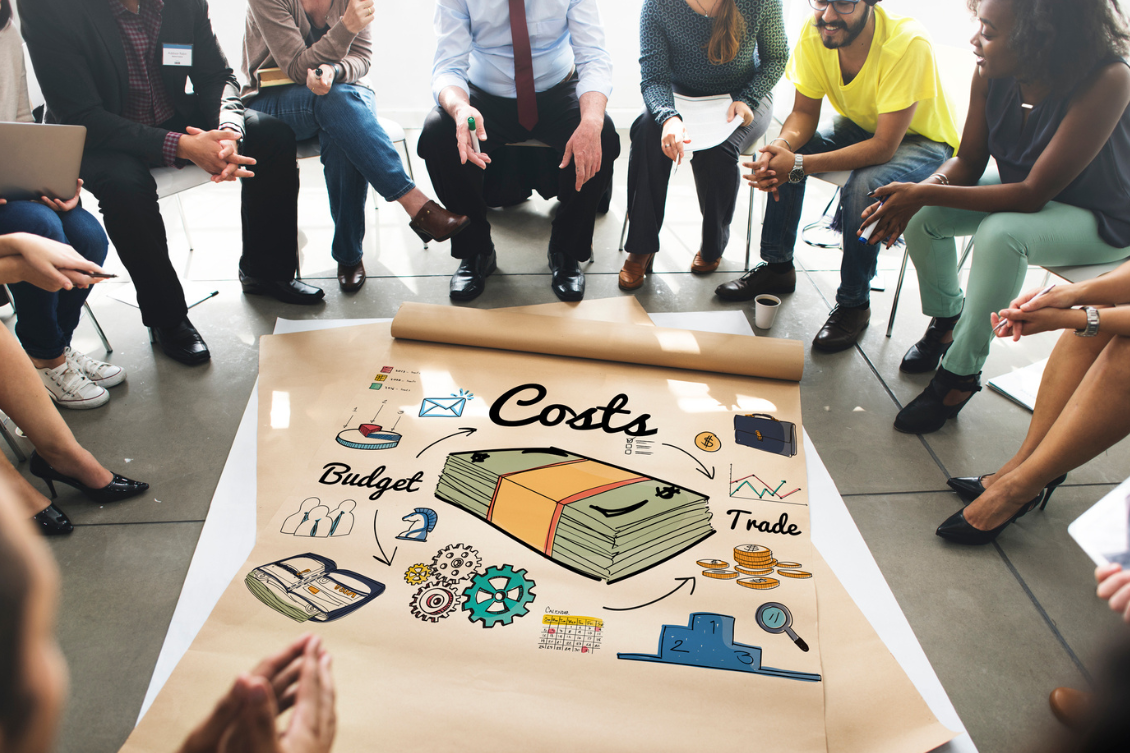
In every manufacturing business, cost is a critical factor that can determine success or failure. Efficient cost management is essential for maintaining profitability, competitiveness, and sustainability. Despite its importance, cost is often treated as a secondary concern in many systems, especially in data management scenarios. It is frequently overlooked or inadequately addressed, leading to inefficiencies and missed opportunities for optimization.
Where Can You Find Cost Information?
A simple question of where you can find the cost info in Engineering Teams and Manufacturing Companies might not be that simple to answer. In the complex landscape of manufacturing, pinpointing responsibility for cost management can be challenging.
While everyone acknowledges the importance of cost, its integration into daily workflows is fragmented. Engineers tend to keep all relevant data within CAD systems, but cost data is not typically included here. Cost management requires pairing with supplier information, minimum order quantities (MOQ), and pricing details, none of which are available in CAD systems.
On the other hand, procurement, ERP, and MRP systems are designed to manage purchasing activities and costs. However, these systems often lack precise engineering details about components, making it difficult to align supplier part numbers and manufacturers with the technical specifications. Finance departments track all purchase orders and expenses but usually lack the technical details necessary to make informed cost decisions on components and assemblies.
So, as you can see, although everyone will agree that cost is very important, it is hard to find the right place where to manage it. Even more, it is hard for all people involved to get on the same page and collaborate in the process of setting all descriptions, vendors, costs, and other options.
The Reality of Cost Management and Collaboration
As much as it sounds obvious, cost management must be centralized. In practice, cost management and collaboration are often disjointed processes. The procurement team and supply chain organizations typically pull cost information from various sources, attempting to manage cost rollups, optimize expenses, and collaborate with engineers to clarify component specifications. This fragmented approach requires collaboration across multiple teams, including engineering, finance, procurement, and production.
