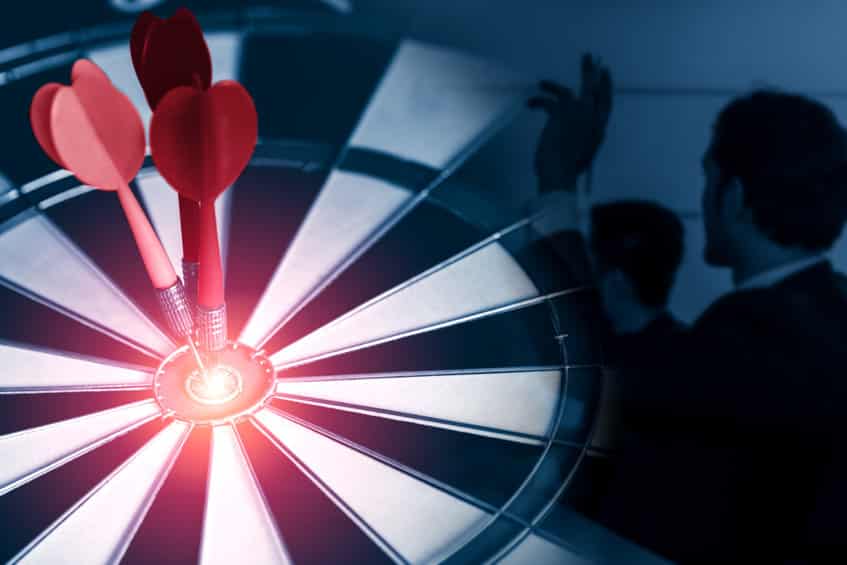
Whether you outsource production to a sole contract manufacturer, or you work with multiple suppliers, your expectations will change as your product matures. Vetting and choosing the right manufacturer depends on where you are in the product life cycle. A supplier who was able to make prototypes and provide low volume production might not be able to scale up for mass production.
Most companies who think they need to change their supply chain base usually take no action. The reason is that it is intimidating to change something with no guarantee of success. Also, it is a long process. However, changing your supplier or contract manufacturer (CM) can have a number of benefits.
There are a number of reasons why someone will want to change their supply chain. After working with thousands of suppliers, contract manufacturers, I can outline the five signs of when you need to make a change in your supply chain.
Sign 1: Can’t control costs
There are many benefits to working with a single supplier or contractor. But keep in mind that certain suppliers have specific expertise. A CM who specializes in sheet metal fabrication might not have the greatest supply chain for electronic components. If this CM is fabricating your electronics as well, you might have an opportunity to search for additional suppliers who have a competitive advantage in this industry.
As your team grows, you can expand your efforts to source parts from suppliers with cost advantages for certain parts/sub-assemblies. This same CM who specializes in metal fabrication might do a good job with cost-down projects for mechanical parts. However, they will be limited in trying to cut down other components, such as electronics because of their lack of knowledge and expertise.
Sign 2: Losing control of quality
When you have a quality issue, suppliers find the quickest and most cost-effective fix as a temporary solution. However, sometimes, for whatever reason, these temporary solutions become the long-term fix. This is why you see the same quality problem come back time after time after time.
As a CM or a supplier, there is a list of steps you need to follow to properly solve the problem. Failing to take these steps will have recurring quality problems.
Quality problems are also taken very seriously. A low-quality product that does not follow the quality standards can damage your brand image.
Sign 3: Lacking the specific team for you
Odds are that when you first vetted and verified your supplier, your plan revolved around your product launch. Perhaps your supplier had the team in order to see you launch your product but they might not have the necessary team to see your product through its lifetime.
As your company grows, you might also pivot your product line from something your current supplier has an advantage into something they do not. Therefore, they lack the knowledge to support you going forward.
No matter how you grow or the product you are launching, it is key to leverage the knowledge and expertise of your CM or supply chain base.
Sign 4: Can not scale-up
Another common reason why you might need to change your supply chain is if your current supplier or CM is not able to scale up production for you. What this means is that they can handle your product launch and low volume production. However, they are unable to increase their output and ship more products.
There are a number of reasons for this. Some factories are happy with their size and don’t want to expand operations. Usually, this is because it’s a financial risk to expand your output because you need to purchase machinery, employ additional workers, take out a loan or fundraise, and more.
Regardless of the reason, if a supplier is unable to procure, fabricate and assemble your forecasted volumes or having trouble keeping up with existing volumes then a change sounds inevitable.
Sign 5: Lack Of Transparency And Bad Communication
Suppliers will do anything to gain your business. They talk themselves up and make many promises. However, once you start working with them, you find it can be quite different than what they promised.
Some of the pillars of a healthy relationship are transparency and communication. If your supplier lacks these skills, you will see multiple different issues that arise:
- Make unnecessary changes to the product
- A long and drawn-out development process
- Longer lead times or late shipments
Lacking proper communication will cause changes to be made that should not have been made,
Conclusion
It is important to ensure you are changing your contractor or supplier if they fail to meet any of these criteria. Now that you know the five reasons, what will be your next step? Will you continue with a company that can’t provide transparency in its communication process and gives you control over quality? Or would you rather find someone who has more experience in scaling up for bigger projects while also being able to maintain low costs so as not to affect profit margins too much?
At OpenBOM we provide you with a tool that can help you measure your work with contractors and suppliers, organize information, streamline data handover between your team and contractor and improve the process.
Check out what OpenBOM can do for you – REGISTER FOR FREE and start a free 14-day trial to test all premium subscription features.
Best,
Jared Haw
Join our newsletter to receive a weekly portion of news, articles, and tips about OpenBOM and our community.