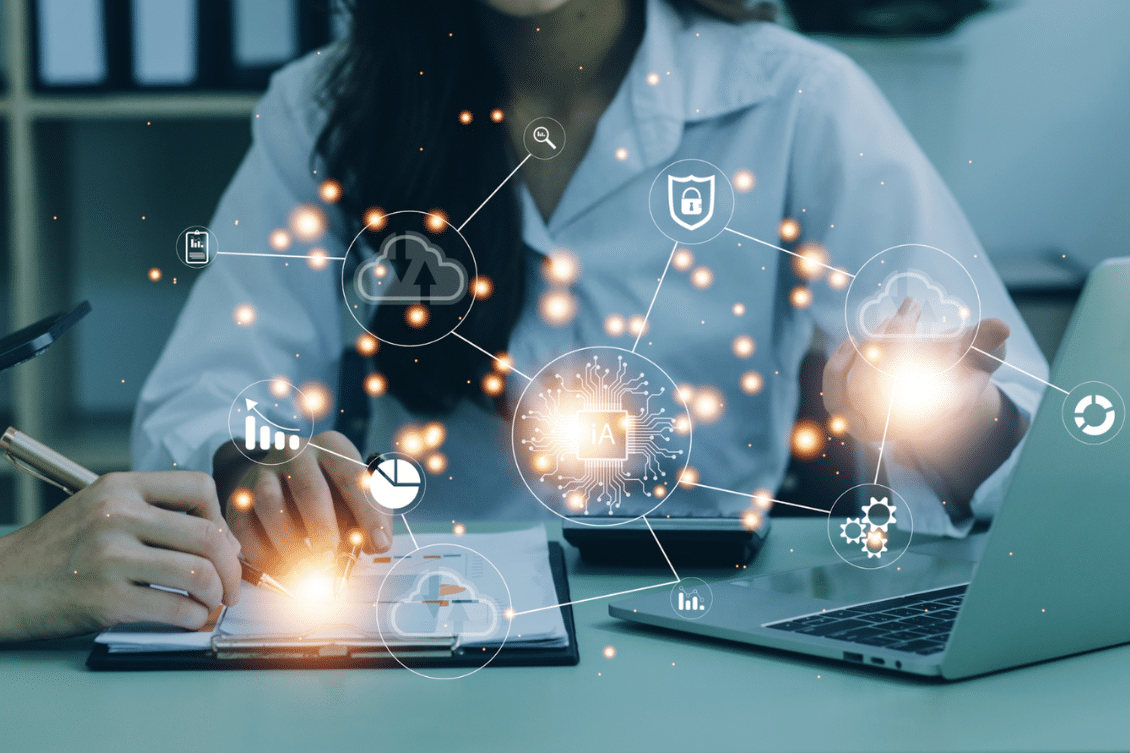
Companies are in the process of discovering how to use digital technologies to change their businesses. COVID caught many businesses unprepared. Companies found that they are bleeding from the processes depending on old technologies and processes that cannot be managed in a digital form. Speaking to hundreds of companies in the past few years, I can see many of them are struggling to organize their information and processes. At the same time, digital transformation has been a game-changer for businesses around the globe, but it hasn’t been without its challenges. In this blog, we will explore the three biggest challenges that engineering businesses are experiencing in the process of digital transformation.
Computers, Folders, Files… It is a mess.
Traditionally, businesses relied heavily on people and documents. Digitalization made it possible to save, store, and manipulate documents electronically. However, the challenge then became emailing copies and maintaining version control. This is how the typical engineering and manufacturing business is working.
Since no one uses drafting boards (at least I didn’t see them for the last two decades), companies are using network drives and CAD systems. This is a typical engineering universe where engineers are crafting their projects and organizing their information. Network drives, folders, files – you will see it in all organizations around the globe. It is the engineering comfort zone. But all these engineers are struggling with the management of these files and processes around them.
On the side of engineering, managing CAD files and revisions was a majority of work organized by PDM/PLM systems. The release process is one of the most important and this is how engineering can push files “over the manufacturing wall” which is heavily dependent on file approvals. Downstream, CAD files are transformed into Excels, PDFs, STEPs, and other useful pieces of information that are barely interconnected into a meaningful and, most importantly, manageable set of information.
How To Move From Documents To Data
Digital transformation happens when moving from documents to data, which creates new challenges. Engineers are pumping CAD files into other forms of files – Excels, Drawing PDFs, STEPs, and others, but even placed in secured “released” folders, these files are not becoming data. They are just files barely organized by PDM (SQL-based data management) systems into the lists of revisions.