Despite the desire to use a special tool to handle cost management tasks, many organizations still rely on Excel as their primary tool for cost management and collaboration. Excel, while versatile, is often a suboptimal solution that serves as a common lowest denominator rather than an ideal tool for comprehensive cost management.
Cost Management – Possible Alternatives
There are two aspects of cost management. One is calculating the cost to make a part. You pull geometry, manufacturing methods, and materials and get the results. There are tools to do so integrated in CAD systems. For standard (off-the-shelf) components, online catalogs can do the job (eg. McMaster Carr, Fastenal, Octopart, etc). This is not what I’m planning to talk about. I want to talk about the solutions for integrating cost management with design and procurement processes where the focus is on product cost assessment, optimization cost, and mitigating risks in materials and supply chain.
There are several alternatives systems that come to mind – CAD, PDM/PLM, and ERP. Each has its own set of advantages and disadvantages. Here is my analysis.
CAD Systems
Pros:
- Detailed Engineering Data: CAD systems excel in providing detailed and precise engineering data.
- Design Integration: Engineers can easily access and modify design-related information.
- Visual Representation: Allows for detailed visual representation of components and assemblies.
Cons:
- Lack of Cost Information: CAD systems typically do not include cost data, making it difficult to manage costs directly within these systems.
- No Supplier Integration: Information about suppliers, pricing, and MOQs is generally not available.
- Limited Collaboration: While excellent for design, CAD systems are not designed for broad collaboration on cost and procurement matters.
PDM/PLM Tools
Pros:
- Comprehensive Engineering Data: PDM/PLM tools manage detailed engineering data and product lifecycles effectively.
- Change Management: These tools offer robust change management capabilities, crucial for maintaining data integrity.
- Integration with CAD: Often seamlessly integrates with CAD systems, ensuring that engineering data is up-to-date.
Cons:
- Lack of Cost Calculations: Typically lacks capabilities for cost rollups and detailed cost management.
- No Supplier Management: This does not usually include tools for managing supplier information and costs.
- Complexity: It can be complex and expensive to implement and maintain, requiring significant resources.
ERP Systems
Pros:
- Comprehensive Business Management: ERP systems manage a wide range of business processes, including procurement, inventory, and financials.
- Cost Tracking: Provides detailed tracking of purchase orders and costs.
- Supplier Management: Includes tools for managing supplier information and procurement processes.
Cons:
- Lack of Engineering Detail: ERP systems often lack detailed engineering data necessary for precise cost management.
- Integration Challenges: Integrating ERP systems with CAD and PLM tools can be challenging and costly.
- Limited Flexibility: ERP systems can be rigid and difficult to adapt to specific business needs without significant customization.
As you can see, with a plethora of options, cost management and collaboration usually “fall between chairs” and companies have a hard time finding the right solution.
How OpenBOM Can Help?
At OpenBOM, we take the problem of cost management seriously. It starts with data management and ends up with easy-to-set-up formulas, rollups, and inventory management.
OpenBOM offers a compelling alternative with several key advantages:
- Robust Product Data Model: OpenBOM provides a comprehensive data model that can handle complex product structures and associated cost data.
- Connected to CAD: Seamlessly integrates with CAD systems, ensuring that engineering data and cost information are connected.
- Vendor and Cost Management: Manages vendor-specific costs, allowing for accurate cost comparisons and supplier evaluations.
- Cost Rollup: Provides powerful cost rollup capabilities, enabling detailed cost analysis and optimization.
- Inventory Management: Manages inventory levels, helping determine if components need to be ordered or are already available.
OpenBOM can turbocharge your cost rollup experience and make people accelerate the product development process.
What about collaboration? OpenBOM patented BOM collaboration methods allow multiple team members to be “on the same BOM” and literally make changes at the same time. Managing multiple BOMs with the same components and getting combined aggregated planning options.
Conclusion
OpenBOM offers a robust set of highly configurable tools designed to pull information from multiple sources, share data between team members, and enable collaborative cost assessments. By integrating engineering, procurement, and financial data, OpenBOM helps streamline cost management processes and improve decision-making. Register for free to explore how OpenBOM can revolutionize cost management in your organization.
REGISTER FOR FREE and check how OpenBOM can help.
Best, Oleg
Join our newsletter to receive a weekly portion of news, articles, and tips about OpenBOM and our community.