Bill of materials is a recipe of your product. Everything you need to make, purchase, and assembly must be placed in the BOM list. Otherwise, it will be lost, forgotten and ordered late. How to manage the process of purchasing on time? How to keep all suppliers and contractors aligned?
Manufacturing companies are continuously asking these questions, while software that can help you get the end-to-end process from early design to purchasing is very rare to find. Especially if you’re a small or medium-sized OEM manufacturing, which is capable to keep IT and manage tons of software for each business function — design (CAD), engineering data (PDM), change management process and BOM (PLM), procurement planning and finance (ERP).
Small companies are lean, nimble, and agile. Also, their contractors are distributed across the globe and they need to stay continuously connected with colleagues, engineers, suppliers, manufacturing shop, and customers. Email and spreadsheets are flexible enough, but this process of managing information using Excel can barely scale to support the complexity of data needed to engineer and develop products.
Today, I want to discuss one problem from a variety of others that manufacturing companies need to solve — how to manage the sourcing of components from multiple suppliers in the same bill of materials?
OpenBOM reference-instance model is giving you an easy way to split information about components (engineering and standard) in catalogs and their usage in BOMs.
Check more here.
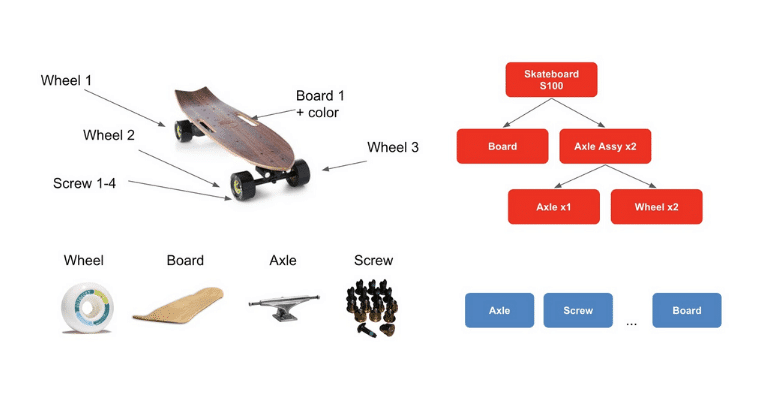
I want to show you how OpenBOM enhanced catalogs to support multiple vendors for a single part.
OpenBOM catalog is used to assign multiple vendors to the same Part Number.
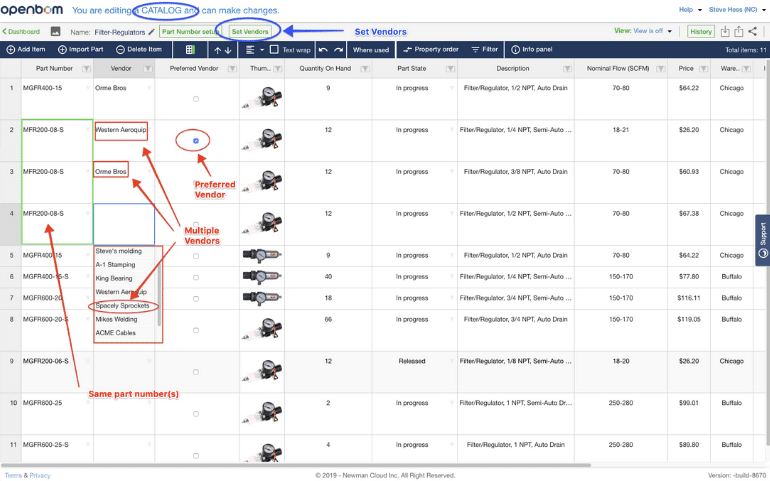
In order to select which vendor is preferred, specify “Preferred” Vendor in Catalog and new Duplicate Item function:
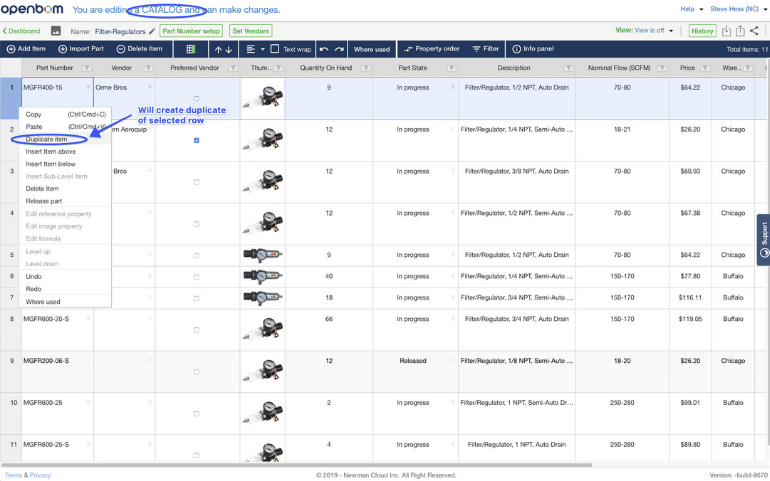
Once it is done, you can create a BOM and OpenBOM will automatically select the vendor you’re going to receive a source part from.
This video illustrates the new multiple vendor functionality while taking you through the process of upgrading your existing Catalogs to support multiple vendors. It’s a must-see video.
The remaining question is how to change a part sourcing in a specific order. You can do it in the Order BOM. Tomorrow I’m going to show you how to do so.
Conclusion
OpenBOM is focusing on how to organize a connected process for a manufacturing shop managing parts, BOMs, vendors, and purchases. It provides a cloud-based data foundation capable to manage structure data set reflecting the product information (BOM and related data), as well as organize transformation of BOMs from design to planning and from planning to purchases.
If you are a manufacturing company, contractor or supplier, you should find it useful. And if not, please talk to me — I’d be happy to help.
Register to create Free OpenBOM account and start your Design to Purchasing process transformation.
Best, Oleg
PS. Let’s get to know each other better. If you live in the Greater Boston area, I invite you for a coffee together (coffee is on me). If not nearby, let’s have a virtual coffee session — I will figure out how to send you a real coffee.
Want to learn more about PLM? Check out my Beyond PLM blog and PLM Book website.
Join our newsletter to receive a weekly portion of news, articles, and tips about OpenBOM and our community.