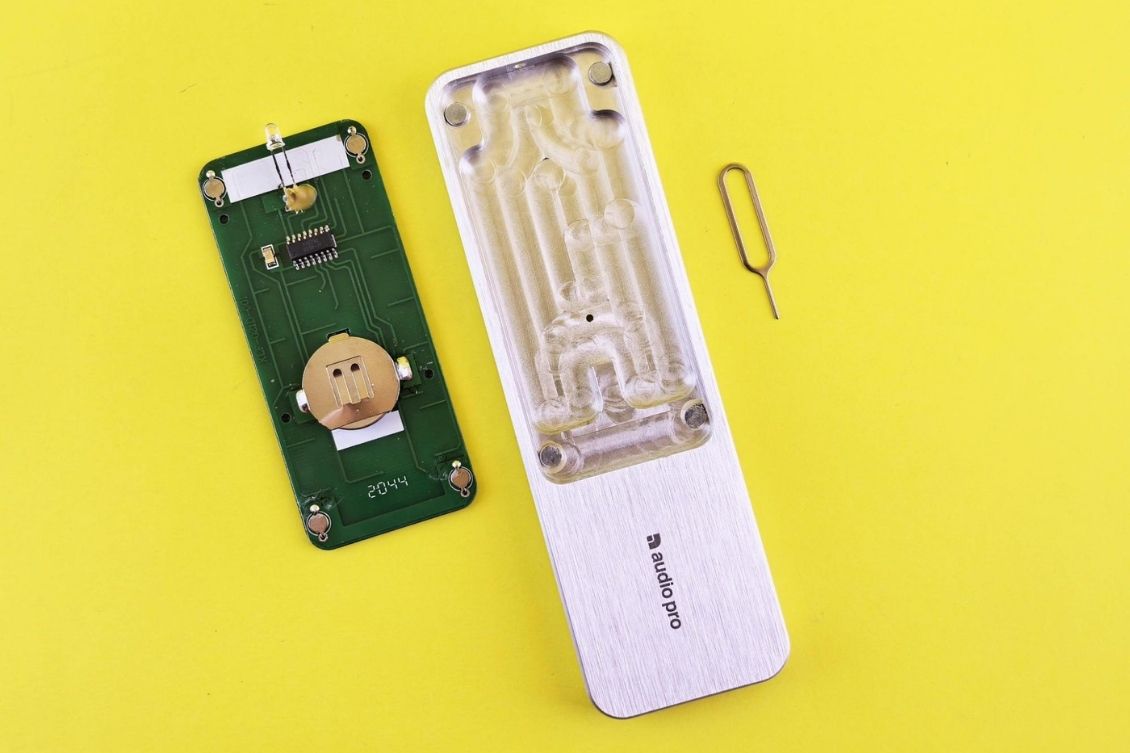
Bringing a product from design to production is a complex process that requires careful coordination between engineering, procurement, and manufacturing teams. At the center of this process is the Bill of Materials (BOM), a critical document that defines the components, materials, and assemblies needed to build your product. However, how you manage your BOM can make or break your transition from prototype to full-scale production.
Many companies still rely on Excel spreadsheets to manage their BOMs. While this might seem manageable in the early design stages, it quickly becomes a bottleneck as the product evolves. Version control issues, manual errors, and miscommunication between teams lead to costly mistakes, delays, and supply chain disruptions.
A digital BOM offers a modern, structured approach to managing product data throughout the entire lifecycle. Unlike spreadsheets, a digital BOM provides real-time collaboration, automated updates, and seamless integration with CAD and other business tools, ensuring that your team works from the latest information.
In this blog, we’ll explore how a digital BOM supports you in the journey from design to production. Whether you’re a startup refining a prototype or a manufacturer scaling up production, adopting a digital BOM will help you streamline workflows, reduce risks, and accelerate time to market.
How a Digital BOM Supports Every Stage of the Process
The transition from design to production isn’t a single-step process, it involves multiple phases, each requiring accurate, up-to-date BOM. A digital BOM ensures that design engineers, procurement teams, and manufacturing personnel are all working with the most current information.
Unlike Excel, which can lead to version mismatches, miscommunication, and ordering errors, a digital BOM dynamically evolves as your product moves from early-stage prototyping to mass production. It helps capture design changes, improve supplier collaboration, and eliminate costly mistakes that often arise from manual processes.
Let’s take a closer look at how a digital BOM supports every stage of the journey, from design and validation to procurement and production.
Design & Prototyping
The design and prototyping phase is where ideas start to turn into products. It’s an iterative process that involves frequent changes, testing, and refinements, making BOM management crucial. A well-structured digital BOM ensures that early-stage designs remain organized, up-to-date, and accessible to all team members.
Many people ask, do I need a digital BOM for prototypes? Here is why you do:
Stop Losing BOM Data During Prototypes
- In the early design stages, engineers create initial BOMs that may include placeholders for materials, components, and subsystems.
- A digital BOM allows teams to build these early BOM structures without manually tracking every change in scattered spreadsheets.
- Engineers can easily modify and update part numbers, quantities, and specifications as they refine the prototype.
Integration with CAD for Real-Time Accuracy
- A digital BOM can directly connect with CAD tools (like SolidWorks, Fusion 360, Altium, and more), automatically create part numbers, and pull in materials, and other critical design data.
- This eliminates manual data entry, reducing the risk of typos, incorrect part numbers, or missing components in the BOM.
- When a design is updated in the CAD system, the BOM automatically reflects those changes, ensuring consistency across engineering and manufacturing teams.
Early Collaboration Between Engineering and Manufacturing
- A common issue in product development is the disconnect between design and manufacturing teams, leading to production delays or costly redesigns.
