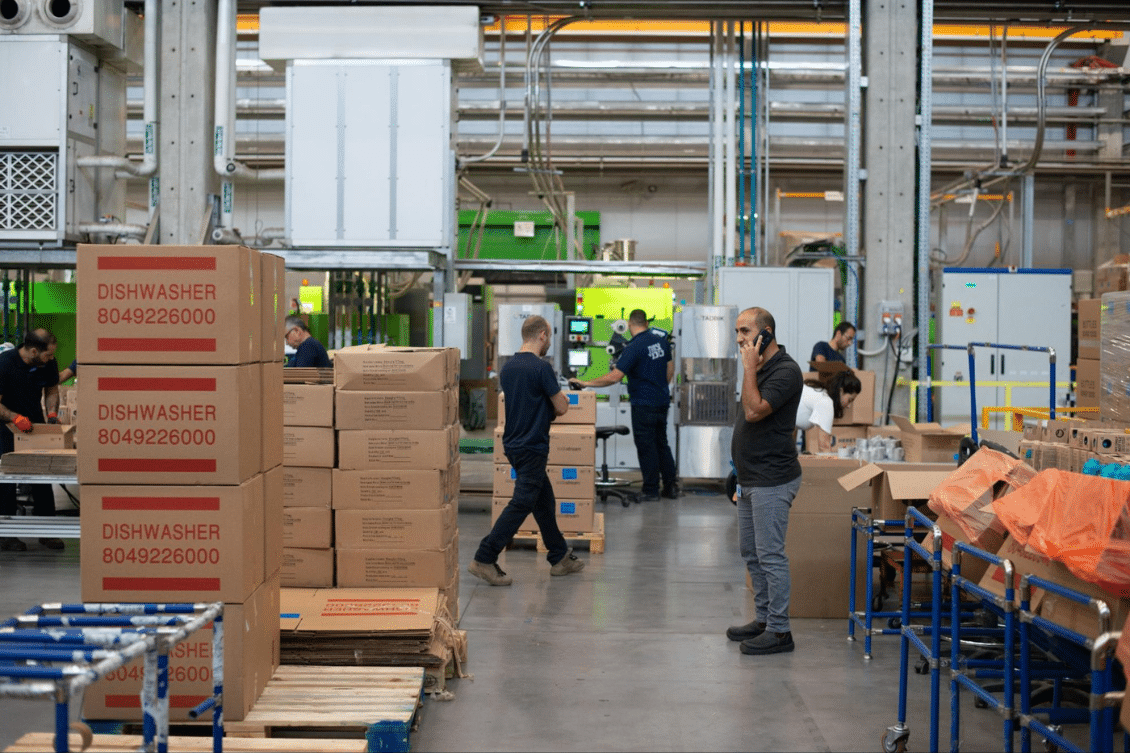
You might have been in a position where you have seen a quality problem and no matter how insignificant this quality problem is, it just keeps coming back. Sometimes, these quality defects fly under the radar or they were not dealt with properly, but whatever the problem is, they need to be addressed.
Regardless, it is common for suppliers to have recurring quality problems. While this is not acceptable, it does happen. In order to prevent these recurring quality problems from occurring again and again then you should follow these pointers.
Communicate the Problem to the Supplier
The first step to solving something is always to communicate the issue directly with your supplier. Make sure your supplier understands the quality problem and why it is not acceptable.
If this is communicated well to the supplier then you and your supplier should take further steps to solve the quality problem.
When you communicate the problem it’s important to understand why the issue occurred. It’s usually not as simple as a simple defect. These issues go back to the previous processes or environment.
What I have found helpful is to ask yourself the 5 Whys. In a nutshell, this is used to continuously ask why something failed. You continue to ask why until you have found the root cause (which is when you can no longer ask why).
Here is a good example from What is Six Sigma on 5 Why’s:
“Problem: High level of rejects of pencils from quality control.
- Why are the pencils rejected? Misalignment of leads.
- Why are the leads misaligned? Poor workmanship.
- Why are the workers not performing well? The factory is too hot.
- Why is the factory too hot? No proper ventilation is in place.
- Why is there no proper ventilation in place? The recent expansion has crowded the factory, disrupting the present ventilation system.”
Usually, you will need to help of your supplier to figure out the root cause. But, the start of the process starts with properly communicating the issue to the supplier so further evaluation can be made.
Communicate the Problem as Quickly as Possible
In other words, don’t wait to inform your supplier of a quality problem. The longer you wait to communicate with the supplier about the quality problem, the more risk you are putting your company at of customer complaints.
There are some reasons issues are not communicated to suppliers at the ideal time. The main reason is that the manufacturer thought the quality defect was not a big deal. But, this is why we have a quality standard and anything out of the quality standard should be reported or added to the standard.
It also depends on the phase of the product’s lifecycle. If you see a defect during prototypes then it’s a great time to have a re-design to fix the problem before it hits mass production. However, if the minor defect made its way to production then there is still potential for this minor defect to give a customer a major headache. Also, the solution during production will always be more expensive to fix rather than the issue being found during development.
Stick to your Quality Standard
Before you launched production, you created a quality standard to promote a consistent product. Sometimes, during production, this quality standard evolved and certain things are added. However, it’s important to not make an exception to your quality standard.
The most common reason to make an exception and ship something out of spec is to save time. The manufacturer has a shipment date that they can’t push back and they are willing to make an exception to what they have convinced themselves to as a minor quality issue that will not have a negative impact on the overall quality. A mindset like this can convince your supplier that you are ok with minor quality problems. Usually, this is the pressure you do not want to release from your supplier.
Switch Suppliers
If you are having recurring quality problems with a known solution then perhaps your supplier is just incompetent. And sadly, this does happen.
A decision needs to be made when you stop believing what your supplier says and decide that your product is too important and switch suppliers.
Unfortunately, switching suppliers is not done overnight, unless you have gone through the correct process. But, switching suppliers is very similar to the process of finding the first supplier. Hopefully, you are more experienced and can identify your preferred supplier quicker.
Conclusion
Quality problems are serious. Even minor quality issues can have a lasting impact on a customer. However, if you are clear in communication and identify the problem early enough then you should be able to work through it with your supplier.
Manufacturing is never perfect and these issues come up. You should also be working with a supplier who is capable to work with you in order to solve these problems. If not, then you might need to find a new supplier.
Interested in what we do? Please contact us. We are actively researching this field and would be excited to share more information as soon as it will become available.
In the meantime, REGISTER FOR FREE and start a 14-day trial to check how OpenBOM can help you.
Best,
Jared
Join our newsletter to receive a weekly portion of news, articles, and tips about OpenBOM and our community.