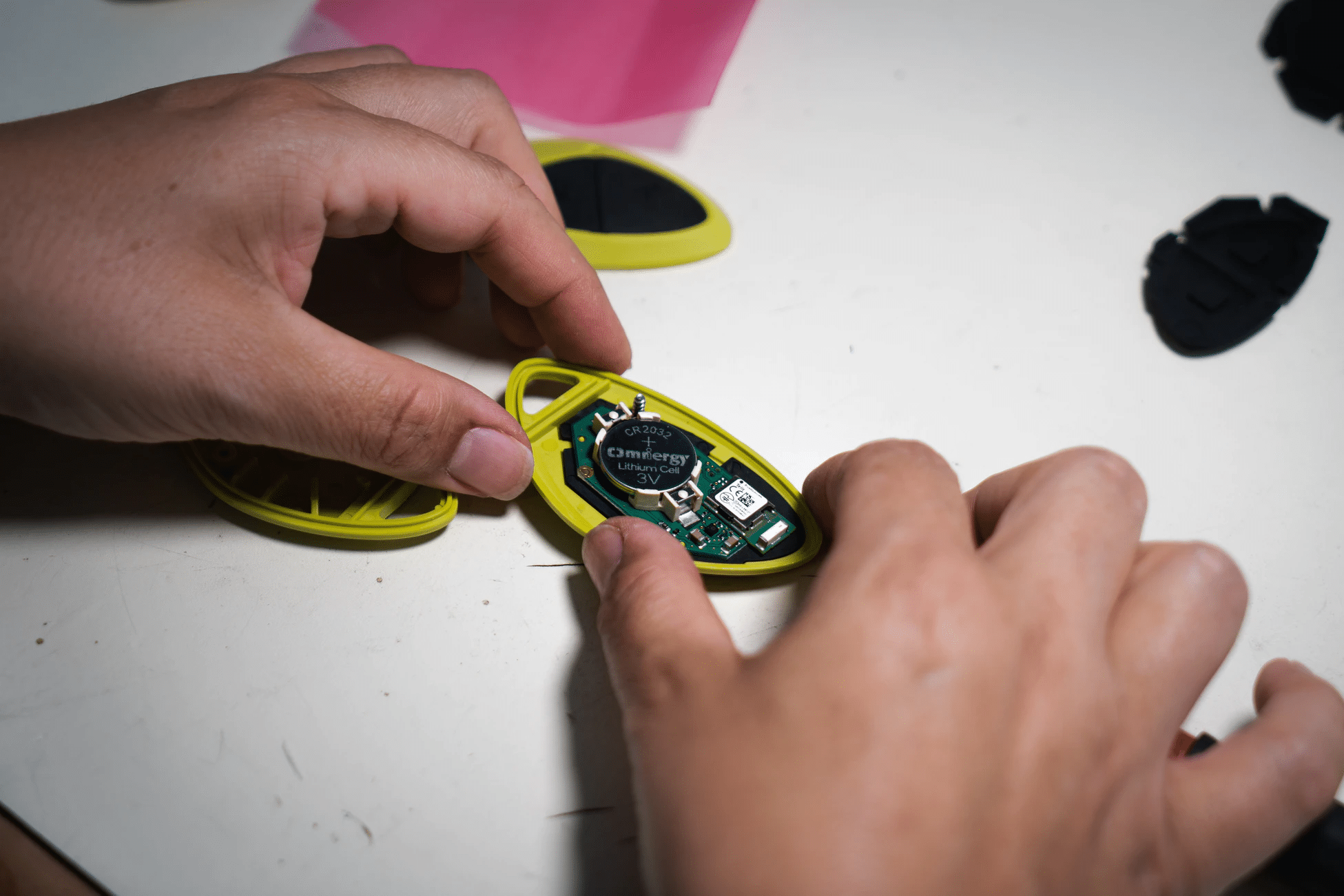
In my previous article, we discussed design for manufacturing (DFM) and why it is necessary.
As a refresher, as stated from Quality-One, DFM “enables a product design to be efficiently manufactured and easily assembled with minimum labor cost. Through the use of DFM/A, a company can prevent, detect, quantify and eliminate waste and manufacturing inefficiency within a product design.”
In other words, DFM is done to transition you from later stage development to production and allows you to scale up. However, who should you work with in order to proceed? With my background in contract manufacturing, I would like to share with you the journey of having your CM provide you with DFM support.
The Start of the Process
Getting your CM involved varies depending on the trust and experience you have with them. For example, if we currently manufacture a product for a client and they are developing a new product, we will most likely get involved with development before we quote it.
However, if they are a new client, we will go through the typical RFQ process. During our quotation process, there is back and forth so we can understand the logic of certain materials, processes and components used but our goal is to provide a quote. From studying the design, we can also provide them with a tentative DFM plan with the product quote.
At this point, we have a product that is usually not optimized for production and a quote reflecting the part that can not be made as efficiently as possible. This is when we will launch DFM.
The Steps & Questions to Ask
I am sure you have heard the three rules of real estate: location, location, and location. For DFM you can look at it similarly, optimize, optimize and optimize. You want to set yourself up for a clean production run with limited waste and quality issues.
Remember that you should not give final authority to your contract manufacturer on all changes. You need to set up a change management process, or an ECO/ECR process in which your CM can freely request changes. But they are just that, requests. Think about how all requests will affect the end product and the certification process you need to follow.
Here are some basic questions that we need to ask ourselves and answer during a DFM project. These are not all of them but enough to get you thinking.
Questions for Parts:
- Is it more cost-effective to use alternative parts, materials, or processes? Such as going from laser cutting to stamping or from CNC machining to die cast.
- What is the machine size (tonnage) needed in order to make this part effectively?
- What are the tolerances for the part vs the acceptable tolerance from the specified manufacturing method?
- What are the most expensive parts and how can we cost them down?
Questions for Assembly:
- How can the parts be assembled?
- What jigs are needed?
- What are design changes that can make it easier to assemble?
Questions for off-the Shelf Components:
- Are these parts readily available?
- Are they a cost-effective option?
- What alternatives are available?
Questions for Tooling:
- What changes are possible to decrease the cost/investment?
- Will there be any textures on the tool?
- What is the finest tolerance achievable for the tool?
Why should your CM support DFM?
The answer is quite simple, the company making your product should have the best expertise on how to efficiently and effectively make your product. When looking at the questions above, they are mostly related to manufacturing processes, sourcing, pricing, and more. These are all questions the company contracted to make should be understood.
This is assuming that the CM you choose is not stuck in the 1970’s with old equipment and outdated processes. This is also why evaluating your supplier is so important to understand what services they can provide you with.
You also don’t need to expect your CM to do everything. They should leverage their supply chain network. So, if they don’t have plastics in-house, then they should be working with their plastics supplier on DFM for both part and tooling.
Conclusion and How OpenBOM Can Help you?
OpenBOM improves the process of how you work with your CM, contractors, colleagues, and other team members. We provide you with the capabilities to seamlessly manage your parts, vendors, bill of materials, purchase orders, and change orders. All BOM, engineering, and manufacturing information is stored in the cloud which you can share with anyone.
Register for FREE to create your OpenBOM account and reach out to us via support @ openbom dot com if you have any questions.
Best, Jared
Join our newsletter to receive a weekly portion of news, articles, and tips about OpenBOM and our community.