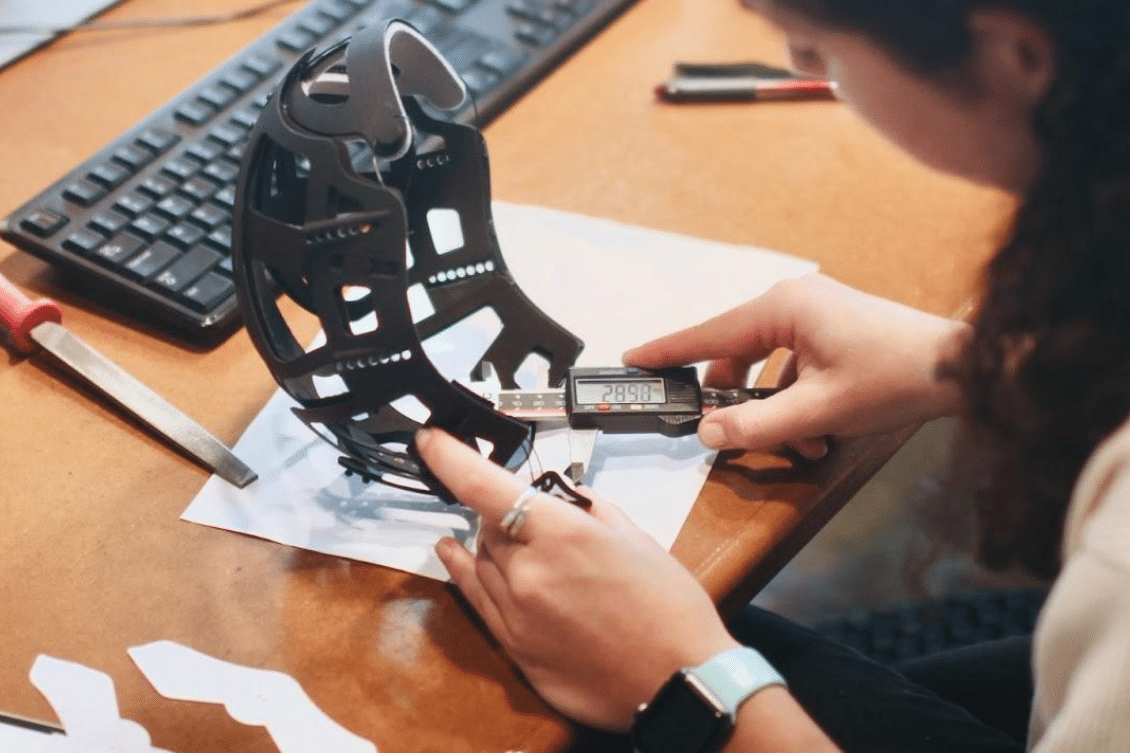
During product development, the journey from concept to production is complex and bumpy. One of the critical factors that determines the success of your product launch is testing. Testing is not a final checkpoint before a product’s release; rather, it is a series of strategic phases that ensure a product’s functionality, reliability, and readiness for mass production. The three key testing phases you need to test before starting mass production are Engineering Validation Testing (EVT), Design Validation Testing ( DVT), and Production Validation Testing (PVT).
In this blog post, we will go deeper into each of these types of tests, what their goals are, and what the overall results should look like. By understanding the differences between these phases, you’ll gain insights into the necessary steps that bridge the gap between concept and product launch.
