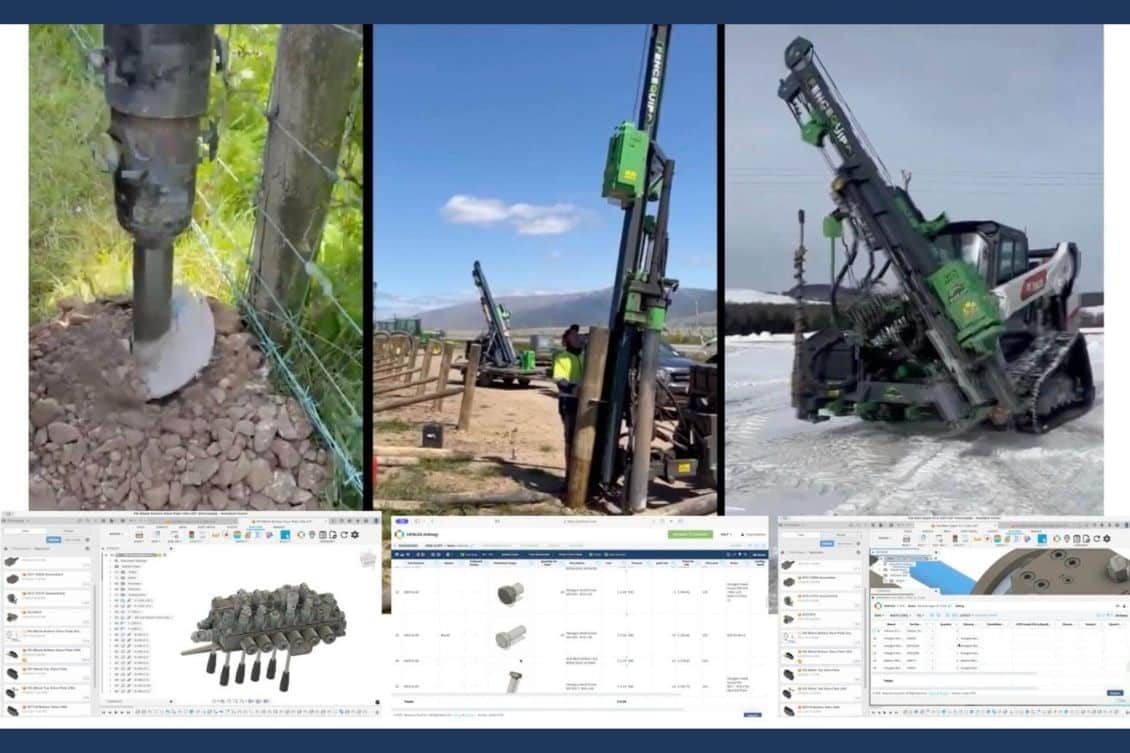
In today’s fast-moving manufacturing environment, efficiency is everything. Companies must ensure that their engineering and procurement teams work together seamlessly to avoid waste, control costs, and streamline production. FENCEQUIP, a New Zealand innovator and manufacturer of FENCEQUIP Post Drivers, recognized the need to modernize its approach and adopted OpenBOM to connect engineering design with ordering and purchasing optimization.
By integrating OpenBOM, FENCEQUIP has successfully bridged the gap between CAD design and procurement, achieving a smoother and more cost-effective workflow. This transformation allows them to move faster from design to manufacturing while ensuring their purchasing decisions are well-informed and optimized for cost and efficiency.
From Design to Procurement: The Challenge
Like many manufacturers, FENCEQUIP faced difficulties in keeping engineering and purchasing aligned. While their Autodesk Fusion 360 CAD system enabled advanced design work, transferring that data into procurement was not straightforward. Manually managing Bill of Materials (BOMs), tracking changes, and ensuring that purchasing decisions were made based on accurate, up-to-date information was a constant challenge.
Another key issue was cost assessment. Without a clear view of material costs early in the design phase, it was difficult to make cost-conscious decisions before committing to production. Additionally, purchasing inefficiencies—such as over-ordering, duplicate purchases, and supplier misalignment—were increasing operational costs and making inventory management more complex.
