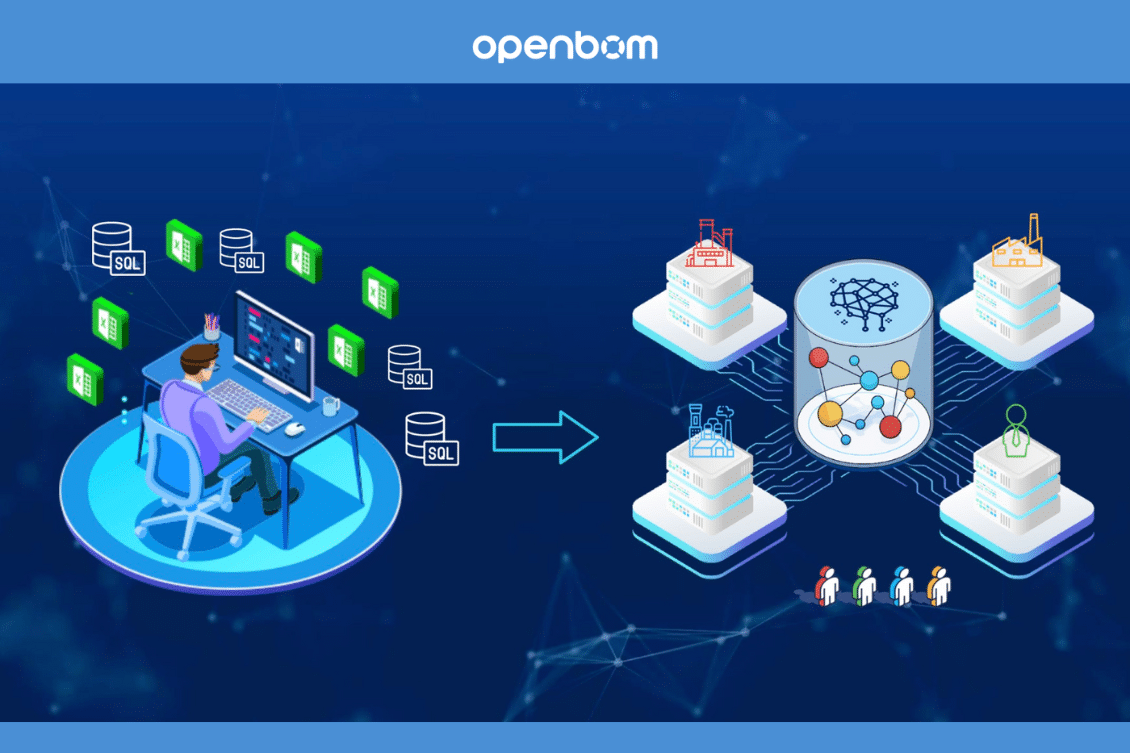
Digital transformation is here and the manufacturing industry is transforming. The last few years left manufacturing companies with a lot of stress in a continuously changing environment including the demand to build better, faster, and with lower cost, multiplied by ongoing supply chain disruption, the demand for sustainability, and a strict set of multiple regulations.
Companies are looking at how to build their businesses sustainably to all these stress levels. This leads companies to switch to a digital strategy to transform business processes and internal and external communication, and often re-think their business models shifting from selling physical products to selling digital services.
In the past, manufacturing companies were built around natural resources (coal mines), sources of energy (rivers), and industrial clusters. We can see it in the history of technological phases.
However, looking back on the last 20 years, I can see the most successful businesses are built by focusing on the power of information and placing data in the middle of their businesses.
In recent years, digital transformation has undeniably disrupted countless industries. No sector remains untouched, and manufacturing is certainly no exception. Manufacturers worldwide are exploring the potential of a data-centric strategy, gradually replacing conventional spreadsheet methods with advanced digital solutions.
The question is how manufacturing companies will be able to figure out the power of information and improve their businesses by focusing on data and how data can improve their design, engineering processes, supply chain, manufacturing, and other activities.
In my article today, I want to talk about how engineers and manufacturing companies will leave Excel habits behind and adopt data-centric ways to do business.
The Old Guard: Excel Lingua Franca in Engineering and Manufacturing
Excel (and spreadsheets) is a powerful tool for engineers due to its flexibility, ease of use, and wide availability. It allows engineers to perform complex calculations, analyze data, create visualizations, and develop models. Excel’s familiarity and ubiquity make it a common language that engineers can use to communicate and collaborate with professionals from different domains, including finance, operations, and management.
But together with all the benefits, Excel brings a massive level of complexity. Have you heard the story of the CEO (Chief Excel Officer) – a person in your company who knows how to control all complex Excel files and get the right information? Guess what? If something happens with your Chief Excel Officer, the company can be paralyzed, data will not be available and everything will eventually stop.