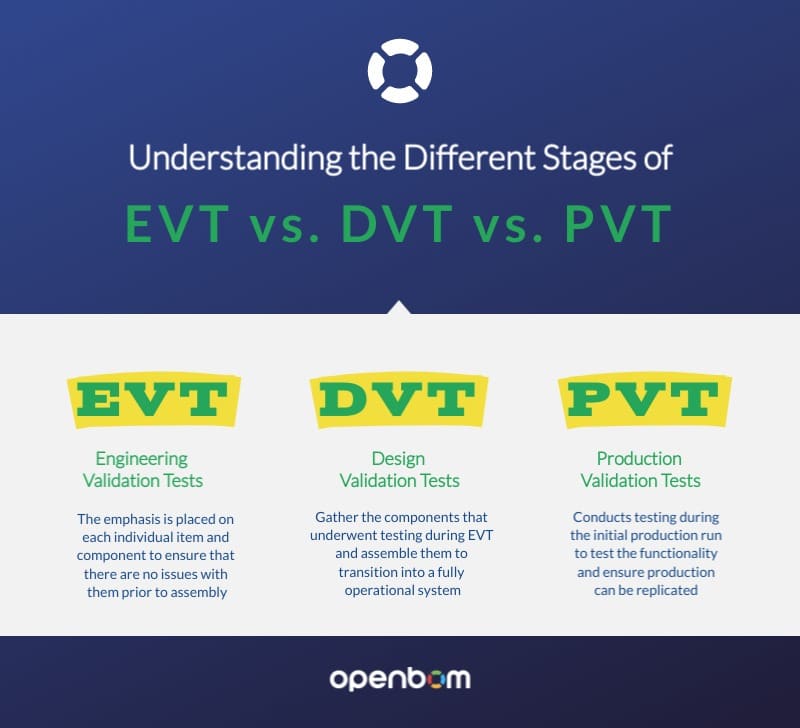
What is Engineering Validation Testing (EVT)?
This phase serves as the initial test that fulfills all of the requirements laid out in the Product Requirements Document (PRD). This phase can also be looked at as the transition from a theoretical design to something physical.
The goal of the EVT is to identify any flaws or shortcomings in individual components before they come together in assembly. Rather than moving towards a fully assembled product, engineers should test each component to ensure that all components are approved before moving to the next steps.
- EVT Quantities: 10 – 40 units
- EVT Timeline: 5 weeks
EVT is also not a one-time deal. As engineers find weaknesses in the design then they need to request changes. Prototypes are made of those proposed changes to test the performance and ensure they are consistent with the PRD.
EVT is seen as the foundation of product development as it inspects the quality of each component. This can save time and reduce the need for rework if components do not achieve the level of quality required.
What is Design Validation Testing (DVT)?
Now that you know each component has acceptable quality, you can shift your energy to combining the EVT with the cosmetic requirements. DVT can be looked at as the bridge that connects the parts validated during EVT with a fully functional system.
The goal during DVT is to verify that the product’s design meets the desired functionality and performance that is required. You are moving away from looking discreetly at individual parts and moving towards the holistic picture, the entire product. Common tests during this phase are the following:
- Drop
- Burning
- Lifecycle
- Durability
- Functionality
Similar to the steps taken during EVT, DVT requires collaboration between multiple teams. Design engineers, mechanical engineers, electrical engineers, and more all need to work together to make sure the prototypes made have acceptable quality.
These prototypes made at this stage can also be used for certifications and marketing purposes as well to show improvements and that milestones are being achieved.
- DVT Quantities: 50 – 100 units
- DVT Timeline: 6 – 8 weeks
If you have successful EVT tests then you have the green light to move into the PVT stages of testing, moving you a step towards a successful product launch.
What is Production Validation Testing (PVT)?
The PVT tests serve as the final line of defense before a product enters the market. The goal of these tests is not just to ensure that the product is functional and made to the correct specifications, but that the product can also be manufactured at scale. PVT are tests on the product that is in production and usually, these tests are made during the pilot run.
While the previous two tests, EVT and DVT, looked at both the components and how the assembled product is, PVT looks at one more step, the manufacturing process. It makes sure that the product can be replicated at high volumes and with consistent quality.
PVT highlights, any processes that might act as a bottleneck as production scales up. These can include anything that acts as a manufacturing bottleneck all the way to issues with parts or sub-assemblies that are sourced from suppliers.
- PVT Quantities: 10 – 20% of first PO
- PVT Timeline: 3 weeks
A successful PVT puts the stamp on the final approval process which means you can finally start to mass produce products for your customers.
Conclusion
Sometimes during the product development process, people want to get ahead of themselves. They end up skipping tests and assume everything is going to work well. While skipping these steps can put you ahead momentarily, the amount of rework and costs that add up when things go wrong put you back at the bottom.
Properly carrying out the proper steps of EVT, DVT, and PVT acts as an unbreakable triad that ensures a product will successfully go from concept to market.
Interested in OpenBOM? Register for free and start the free 14-day trial.
Regards,
Jared Haw
Join our newsletter to receive a weekly portion of news, articles, and tips about OpenBOM and our community.