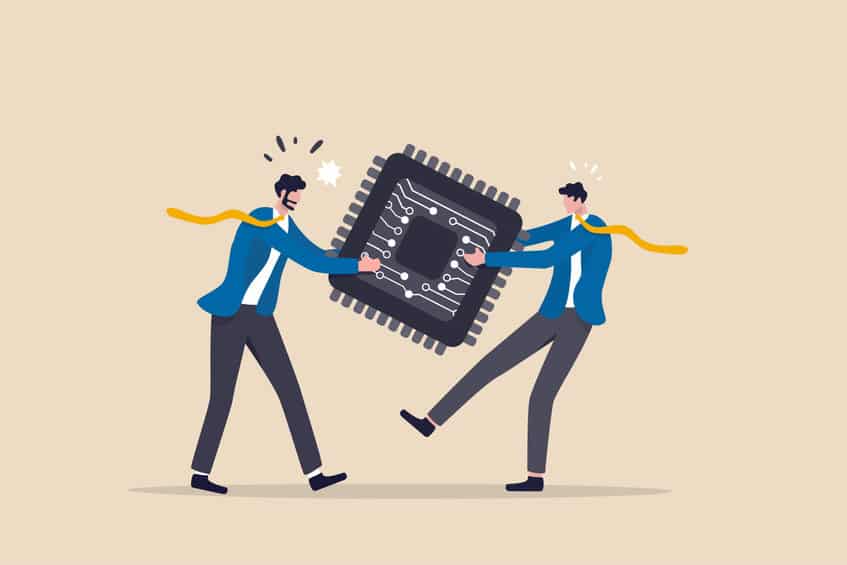
As manufacturers continue to feel the sting of supply chain shortages, many are turning to new strategies to ensure they can keep production lines running. To cope with such a problem, companies need to perform multiple orders and hope that some of them will be delivered and, if they will be delivered, will bring the right quantities. This allows manufacturers to partially receive goods from suppliers, ensuring they have enough components, even so, they are ordering them from more than one vendor using multiple POs. In this blog post, we’ll take a closer look at the partial PO (purchase order) receive function and how it can help your business cope with supply chain shortages.
How to make concurrent POs and optimize the stock levels?
