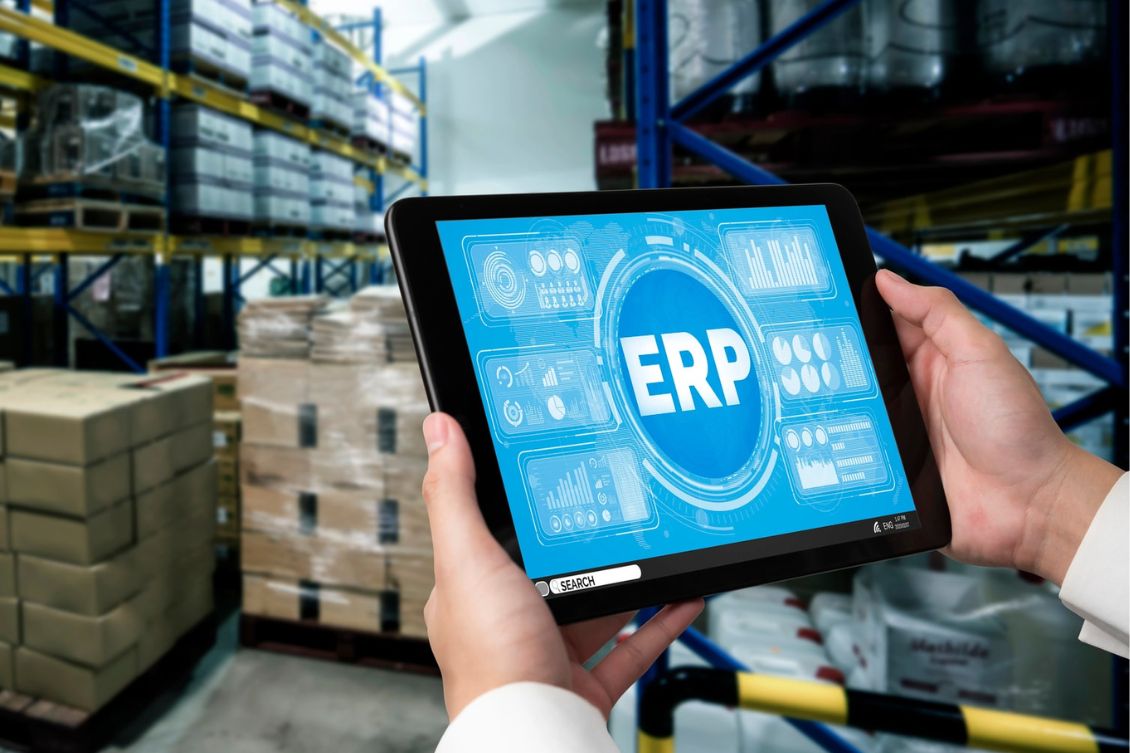
Digital transformation is changing the way how manufacturing companies design products and manage operations. It brings many changes that impact their underlining systems – design and engineering, PDM/PLM, supply chain management, and ERP system. For decades Enterprise Resource Planning (ERP) software has been a crucial tool for manufacturing companies focusing on improvements in how to manage core business processes – finance, procurement, and manufacturing planning. As companies embrace Industry 4.0 and digital-first business models, ERP systems are being redefined and transformed to meet new product development and operational demands.
In my article Bridging the Gap: How Digital Transformation is Merging PLM and ERP Software, I explored the way product lifecycle management and enterprise resource planning software is changing together with growing focus on the data and business processes digitalization. An ERP system is not a silo anymore, but a piece in a set of connected services working together to support the digital value chain from design and engineering to maintenance and support connected into a digital thread.
In my article today I want to talk about the modern transformation of enterprise resource planning systems and how all systems are transforming in a single connected digital thread of services supporting modern manufacturing organizations.
