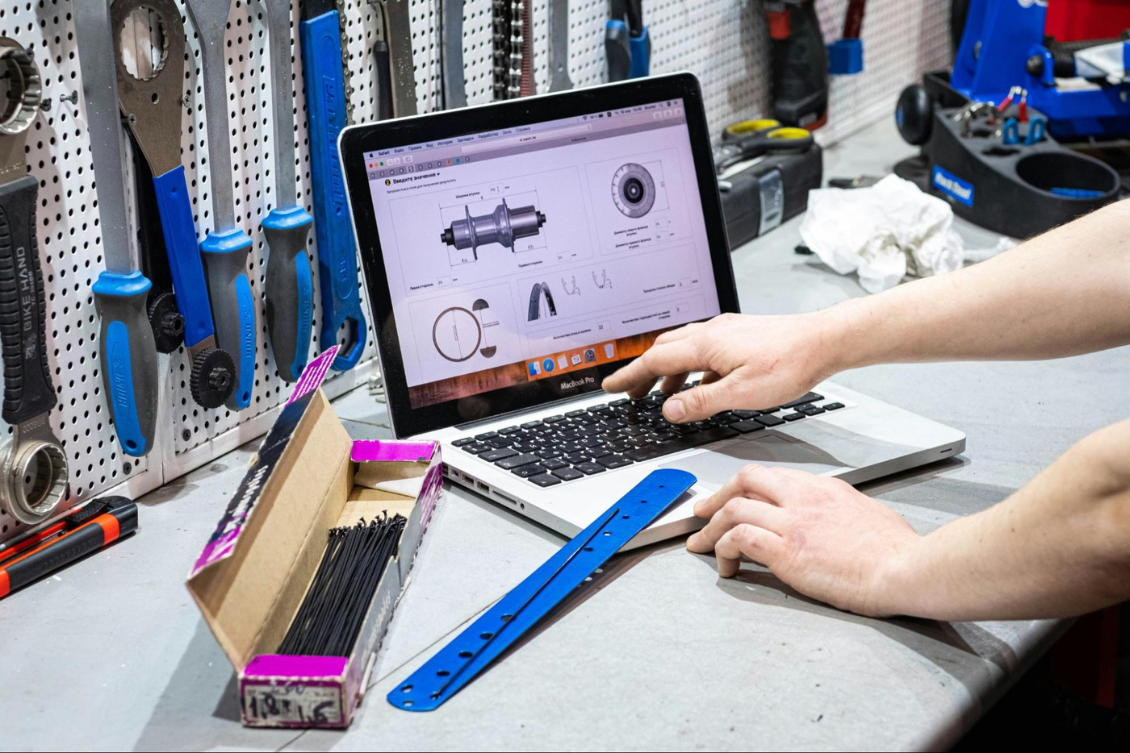
In today’s manufacturing landscape, effective collaboration between manufacturers and suppliers is more critical than ever. From sourcing materials to meeting tight production deadlines, the success of any manufacturing project often hinges on seamless communication. A breakdown in this collaboration can lead to costly errors, production delays, and even missed opportunities.
At the heart of this collaboration is the Bill of Materials (BOM), a vital document that outlines all the components, materials, and specifications needed for production. Traditionally, BOMs have been managed using static documents like Excel, which can lead to miscommunication, outdated information, and errors. As manufacturing becomes more complex, relying on these outdated methods is no longer sufficient.
This is where digital BOMs come in. By providing a dynamic, real-time solution, digital BOMs improve communication and streamline collaboration, ensuring that suppliers and manufacturers are always on the same page. In this blog, we’ll explore how a digital BOM enhances supplier collaboration, leading to smoother operations and more efficient production processes.
What is a Digital BOM?
A digital Bill of Materials (BOM) is an electronic version of the traditional BOM, designed to offer far more flexibility, accuracy, and efficiency. Unlike static paper-based or Excel-based BOMs, which can quickly become outdated or cumbersome, a digital BOM is dynamic and easily accessible across teams in real-time.