A few weeks ago, I shared an article with the best practice on how OpenBOM allows you to make concurrent orders. The picture below shows an idea of how you can organize concurrent orders of parts to get the materials and components from multiple suppliers.
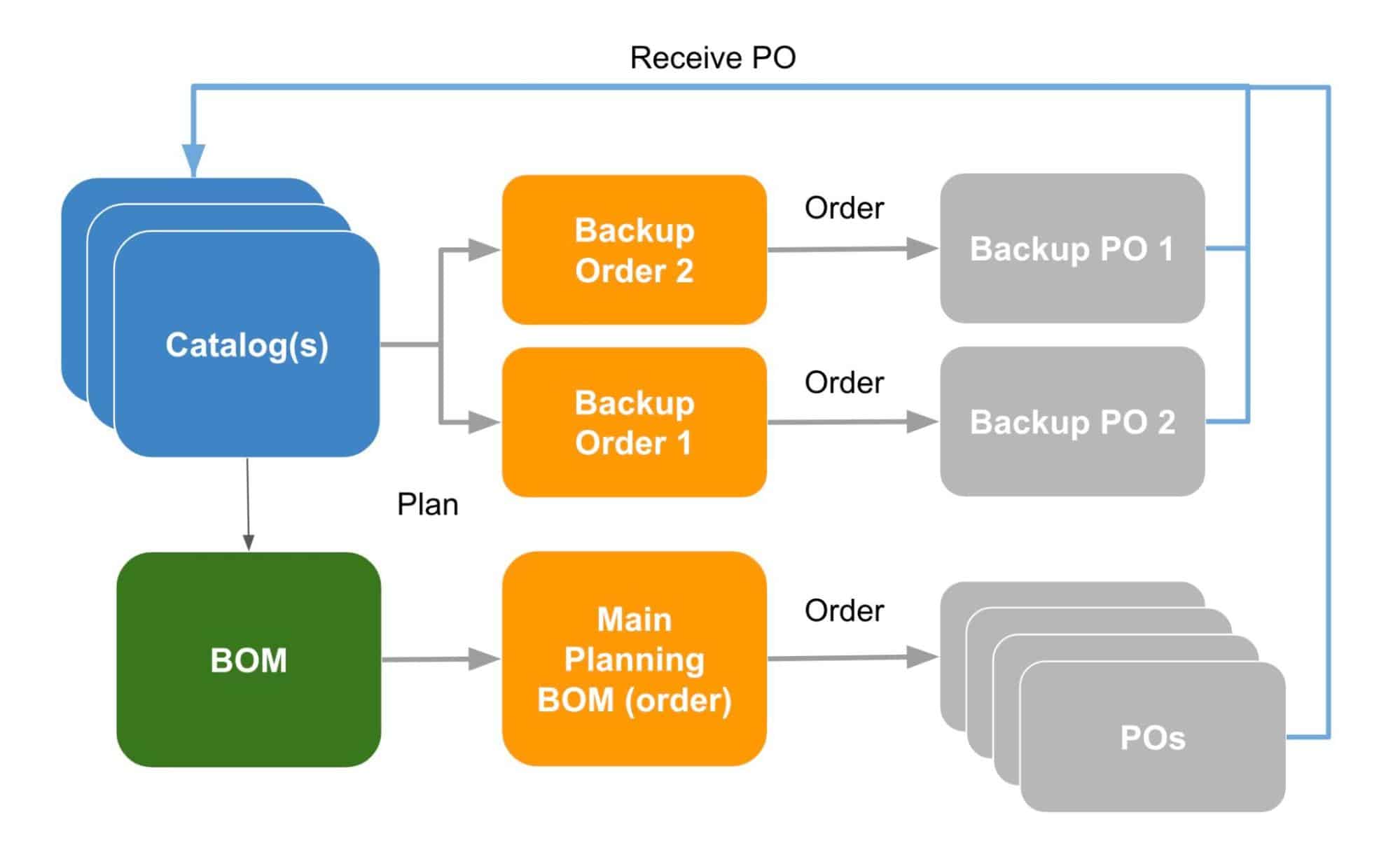
The idea works and you can make these “Backup orders”. However, the processes can be even more optimized by using a new method of partial PO.
What is Partial PO and How does it work?
The idea of “partial PO” is pretty simple. Instead of manually creating Backup Orders as I explained in the previous picture, OpenBOM will help you make this backup order automatically and calculate the number of materials or components that still need to be ordered.
In the picture below you can have a similar process where the remaining PO is automatically created for the difference between Quantity Gap and Quantity Received in the PO.
