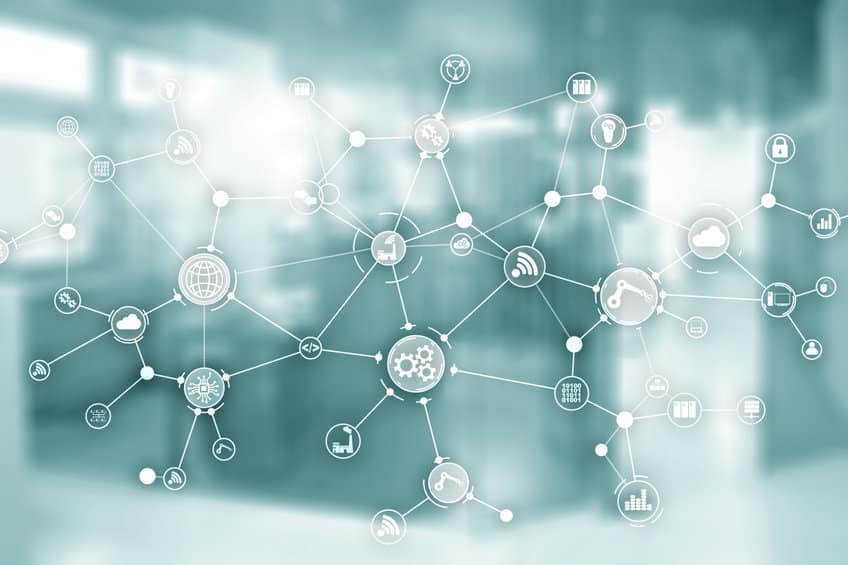
When it comes to supply chain management and procurement, many business owners feel overwhelmed by the complexity of the process. It can be difficult to know where to start when trying to find the right suppliers and manage inventory effectively. However, with a little planning, you can streamline your supply chain and improve your purchasing process. In this article, I will focus on the process to organize and track the partial PO receiving process. Recently we’ve got many requests about this process. We are working on better OpenBOM support, but in the meantime, I’d like to suggest a simple workaround to help you track orders.
Orders and POs Data Model
The fundamental elements of OpenBOM’s data model to support purchasing process contains the following four elements:
- Catalog – manages Part Numbers (P/N)
- Inventory levels using Quantity on Hands (QOH)
- Orders – created from Bill of Materials or directly from any catalog
- Purchase order – a filtered order for a specific Vendor (supplier)
OpenBOM Purchasing Process
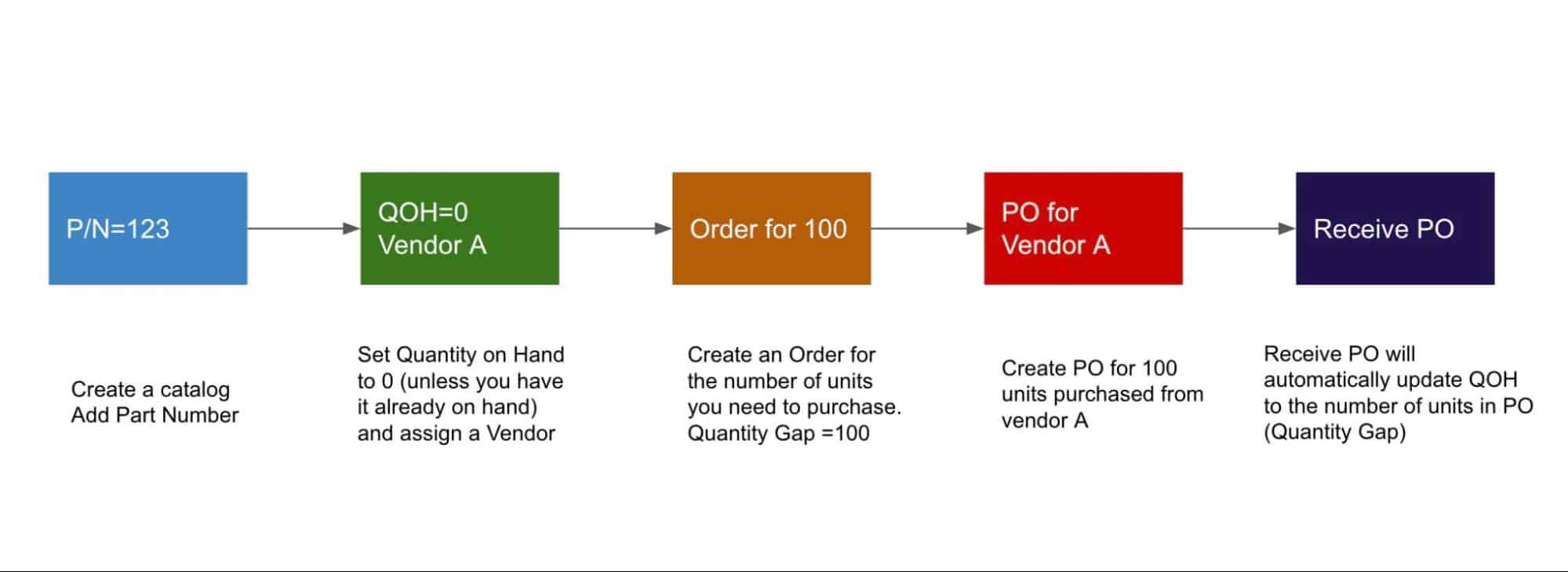
The simplest purchasing process in OpenBOM can be organized by adding a P/N to a catalog with QOH = 0 and then creating an order, selecting a vendor (assuming you already have a vendor list), and generating a PO. If you need to purchase multiple parts you can either select them from the catalog and add them to existing orders or (in case you build an assembly), create an order directly from an assembly.
