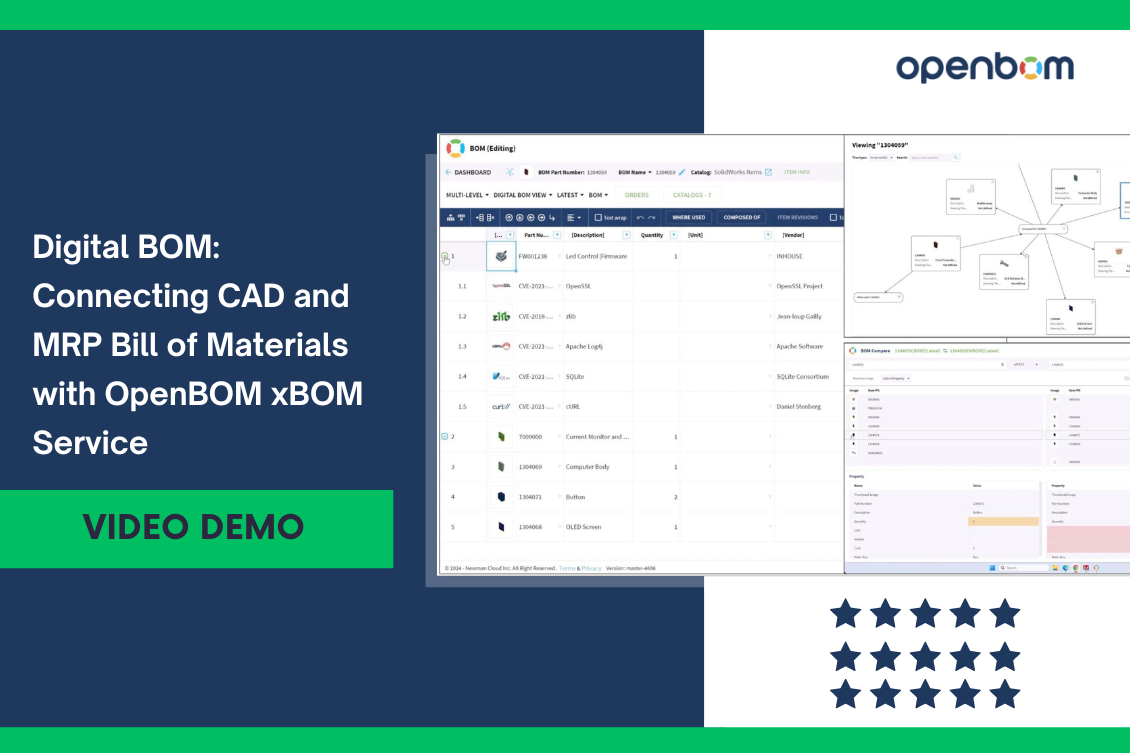
Manufacturing companies look at how to use digital technologies to improve data organization and communication between departments and through the supply chain. To ensure smooth communication and traceability between engineering, manufacturing, procurement, and other departments is a critical element of digitalization.
Each team often works with different data sets—engineering teams rely on CAD for design data, manufacturing teams use MRP or ERP systems for production planning, and procurement deals with supplier information. Without an efficient way to connect this information, it’s easy to end up with mistakes, delays, and miscommunication.
This is why managing a Bill of Materials (BOM) effectively is so critical. OpenBOM’s xBOM service offers a modern, digital solution to seamlessly connect and manage these different views of your product data, ensuring everyone is on the same page.
The Pain of Excel-Based BOM Management
Many organizations still rely on Excel to manage their BOMs because it’s familiar and easy to use for simple tasks. However, as products and processes become more complex, Excel-based BOM management quickly becomes a bottleneck. The task of gathering data from various systems—such as CAD for the engineering BOM (EBOM) and MRP or ERP for the manufacturing BOM (MBOM)—and manually integrating this data into a single Excel file can be daunting. Each department speaks its own language, uses its own tools, and works with its own set of data, making it incredibly painful to combine all this information into one place.
You’ve likely seen engineers and operations staff spending hours (if not days) trying to manually compare two Excel spreadsheets. Whether it’s scanning for part number differences, price discrepancies, or changes in quantities, this process is error-prone and highly inefficient. The larger the BOM, the more time-consuming and difficult it becomes. When mistakes happen, they can have serious downstream effects, such as ordering the wrong parts, delays in production, or even product recalls. Excel simply wasn’t built to handle the complexity and real-time collaboration that modern manufacturing demands.
