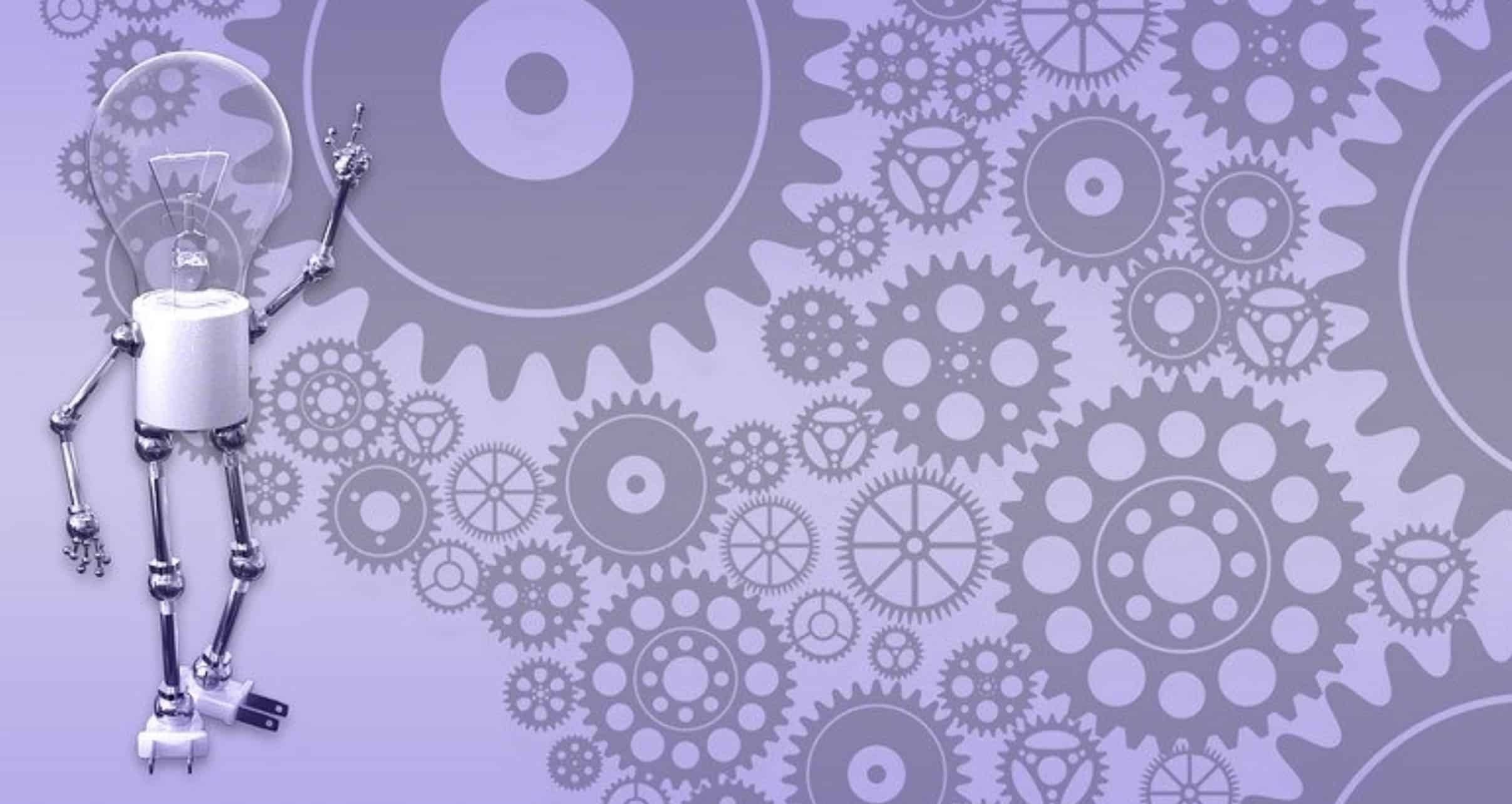
OpenBOM helps you to organize information about the product. As much as it sounds simple and obvious, the organization of the data is one of the most important and complex processes to accomplish in the organization. Even the smallest organization with just a few people can create an enormous amount of complexity by not organizing data.
So, where to start?
As I always say to our customers, if you have a mess, don’t bring the computer to the mess. Because it will create a “computerized mess”. You need to clean the data, think about data organization, classification, storage, semantics, files, and many other things. But, don’t worry, it is not as complex as it might sound from the first place.
Here is a process we recommend to have when you start working with OpenBOM to organize data and properly capture the information you have in the company.
1- Identify the existing data sources
It is very important to start with the data in- the first step. How the data is created, what systems are used to generate the data. If information is created manually, then who does it and who control the data sources. The data source can be an excel file, it can be an export from an existing system or it can be CAD files or local databases. To find all data sources, to decide what to do, what information will be transferred to OpenBOM, and what information will stay with existing data sources, how data will be exported, and synchronized is the first step to understand how to organize data.
2- Classify items and the way to collect item information
Classification of information is the process of identifying what pieces of information need to be managed and how to identify data. A typical process of information classification includes defining of Part Numbers and typical attributes that managed on the item level and instance level.
Item information represents the data that is the same for all usages of the item (think description, cost, manufacturer, etc. Data is organized in catalogs and the OpenBOM catalog defines the set of attributes for all items stored in this catalog. A set of catalogs is a classification schema. Classification can be different for each company. Usually includes, including types of items (standard, engineering), can include contractors or any other specific ways to classify.
3- To define a continuous process to create items
Once you identified sources of item information you need to decide how to manage this information. The main part of the process is to create an Item. In OpenBOM you can create items in multiple ways. The easiest and simple one is just adding an item to the catalog manually. Similarly, if you need to add an item directly from CAD system, you can use OpenBOM CAD Add-in “Save Item” command.
Another way to add items is to get them continuously imported to the catalog using Import Command. Catalog import is a powerful tool to import new item data and also import some other and merge it with the information about available items.
The last method, you can think about is to save “Create/Update Catalog” commands from OpenBOM CAD add-ins. This command can take an entire set of parts and sub-assembly in a specific design and export it to a catalog.
4- To organize access control and change process for items
OpenBOM access control is based on data ownership and sharing settings. If you’re a single OpenBOM user, nobody except you has access to items data by default. In order to get access, you will need to share the data manually. You can share with anyone who has OpenBOM account using Share command.
If you’re part of the OpenBOM Team or Company, you can share automatically the data. The default access levels are none, read-only, edit, and View. The last method involves the definitions of Team Views. Each user in the team (or company) will have a list of applied views and the list will restrict the data access.
Recommended webinars and articles:
How to Manage Data About Parts in the Bill of Materials
How many catalogs should I create in OpenBOM
The archive of all webinars is here.
If you are looking for additional information on how to optimize Bill of Materials, you can learn about the PLM (Product Lifecycle Management). Lifecycle is a critical function that traces changes of the product, it’s the BOM basics that you have to pay attention to.
Conclusion and next steps
If you accomplish everything I described above, congratulations! You don’t live a mess of spreadsheets anymore. You’ve made the first step in the organization of product information -defined items, item types, metadata, lifecycle states, how you manage revisions, and not you’re ready to start using these items in other places – Bill of Materials, Orders and other places.
Check our how OpenBOM helps thousands of users and manufacturing companies to manage data. You can be part of them.
Best, Oleg.
Want to learn more about PLM? Check out my Beyond PLM blog and PLM Book website
Read OpenBOM customer reviews on G2 Crowd to learn what customers are saying about OpenBOM.
Join our newsletter to receive a weekly portion of news, articles, and tips about OpenBOM and our community.