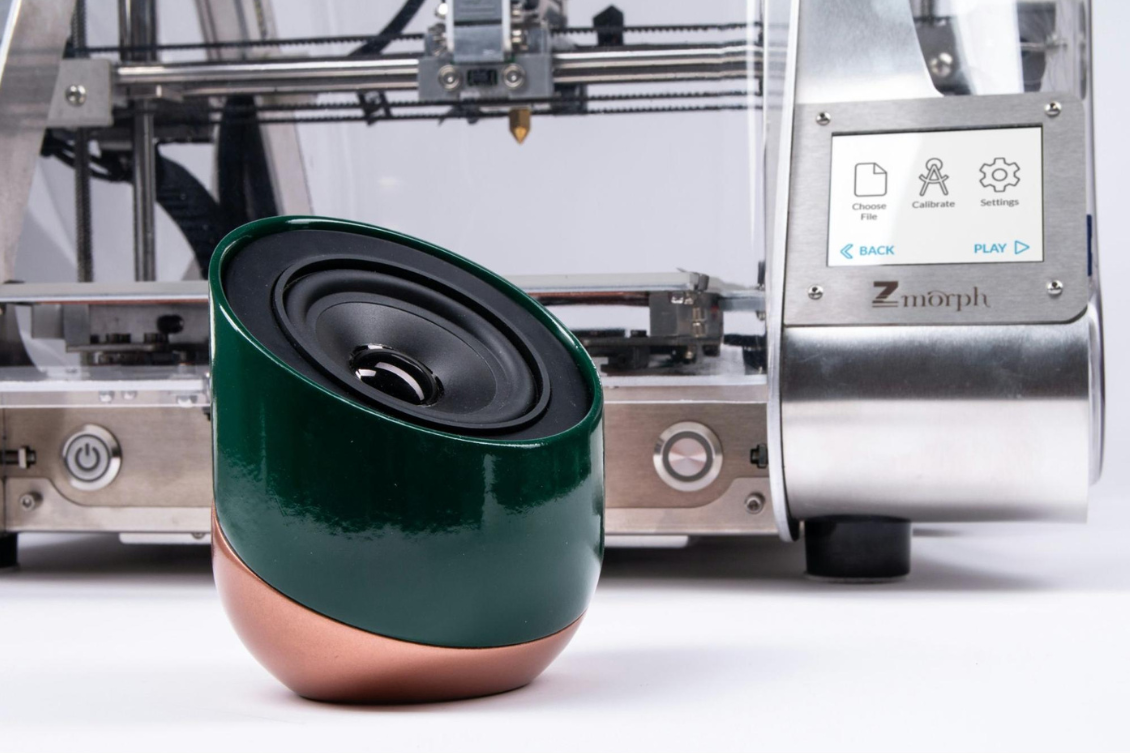
Transitioning from a prototype to full-scale production is one of the most critical phases in product development. While creating a functional prototype is an essential first step, ensuring that this prototype can be efficiently and reliably manufactured at scale is where many challenges arise. The shift from a one-off creation to a reproducible, cost-effective product often uncovers design flaws, material constraints, and production inefficiencies that weren’t apparent during the prototyping phase.
This is where thoughtful planning and adherence to proven best practices come into play. Moving from prototype to production requires not only design adjustments but also close collaboration with suppliers, a focus on manufacturability, and rigorous testing to ensure the final product meets quality standards. Without careful preparation, manufacturers risk delays, costly rework, and production failures that can undermine even the most promising designs.
In this blog, we’ll explore three essential best practices that can help manufacturers navigate this transition smoothly. Let’s take a closer look at how you can streamline the journey from prototype to production.
Design for Manufacturing (DFM)
The transition from prototype to production often reveals hidden complexities in the design that weren’t apparent during the initial development. This is where Design for Manufacturing (DFM) comes in, a critical step in ensuring that your product is not only functional but also optimized for efficient production at scale.
DFM is about designing with the realities of manufacturing in mind. It’s easy to overlook factors like material selection, ease of assembly, and the limitations of manufacturing processes when you’re focused on building a prototype. However, these considerations are key to avoiding costly production delays and minimizing waste.
