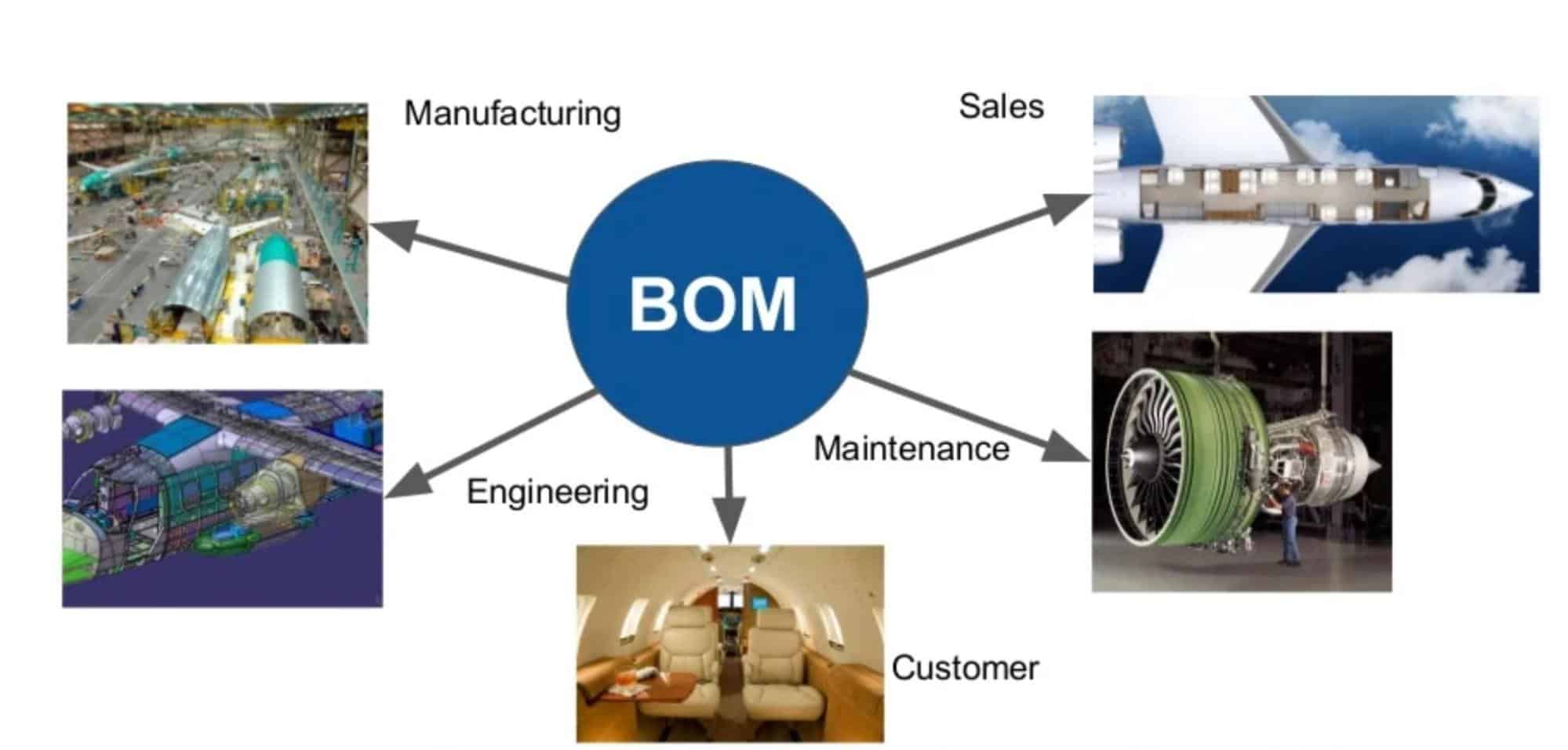
Bill of Materials is the lifeblood of every manufacturing company and product development process. For all companies, a bill of materials is the way to keep information about the product and perform many actions – definition, costing, procurement, maintenance, and many others. While it is clear that the “BOM (bill of materials)” is in the middle of all processes, the discussion about what specific BOM do you need, how information is structured in that BOM, and what should be included or excluded from that BOM is a very complex question. Talking to people in the organization you can find many opinions about how many (Bills of materials) are needed and how to manage them.
Unfortunately, Excel is a common lingua franca for BOMs in many organizations and it creates a lot of complexities and difficulties when managing product information. Let’s speak about some typical situations we can see within companies coming to OpenBOM with help.
Organizational Silos and Multiple BOMs
Usually, the bill of materials is a reflection of organizational silos. This is the most typical way every organization is starting to think about a Bill of Materials – by belonging to a specific group of people focusing on their tasks. This is how companies can easily end up with an engineering bill of materials, manufacturing BOM, production BOM, procurement, and others.
Another (also very typical) way to think about multiple bills of materials is related to the way manufacturing companies are working with other organizations – contractors and sometimes suppliers (especially design suppliers). For many organizations, creating separate BOMs is the way to segregate the data between what can be used in the organizations and outside contractors and design suppliers.
Data Responsibility and Multiple BOMs
Another reason why many companies are ending up with multiple BOMs is partially related to who is responsible for a specific set of information. In such a way, engineers working on mechanical design can easily end up with “mechanical BOM” and engineers developing PCB can create an “electronic BOM”. In complex products, you can sometimes see how separate BOMs are created for different product units and assemblies.
Moving information downstream should put data in the hands of procurement and production planners. In such a way, you can easily get BOMs for OTS (off-the-shelf) parts and custom assemblies. It is very common to see how the procurement team is creating a separate BOM that is used for purchasing only.
From Excel to Information Flow – How Many BOMs Is Needed?
The problem I described above is real and companies are struggling with information spread around in multiple Excels and BOMs. Eventually, companies are looking at how to organize their information (multiple Excels) and the real question that comes up is – how many BOMs are really needed?
There is no universal answer to this question. There are multiple factors that impact the decision of BOM organizations and how information can be managed. Here are some typical factors that can be used to decide:
- The manufacturing process (MTP, CTO, ETO)
- The complexity of the product and changes
- The enterprise system setup
In one of my next articles, I will discuss how to organize Bill of Materials for each of the use cases I described above. Stay tuned…
However, regardless of the number of BOMs you decide to manage, it is absolutely critical to ensure that the Bill of Materials represents a single source of truth about product data and that you organize the mechanism of data synchronization to support keeping the information updated and supporting the flow of information between organizations and multiple functions.
At OpenBOM we are working to provide robust support allowing our customers to manage multiple bills of Materials and share them with the right people in the organization and outside contractors and suppliers. These days we are working on new features to support seamless EBOM-MBOM communication and support for custom BOMs in OpenBOM. Check more about it here – BOM Transformations.
Conclusion
One of the most important functions of every organization is to create a single source of truth for all product structures and related information. Such a strategy eliminates the need to keep dozens (or sometimes even more) of different BOM- excels and send them across your organization’s departments and outside. Having a robust and flexible data management platform such as OpenBOM allows you to forget about how to deal with multiple Excels- OpenBOM allows you to organize all information and instantly share the right subset of data with everyone who needs to consume this information.
REGISTER FOR FREE and start a 14 days trial to see how OpenBOM can help you today.
Best, Oleg
Join our newsletter to receive a weekly portion of news, articles, and tips about OpenBOM and our community.