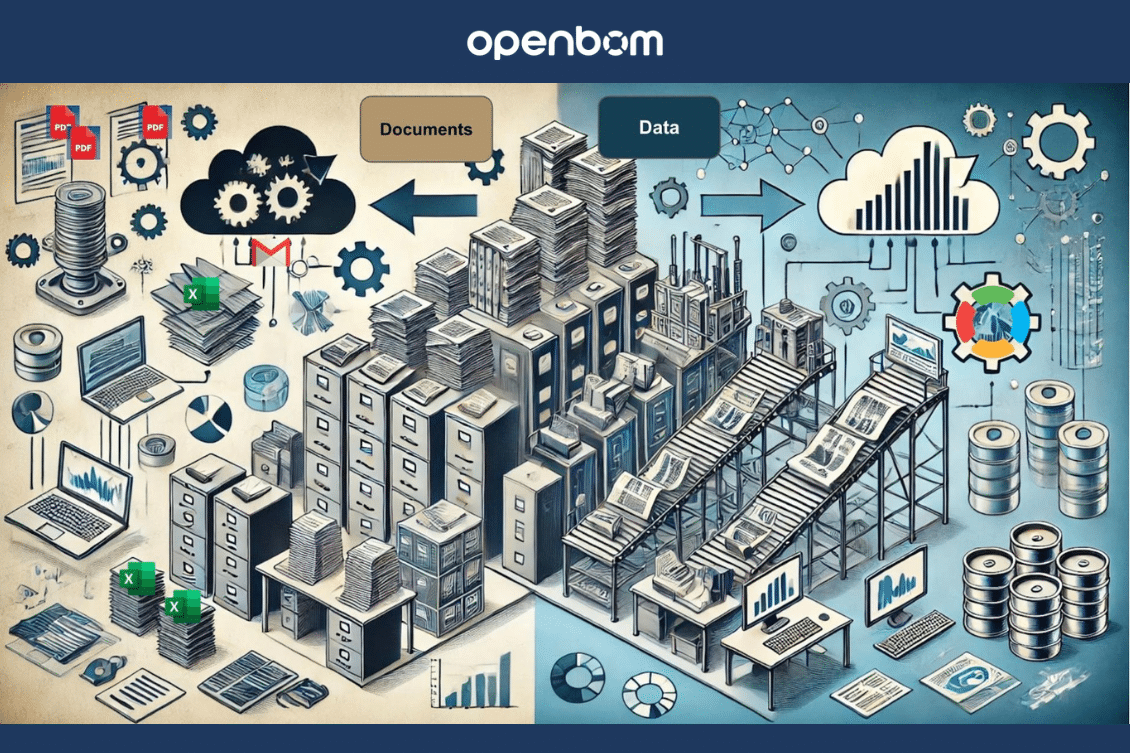
The digital revolution is reshaping industries worldwide, and manufacturing is no exception. Here are a few interesting data points that can demonstrate to you the status quo of a digital transformation. According to recent research made by EY about discrete manufacturing, a staggering 68% of CEOs from the world’s largest industrial product companies are ramping up investments in digital technologies. Yet, only 25% of manufacturers feel confident that their data is properly organized, traceable, and reliable. While digital transformation is a buzzword echoed in boardrooms globally, an astonishing 70% of manufacturers still rely on manual data entry into Excel spreadsheets and other file-based systems. This gap highlights a critical need for a shift from document-centric to data-centric processes to enhance decision effectiveness.
However, the value gap of existing PLM tools is not less shocking. According to CIMdata 2023 market research published earlier this year, only 17% of companies cannot live without their PLM software, the tools mostly used in traditional product data management scenarios, and 37% of companies think those are only engineering tools for product development process and traditional document management. The use of these tools in extended scenarios such as supply chain management, manufacturing process, and maintenance business processes is limited and 27% of companies think that product lifecycle tools are too expensive.
There is a huge gap between management’s desire to digitally transform their work and the reality faced by both small and large manufacturing businesses, as well as the process they need to go through to make that change. In my article today, I will help you learn more about a major element of the digital transformation trend that is happening in the industry and how your organization can take steps to make a change.