For example, a part that was CNC’d or 3D printed during prototyping may need significant redesigning to be injection-molded cost-effectively at scale. Similarly, a complex assembly that worked well in a one-off prototype might be difficult to replicate consistently in a production environment, leading to higher failure rates and increased labor costs.
To optimize your prototype for production, you should evaluate each component with DFM principles in mind. Start by simplifying the design wherever possible. Fewer parts typically mean fewer opportunities for failure during production. Additionally, consider the capabilities and constraints of your manufacturing processes. For example, certain materials might work well in prototyping but may not be suitable for high-volume production due to cost, durability, or manufacturing limitations.
Incorporating DFM principles early in the design phase helps you identify potential production bottlenecks and reduce unnecessary complexity before your design reaches the factory floor. It’s not just about getting the prototype to work—it’s about ensuring that the design can be scaled efficiently without sacrificing quality. By optimizing your designs for manufacturability, you’ll improve production speed, lower costs, and increase the overall success rate of your products.
Choose Your Suppliers Early
Selecting the right suppliers is one of the most critical decisions you’ll make when transitioning from prototype to production. The supplier you choose will directly impact your production timeline, quality, and costs, so waiting until the last minute to engage them can be a costly mistake.
Involve your suppliers early in the prototyping phase, even before you’ve finalized your design. Establishing strong relationships with them early on allows you to tap into their expertise—whether it’s in material selection, manufacturability, or logistics. Suppliers can offer insights into the production capabilities, lead times, and cost implications that might not be obvious during the initial design phase.
Engaging suppliers early also allows you to ensure that the materials, components, or processes used in the prototype are scalable for mass production. A material that’s easy to source in small quantities might not be feasible or cost-effective at scale, and some processes might not be repeatable in a high-volume production environment. By understanding your supplier’s limitations and capabilities upfront, you can adjust your designs to avoid future headaches.
Treat your suppliers as partners, not just vendors. Regular communication, transparency, and collaboration with them will allow you to proactively address potential challenges rather than reactively dealing with them during production. A good supplier who understands your long-term vision will be better equipped to meet your growing demands and ensure your production process runs smoothly. The earlier you solidify these relationships, the more leverage and flexibility you’ll have when scaling up.
Test, Test, and Test Again
Testing might seem like an obvious step, but its importance can’t be overstated when transitioning from prototype to production. This phase is where you move beyond simply proving that your prototype works; it’s about validating that your design, materials, and processes can reliably perform under real-world conditions—time and time again.
Before you scale up production, subject your prototype to rigorous testing. This means running it through stress tests, environmental tests, durability checks, and anything else relevant to your product’s use case. The goal is to expose any weaknesses or inconsistencies that could arise during mass production. It’s better to discover a flaw when you’re still tweaking the design than after you’ve already committed to full-scale production.
Testing shouldn’t stop at the prototype stage either. Each iteration of your product—whether it’s a small design adjustment or a new batch of materials—should be thoroughly tested to ensure it meets both your specifications and customer expectations. Neglecting this step can lead to costly recalls, customer dissatisfaction, and brand damage.
Document everything! Every test, every outcome, every adjustment. This isn’t just about covering your bases—keeping a detailed record helps you track changes, identify patterns, and streamline future production runs. Plus, it provides valuable insights into which design elements are working well and which need further refinement. Regular and systematic testing ensures that when the time comes to scale up, you’ll be confident that your product is ready for production and market success.
Conclusion
Taking a product from prototype to full-scale production is a complex journey that requires careful planning, collaboration, and a proactive approach. By adhering to the best practices of clear communication, optimizing your designs with Design for Manufacturing (DFM) principles, and involving your suppliers early, you can avoid common pitfalls that derail production timelines and inflate costs.
The importance of rigorous testing cannot be overstated—testing repeatedly and thoroughly ensures that your product can handle the realities of manufacturing and the demands of the market. When issues are caught and resolved during the early stages, you save time, money, and resources while delivering a better product to your customers.
Ultimately, transitioning from prototype to production is about building a strong foundation for scalability, quality, and efficiency. By following these practices, manufacturers can streamline this critical phase, reduce the risk of costly errors, and set themselves up for long-term success in production.
By: Jared Haw
Join our newsletter to receive a weekly portion of news, articles, and tips about OpenBOM and our community.