I also want to emphasize the opportunity to use technologies that can simplify the level of PLM-ERP implementation and integration complexity and speak about the potential of combining cloud technologies with advanced data management systems, graph modeling, new types of queries, data science, and AI. At the core of these advancements is the knowledge graph, which provides a foundational framework. A knowledge graph can model the complex constraints inherent in both PLM and ERP systems, offering the flexibility needed for product lifecycle management and engineering models, while also supporting essential business processes and management software. Check out my article – The Importance of Knowledge Graphs for Future PLM Platforms.
The emphasis is now on comprehensive data integration, agility, and connectivity, essential elements for modern manufacturing planning, financial oversight, and strategic growth. Let’s discuss how PLM and ERP software are evolving to meet these demands, highlighting the growing importance of product data, integration across the product lifecycle, connections with the supply chain, and the emergence of innovative business models.
What’s Wrong with Existing ERP Platforms?
Existing ERP software systems typically lack the flexibility required by modern manufacturing businesses, particularly in supporting agile and rapidly configurable product development. Designed primarily for transactional and operational efficiency, ERP systems excel at scaling existing manufacturing, core financials, supply chain, and logistics but struggle to keep pace with the dynamic needs of engineering and product lifecycle management. These platforms often operate on rigid data structures and pre-defined workflows that make it difficult to adapt to evolving product designs, unique configurations, and customization demands. As a result, they fall short of supporting processes like Configure-to-Order (CTO)+, which require a high level of agility and adaptation to accommodate customizable products and specific user configurations and specifications.
Another significant limitation of traditional ERP systems is their disconnect from product development and engineering. Product design and development are typically handled in separate PLM or PDM systems, resulting in fragmented data flows and limited visibility across the product lifecycle. This segregation creates challenges for engineering teams who need seamless, real-time information to collaborate effectively and optimize production. Without a unified view of product and operational data, ERP platforms cannot adequately support the iterative nature of modern engineering processes or enable cross-functional collaboration. As a result, organizations relying solely on ERP often face delays, reduced innovation, and missed opportunities to streamline product design and manufacturing in line with agile and configurable product strategies.
What’s Wrong with Existing PLM Platforms?
The architecture of all leading PLM platforms was built over 20 years ago, primarily to meet the needs of mechanical engineers. The most recent among them, Aras, still dates back significantly, while older platforms like Teamcenter and Windchill have even deeper roots. Despite the sophistication and optimization of these platforms, they are all built on SQL database architectures, which have limited semantic capabilities and struggle to scale to meet the demands of today’s growing digital environments. Additionally, all of these platforms are single-tenant, and their cloud (SaaS) strategies largely focus on hosting and automating existing platforms on cloud providers like AWS, Azure, and GCP, rather than building true multi-tenant SaaS solutions.
While these platforms remain essential for existing customers and will not disappear anytime soon, they have significant limitations. They lack advanced digital modeling capabilities, struggle to support interdisciplinary engineering needs, and fall short in collaborative engineering, query expressiveness, large-scale queries, and the flexibility required to meet the evolving demands of modern manufacturing businesses.
The Modern Transformation of Manufacturing Planning and Finance
Manufacturers today operate in a highly complex environment, balancing the need for agility with the demands for precise financial planning and inventory management. ERP software, historically designed to streamline internal processes and data within a single organization, is now evolving to address a wider ecosystem that spans complex product development, suppliers, partners, and customers. Here’s how ERP software is transforming:
- From Transactional to Strategic: ERP was once mainly transactional, handling tasks like order processing and financial reporting. Today, it has become a strategic tool, enabling real-time insights that inform critical decision-making. Advanced analytics capabilities now allow manufacturers to forecast demand, optimize supply chains, and allocate resources effectively.
- Agile Financial Planning and Operations: Modern ERP systems provide dynamic budgeting, forecasting, and scenario planning capabilities, enabling finance teams to adapt quickly to market changes. By integrating financial data with operational data, ERP systems can now provide a unified view that improves accuracy in cost accounting, pricing strategies, and profit margins.
- Real-Time Product Data Integration: Product data is increasingly integral to ERP systems, particularly in industries that rely on fast design iterations and complex engineering. Access to detailed product data helps ensure that manufacturing plans are accurate, change orders are tracked, and the financial implications of design decisions are clearly understood.