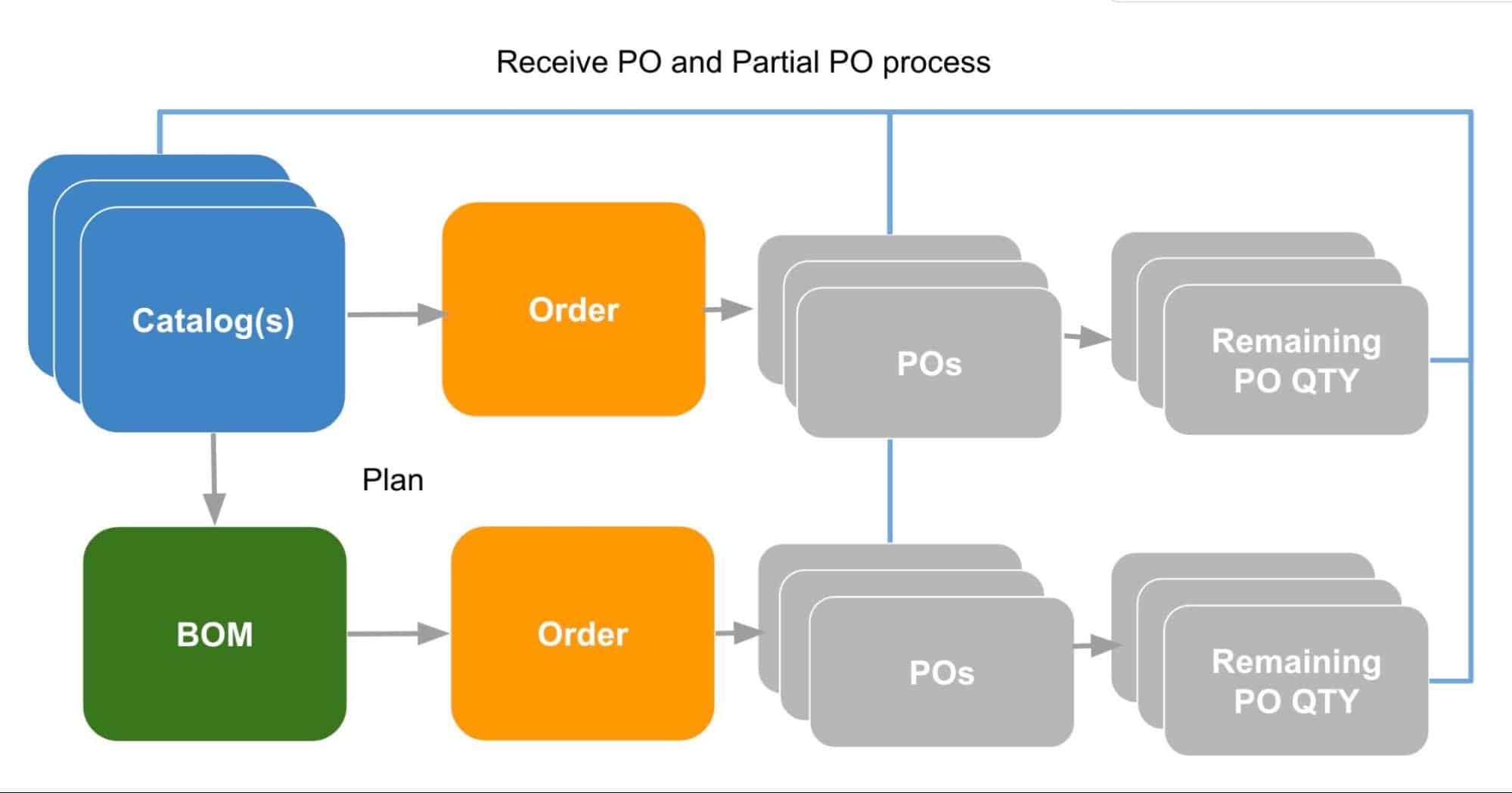
The process described above can be repeated multiple times until the remaining PO quantities are greater than zero. Once you’ve got zero, the remaining quantity PO is not created and the final “Receive” status is obtained by the order.
Video Demo
Please check the following video that demonstrates how the Partial PO feature can be used. Note, that the same process can be used by all types of items – discrete, process, mechanical, electronic, consumer goods, food, etc.
Conclusion
Supply chain shortages are going to stay with us for a long time. Therefore, the importance of OpenBOM’s capability to order the right components from the right vendors at the right time is extremely important. A new partial PO receive mechanism will be very useful to manage a purchasing process during the time of high turbulence of components availability. OpenBOM production planning is becoming, even more, smarter and allows you to streamline the ordering process to help you organize the information handover between engineers and procurement.
REGISTER FOR FREE to check how OpenBOM can help you.
Best, Oleg
Join our newsletter to receive a weekly portion of news, articles, and tips about OpenBOM and our community.