At its core, a BOM serves as a comprehensive list of all the materials, parts, and components required to manufacture a product. It’s an essential document for both manufacturers and suppliers, detailing everything from the type of material to the finish, and everything else that is critical for that part or component. In digital form, the BOM takes on new capabilities, allowing for better data management, instant updates, and seamless collaboration across various stakeholders.
With a digital BOM, manufacturers and suppliers can:
- Access the latest information anytime and anywhere, ensuring everyone works from the same, up-to-date data.
- Track revisions and changes automatically, avoiding confusion about which version is correct.
- Integrate with other systems such as ERP, CAD, and PLM, creating a central hub of accurate product information.
This shift from Excel to a digital BOM offers more than just convenience, it fundamentally improves how suppliers and manufacturers communicate, reducing errors and improving efficiency throughout the supply chain.
Improved Accuracy and Reduced Errors
One of the biggest advantages of using a digital BOM is the significant improvement in accuracy, which directly reduces errors throughout the manufacturing process. Traditional BOMs, whether in paper format or managed through Excel, are prone to human error. These documents can become outdated, misinterpreted, or contain mistakes that lead to costly consequences—such as incorrect orders, delayed production, or even defective products.
A digital BOM addresses these issues by providing:
- Real-time updates: When changes are made to the design or materials, the digital BOM is instantly updated, ensuring that suppliers always have the most current information. This eliminates the risk of suppliers working from outdated versions of the BOM.
- Centralized data: All teams, whether in engineering, procurement, or production can access a single, unified source of truth. This reduces the chance of miscommunication and prevents errors that can arise from using different versions of the same document.
By improving the accuracy of the BOM, manufacturers, and suppliers can avoid many of the costly mistakes that plague traditional BOM management. This not only saves time and money but also strengthens the relationship between both parties, ensuring smoother collaboration and more reliable production outcomes.
Enhanced Communication and Transparency
A digital BOM is more than just a technical tool, it’s a powerful way to enhance communication and transparency between manufacturers and suppliers. One of the biggest challenges in traditional supplier relationships is ensuring that everyone is working from the same information. A BOM managed in Excel, can lead to confusion, especially when changes are made and the updated version isn’t shared with all relevant stakeholders.
A digital BOM solves this problem by offering a shared, single source of truth that is accessible to both manufacturers and suppliers in real-time. This centralization of information fosters clearer communication by ensuring that every team, regardless of location, has access to the same, up-to-date data. Misunderstandings, which often result from working off old or incorrect information, are drastically reduced.
With a digital BOM, tracking changes, material requirements, and specifications become much easier:
- Change tracking: Any updates to the design, materials, or part specifications are instantly reflected in the digital BOM. Both manufacturers and suppliers can see these changes in real-time, reducing the risk of errors and ensuring the correct parts are ordered and produced.
- Material requirements: Suppliers have full visibility into the detailed material lists, making it easier to manage inventory, provide accurate quotes, and ensure timely delivery of components.
- Specification clarity: All technical specifications are clearly laid out and instantly accessible, reducing the back-and-forth communication that can delay projects or lead to mistakes.
This transparency builds trust between manufacturers and suppliers, as both parties can confidently rely on the accuracy of the information. In turn, it leads to more efficient production, faster decision-making, and a stronger collaborative relationship.
Enhanced Communication and Transparency
A digital BOM plays a crucial role in improving communication and transparency between manufacturers and suppliers. Traditional BOMs, often scattered across emails or spreadsheets, can easily lead to miscommunication, as different teams may be working from different versions of the document. This can cause delays, mistakes, and frustration for both manufacturers and suppliers.
With a digital BOM, these issues are eliminated by providing a shared, single source of truth. Both manufacturers and suppliers have access to the same up-to-date information at all times, ensuring everyone is aligned on the latest product specifications, material requirements, and changes. This transparency helps eliminate confusion, miscommunication, and the potential for errors.