The Right Answer: A Digital BOM for Seamless Connectivity
The solution to these inefficiencies is a modern, digital BOM. Unlike static Excel files, a digital BOM is dynamic and connected, providing a unified platform where multiple teams can access and share up-to-date product information. OpenBOM’s xBOM service offers this capability, allowing you to create and manage a digital BOM that can accommodate both engineering and manufacturing data.
With OpenBOM’s digital BOM, you can:
- Seamlessly pull data from various systems like CAD, ERP, or MRP.
- Create a connected set of information that reflects multiple views of your product data—whether it’s engineering, manufacturing, or procurement-related.
- Eliminate the need for manual data entry or copying information from one system to another, reducing the risk of human error.
This digital BOM is organized using a graph-based model that dynamically links different pieces of information, allowing changes in one view to be reflected in others. For example, if a part is updated in the EBOM, the change is automatically available in the MBOM, ensuring that manufacturing always has the latest data from engineering. With this level of connectivity, OpenBOM helps organizations avoid the pitfalls of siloed information, empowering teams to work together more effectively.
xBOM Compare Service: Analyzing EBOM and MBOM Differences
One of the most common challenges when managing a BOM across departments is ensuring that the engineering BOM (EBOM) and the manufacturing BOM (MBOM) remain aligned. Differences between these BOMs can lead to production delays, excess inventory, or incorrect parts being ordered. In a typical Excel-based workflow, comparing these two BOMs is a tedious process involving manual reviews and often hours of scrolling through spreadsheets. The xBOM Compare service in OpenBOM changes this by providing an automated way to compare BOMs from different sources.
With the xBOM Compare service, you can:
- Pull in BOM data from CAD systems for the EBOM and from MRP/ERP systems for the MBOM.
- Automatically highlight differences between the two, such as changes in quantities, part numbers, or descriptions.
- Identify discrepancies quickly, without the need to manually search through rows and columns of data.
The service can also integrate data via direct connections to your systems or through Excel/CSV imports, giving you the flexibility to work with whatever data sources you have at your disposal. Whether your data comes from advanced PLM systems or simple CSV files, the xBOM Compare service ensures you can easily align and update BOMs, making sure all teams are working with the most accurate information. This eliminates the labor-intensive task of manual comparisons and helps prevent costly mistakes.
A Flexible Data Model: Bringing All Your Data Together
One of the key strengths of OpenBOM’s xBOM service is its flexible data model. Traditional BOM systems often force you into rigid data structures that might not fit the way your company works. OpenBOM, however, is designed to be adaptable, allowing you to bring in data from virtually any source—whether it’s CAD, MRP, ERP, or even manually created Excel files.
This flexibility means you can:
- Inject data from multiple systems without worrying about format compatibility.
- Customize your BOM to include different data points that are important to your specific workflow.
- Build a dynamic, connected BOM that can grow and evolve with your product and business needs.
By allowing you to centralize data from different silos, OpenBOM makes it easier to maintain data integrity and ensure that all teams have access to the most up-to-date information. This is especially important for companies that deal with complex products or require frequent updates to their BOMs during the design and production phases.
Watch the Video: See How OpenBOM Works in Action
Want to see how OpenBOM’s digital BOM and xBOM Compare service work in practice? Watch the video below to see how easy it is to build a connected BOM from both CAD and ERP data, helping you streamline your workflows and keep your teams aligned.
Conclusion: OpenBOM’s Digital BOM is the Future of Product Data Management
By adopting OpenBOM’s digital BOM approach, you can finally break free from the limitations of Excel-based BOM management. OpenBOM’s xBOM service allows you to pull in data from multiple sources, including CAD, ERP, and manual inputs, and compare them in real time using its powerful xBOM Compare service. Whether you’re aligning EBOMs and MBOMs or managing changes throughout the product lifecycle, OpenBOM ensures you have the right data at the right time, reducing errors, speeding up production, and improving collaboration.
REGISTER FOR FREE and try OpenBOM to see how it can help you to streamline your data integration processes.
Best, Oleg
Join our newsletter to receive a weekly portion of news, articles, and tips about OpenBOM and our community.