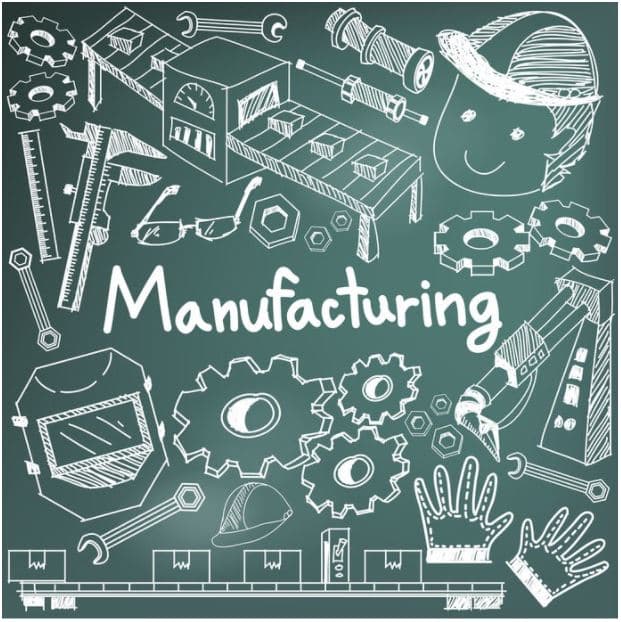
As the creators here at OpenBOM we have had the opportunity to work directly with many manufacturing companies and Engineers. This close relationship has allowed us an inside look on how our customers work and their priorities when it comes to streamlining their processes.
One question that keeps popping up is…”What should I include and exclude from my Bill of Materials?”.
It might sound strange, but after talking to thousands of users and customers, I found that the question is actually more complex than this.
Let me give you an answer and also explain how you can think of Bill of Materials as you work early in the design and later in production and manufacturing.
BOM Should Contain All Information About The Product
The answer to the question that keeps getting asked is simple – everything! The Bill of Materials (or what I like to call it, product structure with business information) includes all the information that is needed to successfully manufacture, procure and assemble the product. While this is simple, for many engineers working with Bill of Materials it is not obvious and it is very confusing.
Product Record vs Communication Protocol
Here is where engineers and companies are making mistakes. In most of the situations I’ve seen, the Bill of Materials is considered as some kind of report that is sent from one group of people to another. It is like an engineer finishing the 3D design, creating a report and sending it to the procurement or production department.
Nothing wrong, but the problem is that in such an approach, it is very easy to make some wrong decisions and assumptions. Let’s say, a procurement department knows that they need to order some materials on a constant basis and Mr. John Smith in procurement has been doing it for ages. One day, for whatever reason Mr. John Smith is no longer with the company and the materials won’t be ordered. Suddenly you figure out that the cost of this separate order is not included in the product cost estimation and the company profit goes down.
The right approach is to think about BOM (or product structure) as a product recipe – a record of everything you need to make a product delivered to the customer. In such a way, you define multiple islands of data, but they are connected together. This is a vision we have of what a Digital BOM should look like.
When To Start Working On Bill Of Materials
Another situation that happens very often is that companies start dealing with BOMs only when they start manufacturing. According to engineers and many other people, during the design and engineering phases, BOM is useless. This is a very common mistake and a big NO-NO!
Think of this method as working blindly, and working blindly will always lead to problems. Here is a perfect example…
You end up finishing a design and only then do you realize that there is some crazy constraint like parts that are expensive and available for a single supplier, shortages and long lead times. You suddenly figure out that the product will cost 30% more than you expected.
To prevent such situations from happening, you should start thinking about BOM from day one. Start planning a record, share it with the entire organization. As soon as you can create a baseline and share it with the procurement team. This and many other steps will allow you to eliminate the stress of getting into trouble in later stages.
BOM For An Entire Product
Last, but not least- you should have a BOM for entire products. Working in silos (e.g. sub-assemblies) can be easier, but you can miss some problems that only can be identified with an entire product structure loaded – eg. cost and similar parts.
Check how FF Robotics is using OpenBOM for their 16k parts robot. Using OpenBOM helped them to optimize the usage of part and simplify data access in the organization – FF Robotics Saves Times And Money by Standardizing 16K Individual Components and Optimizing BOMs.
See what their Co-Founder had to say…
“WIth over 16K individual parts, we needed a better way to manage components,” says FFRobotics co-founder Yoav Koster. “We needed to reduce the number of specific part numbers and OpenBOM makes it easy to understand where each and everyone of the components is being used,” says Yoav. Something which was not the case when he was using Excel.
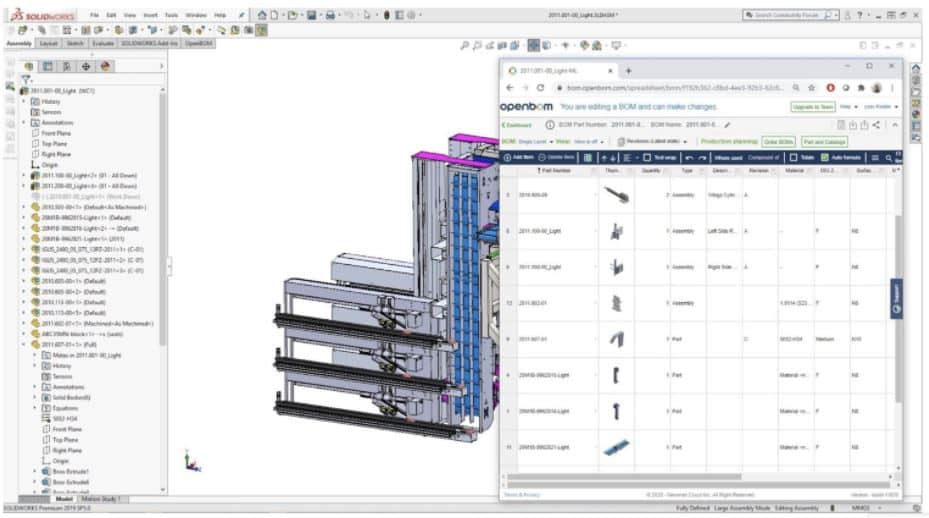
“Getting our BOMs out of Solidworks in Excel was hard. We would add some non-modeled items like hardware then have to manage all those additions individually each time we updated the Excel from Solidworks”. Using OpenBOM with SolidWorks and PDMWorks is much much easier, he says.Conclusion
Think about Bill of Materials as a full recipe of what needs to be delivered to the customer. In such a way, you can think about raw materials, standard parts, components, assembly labor, packaging, etc. The problem for many companies is to think about BOM as a protocol of communication between people. Like BOM in the drawing is a protocol of communication between engineer and the shopflow. Another BOM in Excel is a protocol of communication between engineering and procurement. The challenge of this approach is in silos and an unfortunate absence of the single place to manage an entire product information.
The earlier you start to work on a complete digital product representation, the better it is for you and the company you work for. It will establish the baseline and it will serve as a foundation for better communication, planning and after all a successful product delivered with a predictable cost.
OpenBOM can help you from day one! You can register for free to start using OpenBOM very early in the process. Our subscriptions are risk free and you will scale as you grow with your business.
Register for FREE and start your 14-days trial today.
Best, Oleg
Join our newsletter to receive a weekly portion of news, articles, and tips about OpenBOM and our community.