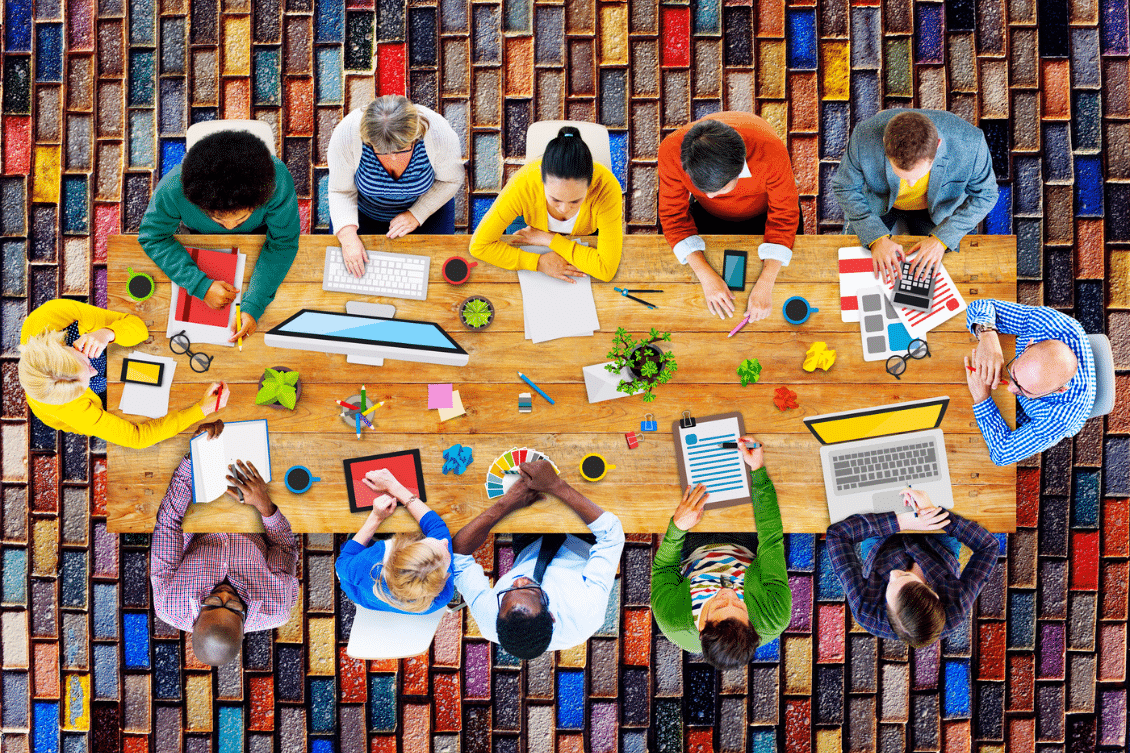
Product Lifecycle Management (PLM) software was traditionally only used by large enterprises due to its complexity and high cost. However, with the advancements in technology and the emergence of cloud-based PLM solutions, small and medium-sized manufacturers can now also benefit from PLM. This has opened up a new market for PLM software, but it has also led to some first-time buyers making costly mistakes. In this blog, we will focus on the specific challenges that small and medium-sized manufacturers may face when purchasing PLM software for the first time. We will discuss the three awful mistakes that you need to avoid to ensure that you select a PLM solution that is right for your business size and delivers the expected benefits.
Hard Tech and Demand For PLM Systems
The manufacturing industry is growing and we can see more engineering and manufacturing companies starting these days. So-called “hard tech” companies are those that focus on the development of hardware products that integrate software and advanced technology. These companies are often at the forefront of innovation, bringing cutting-edge solutions to market that revolutionize industries and change the way we live and work. However, the development of hardware products has traditionally been a costly and time-consuming process, which has limited the accessibility of these products to a select few.
The democratization of manufacturing has changed this, making it easier for small and medium-sized hard-tech companies to develop and bring their products to market. Technologies such as 3D printing, laser cutting have reduced the barriers to entry, together with contract manufacturing making it possible for startups to create prototypes and produce small batches of products without investing in expensive tooling and equipment.
This democratization of manufacturing has led to a surge in innovation in the hard tech space, with more companies bringing their products to market than ever before. It has also enabled new business models, such as crowdfunding, which allow companies to raise funds and validate demand for their products before going into full production.
The democratization of manufacturing has transformed the hard tech industry, making it more accessible to small and medium-sized companies. At the same time, it raised the question for all these companies about software products they can use to manage product information and process. You don’t build new technologies with old tools. This is why all these companies are on the front lines of PLM buyers looking for modern engineering and manufacturing software.
