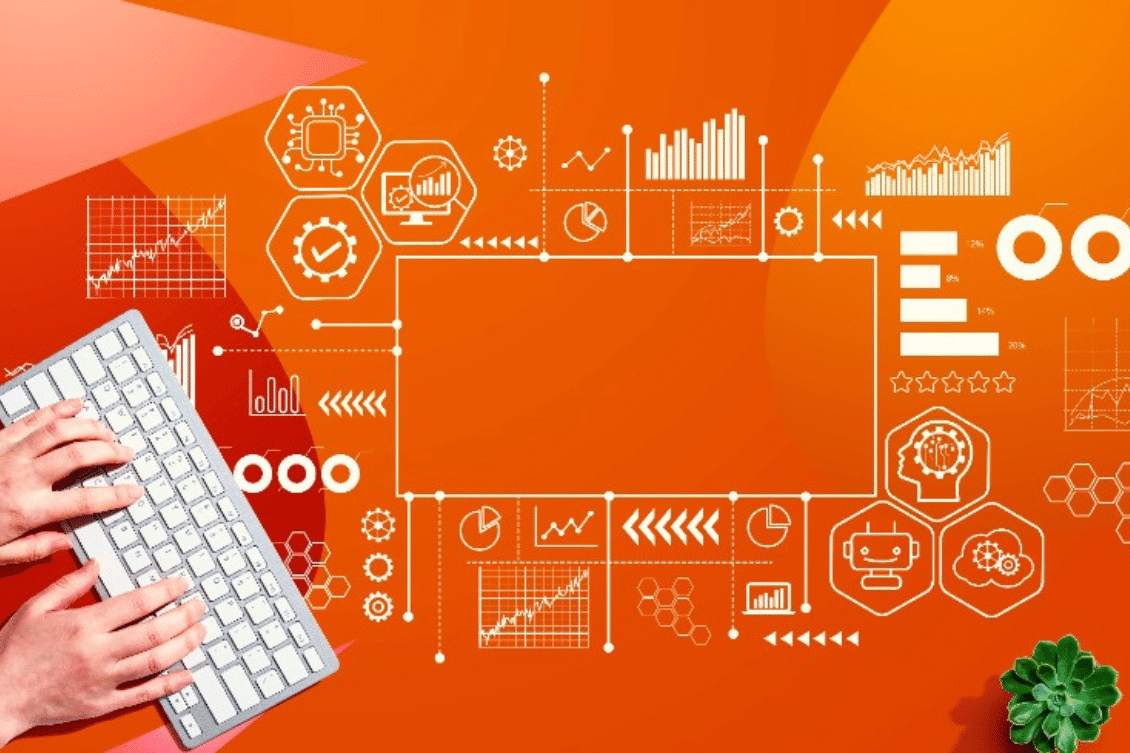
The last few years brought sweeping changes to the manufacturing industry. COVID-19 was a one-of-a-kind event that accelerated digital transformation in the entire world by setting up a unique experiment that pushed companies to switch to remote work overnight. It immediately displayed gaps in manufacturers’ preparation for the future digital world. Followed by 2020 we saw even more challenges such as supply chain turbulence and an even more challenging economical downturn.
Working with many manufacturing companies during 2022, we identified that digital transformation is on the agenda list for many of them. Check our earlier article – PLM and Digital transformation reflection as we conclude 2022. Companies that don’t begin preparing for the digital disruption now will be struggling in many ways. As technology advances and global competition intensifies, there is immense pressure on many companies to stay competitive. Amidst this climate of uncertainty, understanding how to prepare your manufacturing business for these technologically driven advancements can be difficult.
In this blog post series, we’ll start our deep dive into how manufacturing companies can prepare themselves for digital business and more importantly discuss what strategic methods that are available to help manufacturing companies avoid digital disaster in 2023.
Safeguarding Product and Design Data
When did you last check where all the design and product information in your company is located? There is a high chance that the information is spread between multiple locations. Design files owned by engineers and located in multiple shared folders, cloud and remote disk drives, various Excels, and remoted spreadsheets are belonging to different team members and are also stored somewhere. If you’re lucky enough, you might have some network drives with stored “project folders” with shared access and “shared spreadsheets” with BOM data.
Separately, you might find Google Drive (or Dropbox) with files that are shared with contractors and suppliers. The entire system is messy and requires a lot of human effort to get the right information at the right time. Now imagine that a key engineer or manager is leaving or mistakenly deleting some of the important files, folders, etc. Or you share the wrong data with your contractor.
The picture I described above is very resonating with many organizations and I know about it because this is how many of them are coming to OpenBOM and asking to help organize information.
OpenBOM solves the problem by providing a single place to store and manage files, product data, and all related information. The data is structured in the OpenBOM cloud platform, protected, encrypted, and available to everyone based on the OpenBOM access control system and instant sharing mechanism regardless of what company you work for. OpenBOM automatically backup your data and eliminate the long list of headaches you had before.
Digitally Connecting Processes
Companies are run by processes. Your process is as good as the system that allows you to transfer the data to fulfill the process. Bad data handover leads to “data leaks” and broken communication. Sending the wrong file to the contractor or using the wrong excel to estimate the cost – are just two examples of how things can go wrong. Sending data via email or placing the wrong file in the shared drive and you’re lost. Add to this fragmented data located in multiple disks and computers, and you might see a huge digital disaster happening afterward.
How to prevent it? You need to follow these 5 digital transformation rules:
- A single source for information (no information re-entry) in your product data management system.
- Data is shared in real-time and not transferred using multiple data sources and media. Eliminate multiple “shared folders” to transfer data between functions and companies
- Keep the history and create a traceable mechanism to control who was changing files and data. No more “accidental” changes with no name, date, or time.
- Secured access with individual passwords and multi-factor authentication.
- Continuous backup of all information.
By following these digital transformation rules you can avoid a huge potential disaster for your company.
Digital Culture and Proactive Risk Mitigation
Humans are the biggest risk factor for digital transformation. Human mistakes are the root cause of many organizational disasters. Data is accidentally deleted or exposed to the wrong people, information is compromised, and files are lost. This is a short list of top examples and situations. Companies can avoid it by building a culture in which companies are focusing on how to keep their digital assets safe.
Conclusion:
Building a digital business is a new way of using technologies to help manufacturing companies prevent what can be a digital disaster in 2023. Leading manufacturing companies have recognized the need for digital transformation and data management to support digital processes. At OpenBOM, you can get a powerful product lifecycle management platform manufacturing companies can use to create a powerful mechanism to protect your data, connect processes, and by doing so avoid a digital disaster for your business.
REGISTER FOR FREE and start a 14-day trial to check how OpenBOM can help you.
Best, Oleg
Join our newsletter to receive a weekly portion of news, articles, and tips about OpenBOM and our community.