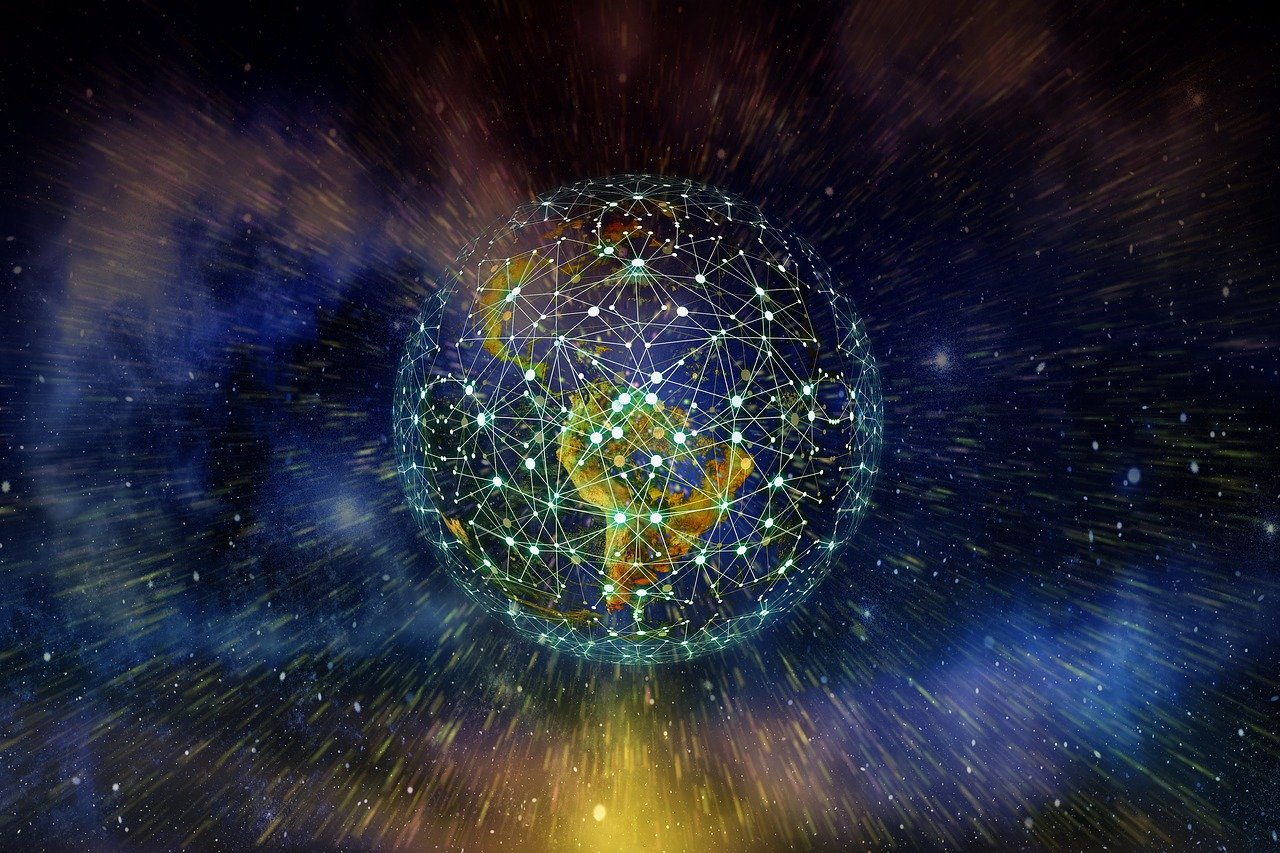
The last six months of COVID19 exposed one of the biggest challenges of many supply chains – to sustain large-scale disruptions and to provide flexible and fast adaptation to new product development and manufacturing conditions. While many manufacturing companies suffered closures because of lack of supplies, others suffered from their lack of new sources to ramp up the manufacturing of medical devices and protective equipment.
