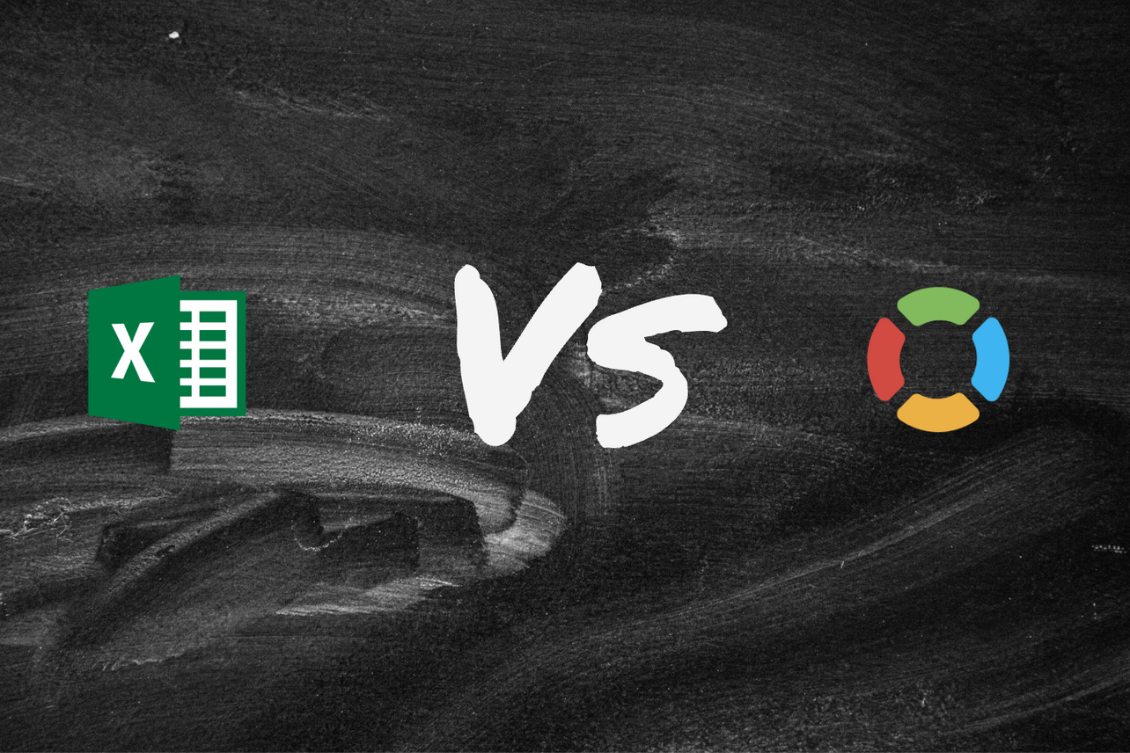
Managing product data accurately is a critical part of any manufacturing process. The Bill of Materials (BOM) plays a central role, outlining all the parts, materials, and components required to produce a product. Many companies have traditionally relied on spreadsheets or manual methods to handle this data, but these approaches are increasingly showing their limitations—errors, version control issues, and inefficient collaboration being just a few.
With the rise of digital solutions, the Digital BOM offers a more reliable, streamlined way to manage product information. Unlike an Excel BOM or other traditional methods, a Digital BOM provides real-time updates, better collaboration, and seamless integration with other tools, making it a powerful option for modern manufacturers.
In this blog, we’ll compare traditional and digital BOMs to explore which one is better suited for today’s manufacturing challenges, focusing on key differences such as accuracy, collaboration, and efficiency.
What is a Traditional BOM?
A Traditional Bill of Materials (BOM) is a document that lists all the parts, materials, and components required to manufacture a product. It has long been the standard for manufacturers, typically managed using spreadsheet tools like Excel or even physical paperwork. At its core, an Excel BOM serves the same purpose as any BOM, to outline the details needed for production, including part numbers, quantities, and specifications.
However, managing a BOM manually through spreadsheets or paper can be a time-consuming and error-prone process. Here are a few common characteristics of a traditional BOM:
Manual Data Entry
In a traditional BOM system, all data must be entered by hand. This opens the door to mistakes such as typos, incorrect part numbers, or outdated information. Since manual updates are required whenever a change occurs, errors can easily go unnoticed until they cause significant delays or cost overruns.
Version Control Issues
Because traditional BOMs are static documents, managing versions can be difficult. If a change is made to the design or materials, it’s up to the team to ensure that everyone has the most recent version of the BOM. This often leads to confusion, with different teams working from outdated versions, causing inconsistencies during production.
Limited Collaboration
Sharing and collaborating on a traditional BOM can be inefficient, especially when multiple stakeholders are involved, such as engineers, procurement teams, and suppliers. Emailing spreadsheets back and forth often leads to versioning issues, miscommunication, and delays, as everyone may be working on different iterations of the same document.
Incompatibility with Modern Tools
Traditional BOMs don’t easily integrate with other digital systems used in manufacturing, such as CAD (Computer-Aided Design) or ERP (Enterprise Resource Planning) tools. This lack of integration forces teams to manually transfer data between systems, increasing the likelihood of mistakes and slowing down the overall process.
While traditional BOMs have served manufacturers for years, these limitations are becoming more pronounced as companies strive for greater accuracy, efficiency, and collaboration in their operations. The reliance on manual processes and siloed systems makes it harder to keep up with the speed and complexity of modern manufacturing, paving the way for more advanced solutions like the Digital BOM.
What is a Digital BOM?
