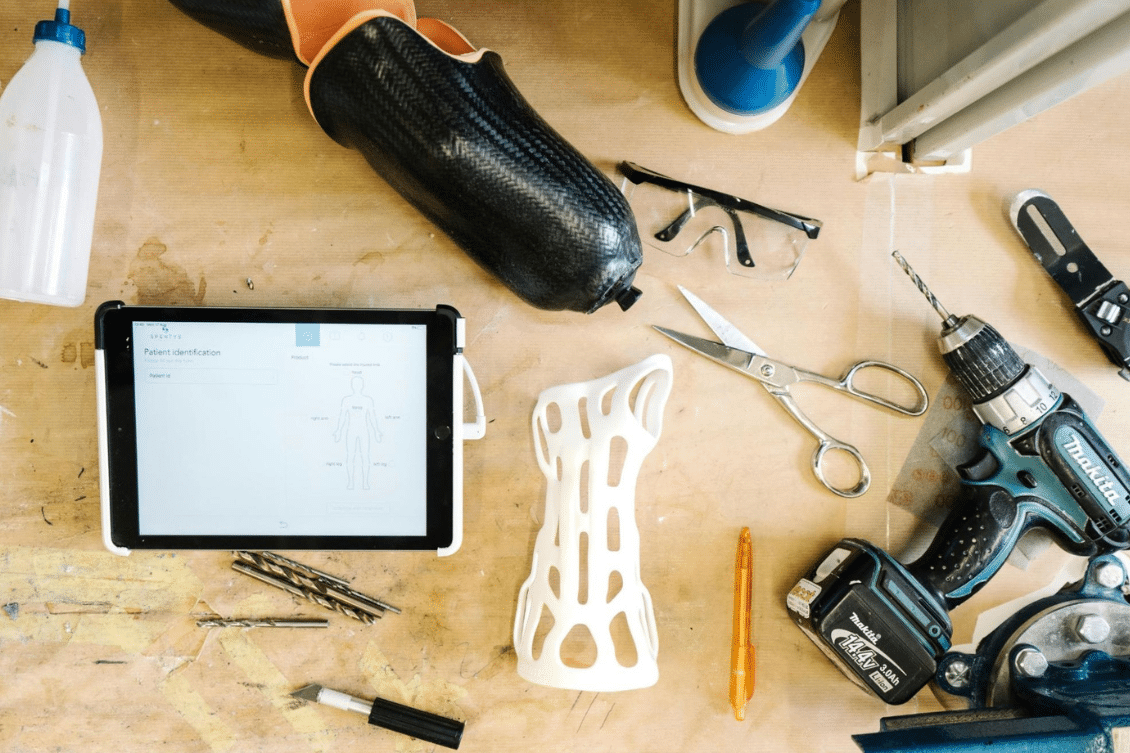
The transition from a prototype to full-scale mass production is a pivotal phase that demands planning, strategy, and execution. The significance of this transition cannot be overstated. For manufacturers, it represents the critical juncture where concepts are transformed into tangible products ready for the market. However, achieving this requires more than just technical prowess; it demands a comprehensive understanding of the challenges and opportunities inherent in scaling up production.
For manufacturers, a well-executed shift from prototype to mass production can spell the difference between success and failure. It not only determines the product’s viability in the market but also impacts crucial factors such as time-to-market, cost-effectiveness, and brand reputation.
Throughout this blog, we will highlight the difficulties of scaling for mass production, exploring key concepts, best practices, and practical strategies to guide manufacturers through this transformative journey.
Purposes of Prototyping
With prototypes, manufacturers can visualize, evaluate, and refine their product ideas before moving forward with mass production. Essentially, prototypes are early iterations or versions of a product that serve as a foundation for subsequent development stages.
The significance of prototypes in product development cannot be overstated. They provide invaluable insights into the feasibility, functionality, and performance of a product design, helping manufacturers identify strengths, weaknesses, and areas for improvement. By creating prototypes, manufacturers can validate their concepts, gather feedback from stakeholders, and make informed decisions that steer the product development process in the right direction.
Prototyping serves multiple purposes throughout the product development lifecycle, such as:
- Testing Functionality
- Refining Design
- Evaluating Market Viability
Common Challenges Faced During the Prototype Stage
Despite its importance, the prototype stage does have its challenges. Some common obstacles manufacturers may encounter include:
- Limited Resources
- Technical Complexity
- Iterative Nature
Despite these challenges, the prototype stage remains an essential phase in product development, serving as a crucial stepping stone towards achieving product excellence and market success. If executed correctly the prototype phase lays the foundation for successfully scaling up your product for production.
Evaluating Readiness for Mass Manufacturing
Before transitioning from prototype to mass manufacturing, it’s essential to assess the prototype’s readiness for large-scale production. During this phase, design for manufacturing (DFM) becomes important as it looks to optimize your product for production.
When evaluating whether or not a product is ready for production, you will need to evaluate multiple factors. These factors include:
- Product Design
- Materials
- Manufacturing Processes
- Cost Analysis
- Thorough Testing and Validation:
Before scaling up production, thorough testing and validation are essential to ensure that the prototype meets all quality and performance standards. Testing should encompass various aspects of the product, including functionality, durability, safety, and regulatory compliance. Any issues or deficiencies identified during testing should be addressed promptly through design modifications or process improvements.
Planning for Scale-Up
Transitioning from prototype to mass production requires meticulous strategic planning to ensure a smooth and successful process. Strategic planning lays the foundation for effectively scaling up production while minimizing risks and maximizing efficiency. By outlining clear objectives, identifying potential challenges, and developing actionable strategies, manufacturers can navigate the complexities of mass manufacturing with confidence and precision.