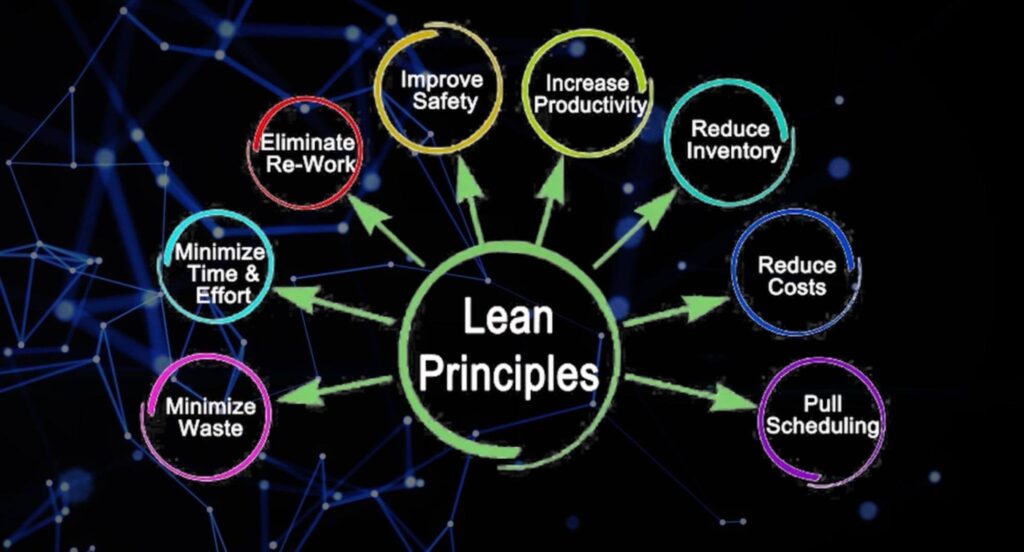
FENCEQUIP needed a modern, flexible solution that could connect engineering design directly with purchasing and ensure the right parts were ordered in the right quantity, at the right time, from the right suppliers.
The OpenBOM Solution: Lean, Connected, and Efficient
FENCEQUIP turned to OpenBOM to implement a lean manufacturing approach that eliminates inefficiencies and enhances procurement accuracy. OpenBOM’s seamless integration with Autodesk Fusion 360 ensures that engineering data flows directly into purchasing without manual intervention. This not only saves time but also reduces errors that commonly occur when transferring data between disconnected systems.
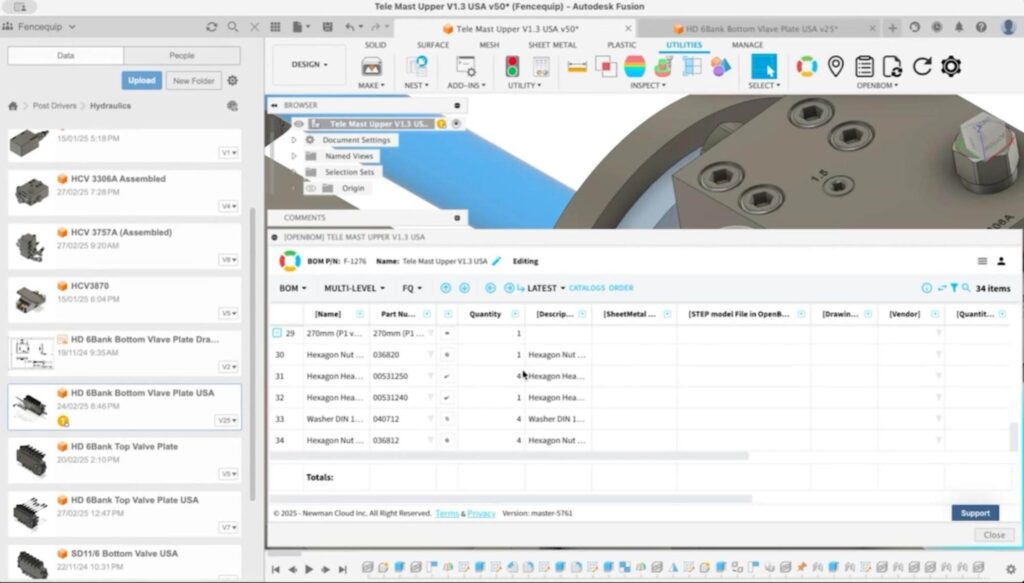
Beyond connectivity, OpenBOM provides the flexibility that FENCEQUIP needed to adapt to changing designs and manufacturing requirements. BOMs are not static—parts change, suppliers shift, and costs fluctuate. With OpenBOM, FENCEQUIP can easily update and manage real-time product structures, ensuring that procurement decisions always reflect the latest design changes.
