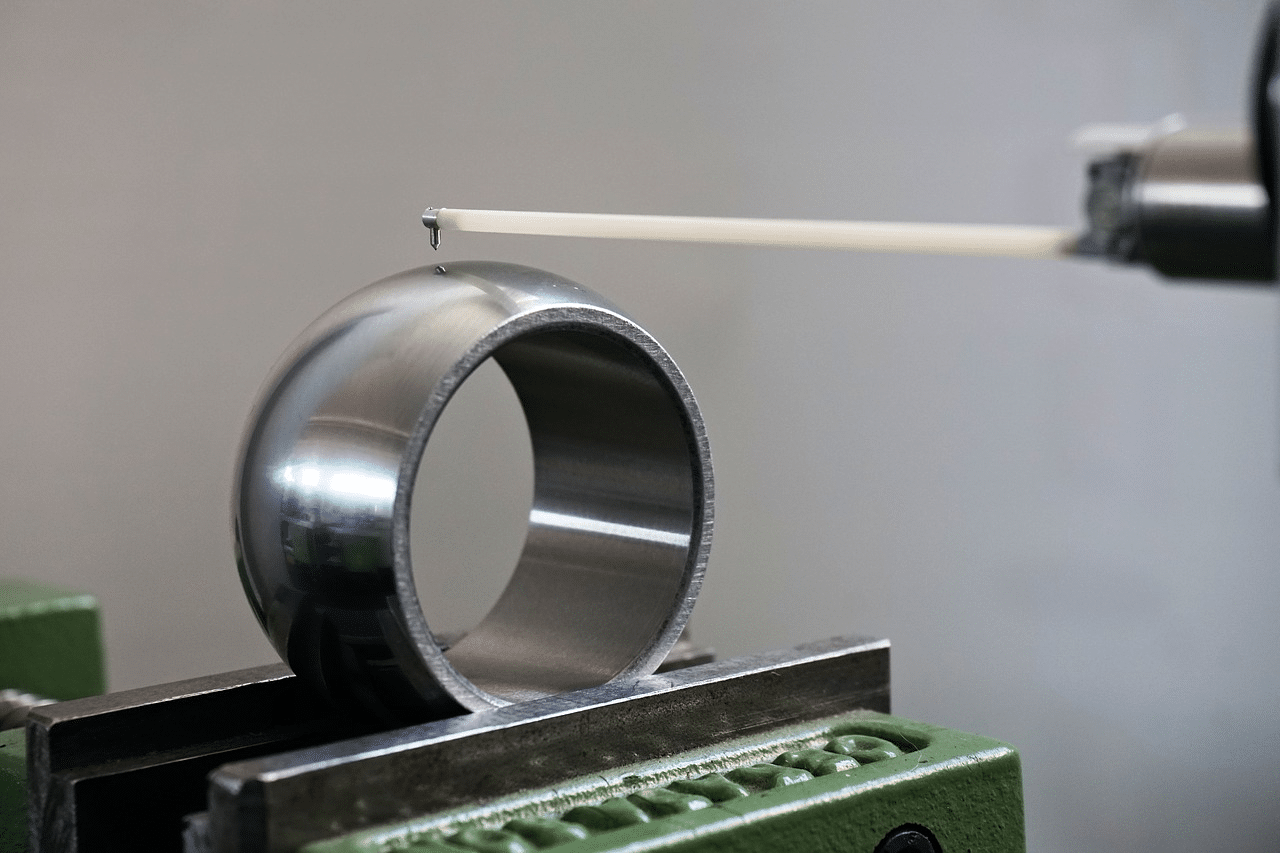
Ask anyone that has made a product, and they’ll tell you that quality standard is one of the most frequently used documents during production. This standard and checklist will be used to ensure production is consistent and that you receive what you expect every time. It creates consistency.
Quality Checklist Document and Process
Since this document is so important, how should you go about making it and who should you consult with? There are three parties you should involve:
- Your Customers
- Your Engineering & Quality Teams
- Your Contract Manufacturer or Supplier
Since the first two, your customers and your engineering and quality teams are focused on you, I’ll dive more into consulting with your contract manufacturer (CM) or suppliers.
For some reason, companies do not like to involve their CM or supplier while creating the quality checklist. This is most likely because they believe the CM or supplier will push back and complain. But then you need to question if they are the right supplier.
InTouch-Quality sums it up best of why you need to include your supplier, “you limit the risk that your supplier will later manufacture a product that doesn’t meet your requirements.” If you do not collaborate with your supplier, they might not know each requirement or worse, might not be able to make it to the specified requirement.
There are multiple reasons to include your CM and supplier while making the quality standard.
Experience & Knowledge
The most important reason why you need to include your supplier is that they know the materials and processes best. They have most likely manufactured similar parts for other companies and they have that experience and knowledge of what will work and what will not work. You should be leveraging your supplier for this information so you can create the most reliable quality standard you can create.
Your supplier can also inform you of where certain parts should be checked. There are three areas to check quality.
- Incoming Quality Control IQC) – These will include off-the-shelf parts, raw materials, and outsourced components and parts. In general, they are parts and materials that come in from the outside.
- In-Process Quality Control (PQC) – These are parts that are being fabricated or any other secondary process and assembly. For example, a part that is CNC, anodized then laser etched will include IQC during all of these separate processes.
- Final Quality Control (FQC) – Parts that have been final assembled. These will usually consist of functional tests of the final product.
Have it be Attainable
There are certain processes that can not hold the tolerances you are looking for. In this case, collaborating with your CM or supplier would be very beneficial. Not just because they will decline but because they will recommend and propose changes towards processes and secondary processes that can hold these tight tolerances.
Things You Might Miss
The quality standard must be objective and thorough. If you have never filled out a standard, you might be a bit lost and not sure on exactly what to add and where to look. For simple parts, they’re most likely just checking dimensions. But other more complex parts and functional tests deserve a thorough inspection and procedures.
Supply Chain Accountability
Depending on the type of product, your CM will most likely be using their supply base (tier 2 and tier 3 suppliers) to procure parts. Your CM will hold their suppliers accountable for the parts they provide. They hold them accountable from the QC standard. It is also a standard process for your CM to receive input from the suppliers about the standard as well.
Who is OpenBOM?
OpenBOM improves the process of how you work with your suppliers, contractors, colleagues, and other team members. We provide you with the capabilities to seamlessly manage your parts, vendors, bill of materials, purchase orders, and change orders. All BOM, engineering, and manufacturing information are stored in the cloud which you can share with anyone.
Register for FREE to create your OpenBOM account and reach out to us via support @ openbom dot com if you have any questions.
Regards,
Jared Haw
Join our newsletter to receive a weekly portion of news, articles, and tips about OpenBOM and our community.