The last one is extremely important because it introduces live connectivity between engineering and manufacturing silos with the goal to bring them together to increase the effectiveness of the decision process and acceleration of development processes.
The Importance of Product Data and Lifecycle Integration
Product data is the lifeblood of manufacturing in the digital age. Breaking the monolithic silos of existing systems is critical to transform manufacturing companies. As product complexity grows, integrating ERP with Product Lifecycle Management (PLM) software becomes essential.
The picture below shows you the research work that is done by Mercedes Benz cars about how to organize layers of applications.
By bridging the gap between design, engineering, and production, manufacturers can:
- Ensure Data Consistency and Accuracy: Integrating ERP and PLM software provides a single source of truth, minimizing errors that arise from disconnected systems. Engineering changes are automatically reflected in manufacturing plans, reducing rework and delays.
- Accelerate Time-to-Market: With a seamless flow of product data from design to production, manufacturers can ramp up production quickly and respond to market demand in real-time, without waiting for manual data transfers or redundant approvals.
- Enhance Collaboration Across Functions: By connecting design and engineering with manufacturing and finance, ERP software enables cross-functional teams to work from a unified product definition, breaking down silos that typically slow down product development and introduce costly errors.
Connecting ERP with the Supply Chain
Modern ERP systems are no longer limited to internal processes; they extend into the supply chain, supporting digital threads that create an interconnected network of suppliers, manufacturers, and customers. Key aspects of ERP and PLM/supply chain integration include:
- Supplier Collaboration: ERP systems can now integrate supplier data for a holistic view of inventory levels, lead times, and production schedules. By aligning manufacturing and supplier timelines, manufacturers can optimize inventory levels and avoid stockouts or overproduction.
- End-to-End Visibility: ERP software provides end-to-end visibility across the supply chain, enabling manufacturers to track raw materials, work-in-progress, and finished goods as they move through the value chain. Real-time data on inventory and logistics status empowers businesses to make proactive decisions and avoid costly disruptions.
- IoT-Enabled Insights: IoT sensors embedded in production equipment and supply chain assets can provide ERP systems with real-time data on machine performance, material usage, and logistics. This data allows for predictive maintenance, demand planning, and optimized scheduling, reducing downtime and ensuring production continuity.
New Business Models: Product as a Service, Maintenance, and IoT
Digital transformation has opened the door to innovative business models that create new revenue streams and align with customer needs. ERP software is increasingly tailored to support these models, including:
- Product as a Service (PaaS): This model transforms the traditional approach to product sales. Instead of purchasing a product outright, customers subscribe to a service that includes the product. ERP systems manage these complex billing and revenue recognition needs, allowing manufacturers to transition from a one-time sales model to a recurring revenue model.
- Maintenance and Service Management: With IoT and ERP integration, manufacturers can offer predictive maintenance as part of their services. By tracking the health and usage patterns of equipment, ERP systems can notify customers when maintenance is needed, minimizing downtime and ensuring optimal performance. This approach enhances customer satisfaction and provides a continuous revenue stream for manufacturers.
- IoT-Driven Operational Excellence: IoT technology is now a core component of digital transformation, providing real-time data that ERP systems leverage for smarter operations. IoT-enabled ERP can monitor equipment conditions, predict failures, and automate routine tasks, leading to greater efficiency and lower operational costs.