Some points to highlight when you are addressing the scale-up phase are the following:
- Production Capacity
- Supply Chain Management
- Quality Control
In addition, scaling up does not happen instantly, nor is it free. It’s important to establish clear timelines. Manufacturers should develop realistic timelines that account for all stages of production, from raw material procurement to finished product assembly, and incorporate buffers for unforeseen contingencies.
On the budget side, this plays a significant role in determining the financial feasibility of mass production. Manufacturers should develop comprehensive budgets that encompass all costs associated with scaling up production, including materials, labor, equipment, overhead, and contingencies. Budgets should be regularly monitored and adjusted as needed to maintain financial viability and control costs.
Streamlining Production Processes
Efficiency and scalability are crucial factors in the successful transition from prototype to mass production. Streamlining production processes involves optimizing workflows, reducing waste, and maximizing productivity.
When you are planning production nothing tends to go right the first time. Oftentimes bottlenecks can slow down a particular process that limits capacity. By analyzing workflow patterns and production data, manufacturers can pinpoint areas where production slows down or becomes inefficient and implement targeted solutions to alleviate bottlenecks.
One of the key tools used to streamline production and eliminate bottlenecks is lean manufacturing. Lean manufacturing principles focus on eliminating waste, improving efficiency, and maximizing value for customers. Techniques such as value stream mapping, and just-in-time production can help manufacturers identify and eliminate waste in their production processes.
As a result, you can expect the following benefits:
- Increased Productivity
- Cost Savings
- Enhanced Quality
Collaborating with Suppliers and Partners:
Collaboration with suppliers and manufacturing partners is indispensable for achieving success in transitioning from prototype to mass production. When evaluating contract manufacturers and suppliers, you will need to see how you can leverage them.
Collaboration with suppliers will instantly offer you access to their expertise and resources. Suppliers and manufacturing partners bring specialized expertise, resources, and capabilities to the table, enriching the production process with valuable insights and resources that may not be available in-house.
In addition, collaborative relationships enable manufacturers to leverage the strengths of their partners, increasing production efficiency, flexibility, and responsiveness to market demands. By working together seamlessly, manufacturers and partners can adapt quickly to changing requirements and optimize production processes for better outcomes.
Selecting reliable suppliers and establishing strong partnerships are crucial steps in the collaboration process.
During due diligence, you can evaluate potential suppliers based on criteria such as reputation, reliability, quality standards, and financial stability. You can also verify references, assess capabilities, and conduct site visits to ensure alignment with your production requirements.
Open collaboration with your supplier is effective for
- Building Trust
- Finding Quick Solutions
- Increased Speed to Market
Overcoming Challenges and Pitfalls
Transitioning from prototype to mass manufacturing presents manufacturers with several challenges and pitfalls that must be navigated effectively to ensure a successful outcome. During the production phase, there will be many challenges, such as production delays, quality issues, increased costs, and more.
While these challenges do come up, it is important how you solve these challenges and the speed at which you solve them. Here are 4 ways you can solve these challenges:
Risk Assessment and Mitigation
Conduct a thorough risk assessment to identify potential challenges and develop mitigation strategies. Anticipate potential risks such as supply chain disruptions, production bottlenecks, or quality issues, and implement proactive measures to address them.
Robust Quality Control
Implement robust quality control measures throughout the production process to detect and prevent defects. Utilize techniques such as statistical process control, inspections, and testing to ensure product quality meets or exceeds standards.
Supply Chain Diversification
Diversify your supply chain to reduce dependency on a single source or supplier. Establish relationships with multiple suppliers for critical components or materials to mitigate the risk of supply chain disruptions.
Continuous Improvement
Embrace a culture of continuous improvement to drive efficiency, innovation, and excellence in production. Encourage feedback from employees, suppliers, and customers, and implement process improvements based on insights and lessons learned.
Ensuring Quality and Consistency
Maintaining quality and consistency is paramount in mass production to uphold customer satisfaction, brand reputation, and long-term success. First, quality is important, if you have poor quality then your customer satisfaction will decrease, your brand will have a poor reputation, and your costs will increase.
Quality assurance measures play a crucial role in ensuring that products meet predefined quality standards and specifications. Establishing comprehensive testing protocols to evaluate product quality and performance at various stages of production. This may include functional testing, durability testing, safety testing, and compliance testing to ensure adherence to regulatory requirements.
You should also conduct regular inspections and audits to monitor production processes and identify deviations from quality standards. Implement quality control checkpoints to detect defects or non-conformities early and take corrective action promptly.
Lastly, work closely with suppliers to ensure the quality of incoming materials and components. Establish quality agreements, conduct supplier audits, and provide feedback to suppliers to maintain consistency in material quality and performance.
Conclusion:
As manufacturers embark on the journey of scaling up production, it’s imperative to adopt strategic approaches and best practices. By leveraging careful planning, collaboration, and continuous improvement, manufacturers can overcome challenges, mitigate risks, and optimize production processes for success. Embracing strategic thinking and proactive decision-making empowers manufacturers to navigate complexities and uncertainties with confidence, paving the way for sustainable growth and excellence in mass manufacturing endeavors.
The transition from prototype to mass production is a pivotal phase in the product development lifecycle, demanding diligence, foresight, and resilience from manufacturers. By embracing strategic approaches, fostering collaboration, and prioritizing quality and efficiency, manufacturers can navigate this transition effectively and unlock the full potential of their products in the marketplace. Here’s to a future filled with innovation, success, and impactful contributions to the world of mass manufacturing.
Interested in OpenBOM? Register for free and start the free 14-day trial.
Regards,
Jared Haw
Join our newsletter to receive a weekly portion of news, articles, and tips about OpenBOM and our community.