Key benefits of digital BOMs for communication and transparency include:
- Real-time change tracking: When design modifications or material substitutions occur, these updates are instantly reflected in the digital BOM. Suppliers can see changes as they happen, ensuring they’re always working with the latest information. This reduces the need for constant follow-up emails and prevents costly mistakes from outdated data.
- Clear material requirements: With a digital BOM, suppliers can easily view the complete list of required materials, along with detailed specifications. This not only speeds up the procurement process but also ensures that the right materials are ordered the first time, minimizing delays and miscommunications.
- Easy specification management: Digital BOMs allow manufacturers to include precise technical specifications for every part or component. Suppliers can easily refer to these specs, avoiding misinterpretations or assumptions that often happen with manual BOMs.
By streamlining communication and offering full transparency, a digital BOM helps manufacturers and suppliers collaborate more effectively, leading to faster production cycles, fewer errors, and a more trusted partnership.
Streamlined Procurement and Quotation Processes
A digital BOM simplifies the procurement process by providing suppliers with clear, accurate, and complete information. In traditional procurement workflows, suppliers often rely on scattered data from multiple documents, which can lead to confusion, delays, or incomplete quotes. A digital BOM addresses these issues by offering a centralized, easily accessible source of truth for all material and component details.
Here’s how a digital BOM streamlines procurement and quotations:
- Clarity and Completeness: With a digital BOM, suppliers receive a fully detailed list of materials, quantities, and specifications in one place. This ensures that they have all the necessary information upfront, reducing the need for follow-up questions or additional clarification. By having a complete view of the product’s requirements, suppliers can confidently begin the procurement process without delays.
- Improved Speed: Digital BOMs enable suppliers to quickly generate accurate quotes. Since all the data is up-to-date and easily accessible, there’s no need to manually cross-reference different files or track down missing details. This speeds up the quoting process, allowing suppliers to respond faster to requests and manufacturers to get the materials they need in less time.
- Increased Accuracy: Manual BOMs are prone to errors that can result in inaccurate quotes or incorrect material orders. A digital BOM eliminates these risks by automatically tracking any updates or revisions. This ensures that suppliers are always quoting based on the most current information, leading to more accurate pricing and fewer procurement issues.
- Automated Integration: Many digital BOM systems integrate seamlessly with procurement and inventory management platforms, allowing suppliers to streamline the entire purchasing process. This connectivity eliminates manual entry errors and helps suppliers quickly generate quotes, check stock levels, and place orders efficiently.
By using a digital BOM, manufacturers and suppliers can avoid the common pitfalls of traditional procurement, resulting in faster, more accurate quotations and a smoother overall process. This efficiency not only reduces costs but also strengthens the supplier-manufacturer relationship through better communication and trust.
Conclusion: Embracing the Future of Supplier Collaboration
In today’s competitive manufacturing environment, efficient collaboration between manufacturers and suppliers is crucial to success. A digital BOM serves a tool that not only enhances communication but also improves accuracy, transparency, and efficiency across the entire supply chain. By offering a single source of truth, suppliers and manufacturers can work together seamlessly, minimizing errors and reducing delays.
The benefits of a digital BOM are clear: it streamlines procurement, speeds up the quotation process, and ensures that everyone is aligned on the most current information. This leads to faster decision-making, more accurate orders, and a more reliable production process—ultimately strengthening the partnership between suppliers and manufacturers.
As manufacturing continues to evolve, embracing digital tools like a digital BOM is no longer optional, it’s essential for staying ahead. If you’re looking to improve supplier collaboration and optimize your production processes, now is the time to transition to a digital BOM solution. Start today and see how it can transform your business.
By: Jared Haw
Join our newsletter to receive a weekly portion of news, articles, and tips about OpenBOM and our community.