- A digital BOM ensures that manufacturers and suppliers gain early visibility into the evolving design, allowing them to provide feedback on manufacturability, cost, and lead times.
- Teams can flag sourcing issues or potential manufacturing challenges before finalizing the design, avoiding costly last-minute changes.
With a digital BOM, the entire prototyping process becomes more efficient—ensuring that design changes are accurately tracked, manufacturing feedback is incorporated early, and teams work with real-time, error-free data.
Engineering & Validation
Once a prototype is developed, it must undergo validation testing to ensure the product functions correctly, meets quality standards, and is ready for production. This phase includes extensive testing, part selection refinement, and supplier collaboration to prepare for scaling up manufacturing.
A digital BOM plays a critical role in this phase by ensuring that teams work with the most accurate, up-to-date data across multiple validation stages. It helps track design iterations, manage part substitutions, and streamline supplier interactions—all while maintaining a single source of truth for the entire organization.
Let’s break down how a digital BOM supports the different stages of validation – EVT, DVT and PVT:
Ensuring Up-to-Date Data for Engineering Validation
During the Engineering Validation Testing (EVT) phase, the design is put through functional testing to ensure it meets performance requirements. Any changes or failures at this stage require BOM updates.
- A digital BOM ensures all stakeholders are working with the latest component data, reducing the risk of engineers testing outdated components.
- Engineers can attach specifications, test results, and compliance documents directly to the BOM, ensuring that product requirements are met.
- Integration with CAD and PLM systems ensures that any component changes in design are instantly reflected in the BOM.
Managing Changes During the Design Process
As the product moves from EVT to Design Validation Testing (DVT), design refinements become even more critical. Material selections, tolerances, and supplier feedback may require part substitutions to improve reliability and manufacturability.
A digital BOM simplifies part substitutions by:
- Providing a structured way to manage approved alternates for each component.
- Allowing procurement teams to identify cost-effective or more readily available substitutes.
- Ensuring that any replacements don’t impact performance or regulatory compliance.
Collaborating with Suppliers Early to Avoid Production Delays
By the time a product reaches Production Validation Testing (PVT), it should be nearly production-ready. However, last-minute supplier issues can still arise, causing delays or unexpected costs.
A digital BOM facilitates early supplier collaboration by:
- Allowing manufacturers to review and comment on BOM components before production.
- Automatically generating structured RFQs (Requests for Quotation) based on the BOM.
- Tracking supplier lead times, availability, and pricing in real-time.
By leveraging a digital BOM, companies can streamline the EVT, DVT, and PVT phases, ensuring a faster, smoother transition from engineering validation to full-scale production.
Production & Scaling Up
After the parts have been validated and you have sourced the right supplier, the next critical stage is moving from small-batch production to full-scale manufacturing. This transition requires tight coordination between engineering, production, and quality control to ensure that products are built correctly, efficiently, and at scale. A digital BOM plays a crucial role in maintaining consistency, reducing errors, and optimizing production workflows.
On the other hand, relying on Excel BOMs at this stage creates serious risks, including outdated information, version control issues, and manual errors. A digital BOM provides a single source of truth that keeps engineering, manufacturing, and suppliers in sync—ensuring production runs smoothly from the first unit to mass production.
Ensuring Manufacturing Readiness
Before ramping up production, manufacturers must validate that every component, process, and assembly step is ready for large-scale manufacturing. A digital BOM provides manufacturing teams with real-time access to the latest, approved product data, preventing costly miscommunication and errors.
For example, if an engineer updates a fastener specification, the digital BOM instantly reflects the change across all teams, ensuring that manufacturing orders the correct part and avoids rework. Without a digital BOM, these changes often get lost in email threads or outdated spreadsheets, leading to production delays.
Standardizing Work Instructions & Assembly Processes
A structured, well-documented BOM is essential for standardizing assembly instructions and ensuring product quality. Unlike Excel, a digital BOM can link to detailed assembly instructions, CAD drawings, and work procedures, allowing production teams to access the correct build information in real-time.
This is especially critical when scaling up, as misaligned production instructions can lead to defects, inconsistencies, and increased scrap rates. By using a digital BOM, manufacturers can provide clear, up-to-date work instructions to assembly teams, minimizing errors and ensuring consistent product quality across multiple production runs.
Managing Changes Without Disrupting Production
Even after production begins, engineering change orders (ECOs) are inevitable. If these changes are not properly communicated, manufacturers risk producing outdated or defective products.
A digital BOM integrates with change management workflows, ensuring that any updates—whether to part specifications, suppliers, or assembly processes—are instantly reflected in production. This prevents scenarios where manufacturing unknowingly builds with obsolete parts, reducing costly scrap and rework.
Conclusion
Transitioning a product from design to full-scale production is a multi-step process that requires collaboration across engineering, procurement, and manufacturing teams. Relying on Excel BOMs creates serious risks, miscommunication, outdated data, version control issues, and costly production errors. A digital BOM eliminates these challenges by ensuring that every on your team has real-time access to the latest product data, enabling a smooth, efficient, and error-free production process.
As companies scale from prototypes to mass production, the importance of efficient BOM management only increases. A digital BOM helps manufacturers maintain quality, reduce costs, and adapt quickly to design changes, giving them a competitive edge in fast-moving industries.
If you’re still using Excel to manage your BOMs, it’s time to rethink your approach. Investing in a digital BOM will streamline your entire product lifecycle, helping you bring better products to market.
By: Jared Haw
Join our newsletter to receive a weekly portion of news, articles, and tips about OpenBOM and our community.