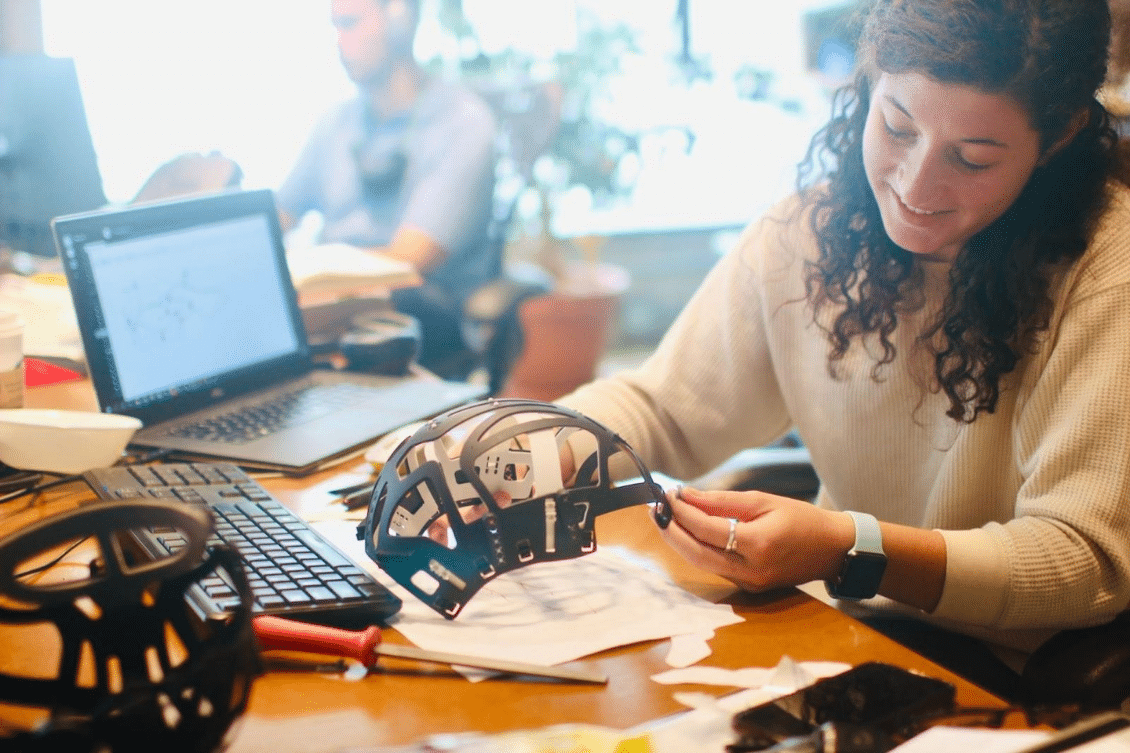
Manufacturers are tasked with developing and bringing to market products quicker than ever. Doing this internally, without the help of contractors and suppliers is nearly impossible to do. Therefore, manufacturers are looking for partners they can leverage to achieve this goal. One of the partners that manufacturers leverage is the one with their supplier or contract manufacturer (CM).
The reason the partnership between the manufacturer and the supplier is so close is that the supplier usually has the resources and knowledge that the manufacturer lacks. This is usually taking the product from the prototype stage all the way through mass production.
During the new product introduction (NPI), there are several steps, such as design, prototyping, testing, and production. Accomplishing the goals of each step and transitioning to the next step is challenging. The supplier you evaluate and choose to work with should have the engineers, supply chain, network, and production lines to navigate these steps.
How Your Supplier Helps with NPI Roadblocks
There are several roadblocks that hinder you from a successful product launch. Having a CM who is able to transition you from the development steps to manufacturing will be highly valuable.
Transitioning from Prototypes to Production
Creating prototypes is an important step in the development process They are used to show investors, executives, key accounts, and to create a crowdfunding page.
However, just because you have this nice-looking prototype does not mean that you can replicate it during production. The tools, fabrication methods, and materials are all different. So how do you take this prototype and transition it into something that can be made in mass production?
If you are working with a CM then one of their biggest assets at this moment is to help you move from prototypes to production. This stage is usually referred to as design for manufacturing (DFM). During this stage, your CM will be looking at how they can optimize every part, and assembly for production. They will also look at ways to bring the cost down, improve the quality, and more.
Increased Costs
A common trend is that manufacturers want the highest quality but are not prepared to pay for this quality. Having a team that does not understand materials and production processes will always end up with the highest costs.
However, if you are working with a CM then they will have a strong understanding of the materials and production processes that work best for your product. They will be able to create change requests for material changes and process changes.
Quality Issues
One of the biggest parts that hold manufacturers back is quality problems. Unfortunately, quality problems can come from multiple paths. The biggest path is that the product was not designed correctly. Or it was designed for prototypes but not mass production, leading to a high defect rate in production.
Optimizing the design does not just decrease the price of the product, but it also improves the quality at the same time. Having a CM who understands the quality advantages and disadvantages of certain processes and materials will improve the value of the product.
With their knowledge and expertise, you can transition a product with quality problems into a product that can be produced with minimal quality defects.
The Importance of Managing Data
During all of these development steps, you need to create and manage certain data about your product. This is especially important during the early stages because of how many changes are happening and how quickly you are developing your product. Losing and not correctly capturing this data will lead to building incorrect prototypes or not fully knowing what you actually built.
Sadly, it happens a lot. You purchase a part for a prototype but never add it to the BOM so you need to go through some old emails to find what you used.
While managing your data is important during the early phases, it also helps you to quickly navigate to the next development step. For example, if you are not properly managing data during the prototype stage then how are you expected to quickly navigate to production? You can’t.
Also, the way you share your product data with your supplier is important. Sending excels and emailing CAD files will create data silos. As a result, your supplier will have their own product data and you will have something separate.
Creating a single source of truth will open the lines of collaboration. With this single source of truth, all of the product, engineering, manufacturing, design, and CAD data will be stored and managed together.
Setting up this platform will allow your supplier to provide quick value by accomplishing the following:
- Instant access to all data
- Setting workflows to approve change requests
- Capture all revisions during the development process
- Manage the quantity of each component and part during prototype builds.
The way you manage your product data is a fundamental part of how your supplier can help support you through NPI.
How to Start the Process Now?
The first step in order for your supplier to help you with the NPI process is to provide them with the tools in order to succeed. One of the biggest trends in manufacturing is transitioning to the cloud and starting your digital transformation journey.
OpenBOM is a cloud-based PDM & PLM platform to manage your engineering and manufacturing data. Companies from startups to Fortune 500’s use OpenBOM to create a centralized database to bring in, store, and manage their manufacturing data. With this infrastructure, users also use OpenBOM to streamline both their change management and PO processes.
If you need to improve the way you manage your data and processes, contact us today for a free consultation.
Regards,
Jared Haw
Join our newsletter to receive a weekly portion of news, articles, and tips about OpenBOM and our community.