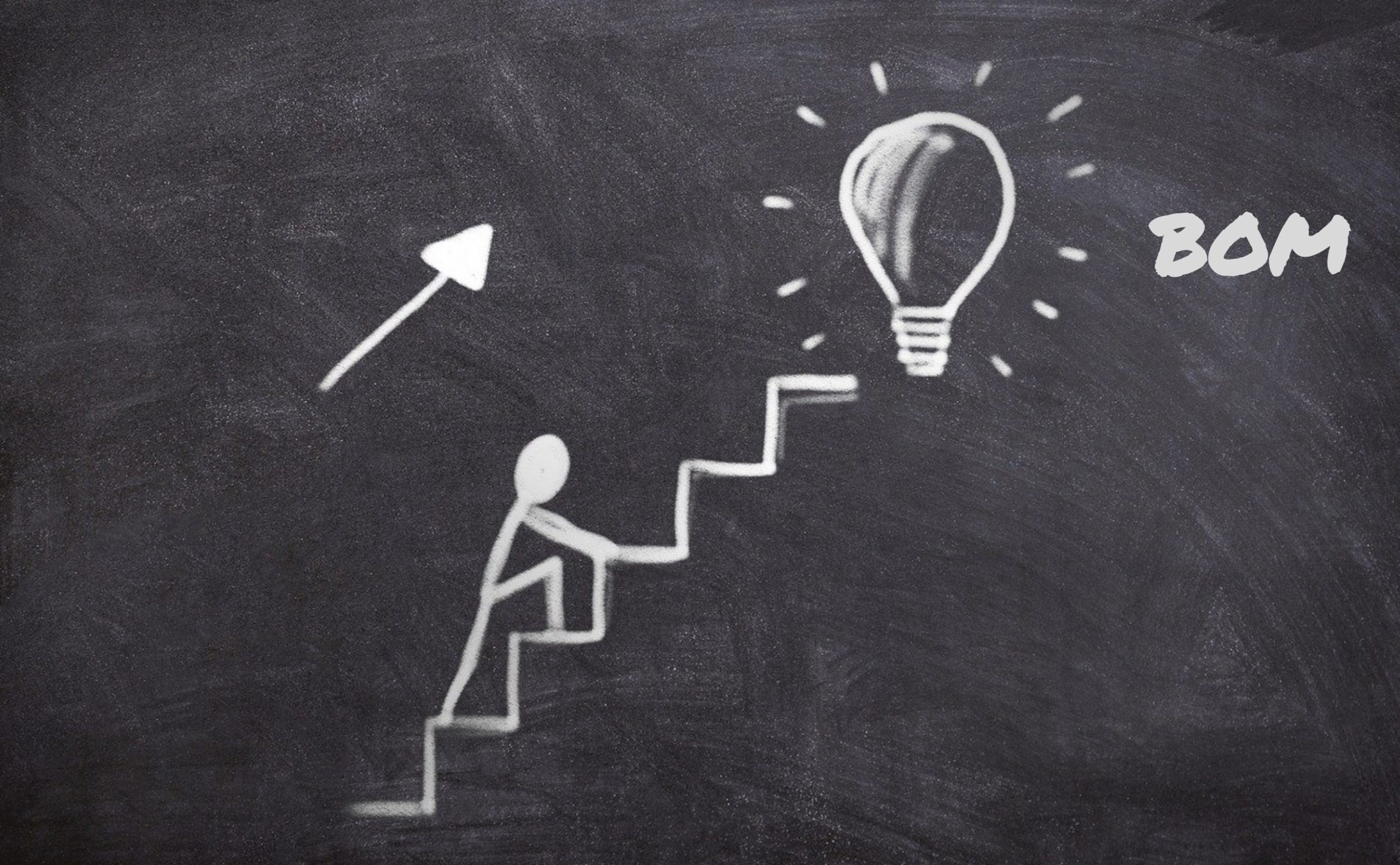
Is your company ready for BOM Management? Do you think it is a funny question? Not really… Many companies, especially in the early stages of its development, prone to the illusion of BOM that needs to be done once to list part in the product and place it on the drawing or to keep it in Excel.
The confusion about the Bill of Materials has a long history and goes back decades when companies were using drafting boards. It was a time when companies have a single BOM – the one that used to build a product. Back in these days, the PLM industry didn’t invent fancy words like xBOM, Digital Twin, or Digital Thread. Engineers were creating documents (literally drawings) and the company database was used to putting all items (BOMs) together defining what needs to be included in the product. The BOM was a final report.
I can see the challenge for many companies. While CAD tools are ubiquitous in the 2020s, the idea of placing product data and planning under control is taking companies to a complex decision of acquiring PLM and/or ERP software. Both are complex and expensive. But the biggest problem is that it requires engineers, product planners, buyers, schedulers, and many other people involved in product development to wrap their heads around the idea of managing data in the company. Everyone needs the data, but nobody really wants to manage traditional PLM software, which is such a pain.
As a result, this is what we can see – companies are leaving one of the most important questions of how to manage all product records to the later stages. It is a kind of fatal decision, but when the time comes up, it is too late in many ways to do such things like cost assessment, long lead items planning and purchasing as well as doing many other things that require changes in the design.
So, what is the solution? You should start with understanding how to manage a single source of truth is absolutely needed to manage product records. Once you decided about it, you will have to organize the process to consolidate the information and start managing permanent records with BOMs and all related information. Third and final, start planning off that BOM record all aspects such as cost, vendors deliveries, purchase orders, and many others. From our webinar this week, I’d recommend a webinar – A Single Source of Truth.
Once you setup the foundation, you can build things on top of it. Think cost calculations and other rollups. Then purchasing, which can be tricky. Especially when it combined with the BOM. Purchasing and BOM are using different units of measure. OpenBOM can help you to manage it in a very easy form. Check this article to learn how to manage different units of measures in BOMs and Order BOMs.
The next step is to manage change processes. You can think about essential PLM functionality OpenBOM provides in OpenBOM company subscription – Change Management and Change Request. OpenBOM has a few unique features. One of the most important is to be able to combine a superb set of CAD integrations combined with providing a better connection with suppliers and contractors. With OpenBOM, you can escape from the dilemma of choosing one – engineering vs supply chain. OpenBOM can do both. Read more here – Engineering centric vs Supplier Centric PLM.
Conclusion
Thinking about BOM as a report is so ‘95. Think about establishing a strategy how to manage product data and build a foundation of your company product data to drive more business, sales, and transforming manufacturing business into an agile and lean product development environment.
Best, Oleg @ openbom dot com.
Want to learn more about PLM? Check out my Beyond PLM blog and PLM Book website. Read OpenBOM customer reviews on G2 Crowd to learn what customers are saying about OpenBOM.
Join our newsletter to receive a weekly portion of news, articles, and tips about OpenBOM and our community.