Future Product Development Platforms
What is the future of product development platforms covering functions of product lifecycle management, customer relationship management, project management, human resources, and accounting software? How do ERP vendors and an Enterprise resource planning system concept evolve from the current rigid model to a flexible set of services? I captured the following picture from an article published by Prof Martin Eigner in his LinkedIn post, where he was sharing his thoughts about single PLM+ERP system development and the example of SAP EPD. Here is an interesting passage:
I am following the EPD approach with interest and am also associated with this project via a doctorate. In fact, we are getting closer to our basic idea of “one system”. I am already recommending the system to my customers for medium-term PLM decisions. According to Figure 1 and 2, the system is clearly one of the innovators together with OpenBOM by Oleg Shilovitsky. Unfortunately, here comes the typical engineer “but” …. Functional coverage is not yet guaranteed and I still see the old 30-40 year old data model with unrevised parts and a connection of the so-called Effectivity (valid from-valid until) that is completely unsuitable for traceability and Digital Twin solutions. I don’t like to use specific system names in posts, but here’s the exception. Let’s dream of the One-System solution. Let’s mix the Low Code engine of Aras with the functional scope of Contact, the technology of OpenBOM and the strategic and integrative importance of SAP EPD.
So, where will the future take us? The engineering and manufacturing world is moving away from the monolithic architectures of the past. We are departing from a siloed and disconnected world in the future of composable architectures and online services. The first step is to break monolithic systems and create a cohesive and connected data model to focus on solving business problems. Although current mainstream PLM platforms are widely adopted, I can hear the voices of many companies that are looking for “different ways to do business”. Although it won’t stop existing PLM business immediately, it creates a trigger for PLM vendors and customers to think about what is coming.
Here are principles of modern product development platform architecture with the example of OpenBOM technological foundation.
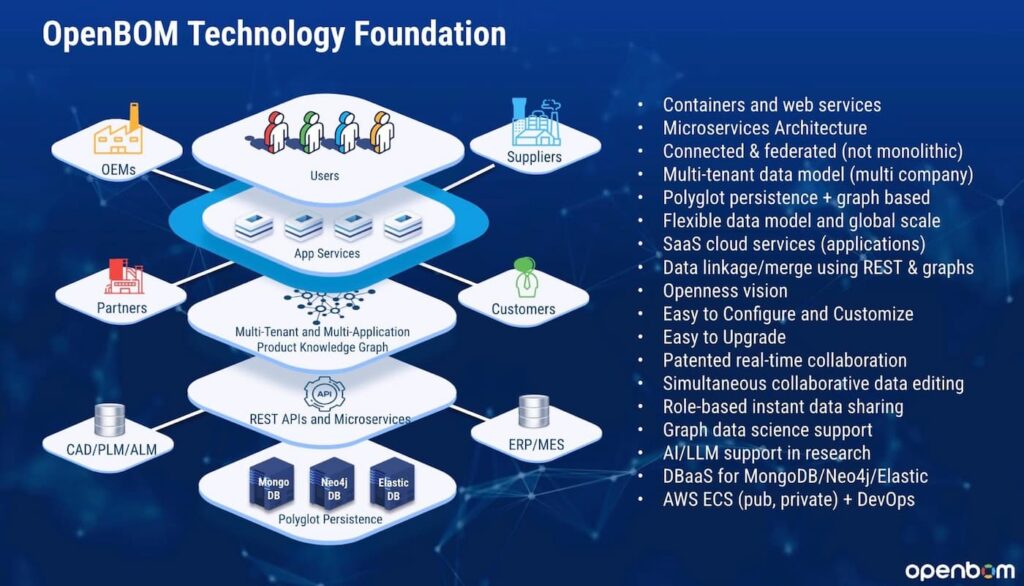
OpenBOM solves the problem of monolithic applications by bringing a new architecture of PLM applications. The three foundational principles of OpenBOM architecture are
- Multi-tenant architecture
- Real-time dynamic flexible data model
- Real-time collaboration and change management
These three principles allowed us to create a robust architecture and platform that can be used in combination with many applications and services
Future Digital Workflows
Digital workflows streamline the flow of information and tasks across departments, transforming traditional, paper-based processes into automated, collaborative operations. In product lifecycle management, a digital workflow unites design, engineering, and procurement, providing a multidisciplinary (product lifecycle twin) view of product data. OpenBOM plays a crucial role in enabling this digital transformation by connecting teams through a cloud-native, real-time environment.
