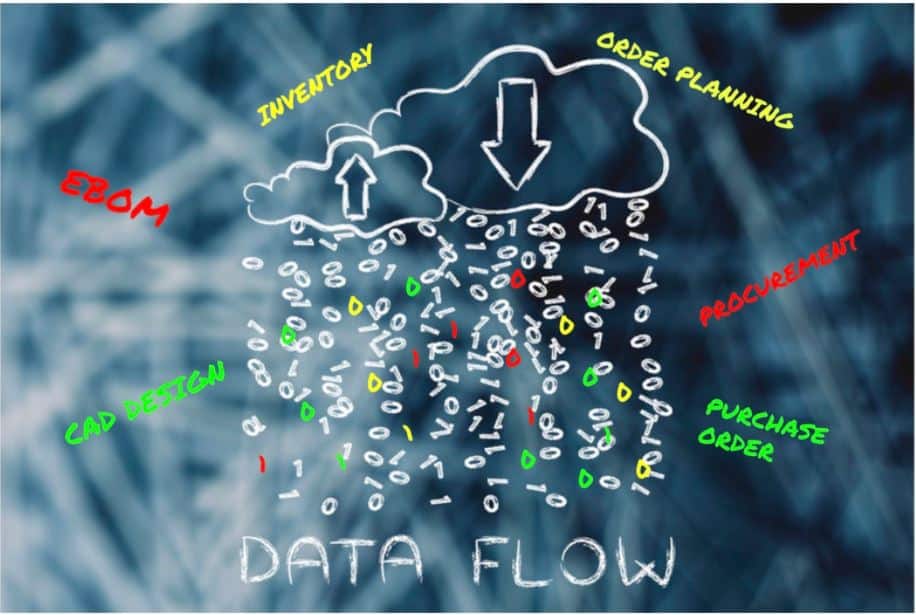
As someone who has spoken and dealt with many engineering teams and manufacturing companies, I’ve seen a lot of examples of inefficient information flows between individual users, teams, departments, contractors, and suppliers.
Therefore when somebody tells me about creating another Excel spreadsheet from the CAD system and sending it to a procurement team, I usually cringe because I know how things will end.
The company creates a vicious loop of interaction between trying to optimize the data and the process flow, which leads to them stepping on each other’s toes when they do updates on both sides. It is repeatable and leads to mistakes, miscommunication, wrong orders of components, and additional expenses.
The Law of The Instrument
To organize and optimize the information flow in the company is a big challenge. This is where companies should spend more time coming up with the organizational strategy of managing information and stop thinking in silos.
While planning is very important, the tools used in the process can be just as important. Remember, the law of the instrument if all you have is a hammer, everything looks like a nail. So, following this law, if everything you have is a spreadsheet, you’re going to end up with messy emails with Excel attachments flying around.
From Silos to Optimized Information Flow
At OpenBOM, we’ve been rethinking the tool, by creating technologies and organizing the way to optimize the information flow between teams working in product development. It includes three main elements:
- We built a cloud-based data management system with direct drop-in within Solidworks. It allows you to support the first step of the communication process – seamless extracting the data from any Solidworks assembly and organizing it in a product structure capable of counting parts, assemblies, making calculations, etc.
- Manage a flexible catalog of all items (materials, parts, assemblies, etc) in the way to allow their metadata management as well as management of inventory levels (Quantity on Hands).
- Organizing the process of seamless data flow between two sides of the product development process (engineering – design and production planning/procurement).
OpenBOM Production Planning
In our recent articles with VIDEO stories about product planning, we described in detail how OpenBOM helps to organize and streamline information data flow and supports the handover of the data between people inside organizations as well as between contractors and suppliers. Check it out here – Production Planning – VIDEO Stories.
I’d like to share a video where we demonstrate a very typical situation – the turnaround in data flow between engineering (BOM) and procurement (Order) changes. This is a scenario that probably happens in 100% of organizations when the initial ordering plan needs to be corrected or adjusted. Change is the only constant, so these things are happening all the time.
Check this video Out…
Conclusion
The main goal of any Data Management should be to change the paradigm and focus on information flow optimization.
You need to step outside of silo thinking and apply the data strategy of connecting people and processes together. OpenBOM production planning process is a simple, yet powerful and most importantly flexible way to organize data flow and collaborate to achieve optimal organizational performance.
Check it for yourself. Register for FREE to OpenBOM and start a 14-day trial to discover how OpenBOM can help.
Best, Oleg
Join our newsletter to receive a weekly portion of news, articles, and tips about OpenBOM and our community.