A Digital BOM is a modern, cloud-based solution for managing the parts, materials, and components required to manufacture a product. Unlike traditional BOMs, which are often maintained manually in spreadsheets, a Digital BOM is stored in digital systems like PLM (Product Lifecycle Management). These systems enable real-time collaboration, automatic updates, and seamless integration with other digital tools, making the Digital BOM a vital resource for today’s manufacturing needs.
Here’s how a Digital BOM stands out:
Real-Time Data Sharing
One of the most significant advantages of a Digital BOM is the ability to share data in real-time. Everyone involved—engineers, procurement teams, suppliers—can access the same up-to-date information at any time. This eliminates the confusion that comes from working with outdated versions of the BOM, ensuring that all teams are aligned and working from the latest specifications.
Improved Version Control
Managing changes and updates becomes effortless with a Digital BOM. When any change is made to the product design or materials, it is automatically updated across the system, and the history of changes is recorded for easy tracking. This ensures that there’s always a clear audit trail, reducing the risk of mistakes and miscommunication. Teams no longer need to worry about whether they have the correct version of the BOM, as all changes are immediately reflected for everyone.
Enhanced Collaboration
Collaboration is streamlined with a Digital BOM. Because the BOM is stored in a centralized system, different teams and external partners, such as suppliers, can easily access and work together on the same BOM in real-time. This not only improves communication but also speeds up decision-making, as any adjustments or approvals can be handled faster and more efficiently.
Integration with Digital Tools
A Digital BOM integrates seamlessly with other software tools commonly used in manufacturing, such as CAD systems, ERP software, and supply chain management platforms. This integration allows for the automatic transfer of data between systems, reducing the need for manual entry and minimizing the risk of errors. For example, design changes in a CAD system can automatically update the BOM, ensuring that all parts and material specifications remain current.
Reduced Errors and Faster Updates
By automating updates and eliminating manual data entry, a Digital BOM significantly reduces the chances of human error. Changes are instantly reflected across the system, which speeds up processes and reduces bottlenecks caused by outdated or incorrect data. Procurement teams can act on up-to-date information without delay, ensuring that the right materials are ordered on time and in the correct quantities.
Key Differences Between Traditional and Digital BOMs
One of the most significant challenges with Traditional BOMs is the reliance on manual data entry and updates. This manual process often leads to inaccuracies, such as incorrect part numbers, outdated information, or missed changes, which can cause production delays and costly mistakes. Because traditional BOMs are often managed using spreadsheets, it’s easy for errors to go unnoticed until they create significant issues down the line.
In contrast, Digital BOMs automatically sync data across teams and systems. Changes made in one part of the system are instantly reflected throughout, ensuring that everyone has access to the most up-to-date and accurate information. This automation reduces human error and keeps the BOM aligned with the latest design and production requirements, resulting in smoother operations and fewer production delays.
Collaboration Across Teams and Supply Chain
Traditional BOMs are often shared manually between departments, engineers, and supply chain partners. This can lead to delays in communication, as teams wait for the latest version to be emailed or shared, creating version control issues. The manual sharing process also opens the door to miscommunication, with teams potentially working from different or outdated versions of the BOM.
Digital BOMs, on the other hand, enable real-time collaboration. Teams across departments and external partners, such as suppliers, can access the BOM simultaneously, ensuring that everyone is working from the same data set. This improves coordination, reduces delays in communication, and ensures that all stakeholders are on the same page. The ability to collaborate in real-time minimizes errors and streamlines decision-making, particularly for complex manufacturing projects involving multiple teams and locations.
Scalability and Complexity Handling
As product complexity increases, managing a BOM manually becomes a significant challenge. Traditional BOMs struggle to handle complex products with multiple parts, configurations, and versions. Organizing and keeping track of large quantities of data in a traditional BOM can be overwhelming, leading to confusion and errors.
Digital BOMs are designed to handle complex product structures with ease. They can scale to manage products with thousands of parts and multiple configurations without sacrificing accuracy or efficiency. Digital systems are equipped to handle advanced features such as multi-level BOMs, variant management, and configuration control, making them well-suited for companies with large product lines or custom manufacturing needs. This scalability is essential for manufacturers looking to grow and handle increasingly complex product designs.
Time and Cost Efficiency
Traditional BOMs can slow down production processes, especially when manual updates lead to errors or delays in communication between teams. These inefficiencies often result in costly rework, extended lead times, and even missed production deadlines, all of which drive up costs.
Digital BOMs streamline the entire process, significantly reducing turnaround times. By automating updates and providing real-time access to accurate information, Digital BOMs eliminate the need for manual intervention and rework. This reduction in errors, faster communication, and improved data management ultimately leads to lower production costs and faster time-to-market. The time and cost savings achieved by switching to a Digital BOM can have a significant positive impact on a company’s bottom line, especially for manufacturers dealing with high volumes and complex products.
Conclusion
The shift from Traditional BOMs to Digital BOMs represents more than just an upgrade in tools—it’s a transformation in how manufacturers manage their product data, collaborate, and streamline production processes. While traditional methods may still work for simple projects, their limitations become clear when accuracy, collaboration, scalability, and efficiency are required.
Digital BOMs provide manufacturers with real-time data synchronization, improved version control, enhanced collaboration, and the ability to manage complex product structures with ease. These features not only reduce errors and miscommunication but also lead to faster production times and lower costs.
As manufacturing continues to evolve and demands for greater precision and efficiency increase, adopting a Digital BOM is a critical step for companies looking to stay competitive. Whether you’re managing small-scale production or handling large, complex product lines, a Digital BOM can significantly enhance your operations and provide a solid foundation for future growth. The question is no longer if you should move to a Digital BOM, but when.
By: Jared Haw
Join our newsletter to receive a weekly portion of news, articles, and tips about OpenBOM and our community.