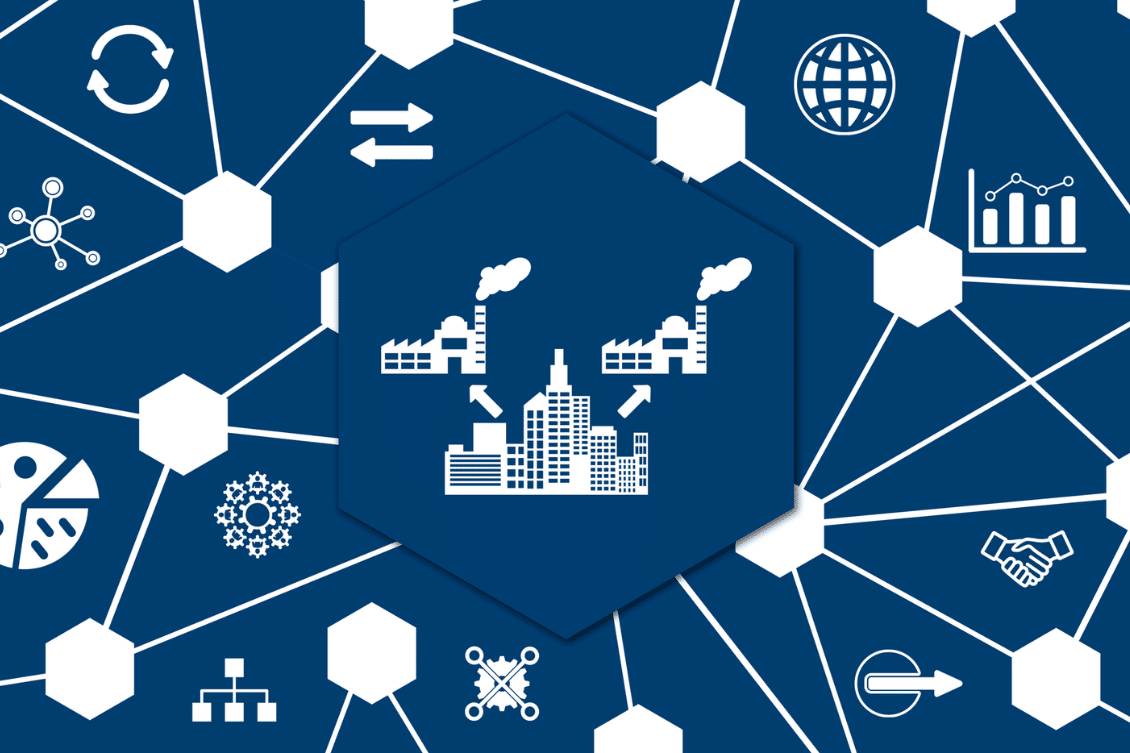
In the ever-evolving landscape of product development, companies must leverage technology to stay competitive. Therefore, manufacturing companies are looking at how to accelerate their processes starting from design and connecting processes downstream to production planning and manufacturing. The most fundamental thing in this process is to connect two silos – (1) Engineering and (2) Procurement. By solving the problem of connecting these two silos, manufacturing companies can unlock the huge power of agile new product development and acceleration of processes. The disconnect between engineers and procurement (supply chain) planners is one of the biggest ones in industrial companies.
In my recent articles earlier this week, I was speaking about how OpenBOM can help you to accelerate the new product development process by connecting these two main silos – engineering and buying parts and materials needed to build a product. Check them out first:
- What Differentiates OpenBOM NPD Solution From Traditional PLM Systems?
- New Product Development User Stories: A New Dawn with OpenBOM
What makes OpenBOM different is a combination of functions that are traditionally available in two different application suites – PLM and ERP. While the separation makes sense for large high-scale production environments, it cannot be used for small batches and prototypes. It slows them down and turn them away to use Excels and other similar solutions.
When you’re building new products in both SME and enterprise companies, you don’t need to have a high-scale ordering system. Actually opposite, you want to work on small batches, but… have a quick turnaround time between engineering changes and purchasing of companies for prototyping or small production batches.