Working with many companies I found these limitations of Excel-ware quite common.
Automation Challenges: Although Excel has automation capabilities through macros and VBA programming, it’s not designed for full-scale automation of complex tasks, limiting the speed and efficiency of digital transformation.
Data Integrity: As Excel is highly prone to human errors, it can lead to concerns over data integrity. There’s a risk of erroneous data due to manual input errors, incorrect formulas, or data corruption.
Collaboration Difficulties: Excel can be challenging for collaboration. Multiple people working on the same document can lead to version control issues. Digitally native systems allow for real-time collaboration and updates, which is critical in a digital transformation context.
Lack of Integration: Although every product can do some sort of Excel export, it’s not designed for seamless integration with other systems or software. Multiple exports create many Excel files that got lost and eventually, the wrong Excel will be used when needed. This can impede data flow and limit the ability to create interconnected, automated systems essential for digital transformation.
Security: Your BOMs with sensitive engineering and supply chain information are a super vulnerable set of information. Excel spreadsheets are typically not as secure as modern cloud-based solutions. They can be vulnerable to loss, theft, or unauthorized access, which could pose significant risks during a digital transformation initiative.
Altogether, this makes Excel the enemy of digital transformation. Traditionally, Excel has been a mainstay in the manufacturing industry, owing to its versatility and widespread familiarity. From managing inventory to tracking production schedules, and from finance to quality control, Excel has been at the center of manufacturing operations.
However, as the complexities and scale of manufacturing operations grow, the limitations of Excel become more apparent. Manual data entry is not only time-consuming but also prone to human error. Collaboration and real-time updates are other areas where Excel-based systems falter. Finally, the demand for data analytics is as high as ever and Excel is not the right place to make it happen.
Embracing a Data-Centric Approach
Manufacturing companies need to rethink the way they are thinking and implementing data management systems. In the PLM business, organizations were focusing on how to control CAD files, and managing engineering change and release processes. If you think about traditional PLM systems, you see how all they do is about managing the efficiency of traditional paper (document)-like processes. While these processes are needed, companies must re-think them and move towards a data-centric approach.
In a data-centric approach, the focus of the system moves from the organization of documents to the definition of granular data sets describing data and processes, connecting people to the right information, and organization of seamless information flows. These three elements of digital transformation are the foundation of new manufacturing business processes.
Instead of disparate CAD files and Excel spreadsheets, a data-centric strategy allows manufacturers to create information only once, to share it between multiple people, departments, and organizations, to provide tools to perform analytics and provide decision support. Most importantly, the data is not lost in zillions of Excel files, but instead, collected, analyzed, and used for future optimization of processes and decisions.
Old Habits Dying Hard
Moving from Excel to new ways to manage information is hard. Last year, I wrote an article – How to stop boiling a frog with Excel BOM management. The main point I want to make is that you cannot transform engineering and manufacturing processes overnight. The engineering Excel frog will jump. You need to have a transition. Engineers need to have that “aha moment” to think about how to stop managing their business processes using the Excel-ware tools. After speaking to many organizations, we discovered that many of them are using the same “boil the frog” strategy but in the opposite direction. Here is how it can work…
You can take an engineering or manufacturing team and instead of switching them one day from their old and comfy Excels to a fully-fledged PLM platform, we make them jump immediately and reject the change. At the same time, if you bring PLM and other digital services to an organization, changing existing data management practices and business processes gradually, your engineers are getting ready for PLM and adopting the change.
Agile PLM services adoption is the way for many manufacturing companies today to think about their digital transformation strategy. You can ask – PLM vendors always offered the agile gradual adoption approach avoiding PLM big bang change event. It is true, but here is the thing – new modern PLM SaaS Digital Web services make a difference in the way new platforms can be adopted and used.
Conclusion
While Excel has been an invaluable tool for manufacturers, the industry’s growing complexity and scale necessitate a more powerful and easy approach. Adopting a data-centric strategy can help manufacturers leverage their data more effectively, driving efficiency, enhancing decision-making, and providing a competitive edge in the evolving digital manufacturing landscape.
The change will not happen overnight. Manufacturing companies will have to go agile and bring tools to reorganize processes, get rid of Excels, manual data entries, and re-entries, and optimize information flow inside and outside their organization.
At OpenBOM we help manufacturing companies to organize this digital journey.
REGISTER FOR FREE and check how OpenBOM can help you today.
Best, Oleg
Join our newsletter to receive a weekly portion of news, articles, and tips about OpenBOM and our community.