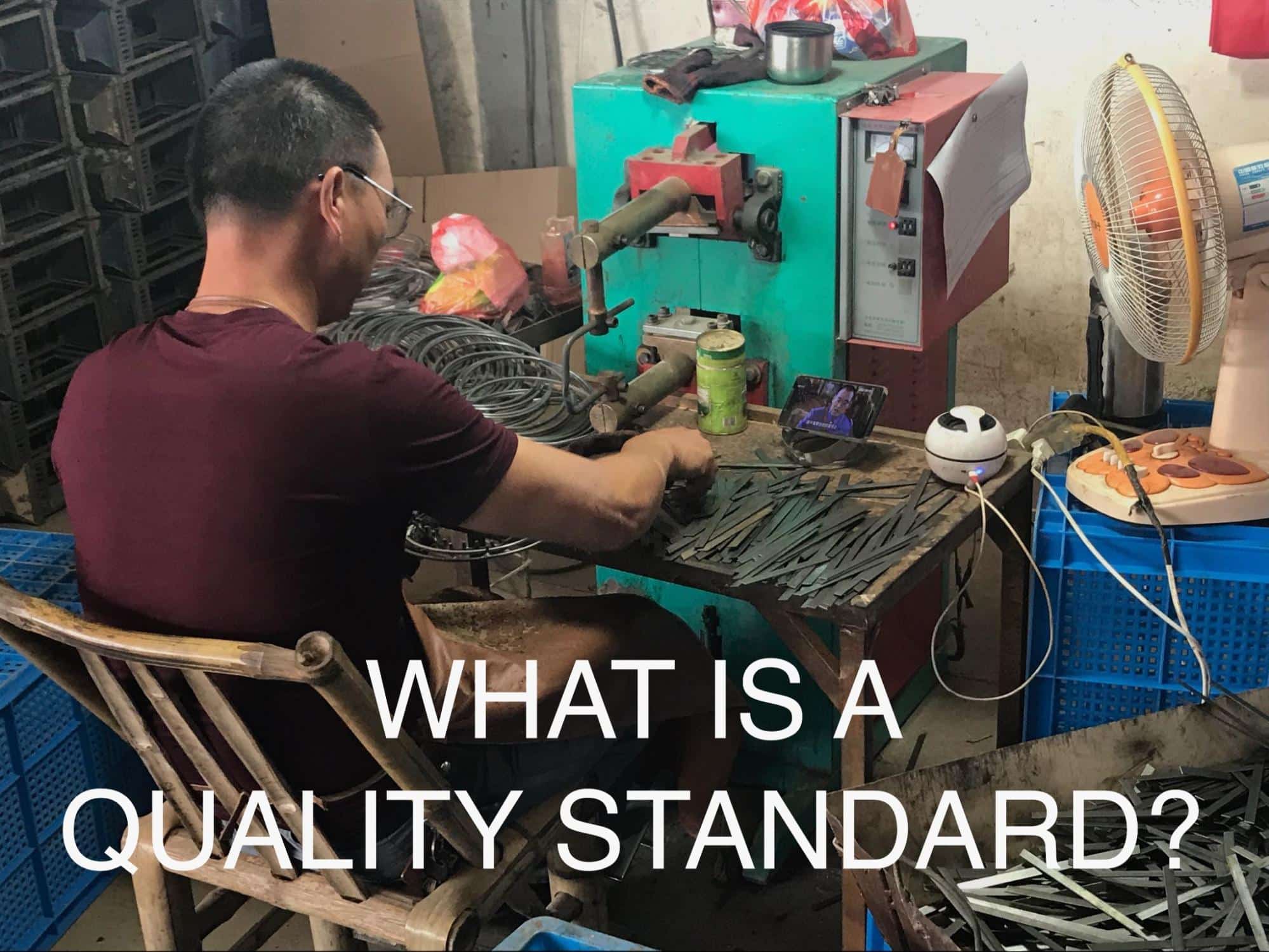
A common misconception is that quality is just making sure your product is made properly. However, this could not be further from the truth. A company that prioritizes quality will have quality ingrained in their organization, not just on the assembly line.
Quality Process
For example, on the assembly line, the QC guy at the end of the line is not the only one responsible for quality. Each operator and assembly worker that passes his work to the next station is responsible for the quality of their work. If the assembly worker does not take responsibility for their work then there will be a build up of rejected parts at the end of the line. Unfortunately, with some suppliers and contract manufacturers, this is how they work. You might know a few.
This is because of a lack of quality standards. This example was just for the assembly line but it also extends out to the entire company.
Why Quality Standards?
According to ASQ, “Quality standards are defined as documents that provide requirements, specifications, guidelines, or characteristics that can be used consistently to ensure that materials, products, processes, and services are fit for their purpose.”
As you can tell from this definition, the quality standard defines not just what’s made in production but also the entire business. The quality standards are not just for products but it reflects how their company should present themselves.
This is why sometimes you can tell if a company has a poor quality system before you even purchase from them. If the company poorly presents itself then you can also assume that their standards on the production line are not much better.
Let’s look deeper into the previous example, the assembly line. Let’s say you go out to China (I guess when it reopens) and you’re visiting a supplier for a particular part. Unfortunately what we are most focused on is the price and we ignore everything else. It doesn’t matter how disorganized the factory floor is, how dirty the bathroom is, the condition of the office, and more. Sometimes having the right price trumps everything else.
How to check Quality Standards?
The picture above was a picture I took visiting a supplier in China. The guy was watching a movie on his phone while working…. I don’t believe there are quality standards in place at this facility. But they had a lower price than anyone else.
I feel that the shop floor, bathrooms, and overall conditions represent the product I will receive. Now, the factory does not have to be perfect. However, more likely than not, the company that negatively presents itself will also not be the one to answer or return your call once there is a quality problem. You might have had this problem as well.
You can also run this down the organization. Usually, their engineering support will be poor. Why would someone want to work in a dump? The good workers with respect leave for a better working environment.
The poor working environment, dirty bathrooms, and more show the lack of quality standards. If they do not have a quality standard for their organization, why would they have a quality standard on their assembly line? And how sustainable is a business to grow and scale-up when they do not have this in place?
Quality standards are not just important for the shop floor but are represented across the company as a whole. Next time you visit your supplier, pay attention to the overall working environment and the attitudes of their employees.
Why OpenBOM?
OpenBOM improves the process of how you work with your suppliers, contractors, colleagues, and other team members. We provide you with the capabilities to seamlessly manage your parts, vendors, bill of materials, purchase orders, and change orders. All BOM, engineering, and manufacturing information are stored in the cloud which you can share with anyone.
Register for FREE to create your OpenBOM account and reach out to us via support @ openbom dot com if you have any questions.
Regards,
Jared Haw
Join our newsletter to receive a weekly portion of news, articles, and tips about OpenBOM and our community.