Let’s check the following 5 elements of the OpenBOM NPD solution and how it streamlines the process. This guide takes you through the salient features of OpenBOM, showing how it seamlessly connects the digital thread from design and engineering BOM to inventory and ordering.
Digital Thread – Closing Gap Between Engineering and Procurement
OpenBOM bridges the divide between engineering and procurement in a groundbreaking way. The platform creates a continuous digital thread, linking the initial design phase with procurement. The digital thread begins with the engineering BOM, a detailed list of all components needed to design a product. The engineering team uses the BOM to specify the parts and assemblies used in the design. Once finalized, the BOM is directly passed on to the procurement team (Order BOM). This seamless transition eliminates miscommunication and data redundancy, reducing time and error risk.
But the seamless transition is just the beginning. OpenBOM collaboration and instant data sharing allow teams to work faster in an agile way. Passing early design/BOM with all Long Lead Items to procurement, iterating fast, and focusing on the supply chain from the early beginning is a killer capability to accelerate new product development.
Digital Catalogs With Items, Quantity on Hand, and Vendor Information
OpenBOM’s digital catalogs function as a central repository for all product-related data, including items, their quantities, and vendor information. This feature not only standardizes data across the organization but also ensures real-time information access. These digital catalogs can be updated in real-time and shared with all stakeholders. They contain comprehensive data for each item, such as item specifications, current stock, and vendor contacts. This centralizes data management, simplifying procurement, inventory, and supplier management.
BOM and Integrated Product Data
One of the key advantages of OpenBOM is its ability to integrate the BOM with all product-related data. It provides a holistic view of all the elements necessary to manufacture a product, from raw materials to the final assembly. This includes data such as cost, weight, and measurements, creating an integrated and easy-to-navigate product roadmap.
Most importantly, OpenBOM supports multi-disciplinary product organization. Companies can have a holistic data set of all systems – mechanical, electronics, software, etc. No more siloed BOM in multiple systems. By utilizing the BOM and integrated product data, teams across the organization can access consistent and updated information, reducing the likelihood of errors and miscommunication.
Create Batch Order and Gap Calculation
The next phase in the digital thread is creating a batch order. The batch order is essentially a command to produce a specified number of units of a product. OpenBOM streamlines this process by allowing the batch order to be directly generated from the BOM.
Once the batch order is created, OpenBOM calculates the gap – the difference between the required and available inventory. This gap calculation assists the procurement team in understanding what materials need to be procured and in what quantity.
Closing the Circle by Sending PO/ Receiving PO and Updating Inventory
Finally, OpenBOM allows you to close the circle by sending and receiving purchase orders (POs), and updating the inventory accordingly. After the gap calculation, the procurement team can generate and send POs to the suppliers directly from the platform.
Once the goods are received, the POs are updated, and so is the inventory. This real-time updating of inventory levels assists in maintaining optimum stock levels and avoiding overstocking or stockouts.
Inventory Management and Lifecycle
The following picture shows you the entire Item and Inventory management lifecycle in OpenBOM. As you can see on the diagram below, BOM –> Order –> RFQ/PO is the foundation of this thread.
Hands-on Demo Video
In this video, I will take you through the all steps of the process starting from catalog creation, defining vendors, quantity on hand, all information about items, prices, etc. Then defining BOMs, creating Order (Planning BOM) and finally generating POs and receiving them back. It is quite long (7 minutes), but it is worth it to see OpenBOM NPD end-to-end.
Conclusion: An Entire Digital Thread Done Fast and Collaboratively
OpenBOM integrates every aspect of the product lifecycle, creating a digital thread that stretches from the design and engineering phase, through inventory management, and finally to the ordering process. This holistic approach ensures that all stakeholders are working with the same, real-time information, promoting collaboration and efficiency.
The result? Faster production cycles, fewer errors, and a streamlined workflow that will revolutionize the way you manage your product lifecycle. Now you’re ready to build!
Register with OpenBOM to check it out for yourself. Step into the future of new product development today!
Best, Oleg
Join our newsletter to receive a weekly portion of news, articles, and tips about OpenBOM and our community.