How to select the right solution for your growing manufacturing business and not make mistakes? In the next 3 use cases, I would like to outline possible mistakes you can make when using “traditional” PLM thinking.
PDM vs PLM Dilemma
There is almost no company in the world today that designs or build something without CAD systems. Therefore, every company starting to build something is connected to one or more CAD systems. MCAD and PCB CAD are among the most frequent choices. Many of these systems are 20+ years old and run on desktop systems producing their design outcome in a form of CAD files and their derivatives (STEP, PDF, IGES, etc). The folders and files paradigm is among the most popular and you can see how a “conventional thinking” process can lead companies to decide that PDM (the system to manage files and sometimes projects) is what is needed for them to manage their processes. By making this step, companies are losing their grip on the overall product lifecycle management and their ability to control full product data for the entire process.
One of the problems that product data management (PDM) decision brings to these companies is the isolation of the design process from the rest of the company or team. It is basically document management for CAD files. When everything you have files, the rest of your processes will look like folders and emails with file attachments. While PDM is needed for every business process in the engineering & manufacturing business, not to think how to connect your engineering and design team to the rest of the world is a mistake you’re going to pay for later.
PLM vs ERP Dilemma
Come to every large manufacturing business and you will find their MRP/ERP system. It is an absolute necessity to manage financials and transactional aspects of the business – materials, vendors, procurement, and related processes. But the challenge here for a small company is to grow to the level when ERP does help. Most (even very small) ERP system demands a certain level of management, processes, control, and resources. While having an ERP is the right thing, to believe that ERP will play the role of engineering and PLM systems is a mistake that often turns out to be very costly for many young manufacturing businesses.
A typical mistake is to believe that ERP is capable to manage bills of materials to hold all information about the product, including CAD designs and related information. It is not what usually is happening. Companies deciding for ERP to become a foundation of their PLM end up with a lot of additional informational silos that don’t fit the simplest ERP model they decide to implement. The result is disconnected engineering data including CAD design, absence of engineering collaboration, and lack of process management outside of procurement and production planning. Most of these businesses are managing tons of Excel and other data storage for CAD data and related processes.
Hosted Enterprise PLM
“Nobody ever got fired for buying IBM” is an unattributed quote that’s been repeated so often in tech circles that it’s buried into the mindset of a lot of enterprise software buyers. And that’s a problem for innovation. The quote expresses that the safe choice is to stick with well-known brands. And this is how some of these young manufacturing companies can decide sometimes, especially when people coming to these small and innovative companies are coming from large mega-corporation. Because they had previous experience with large PLM tools, they recommend using them.
The problems with these decisions are related to the complexity of enterprise PLM and the processes they need to establish and maintain. It very often ends up as a huge frustration and expense that later needs to be fixed.
Flexibility, Integrated Functions, Collaboration, and Information Flow
So, what is important when you are choosing a PLM system for your modern and agile manufacturing business? Talking to thousands of industrial companies, we learned that these are the most important characteristics and why they are important.
- Flexibility: Small companies are not formalized and usually like to have more adaptable technologies and processes for their work. Having a flexible data management platform is really important for these companies.
- Integrated Functions: Small companies don’t have time to do their own integrations and combine tools together. Therefore to have an integrated set of functions under a single roof can be a huge value. Integration with CAD data is the beginning to have design data capture fast. Then to have all PDM, PLM, and ERP functions combined and integrated in a simple way is the key that all hard-tech companies are looking for.
- Collaboration: In the last years of COVID and also before, I’ve seen a growing need to communicate and work together with people located in different places, companies, and processes. Emails and files are not a collaboration process. Instant data sharing and real-time data access are among the top priorities for modern collaborative product lifecycle management (PLM) solutions.
To summarize, I recommend new hard tech companies focusing on modern PLM systems, check your choices, to look outside of the box for systems that help them to make the right decision at the right time. Which is based on streamlining data management, information flow, and decision support uniquely tailored to companies your size.
Conclusion
Modern product lifecycle management systems are different from old predecessors. They are flexible, smart, and simple to use. Modern PLM systems are looking beyond current needs but provide for manufacturing companies’ growth horizons. When you’re selecting a new PLM system for your business, check what are the Top PLM Systems based on the reviews and also try to use these systems. The last is not less important. You should be able to try modern PLM tools today without any issues. Absences of a trial are usually one of the signals indicating that this specific PLM system is leaning on the traditional hosting options and cannot make the system available for trials.
REGISTER FOR FREE and start a 14-day trial to check how OpenBOM can help you today.
Best, Oleg
Join our newsletter to receive a weekly portion of news, articles, and tips about OpenBOM and our community.