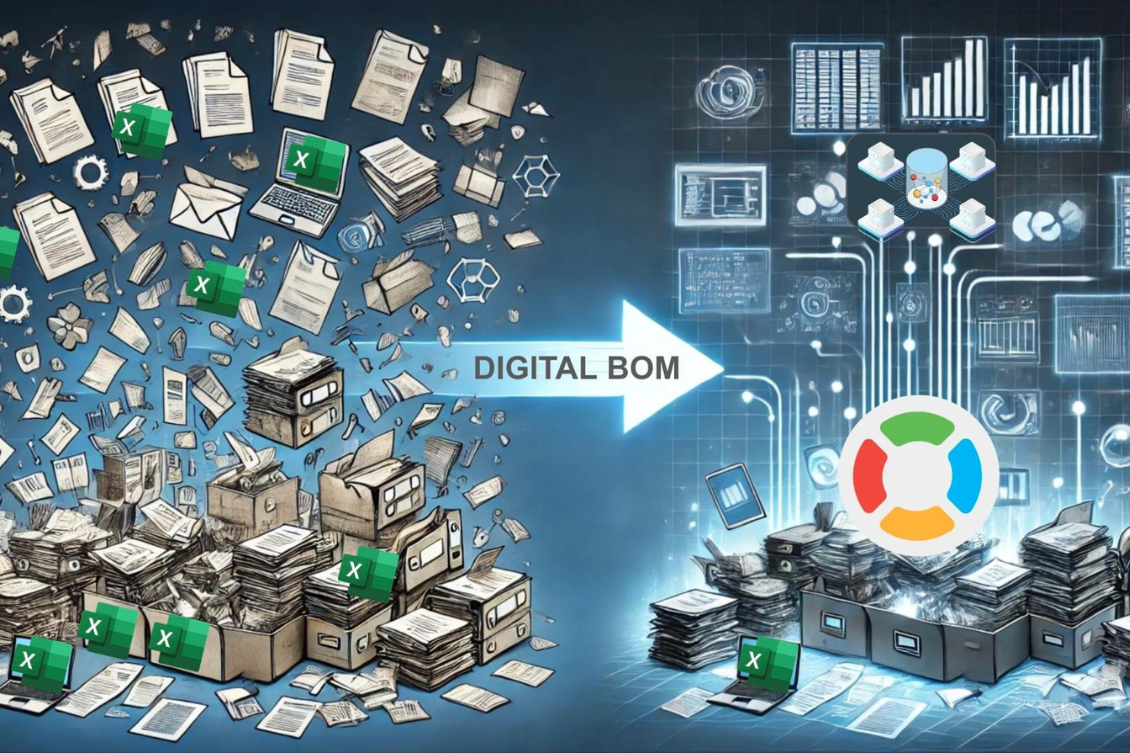
The last decade, particularly the years following COVID-19, has shown us the potential of digital transformation. We live in a space where everything, from talking to friends to ordering food, booking travel, or buying a house, is just a click away—seamless and fast. Yet, when it comes to engineering and manufacturing processes, things are not as smooth or simple as we’d like. They feel disconnected and sluggish. At the same time, there is a growing complexity in the engineering and manufacturing process.
The Status Quo of a Manufacturing Team
Let’s consider a typical manufacturing company planning to build industrial robots. This process requires the collaboration of mechanical, electrical, electronics, and software engineers, each using their own CAD system to store files on their computers or shared drives like Google Drive. As progress is made, the need to shift to production planning comes, demanding the organization of all product-related data—CAD files, part lists (BOMs), STEP, PDF, DXF, documentation, packaging details, etc.
For even the simplest products, multiple suppliers and contract manufacturers are involved. Managing long-lead items, creating orders, and tracking the procurement process becomes a challenge, especially when it needs to be done earlier in the design process when the design isn’t finalized. Engineers and procurement teams exchange countless emails with Excel sheets, CAD files, and other documents, going back and forth in a loop, and clarifying details and specifications.
But that’s not the end. Once orders are placed, the team must track incoming components. With a few hundred parts to manage, the risk of delays, missing parts, or incomplete deliveries becomes real. Last-minute surprises—missed or delayed parts—can derail the project.