The real-time data changes, collaboration, communication, and processes. Sending Excel and PDF files to a contractor won’t make it a process. Even more, it won’t make it a digitally signed contract with correct engineering information (drawings, specs, comments, quotes, etc.). Without having these pieces of information organized and traceable, the process is still sharing files (although in digital form). It is still not a fully digitally described product with all pieces of information that are connected.
Applying connections between data is another big challenge for most companies. Having a way to connect engineering data to production, manufacturing, and customer experience is a big deal, and without the organization of processes with digital data presentation connected together, it will remain pieces of documents without a way to trace back what happened a few months (or a few releases ago). Even more, you have practically zero chance to connect it to the supplier or customer information in real-time.
Closing The Gap Of Digital Transformation
If you have a mess, don’t bring computers in. You will create a “computerized mess”. Bringing computers to manage files (digital documents) helps to put them in a server room (or even into cloud file storage), but in no way helps you to organize the process. It also doesn’t allow you to connect data and processes together.
Setting digital product data management and organizing digital business processes must be a goal for every organization if you don’t want to live in a place where you have all your information disconnected, not updated, and lost one day. That is the foundation of your digital transformation strategy. The foundation of this is to move from files to product lifecycle management strategy and supply chain management processes using digital data instead of files. Check these two articles – 3 Steps to Take Your Product Strategy Beyond Excel and Rethinking Design Collaboration. But let me give you a very short cheatsheet of what you need to do first.
Organize a system of items
Everything is an item in the engineering and manufacturing world. Material, Off-the-shelf component, purchased assembly, custom assembly, an entire product. You need to create records of everything. Don’t think “file”, “CAD part”, “Solidworks assembly”, etc. Think about items and how to classify them, and how to attach valuable information to them.
Build products, assemblies, and everything else using Items
You can call them assemblies, products, BOMs, etc. But the important point is that you build them using Items. Not by creating Excel files and sticking Part Numbers there. That will not scale. It is not a Solidworks assembly or PCB design file. Building product structures from a database of items ensures that not a single piece of data will be duplicated instead of being re-used. This is how it starts. The outcome is a single model, with no duplicates and the ability to make analyses, discover relationships, and many others.
Connect engineering, production, and customer silos
While product information is organized using Items and Assemblies (BOMs) using well-defined items, you are halfway done. The third step is to start linking information together. Most of the manufacturing businesses today are copied (I call it syncing data) between multiple places. You can see Excel files copied from folder to folder, CAD files copied and transformed between formats, etc. It is a super inefficient way to work that leads to mistakes and doesn’t help you to build a set of intertwined information. That would be your goal. Instead of copying data that will soon become outdated and not updated, you need to build connections.
What System Do I need?
This is a big question many engineering and manufacturing businesses are asking themselves. And this is one of the most confusing ones. For a very long time, business systems were in the state of developing “databases for a company” to manage all data. This is how most enterprise business models worked. The logic was to find the right system to put all data in a single database and then everyone will have up-to-date information. It was (still is) in many ways a business culture, business value, and business strategy. But the best-kept secret of the industry is that these systems don’t want to share data with others. They want to sell you other “functions” of the same system. Things are going to change in the coming years. In a modern business transformation, companies are looking at how to build a digital foundation for their business, create a collaborative effort, and connect their product-related data with operating models and supply chains. Therefore DATA will be coming first in business systems of the future. Pick the system that focuses on the data, and makes it shareable and open – this is a goal of business transformation for modern manufacturing businesses. We will talk more about it in future articles.
Conclusion:
Digital transformation has brought many benefits to businesses, but engineers and manufacturing companies still need to find their path to digital nirvana. From the limitations of digitalization to applying it to the digital thread, businesses must overcome various obstacles to succeed in their digital transformation journey. It all starts with the right way to manage information, leaving the old folders, files, and spreadsheets paradigms behind. It is not a simple problem to change, because it was cultivated by businesses in the last 20-30 years. But we are close to solving these problems. Because in the current manufacturing world, companies operating with CAD/PDF files and Excel won’t survive.
Want to check how to make a switch? Check what we do at OpenBOM. Learn more from our blog and REGISTER FOR FREE to learn more about what we do.
Best, Oleg
© Image credit armmypicca, 123RF Free Images
Join our newsletter to receive a weekly portion of news, articles, and tips about OpenBOM and our community.