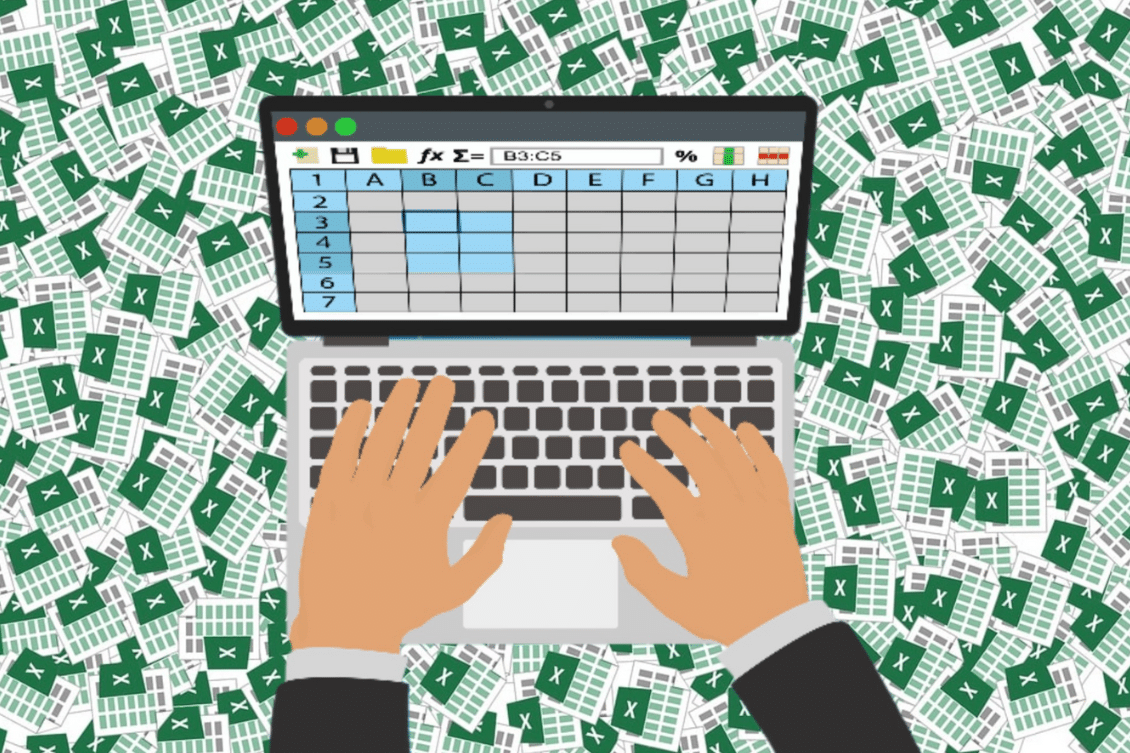
Manufacturing businesses are looking at how to build products faster, cheaper, and better. The demand for digital transformation is high and businesses are looking at how to speed up this process. Automation, artificial intelligence, cloud data management, and many other tools are available for engineers today, but engineers remain inexplicably tethered to archaic spreadsheet tools such as Microsoft Excel or its online clones. This seemingly absurd attachment to decades-old software has baffled many, raising the question: Why are engineers stuck in the past when the world is moving rapidly into the future?
I’ve been researching this paradox for many years coming up with different PLM and other data management solutions. As we embrace different possibilities presented by modern data management technology, it is ironic that engineers, people that design amazing robots, space shuttles, self-driving cars, and many other amazing devices, continue to rely on the limited capabilities of Excel to manage product information such as part lists, product structures, and inventing complex workflows or moving PDF files and Excels between folders to master their information flow in the company and to communicate with contractors and suppliers.
The amazing engineering loyalty to spreadsheets usually ignites fiery debates among industry experts, PLM analysts, and vendors. I can see how engineers’ obstinate dependence on Excel is hindering progress, slowing product development, creating mistakes, and holding us back from reaching the full potential of the digital manufacturing business.
Is it possible that the very individuals responsible for the greatest manufacturing and engineering innovation are also the ones inhibiting it? Are engineers knowingly or unknowingly sabotaging their own potential for growth and innovation?
In this article I will probe into the controversial love affair between engineers and Excel, exploring the reasons behind this perplexing phenomenon and assessing possible routes to get out of this spreadsheet dead end.
It Is Hard To Escape From Decades of Experience
Excel has been a go-to tool for engineers for several decades now, and its prevalence in the industry has made it a familiar and comfortable choice for many of them. You can export anything to Excel, copy/paste, import, massage the data, and feel in full control. This familiarity combined with the absence of trust in PLM tools and poor usability of enterprise software has made it difficult for engineers to escape from its use, as they have spent years developing their skills with the software and are often resistant to change.