Does this sound familiar? Have you or your team experienced this?
Why This Process Is So Difficult
The core issue is information management. Engineering data is inherently complex, involving a mix of mechanical, electronic, and software components. This complexity is compounded when different teams, often spread across different locations and time zones, rely on disparate systems. Data is scattered across Excel sheets, CAD files, PDF derivatives (like STEP, DXF), and emails. Managing, updating, and organizing this information is time-consuming, error-prone, and chaotic.
And that’s before even getting to managing inventory, organizing parts, and ensuring everything is ready for assembly. The result? Delays, errors, and inefficiencies that slow down production and disrupt operations.
Unlocking Digital Transformation
So, how can you solve the problem of organizing engineering information, ensuring timely orders, and delivering products without delays?
The answer lies in digital transformation. Think about how modern digital tools work in other industries—whether you’re ordering from Amazon or calling an Uber, you’re not sending PDF files or making phone calls. These systems communicate seamlessly, handling orders and processes digitally.
In manufacturing, a similar shift is needed. Instead of relying on outdated methods (emails, Excel, or PDFs), digital transformation allows for real-time, accessible, and traceable information sharing across teams. And it’s happening now. A staggering 63% of CEOs in large manufacturing companies have increased investments in digital transformation over the last year (based on EY research of the discrete manufacturing industry)
Why? Because it’s not just about surviving in the present but also about thriving in the future. Just as you wouldn’t use an outdated flip phone in today’s world of smartphones, your manufacturing processes need to evolve to stay competitive. The industry is moving fast, and companies that fail to transform will fall behind.
Three-Step Strategy to Transform Product Development and Procurement Loop
At OpenBOM, we’ve developed a proven strategy to help manufacturers digitally transform their product development, procurement, and production processes. Trusted by thousands of engineers and manufacturers worldwide, OpenBOM has earned recognition as one of the Top 50 companies in PLM, according to G2 reviews in both 2023 and 2024.
Here’s how to fix your product loop in three steps:
1. Digital BOM
Ditch the spreadsheets and move to Digital BOM. With OpenBOM, manufacturers can create digital representations of BOMs (Bill of Materials) that are accessible, traceable, and reliable. This digital foundation streamlines the process, eliminating errors and enabling real-time collaboration. A flexible data model allows seamless organization of data items, file attachments, different attributes, revisions, history, etc. Available via a collaborative “Google sheet-like” user experience, it keeps everyone “on the same BOM”.
2. Seamless Design Integration:
OpenBOM leverages its flexible Product Knowledge Graph technology, allowing manufacturers to integrate data seamlessly across CAD and other design systems. OpenBOM’s CAD add-ins, open APIs, and features like “One-Click BOM” and Quick Start function reduce friction between design and production. Check more about it and learn about design digital thread supported by OpenBOM integrations.
3. Connected RFQ and Supply Chain:
OpenBOM connects procurement processes directly with real-time data. An integrated inventory control system allows gap calculation and vendor allocation to be done directly in OpenBOM. OpenBOM gives you a way to create orders and aggregate RFQ/PO for each vendor (suppliers) automatically. By integrating supply chain management with financial applications and ERP systems, OpenBOM enables smoother communication, minimizes lead times, and provides complete visibility from CAD to order fulfillment.
Conclusion
Now is the time to embrace digital transformation in your product development, planning, and manufacturing processes. Not tomorrow and not next year. Data should be viewed as a strategic asset for your company—a key to building accurate, efficient, and competitive products. From tracking supplier performance to managing orders and historical data, digital transformation will enable your team to operate faster, smarter, and more competitively.
As we often say, businesses don’t fail overnight; they decline gradually, and then suddenly. The same is true for digital transformation. Today, you may still survive with Excel and manual processes, but tomorrow, your competitors will outpace you by building products faster, better, and cheaper.
Ready to discuss your digital transformation journey? OpenBOM advisors can help you to start the journey as we did for many OpenBOM customers. Check G2 reviews to learn more unbiased information about what our users say. Subscribe to OpenBOM and try your FREE 14-day trial today and experience it firsthand.
Best, Oleg
Join our newsletter to receive a weekly portion of news, articles, and tips about OpenBOM and our community.