Moving from Documents to Data
Over a decade ago, industry expert and blogger Jos Voskuil penned an insightful three-part series discussing the fundamental shift from file-based to data-centric systems. In part one, he explained how file-based systems lead to data silos, duplications, and version control nightmares. Part two dug into the advantages of data-oriented environments where structured, intertwined data fosters better collaboration, consistency, and informed decision-making. In part three, Jos emphasized the long-term business value of data-centric systems, illustrating how they unlock flexibility, seamless integrations, and more efficient workflows across industries.
For those interested in a deeper dive, Jos Voskuil’s original articles provide valuable insights into this transformative shift. I didn’t realize how fast those 10 years passed. I can see many examples of new “digital” experiences around us these days. B2C businesses clearly were on the front lines of transformation. They realized that the only way to win the business is to create technologies that connect well with a smartphone and personal digital experience.
Is Manufacturing Moving Digital?
In B2B and manufacturing, I can see signs of progress with companies thinking about providing services online (so-called online manufacturing). Among them online platforms provide on-demand manufacturing services similar to Xometry, offering rapid prototyping and production solutions. Proto Labs specializes in fast prototyping using various technologies like CNC machining and injection molding. Fictiv connects users with a global manufacturing network, focusing on CNC and 3D printing for agile production. Fast Radius integrates digital tools for streamlined manufacturing across different processes. Hubs(formerly 3D Hubs) offers localized production and instant quotes for 3D printing and machining. Lastly, Plethora is known for custom parts manufacturing with real-time pricing and rapid delivery.
On the side of software providers, I can see tools that can digitally transform and provide an experience to provide their services in a digital form. Here are a few examples of companies like Paperless Parts that help manufacturing shops make faster quotations for customers. Another example is Jiga.io which helps companies find contractors for custom parts.
A Familiar Digital Transformation Example Outside PLM
Consider a commonplace scenario: planning to buy new tires for your car. Initially, you might find a tire shop through Google—a digital tool—but then the process reverts to traditional methods. You call them, provide your car model and tire specifications, and wait for them to email you a quote. They might send multiple emails, request more calls, and require you to schedule an appointment over the phone. This convoluted process can be frustrating.
Contrast this with a more streamlined experience. Visiting the Costco Tire Center website, you’re asked for just one piece of information: your car’s license plate number. Instantly, you’re presented with tire options tailored to your vehicle, and you can schedule an appointment online. The difference is stark—a cumbersome, document-heavy process versus a seamless, data-driven experience.
The PLM Parallel: From CAD to Quotation
This analogy extends to Product Lifecycle Management (PLM) systems. Many engineers export Bill of Materials (BOMs) from their CAD systems into Excel files. These spreadsheets, along with various STEP, STL, PDF, and DXF files, are organized in folders by revision and sent to procurement. The procurement team then validates part numbers, and descriptions, and contacts vendors—much like making that phone call to the tire shop—or uses financial systems like QuickBooks to send quotes and orders.
Now, envision an alternative. A company organizes all components—both off-the-shelf (OTS) and custom—in a centralized database using a service like OpenBOM. This collaborative platform allows data import from CAD designs, online catalogs, and manual entries. QR codes are automatically generated for traceability. Engineers access validated data during the design process, and quotes are prepared automatically. The receiving process is tracked using QR code scanners, closing the delivery loop. Order histories are saved for future analytics, and maintenance BOMs are created once the product is shipped. When customers need maintenance parts, they simply reference the specific maintenance BOM with the appropriate serial number.
Old Way vs. New Way: What is Next?
Do you see the difference between these approaches? The traditional method relies on familiar tools like Excel, allowing companies to maintain “business as usual.” The entire lifecycle is broken. This leads to mistakes, delays, and increased costs. How to organize a product’s lifecycle in connected digital form, and create a business strategy to change manufacturing companies? Resistance to change is natural; altering established processes is challenging. But it’s the responsibility of management to spearhead this transformation. Just as the tire shop lost a customer to a more digitally adept competitor, businesses clinging to outdated methods risk being outpaced by those embracing digital transformation.
Conclusion
The journey towards digital transformation is complex and requires organizational change. Even in companies with as few as 25 employees, leadership must have a vision to transition from disjointed folders and files to digital tools that streamline and organize processes. At OpenBOM, we specialize in consulting with companies to rethink their operations and adopt digital solutions that enhance efficiency and decision-making effectiveness.
Contact us, and we’ll be happy to help you navigate this crucial transformation.
Best, Oleg
OpenBOM CEO and co-founder
Join our newsletter to receive a weekly portion of news, articles, and tips about OpenBOM and our community.