OpenBOM Purchasing Process
Now, let’s take it to the next step. Let’s say you created a PO for 500 units, but the vendor can only send you 50. In modern supply chain realities, you would like to get these 50 and try to buy the remaining 450 from other vendors or to wait and get the remaining items later.
How to organize this process in OpenBOM? The flexibility of order creation and manipulation with Quantity Gaps, allows you to organize it. The following picture gives you an idea about how to do so.
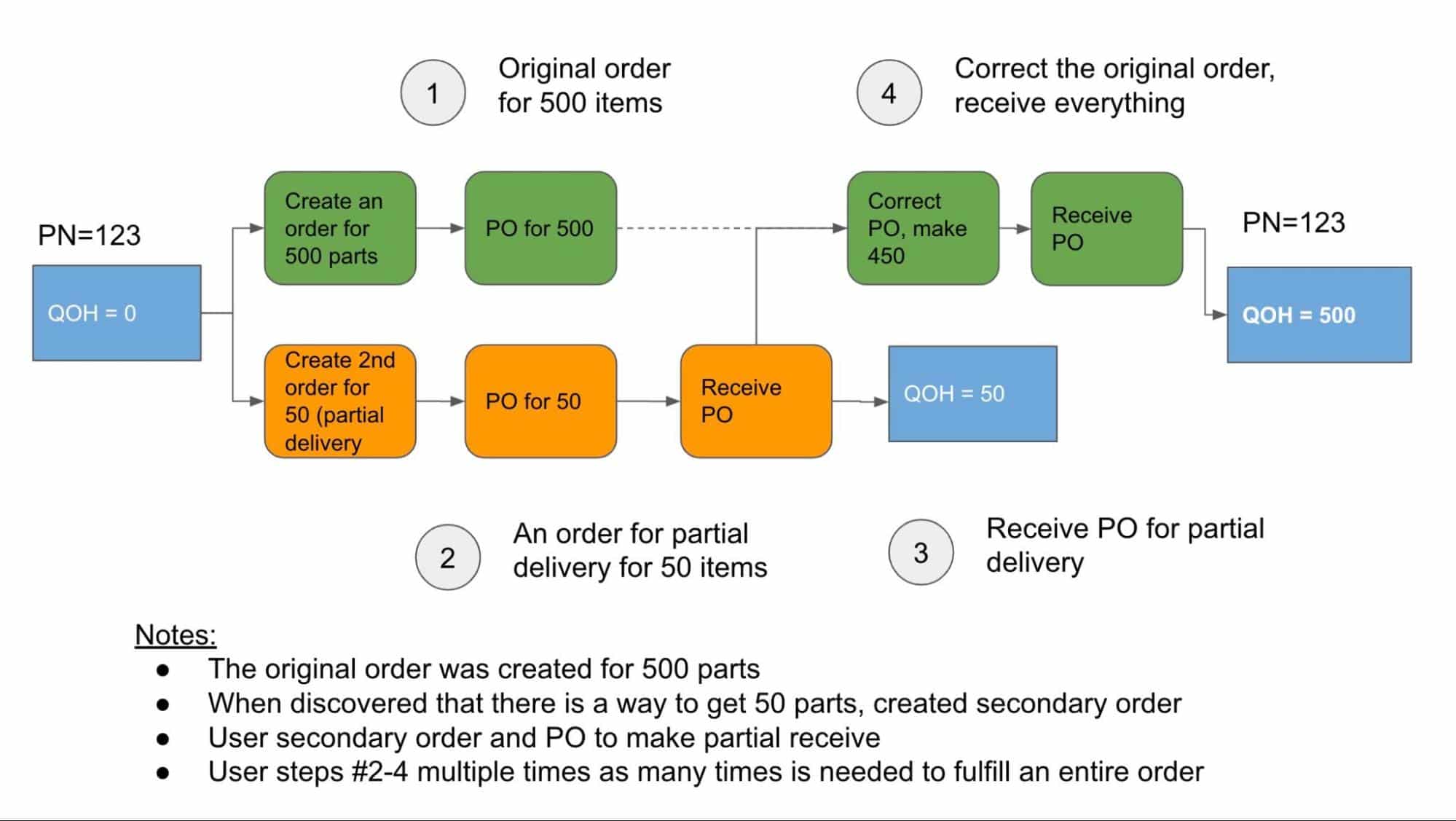
As you can see from the picture, the basic idea of the partial receive process is to create a second-order that is used for the partial delivery, generate PO and receive the PO. Once it is done you can adjust the original order (and PO) or just add notes to the order / PO and update the Quantity Gap to the remaining amount. Here are a few screenshots to help you to understand how to do so.