Furthermore, Excel has become deeply integrated into the workflows and processes of many engineering teams. Predefined exports, imports, formats used for data storage, and some unexpected “workflow solutions” relying on Excel are amazing. Many engineering firms have invested heavily in Excel-based software and tools, making it a core part of their “Excelware” technical infrastructure. As a result, engineers may feel pressured to continue using Excel, as changing to a new tool or software would require a significant investment in time and resources.
The Importance of Digital Transformation
The number of articles speaking about digital transformation is skyrocketing these days. Below, I’d like to elaborate on why it is important for engineering and manufacturing data management in industrial companies and why good old Excel is not enough.
1) Streamlined Processes: One big key benefit of digital transformation is to stop relying on document and shift to data. Old envelop “spreadsheet” is semantically dead, doesn’t provide meaningful information, and stops companies from automatic control data and connecting people and processes together. The processes are switching from sending files with unknown information into meaningful data sets that can be automated and connected together. It helps to prevent mistakes and move faster.
2) Improved User Experience: Did you ever try to do something with spreadsheets created by someone else? It is a nightmare. Every organization using Excel has its own Chief Excel Officer. Understanding data without this person is hard to impossible. I’m not even talking about changes. Modern data management systems can provide an improved user experience allowing you to access “data” and not “files with cells and tables”.
3) Reliable Decision Making: Making accurate decisions requires access to relevant and reliable information. A single source of truth instead of looking for the “last version of Excel file” is much better for user experience and prevents companies from making mistakes. Digital tools provide real-time data, which allows manufacturers to make better, data-driven decisions.
4) Enhanced Flexibility: Flexibility and data transformation is extremely important. By unlocking data from Excel, companies create a framework to organize information that can be shared, accessed by API, and automate the process of communication. Data can be accessed by everyone on any device in a meaningful way. Digital transformation enables teams to collaborate remotely using online applications.
5) Competitive Edge: By adopting digital transformation, manufacturing companies can stay ahead of the competition. Advanced technologies such as automation, the Internet of Things (IoT), and artificial intelligence (AI) are rapidly changing the way industrial companies are operating these days. It allows us to focus on the effectiveness of the decisions instead of doing “the same thing again because we always do so”
Why Do Engineers Need Help?
Engineers are highly skilled in designing and building physical products, but they may not have the necessary expertise to develop a comprehensive digital data management and communication strategy for a company.
In the following list, I can give you some ideas on why I think engineers need help in building data management strategies.
- Need to build a data management strategy:
Everyone understands the Folder/Files paradigm. It was part of our lives for the last 50 years. Modern tools are much more complex. Don’t expect engineers to get it immediately – they have no background in data management. Modern systems are much more complex and require planning and orchestration to be used in the company. Engineers might lack a holistic view of a company’s data management needs. They may not understand the larger organizational goals and objectives that should drive the data management strategy. Without a clear vision for data management and company-wide values to guide decision-making, engineers may struggle to develop an effective strategy. - Not familiar with data management tools, heavily loaded history of desktop CAD tools:
Remember, in the past, an engineer who has a better understanding of computers usually becomes “a CAD administrator”. Engineers are often trained on desktop Computer-Aided Design (CAD) tools and may not be familiar with modern data management tools and software. While they may understand the technical details of data management and communication tools that are essential for an efficient and effective digital strategy. - Limited perspective on modern data sharing and communication:
Traditional data sharing is email and shared folders. While it is indeed powerful, it is not enough to build an efficient mechanism to share information (not files) and doesn’t support best practices in data management and communication, such as cloud-based collaboration and real-time data sharing. Without this knowledge, they may not be able to develop a strategy that meets the needs of a modern, digital workforce.
Conclusion:
The importance of digital transformation in manufacturing companies should not be underestimated. While engineers bring valuable technical expertise to a company, they may not be the best choice for developing a comprehensive digital data management and communication strategy. A heavy load of the past plays a bad game preventing engineers to come up with the right approach and support digital tools adoption to replace Excel.
While a digital transformation strategy may take time and financial resources to implement, the long-term benefits are worth the investment. Manufacturing companies must keep up with the fast-paced world of technology to stay relevant, efficient, and profitable.
REGISTER FOR FREE and check how OpenBOM can help you build a better data management strategy.
Best, Oleg
Join our newsletter to receive a weekly portion of news, articles, and tips about OpenBOM and our community.