One of the best ways to make the supply chain more resilient is to be ready upfront and provide a network of suppliers, manufacturing plants, and other elements of the manufacturing network. For many manufacturing, it became obvious the need to apply a test and simulate how sustainable their manufacturing capacity and supplier network in case of emergency, closure of contractors plants, unavailable workforce, and many other factors that can risk their manufacturing capacity.
How to create a network of suppliers and simulate the test is an interesting question that is demanded by many manufacturing. Risk mitigation systems are available, but the dynamics and unpredictability of modern manufacturing environments is too high and you can quickly run into high-level uncertainty. How to identify bottlenecks, single sources of suppliers, and other elements of your manufacturing process?
Modern manufacturing products are not made by a single company and combined from parts made by hundreds or sometimes even bigger numbers of suppliers. Think about this product and it is easy to imagine how the absence of a single supplier can disrupt an entire manufacturing and production process.
The story of the Fukushima quake is only one that can give you an idea of how a single supplier can disrupt an entire industry.
Since the 2011 disaster, global auto suppliers have changed the way they produce and source the 30,000 parts required to assemble a single car, including raising stocks, diversifying production and creating alternative manufacturing capabilities. “The costs of maintaining extra inventory, or the view that extra inventory may be wasteful are considered to be reasons not to hold more stock,” said Hiroaki Mochida, an analyst at Marusan Securities.
A spokesman at Japan’s Renesas Electronics Corp, whose plant in Ibaraki Prefecture that produces microcontrollers used in automobiles was devastated in 2011, said it had not increased its inventories as a risk management strategy. However, he said it had begun to standardize more parts across vehicle models to improve efficiency and enable alternative production during emergencies.
Identifying risks in supply chain management is a topic many manufacturing companies are working on and looking for solutions to solve it.
Firms are exposed to a variety of low-probability, high-impact risks that can disrupt their operations and supply chains. These risks are difficult to predict and quantify; therefore, they are difficult to manage. As a result, managers may suboptimally deploy countermeasures, leaving their firms exposed to some risks, while wasting resources to mitigate other risks that would not cause significant damage. In a three-year research engagement with Ford Motor Company, we addressed this practical need by developing a novel risk-exposure model that assesses the impact of a disruption originating anywhere in a firm’s supply chain.
Modern data management technologies can open a new way of identifying risks and one of them can be taken from analyzing product information and finding possible supply chain bottlenecks. Manufacturing companies are diving in the ocean of product and supply chain information. However, for a long time, the challenge is to analyze the information was a showstopper to find possible solutions.
Cloud computing and novel data management including graph databases and multi-tenant data models can be used to accumulate information from multiple companies, anonymize the information, and find possible bottlenecks. A risk analysis based on analysis of product information cab be performed to identify a single-source supplier, find a bottleneck, and prevent future manufacturing disruption. Flexible data modeling, automation, and cloud-scale can bring such systems to manufacturing companies and tests the vulnerability of their supply chains.
Conclusion
Modern product data management technologies are using scalable cloud-based computing combined with novel graph databases enabling a new level of intelligence in organizing data and finding sources of potential problems in manufacturing processes. Collecting information about products, fusing the information between design, manufacturing, and finance and later applying intelligence based on information coming from multiple companies in the anonymous form will give a new way to mitigate the risks of supply chain and build resilient manufacturing networks.
At OpenBOM, we build new SaaS products providing data management solutions for manufacturing companies helping to connect product design, manufacturing, and procurement. The foundation of OpenBOM is scalable multi-tenant data management technology allowing securely manage data from multiple companies and help companies to build a secure way to reduce risks of supply chain disruptions.
Best, Oleg @ openbom dot com.
Want to learn more about PLM? Check out my Beyond PLM blog and PLM Book website
Read OpenBOM customer reviews on G2 Crowd to learn what customers are saying about OpenBOM.
Join our newsletter to receive a weekly portion of news, articles, and tips about OpenBOM and our community.