OpenBOM allows engineers to effortlessly update product designs, while procurement teams gain immediate visibility into parts requirements, pricing, and availability. By establishing a unified platform, OpenBOM ensures that accurate, up-to-date information flows between stakeholders, supporting faster decision-making and reducing costly errors.
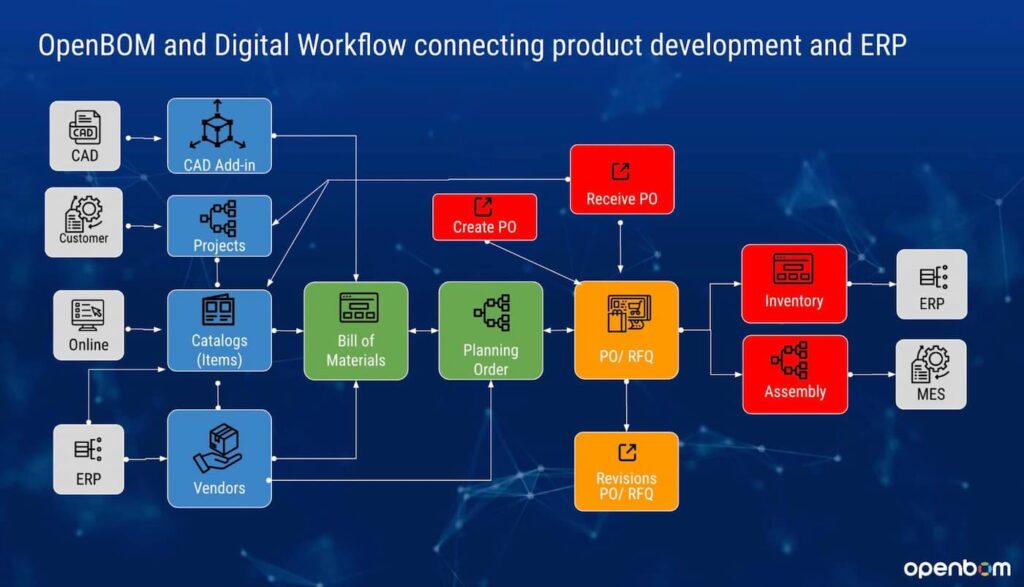
OpenBOM’s integration with ERP systems further enhances this digital workflow by aligning engineering and procurement with broader business processes like inventory management, costing, and supplier coordination. Through seamless data exchange, OpenBOM enables a smooth transfer of product data from CAD systems to ERP, ensuring that every item and its associated attributes are readily accessible. This integration not only bridges the gap between engineering design and enterprise resource planning but also eliminates redundant data entry, minimizes discrepancies, and enhances traceability. With OpenBOM, companies benefit from a streamlined digital workflow where engineering insights and procurement requirements are synchronized, enabling a more agile, connected, and efficient operation across the product lifecycle.
Conclusion
ERP software that once provided a backbone for transactional processes will be evolving into one of the three foundational pieces of modern product development platforms – engineering and product development (PLM); operational and purchasing services (ERP/MES), and sales and customer-related processes (CRM). All these systems together evolved into a pivotal change to bring digital transformation strategies, connecting data and processes across manufacturing, finance, and supply chains. Modern PDM, PLM, ERP, MES, and CRM systems support digital engineering and allow manufacturers to unlock the full potential of digital transformation by integrating once-siloed systems into a cohesive digital thread.
By breaking down traditional silos, ERP software now offers manufacturers a more agile, connected, and data-driven approach to planning and execution. With advanced capabilities in data connectivity and IoT integration, ERP systems allow manufacturers to capitalize on emerging business models, foster innovation, and enhance customer satisfaction. Ultimately, digital transformation in ERP supports a future where manufacturing and finance work seamlessly together, unlocking value across the product lifecycle and building a foundation for sustained growth in an increasingly interconnected world.
REGISTER FOR FREE to check how OpenBOM can help you.
Best ,Oleg
Join our newsletter to receive a weekly portion of news, articles, and tips about OpenBOM and our community.