To create a first-order for 500 items
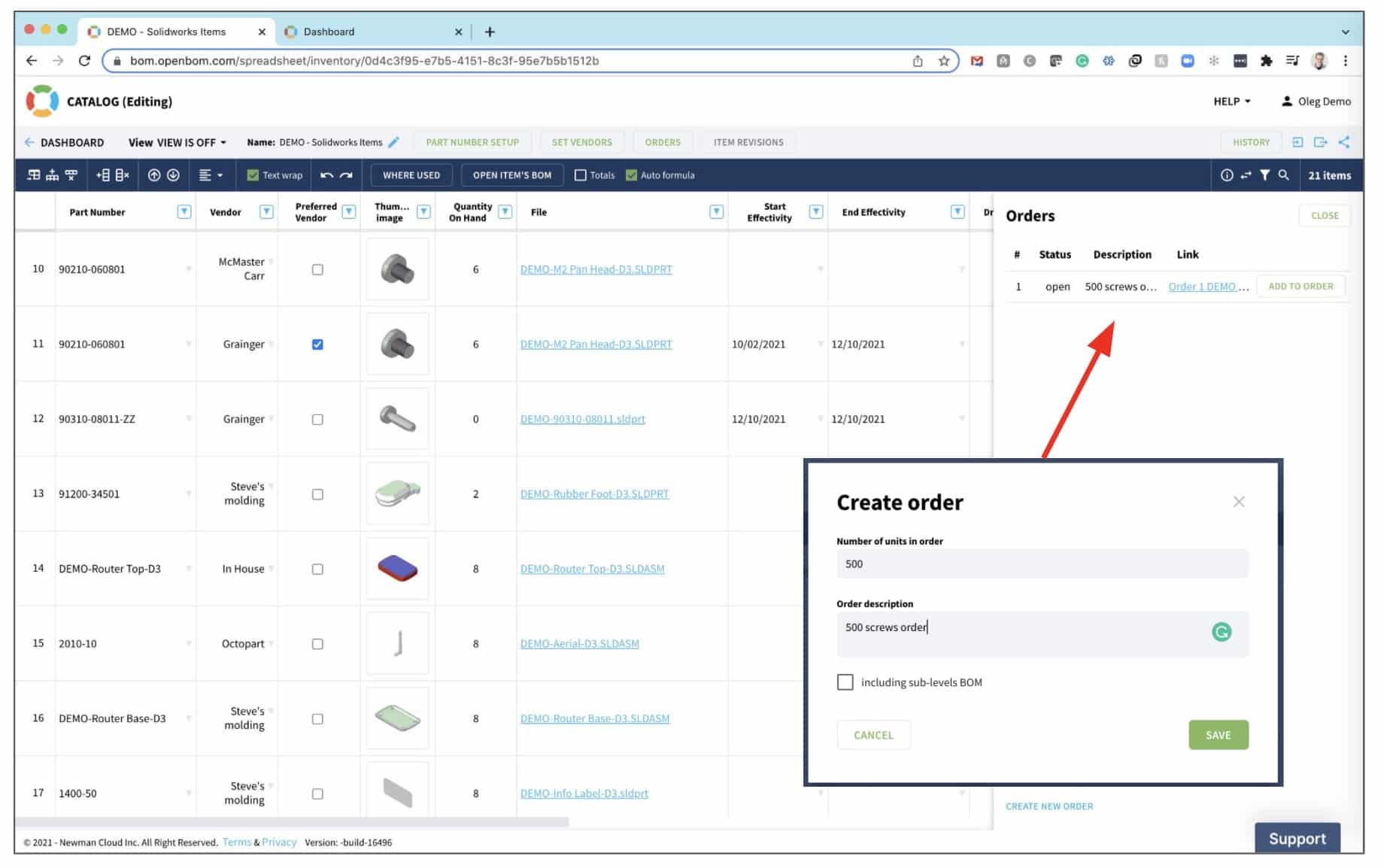
Create an Order and PO for a partial receive (quantity 50)
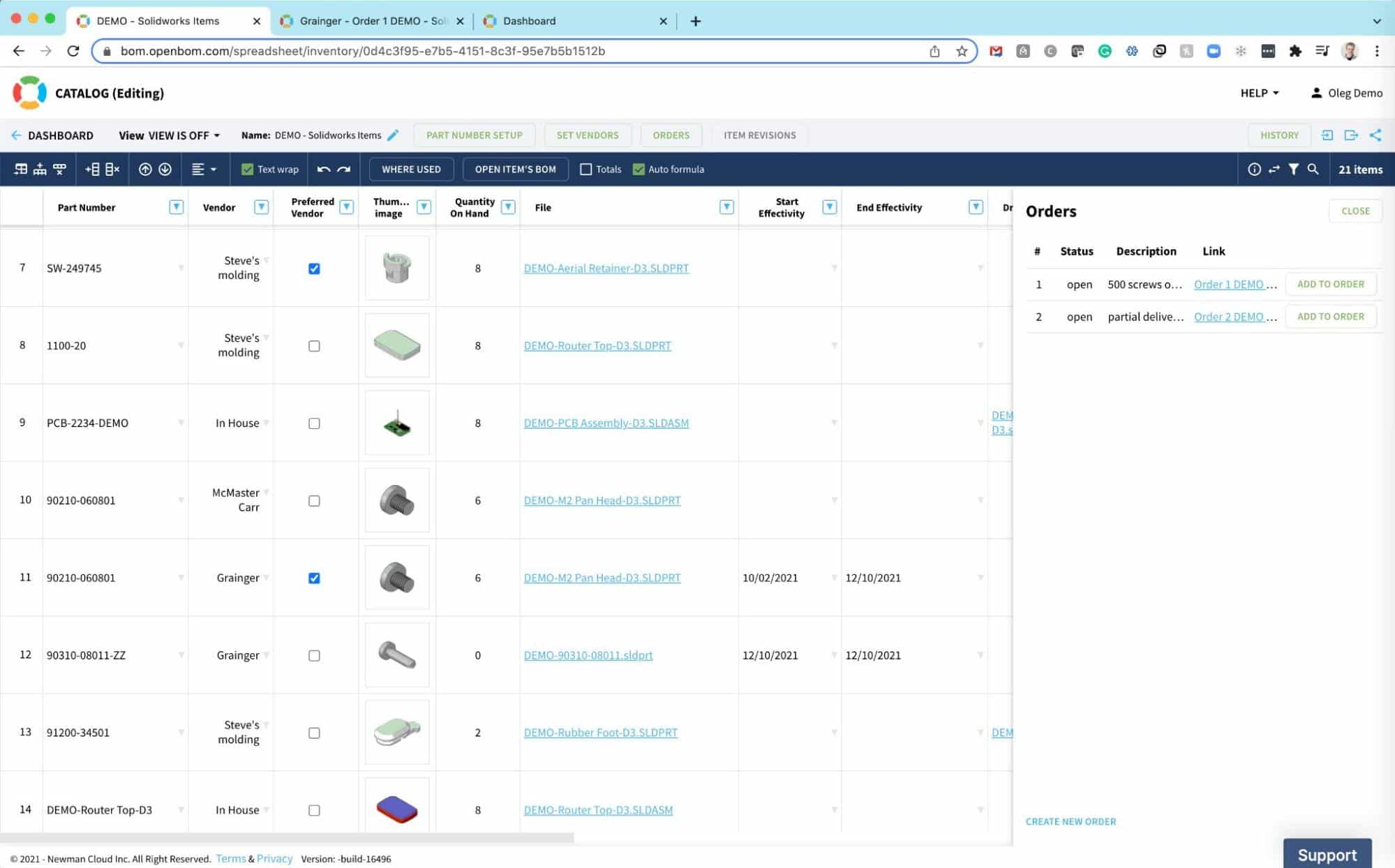
Receive PO for 50 (QOH is updated)
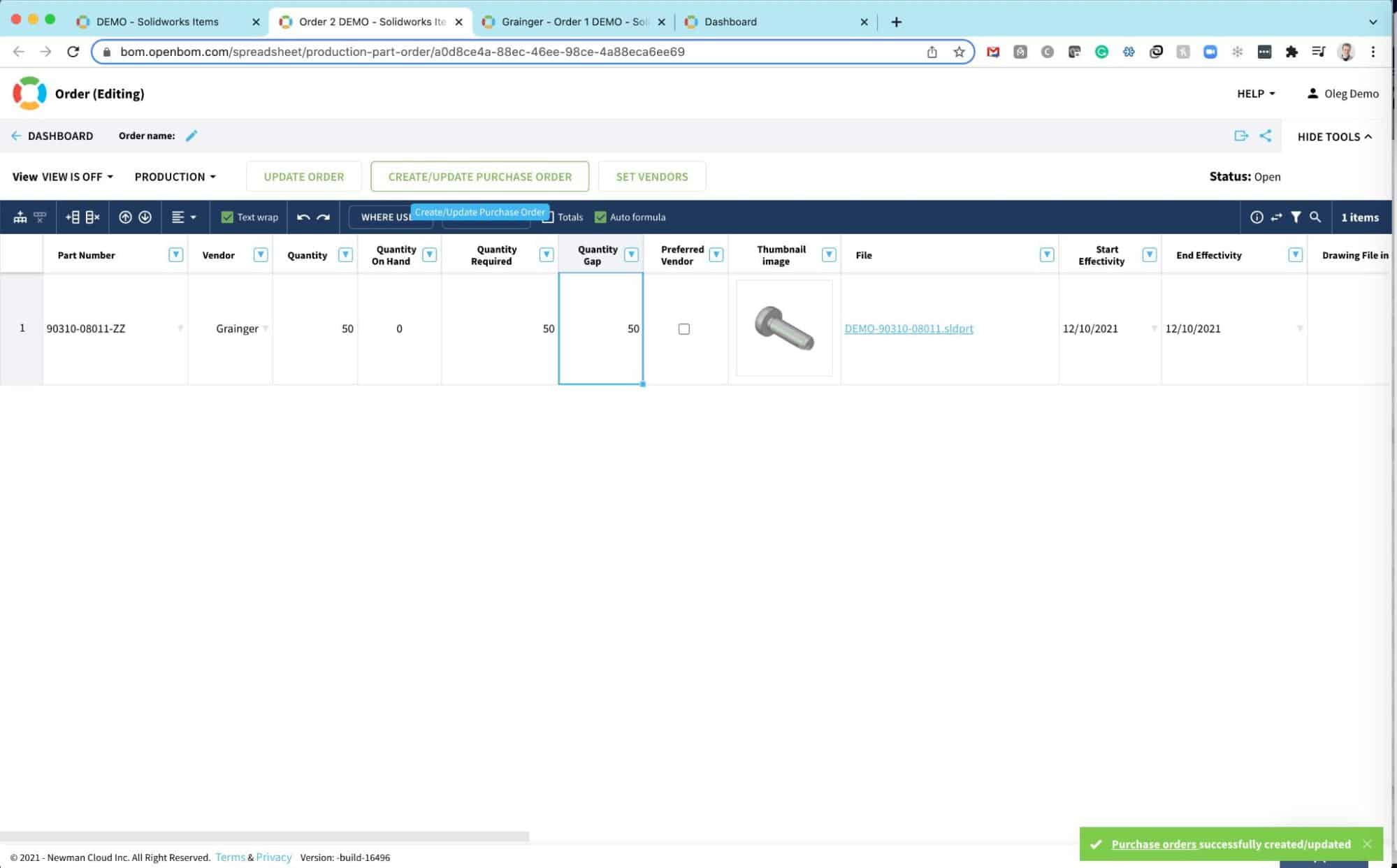
To update, the original order gap is recalculated to the difference (QOH is set to 450) and you can use it to track remaining deliveries.
Conclusion
OpenBOM’s data model and process flexibility allow you to organize and adjust processes, the Order and PO process is one of them. In a modern business environment, partial PO receive is a very often happening situation, and OpenBOM’s best practices described in the article will allow you to organize a purchasing process. We are planning to improve this process more in the upcoming releases of OpenBOM to provide an option for a partial PO received in OpenBOM.
If you haven’t yet, Try out our free 14-day trial today. As always we are here to help, feel free to reach out and talk to us about your purchasing processes and how we can help you. Contact support @ openbom dot com.
Best, Oleg
Join our newsletter to receive a weekly portion of news, articles, and tips about OpenBOM and our community.