One of the most significant improvements has been in cost assessment and purchasing optimization. With OpenBOM, FENCEQUIP now has instant visibility into material costs, supplier options, and order quantities, allowing them to make smarter financial decisions early in the design process. Instead of waiting until production to analyze costs, they can now evaluate different options and choose the most cost-effective materials before an order is placed.
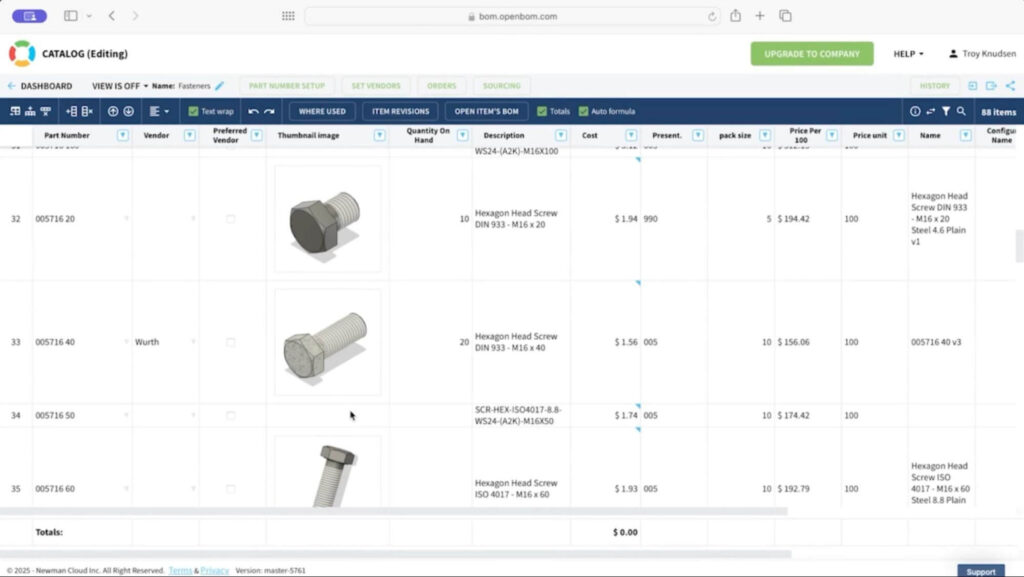
This optimization has led to reduced material waste, better supplier negotiations, and a leaner, more efficient purchasing process. By ordering only what is needed—when it’s needed—FENCEQUIP has dramatically improved inventory management and overall operational efficiency.
OpenBOM – A Team That Supports Success
Technology is just one part of the equation. The OpenBOM team played a crucial role in making this transformation a success for FENCEQUIP. Their expertise in data management, cloud technology, and lean manufacturing provided invaluable support during the implementation process.
FENCEQUIP found the OpenBOM team easy to work with, responsive, and knowledgeable, helping them navigate the transition and tailor the solution to their specific needs. This level of customer engagement has made a significant difference, reinforcing the value of OpenBOM not just as a tool, but as a trusted partner in their digital transformation journey.
Watch the Video: See OpenBOM in Action
To better understand how FENCEQUIP is leveraging OpenBOM for lean manufacturing, check out our video where we walk through their seamless Autodesk Fusion integration, cost-saving strategies, and purchasing optimizations.
📺 Here is a video to watch
In this video, we dive deeper into how OpenBOM helps FENCEQUIP connect engineering, procurement, and cost assessment into a single, streamlined workflow. You’ll see firsthand how they have reduced errors, saved costs, and improved operational efficiency—all while working with a system that is flexible, modern, and easy to use.
Conclusion: A Smarter Way to Manufacture
By adopting OpenBOM, FENCEQUIP has transformed its manufacturing process. What was once a fragmented and inefficient system is now a seamlessly connected, cost-optimized, and lean operation. The integration of engineering, procurement, and cost management has not only saved time and money but has also improved overall business agility.
For manufacturers looking to improve their design-to-purchase process, OpenBOM provides a proven, cloud-based solution that enhances flexibility, improves cost control, and streamlines procurement. Whether you’re dealing with complex product structures or need better inventory control, OpenBOM offers the right tools and expert support to make it happen.
If you’re interested in learning more about how OpenBOM can help your company achieve lean manufacturing, get in touch with us today!
🔗 REGISTER FOR FREE to check how OpenBOM can help you.
Best, Oleg
Join our newsletter to receive a weekly portion of news, articles, and tips about OpenBOM and our community.