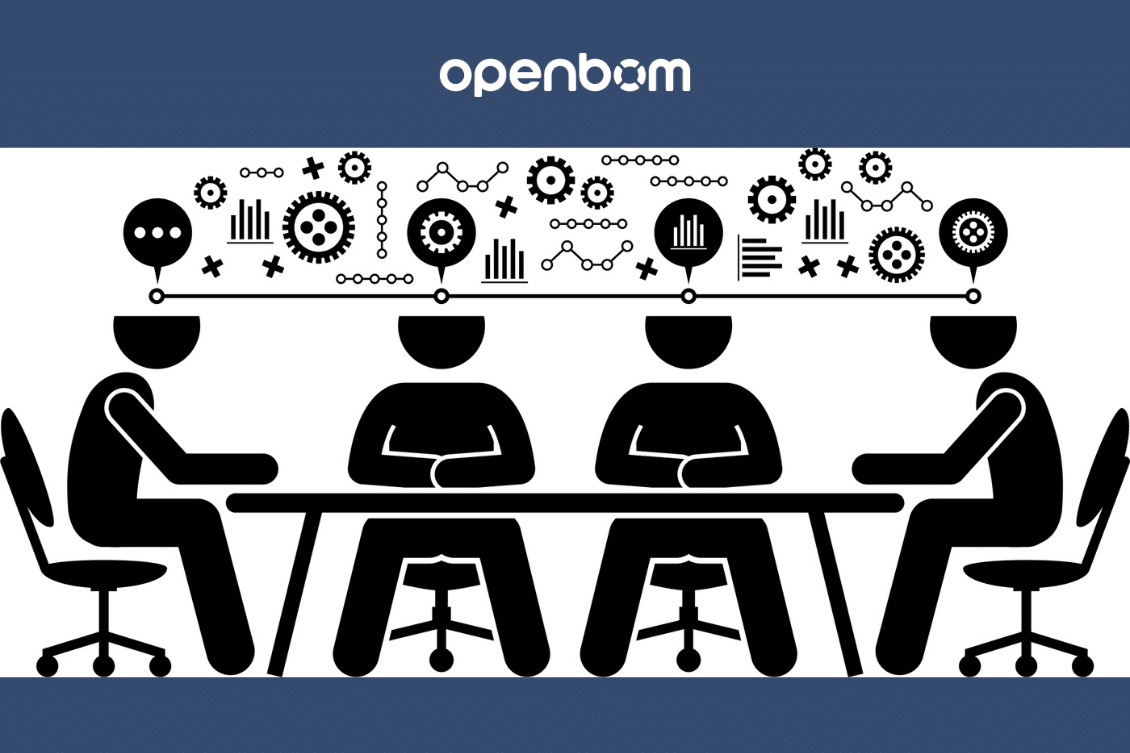
Last year, we engaged with over 1000 companies to discuss their approaches to developing new products and organizing manufacturing processes. The consistent message throughout these meetings was clear: the use of Excel, emails, and files creates a messy, time-consuming, and confusing environment, hindering companies from rapidly achieving their product development goals.
While individual engineers may find sending an Excel sheet to procurement a convenient solution, management and company owners must recognize the current state of product development. In an era where leading manufacturing companies are focusing on digital transformation, relying on Excel spreadsheets, files, and emails is similar to a ticking time bomb. Organizations cannot depend on these outdated methods and still expect to develop new and innovative products with the desired performance and cost-efficiency.
So, what is actually happening, and why are companies slow to recognize this problem?
Digital Transformation and Manufacturing Reality
Product complexity, spanning mechanical, electrical, software, and cloud systems, has reached unprecedented levels. Furthermore, teams have become increasingly global and remote.
Engaging in complex product development with global teams and remote work may sound exciting, but it often turns into an inefficient process marred by complex communication, file transfers, Zoom calls, and a multitude of mistakes.
The core reason for this inefficiency lies in company processes and legacy tools. Astonishingly, the same CAD files, STEP files, PDFs, and Excels used by companies two decades ago are still in use today. Hosting a remote desktop with a 25-year-old CAD tool and exporting a Bill of Materials (BOM) to Excel, bundled with a PDF in a zip file, is a method I recall from the early 2000s. While some advanced companies have adopted Slack and Zoom as collaboration tools, these tools alone cannot meet the demands of modern product development.
In essence, companies are unwittingly exacerbating stress by clinging to old tools and legacy product development methods. Although Product Lifecycle Management (PLM) tools are gaining acceptance, the focus remains far from optimizing data utilization. The mantra of a “single source of truth” still echoes, despite PLM vendors merely shifting their on-premises products to cloud platforms like AWS, Azure, and GCP to address migration and upgrade issues. However, the core products remain unchanged.
Excel Burnout
Here are some examples of how old-fashioned file and Excel-driven processes accumulate, leading to inefficiencies, sluggishness, and mistakes:
- Extracting data from designs is a manual process using Excel, resulting in low efficiency and requiring the manual collection of Excel, PDF, STEP, and other files. Making updates in such a system is challenging, leading to a buildup of mistakes and forcing engineers to perform a substantial amount of non-value-added work.
- Collecting information from multiple engineers working in different disciplines is difficult because they often operate in isolation, with folders and files being the primary repositories for information before it is transferred to procurement, production, and contractors.
- Involving more people in different departments and locations extends the time required to coordinate and review information before it can be transferred for production planning.
- Feedback and changes become chaotic. Controlling who makes changes is nearly impossible, and ensuring consistent data usage across multiple products, projects, and teams remains a distant dream. Excel files (or Google Spreadsheets) are copied and shared via Google Drive, making it exceedingly difficult to locate the correct data.
- Even if the MASTER EXCEL file is stored on the server, extensive communication is required to make changes, and files are not linked to that spreadsheet, necessitating a significant amount of coordination.
- Tracking purchasing and coordinating with contractors and suppliers are buried within email threads, making them nearly impossible to follow up on. Inquiring about historical data, changes, and purchases is a daunting task.
As a result, product development processes have failed to keep pace with the evolving complexity of work. While individual engineers may excel in their tasks, the overall organizational performance is cast into doubt, and the entire process becomes a quagmire of manual labor and coordination. Project management struggles, impeding timely deliveries, overshooting cost targets, and compromising quality.
Conclusion
So, what’s the good news? Here’s the solution: we’ve developed OpenBOM, a tool that can help you bring order to this chaos. OpenBOM enables you to consolidate processes, streamline tool integration, automatically extract data from engineering tools, organize digital BOMs, facilitate RFQ/PO planning, and seamlessly share information with contractors and suppliers.
OpenBOM isn’t a magic button; it requires some digital transformation effort. However, we’ve made it easily accessible to you, offering online support and onboarding training, all at an affordable price for organizations worldwide.
The cost of an OpenBOM subscription will quickly be offset by preventing a single costly mistake next month.
Perhaps the most significant benefit is this: if you are an operations manager, engineering manager, startup founder, or owner of a manufacturing company, OpenBOM provides you with a single repository where you can effortlessly access all information and find answers about your product and control processes in a much more efficient way.
Don’t just take my word for it—explore the stories of OpenBOM customers and G2 reviews to witness the transformative impact firsthand.
Call to Action
Ready to revolutionize your product development processes? Contact OpenBOM today, and embark on a journey toward enhanced efficiency and productivity.
REGISTER FOR FREE and start using OpenBOM today.
Best regards, Oleg
Join our newsletter to receive a weekly portion of news, articles, and tips about OpenBOM and our community.